Testing standards for clean rooms
Testing standards for cleanrooms typically include national, industry and international standards. For example, China's national standard “Cleanrooms and Related Controlled Environments Part 1: Air Cleanliness Levels” (GB/T 25915.1 - 2010) provides basic specifications and requirements for environmental testing of cleanrooms. In addition, international standards such as ISO 14644 series are also widely used for cleanroom environmental testing. Third-party cleanroom testing and acceptance units need to be accredited by the National Laboratory Accreditation Board (CNAS) and metrological certification (CMA), and the cleanroom test reports issued by them can truly reflect the actual situation of the cleanroom.
Clean room testing scope and program
The testing scope of clean shed includes clean room environment rating and project acceptance testing, covering food clean room, health care purification workshop, cosmetic clean project, bottled water filling workshop, clean production workshop for electronic products, GMP purification workshop, hospital operating room, animal laboratory, biosafety laboratory, biosafety cabinets, ultra-clean workbench, dust-free workshop, aseptic workshop and so on. Testing items include clean room dust particle count, settled bacteria, planktonic bacteria, differential pressure, ventilation frequency, air velocity, fresh air volume, illumination, noise, temperature, relative humidity, etc.
Tools and equipment for clean room testing
Clean room testing usually requires the use of specialized testing tools and equipment, such as dust particle counters, bacterial samplers, differential pressure meters, anemometers, anemometers, air volume hoods, noise meters, illuminance meters, temperature and humidity meters, and so on. These devices are used to measure and monitor the air quality and environmental parameters in the clean room to ensure that they meet the required standards.
Processes and steps for clean room testing
Initial inspection in empty state: The first inspection of the clean room is carried out without any personnel and equipment in operation to assess whether the infrastructure and facilities meet the design requirements.
Functional verification under the static state: all the equipment in the clean room has been installed but not running, and no production personnel in the case of testing, focusing on temperature and humidity control, particle concentration and illumination and noise testing.
Acceptance for use under dynamic conditions: Testing in which all equipment is operational and production personnel are present, simulating a production process and again checking particle concentrations to ensure that cleanliness is maintained even in a production environment.
Documentation and Record Review: In addition to physical testing, complete documentation is an important part of acceptance, including design drawings, construction logs, equipment specifications, test reports, and proof of compliance with all relevant standards.
Importance of Clean Room Testing
Clean room testing is critical to ensuring product quality and production safety. It controls not only airborne particles and microorganisms, but also chemicals and other potential sources of contamination. Through regular testing and maintenance, potential problems can be identified and solved in time, avoiding product quality accidents and economic losses caused by environmental problems.
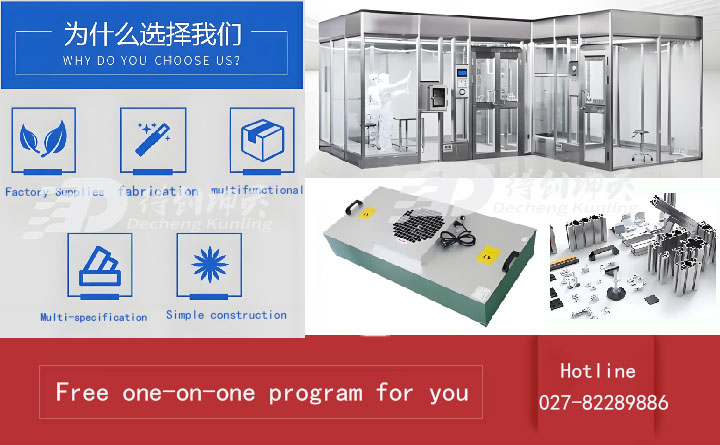