GMP Class C Clean room
A GMP Class C Cleanroom is a controlled environment commonly used in the pharmaceutical, biotechnology, and healthcare industries where certain manufacturing processes require a moderate level of cleanliness. Class C cleanrooms are less stringent than Class A or Class B cleanrooms but still maintain high standards for controlling contamination and ensuring product quality. These cleanrooms are used for processes that are not directly involved in aseptic handling but require a controlled environment to prevent contamination of products, materials, or equipment.
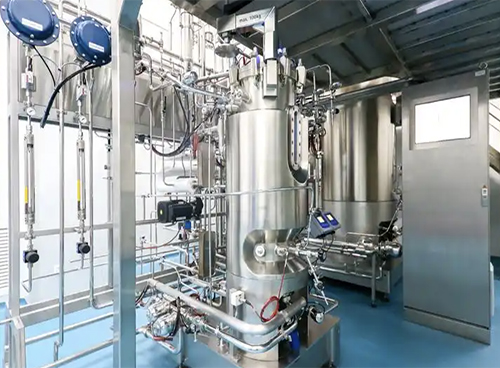
GMP Class C Cleanroom Air Changes Per Hour
Class C Cleanroom (ISO 7 Cleanroom)
The filtered air sweeps down the room in a unidirectional way, at a velocity generally between 0.3 m/s and 0.5 m/s, and exits through the floor, removing the airborne contamination from the room. Cleanrooms using unidirectional air flow are more expensive than non-unidirectional ones, but can comply with more stringent classifications, such as ISO 5 or lower. |
GMP Class C Clean Room Grade Table
|
|
Key Characteristics of Class C Clean Room
Class C cleanrooms are typically classified as ISO Class 7 according to the ISO 14644-1 standard, allowing up to 352,000 particles per cubic meter for particles ≥ 0.5 microns. This level of cleanliness is suitable for environments where air cleanliness is important but not critical, such as the preparation or storage of materials that will later undergo sterilization or more critical processing steps. | |
Class C cleanrooms typically have an air change rate of 20-30 air changes per hour (ACH), which ensures the removal of airborne contaminants and helps to maintain a stable environment. The air filtration systems usually include HEPA (High-Efficiency Particulate Air) filters to capture airborne particles and prevent contamination. | |
![]() |
Class C cleanrooms are generally maintained at a positive pressure relative to adjacent, lower-grade environments (e.g., Class D). This ensures that air does not flow from less clean areas into the Class C room, preventing contamination from external sources. |
![]() |
While Class C cleanrooms do not require the strict gowning standards of Class A or B environments, personnel are still required to wear protective clothing such as lab coats, gloves, masks, and hair covers to minimize the risk of contaminating the room. Gowning requirements will vary based on the specific processes and the level of contamination control needed. |
![]() |
Preparation of Non-Sterile Pharmaceutical Products: Class C cleanrooms are commonly used in the preparation, mixing, and blending of raw materials, excipients, and active pharmaceutical ingredients (APIs) that will later undergo sterilization or other critical processing. |
![]() |
Cell Culture and Media Preparation: In biotechnology, Class C cleanrooms are used for the preparation of cell culture media, buffers, and other culture-related materials that do not require a Class A environment but still need to be processed in a clean environment to maintain the integrity of the biological materials. |
![]() |
Assembly of Non-Sterile Medical Devices: Class C cleanrooms are used for assembling medical devices that do not need to be sterile but still require an environment free from excessive contamination. These can include devices like diagnostic instruments, surgical tools (before sterilization), and other medical equipment where cleanliness standards need to be controlled but are not as critical as in aseptic production. |
![]() |
Assembly of Sensitive Electronic Components: In industries like electronics and semiconductor manufacturing, Class C cleanrooms are used for the assembly of sensitive components where contamination could negatively impact performance, such as in the production of semiconductors, circuit boards, or optoelectronic devices. These rooms help reduce particulate contamination during assembly processes. |
GMP Class C Clean Room Wall
| |
| |
|
GMP Class C Clean Room Celling
![]() | ![]() | ![]() | ![]() |
|
| ||
![]() | ![]() | ![]() | ![]() |
|
|
GMP Class C Clean Room Floor
![]() | ![]() | ![]() |
| ||
![]() | ![]() | ![]() |
| ||
![]() | ![]() | ![]() |
|
FAQ
Q: What is GMP class A and B cleanroom environments?
A: GMP Class A and B cleanrooms are highly controlled environments used primarily in pharmaceutical and biotechnology industries where contamination control is critical. Class A is the most stringent and is typically used for aseptic processes, such as filling sterile products and handling sterile materials. It requires a particulate count of ISO Class 5, with the highest level of air filtration and control to ensure the sterility of the products. Class B cleanrooms, while still stringent, are used for less critical stages, such as the preparation of materials for aseptic processing. Class B cleanrooms have an ISO Class 5 air quality requirement in critical zones and ISO Class 7 for non-critical areas.
Q: What is a class C cleanroom?
A: A Class C cleanroom, according to GMP guidelines, is a controlled environment typically used for processes that do not involve aseptic handling but still require a clean environment to avoid contamination. It is classified as ISO Class 7 and allows a particulate count of up to 352,000 particles per cubic meter for particles ≥0.5 microns. Class C cleanrooms are commonly used for the preparation and packaging of non-sterile pharmaceutical products or for stages that do not directly affect product sterility but still require contamination control.
Q: What is type C cleaning in pharma?
A: Type C cleaning in pharma refers to a specific cleaning procedure used for cleaning equipment, surfaces, or environments that fall under GMP guidelines for Class C cleanrooms. It involves the removal of visible contamination, followed by a disinfection process to reduce microbial load. This cleaning method is crucial for preventing contamination during the production of non-sterile pharmaceutical products and ensures that the manufacturing area meets the required cleanliness standards for GMP Class C environments.
Q: What are the GMP grades for cleanrooms?
A: GMP cleanrooms are classified into grades A, B, C, and D based on the level of contamination control required for different stages of pharmaceutical production. Grade A is the highest level of control and is used for sterile products or critical processes, with the strictest contamination control measures. Grade B is used for less critical stages of aseptic processing. Grade C is used for intermediate stages where contamination control is important but not as stringent as Grades A and B. Grade D cleanrooms are used for basic activities that require minimal contamination control, often for packaging or storage.
Q: What are the requirements for Grade C GMP?
A: Grade C GMP cleanrooms require air quality standards that maintain particulate contamination within ISO Class 7 limits, which allow up to 352,000 particles per cubic meter for particles ≥0.5 microns. The air exchange rate typically needs to be 20-30 air changes per hour, and the room must maintain positive pressure relative to surrounding areas to prevent contamination. Strict cleaning and disinfection procedures must be followed, and environmental monitoring is essential to ensure that contamination levels remain within acceptable limits for non-sterile production processes.
Q: What is the difference between Grade B and Grade C cleanroom?
A: The key difference between Grade B and Grade C cleanrooms lies in their cleanliness standards and applications. Grade B cleanrooms are used for critical processes, such as aseptic processing, and maintain a higher level of cleanliness with air quality typically at ISO Class 5 in critical zones. Grade C cleanrooms, on the other hand, are used for less critical stages of production where contamination control is still necessary but not at the same level as Grade B. Grade C cleanrooms typically meet ISO Class 7 standards, allowing a higher level of particulate contamination compared to Grade B.
Q: What class clean room is a semiconductor?
A: Semiconductor manufacturing cleanrooms are typically classified as ISO Class 1 to ISO Class 5, depending on the specific stage of the process and the required cleanliness level. These cleanrooms are highly controlled environments due to the sensitivity of semiconductor components to dust and particulate contamination. The cleanrooms must maintain extremely low levels of airborne particles to ensure the integrity and functionality of the semiconductor products being manufactured.
Q: What is a Grade C clean room?
A: A Grade C cleanroom is an environment classified as ISO Class 7, used in pharmaceutical manufacturing for non-sterile processes where contamination control is important, but not as critical as for sterile products. It allows up to 352,000 particles per cubic meter for particles ≥0.5 microns and is typically used for stages such as material preparation, mixing, or secondary packaging of pharmaceutical products. It requires regular cleaning, air filtration, and monitoring to ensure compliance with GMP standards.
Q: What is class D clean room?
A: A Class D cleanroom is the least stringent classification, typically classified as ISO Class 8. It is used for less critical applications, such as the packaging of non-sterile products, or for areas where contamination risk is lower. While it still adheres to GMP standards for cleanliness, it does not require the same level of air filtration or particle control as higher-class environments like Grade A, B, or C cleanrooms. Class D cleanrooms are often used for tasks that do not directly impact product sterility or contamination levels.
Q: What is grade C gowning?
A: Grade C gowning refers to the protective clothing worn by personnel working in a GMP Class C cleanroom to minimize the risk of contamination. The gowning procedure includes wearing a lab coat, gloves, hairnet, face mask, and sometimes shoe covers or booties. This ensures that personnel do not introduce contaminants such as particles, oils, or microorganisms into the controlled environment. While the gowning requirements for Grade C are not as strict as for Grade A or B, they still play a crucial role in maintaining cleanliness standards.
Q: What is the FDA classification of clean rooms?
A: The FDA classifies cleanrooms based on the level of cleanliness required for different stages of pharmaceutical production, similar to GMP classifications. FDA cleanroom classifications are aligned with ISO standards and range from Class 1 to Class 8. These classifications reflect the maximum allowable particle count in the air for different room types. For example, Class 100 (ISO Class 5) is used for critical aseptic processing, while Class 100,000 (ISO Class 8) is used for less critical processes where contamination control is still necessary but not as stringent.
Q: What is type AB and C cleaning in pharma?
A: Type AB and C cleaning in pharma refers to cleaning procedures for different areas within pharmaceutical manufacturing environments. Type AB cleaning is used for areas that require higher levels of contamination control, such as aseptic processing zones, where particulate contamination and microbial growth must be minimized. Type C cleaning refers to procedures for environments with less stringent cleanliness requirements, like Grade C cleanrooms, where cleaning focuses on removing visible contamination and controlling microbial growth but does not require the same level of disinfection as Type AB areas.
Q: What are the classification of pharmaceutical cleanrooms?
A: Pharmaceutical cleanrooms are classified according to the level of contamination control required, with classifications ranging from Grade A (ISO Class 5) to Grade D (ISO Class 8) under GMP guidelines. Grade A cleanrooms are used for aseptic processing and critical manufacturing steps, while Grade B is for less critical aseptic stages. Grade C cleanrooms are used for intermediate processes that do not require aseptic conditions but still require a clean environment, and Grade D is used for basic operations like packaging and storage of non-sterile products. These classifications ensure that contamination is controlled throughout pharmaceutical production.
Q: What is GMP class A and B cleanroom environments?
A: GMP Class A and B cleanrooms are environments used in pharmaceutical manufacturing with stringent contamination control standards. Class A cleanrooms are used for aseptic processes, such as sterile product filling, with the highest level of cleanliness (ISO Class 5). Class B cleanrooms are used for other critical stages, like preparation of sterile materials, with slightly less stringent controls but still maintaining high air quality (ISO Class 5 in critical zones). Both classes require advanced air filtration systems, strict gowning procedures, and rigorous cleaning protocols to ensure the safety and sterility of pharmaceutical products.
Q: What are the cleanroom classifications in GMP?
A: In GMP (Good Manufacturing Practice) guidelines, cleanrooms are classified into Grades A, B, C, and D based on the level of contamination control required for different stages of pharmaceutical production. Grade A is the most stringent and is used for aseptic processing, such as filling and handling sterile products. Grade B is used for critical but non-aseptic stages. Grade C is for intermediate processes like material preparation or mixing, while Grade D is used for less critical processes such as packaging and storage. Each grade has specific air cleanliness and contamination control requirements as per ISO standards.
Related Information
-
共1页 6条