What Does Class 10,000 Clean Room Mean?
A Class 10,000 clean room is a controlled environment designed to minimize the introduction, generation, and retention of airborne particles. According to the Federal Standard 209E, a Class 10,000 clean room allows no more than 10,000 particles per cubic foot of air that are 0.5 micrometers or larger. This classification signifies that the room has a maximum allowable particle count of approximately 352,000 particles per cubic meter, making it suitable for industries such as pharmaceuticals, biotechnology, and Electronics manufacturing.
The cleanliness of a Class 10,000 clean room is achieved through a combination of high-efficiency Air Filters, regular cleaning protocols, and strict personnel controls. The room is typically ventilated at a rate that ensures a minimum of 10 air changes per hour, which helps maintain air quality and reduces contamination risks. The air filtration systems often use HEPA (High-Efficiency Particulate Air) filters, which can capture 99.97% of particles as small as 0.3 micrometers.
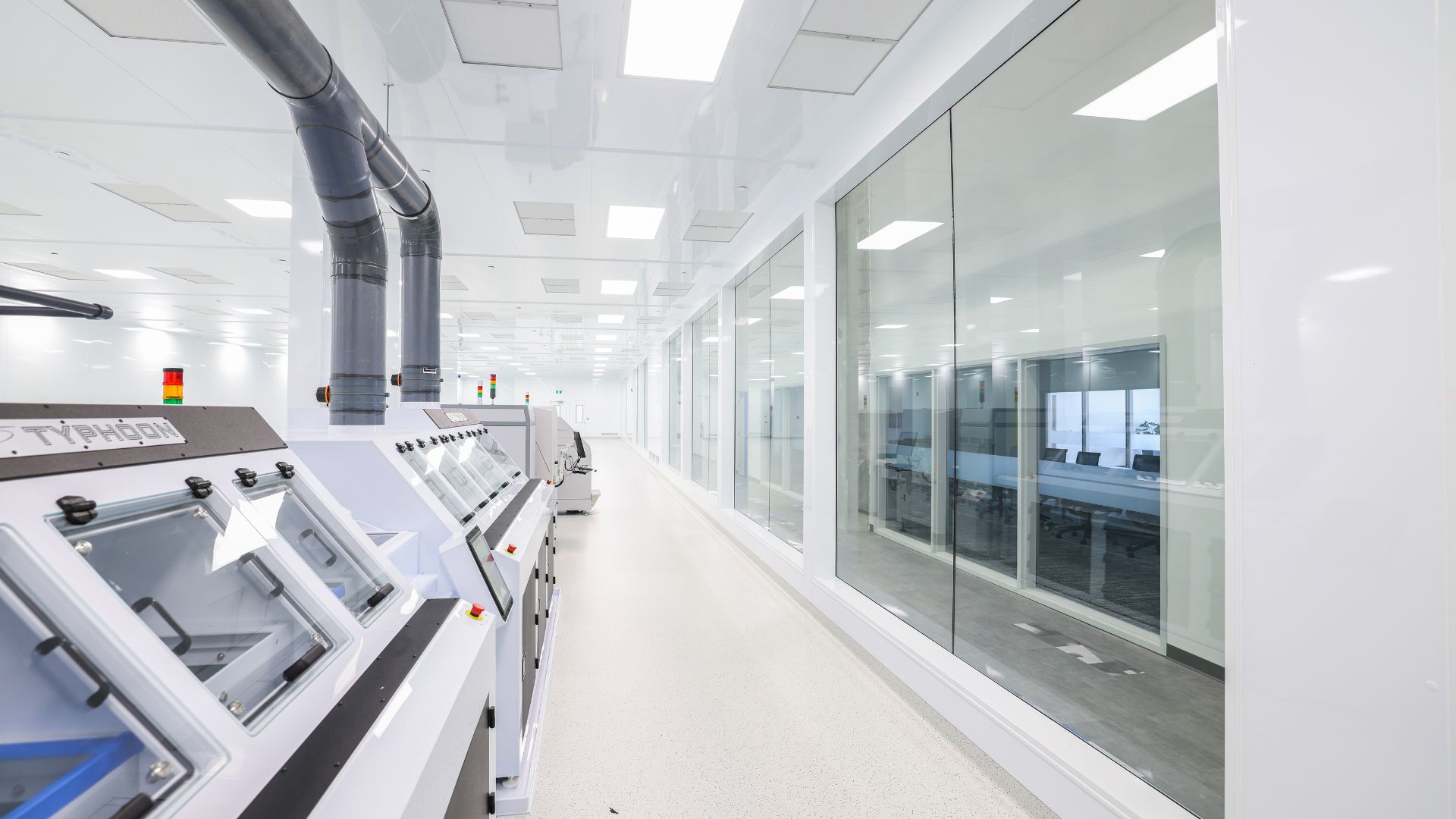
In terms of temperature and humidity control, Class 10,000 clean rooms maintain specific environmental conditions to ensure product integrity and personnel comfort. Temperature levels are usually kept between 20°C to 22°C (68°F to 72°F), while relative humidity is controlled to remain between 30% and 60%. These conditions help prevent static electricity buildup and other environmental factors that could compromise sensitive processes or products.
A Class 10,000 clean room is a vital facility in various industries requiring stringent control of airborne contaminants. Its specifications are critical for ensuring product quality and operational efficiency, adhering to international standards such as ISO 14644-1.
Relevant Standards and Specifications:
- iso 14644-1: Cleanrooms and Controlled Environments
- Federal Standard 209E: Cleanroom Standards
- iso 14644-2: Monitoring to Provide Evidence of Cleanroom Performance
Class 10,000 Clean Room ISO Equivalent
A Class 10,000 clean room is equivalent to ISO 7, as per iso 14644-1 standards. ISO classification systems categorize clean rooms based on the maximum allowable particle concentration in the air. For a Class 10,000 clean room, the permissible particle count is up to 10,000 particles per cubic foot, which translates to about 352,000 particles per cubic meter. In contrast, an ISO7 clean room allows for a maximum of 352,000 particles per cubic meter, creating a direct correlation between these two classification systems.
The ISO standards provide a global framework for Clean Room Classification, ensuring consistency across different regions and industries. This standardization is essential for companies that operate internationally, as it enables them to meet varying regulatory requirements while maintaining product safety and quality.
Class 10,000 Clean Room Cost
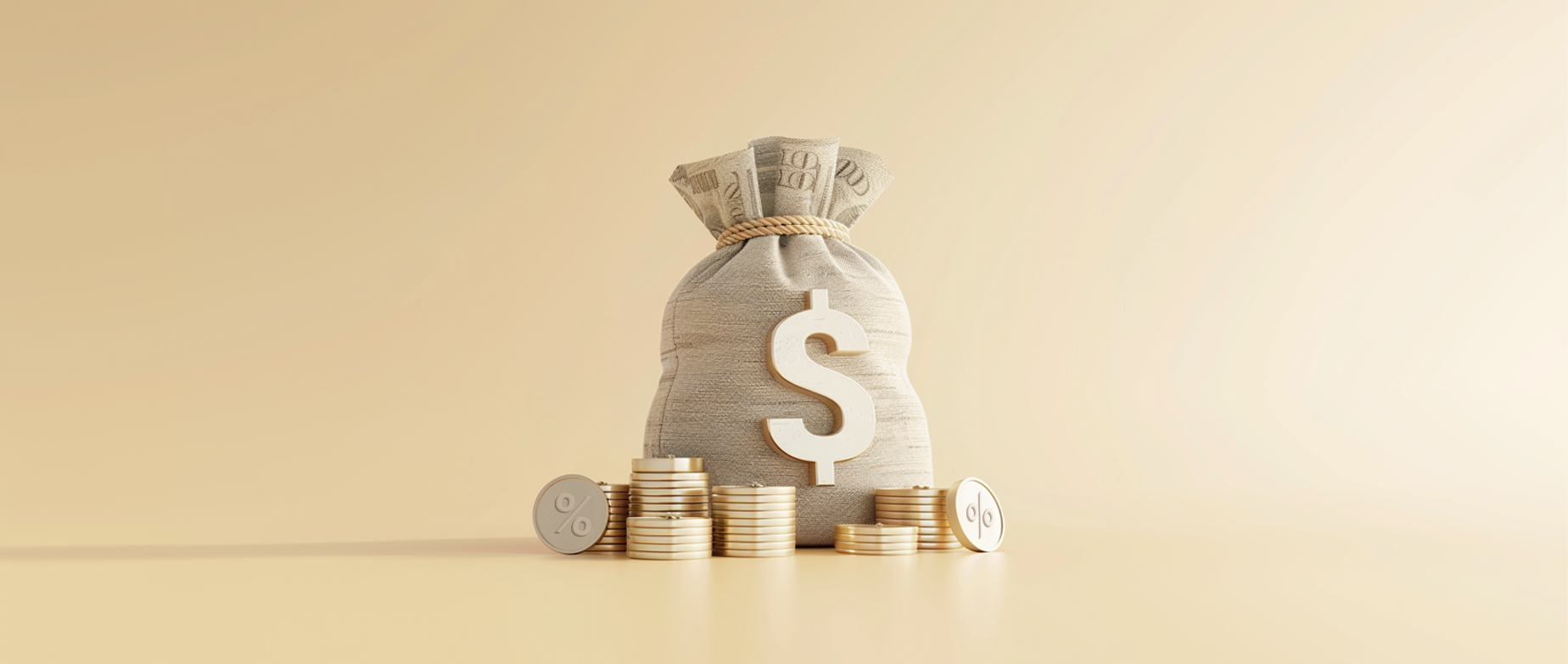
1. Initial Setup Costs
The cost of establishing a Class 10,000 clean room can be significant. Factors include the construction of the facility, installation of specialized HVAC systems, and the deployment of HEPA or ULPA filters. On average, the setup costs can range from $100 to $400 per square foot, depending on the complexity and location of the clean room.
2. Operational Expenses
Operating a clean room incurs ongoing costs, including energy consumption for ventilation and climate control systems, regular maintenance of filtration systems, and staffing expenses. Monthly operating costs can range from $2 to $5 per square foot, especially in high-demand environments where strict cleanliness must be maintained.
3. Compliance and Monitoring
Regular monitoring and compliance with industry standards add to the overall cost. This includes routine air quality testing, personnel training, and equipment calibration. Companies may spend upwards of $5,000 to $20,000 annually on compliance and monitoring services to maintain their clean room's certification and operational integrity.
4. Total Investment
Overall, the total investment in a Class 10,000 clean room can exceed $500,000 for a small facility and can escalate into the millions for larger operations. Businesses must weigh these costs against the potential benefits, such as improved product quality, reduced contamination rates, and compliance with regulatory standards.
Class 10,000 Clean Room Requirements
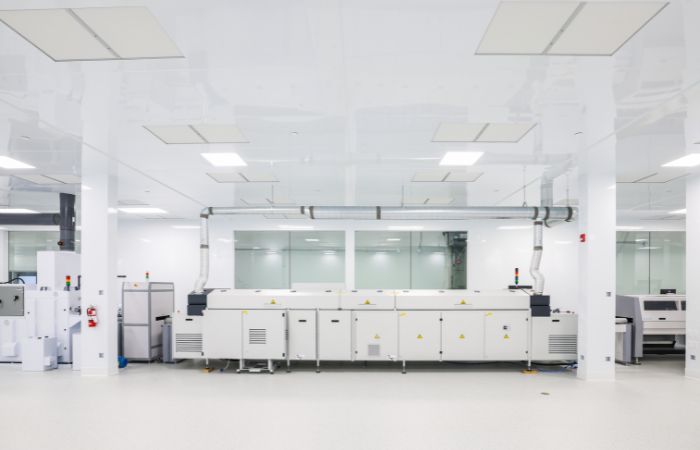
1. Design Specifications: A Class 10,000 cleanroom must ensure effective contamination control through a suitable layout, non-porous materials, and a ceiling height of 8 to 10 feet. It should achieve 10 to 15 air changes per hour to maintain cleanliness levels.
2. Environmental Control: Maintaining environmental parameters is crucial in a Class 10,000 clean room. The temperature should be controlled within a range of 20°C to 22°C (68°F to 72°F), while humidity levels should be kept between 30% and 60%. These conditions help prevent static electricity and moisture-related issues that can affect sensitive materials and processes.
3. Personnel and Protocols: Strict personnel protocols are essential for maintaining the cleanliness of a Class 10,000 clean room. All personnel must undergo training on clean room practices, including gowning procedures and the importance of minimizing particle generation. Gowning requirements typically include wearing cleanroom suits, gloves, masks, and shoe covers. Access to the clean room should be limited to authorized personnel only, and an anteroom is often utilized for gowning and decontamination.
How to Reduce Particle Count in a Clean Room?
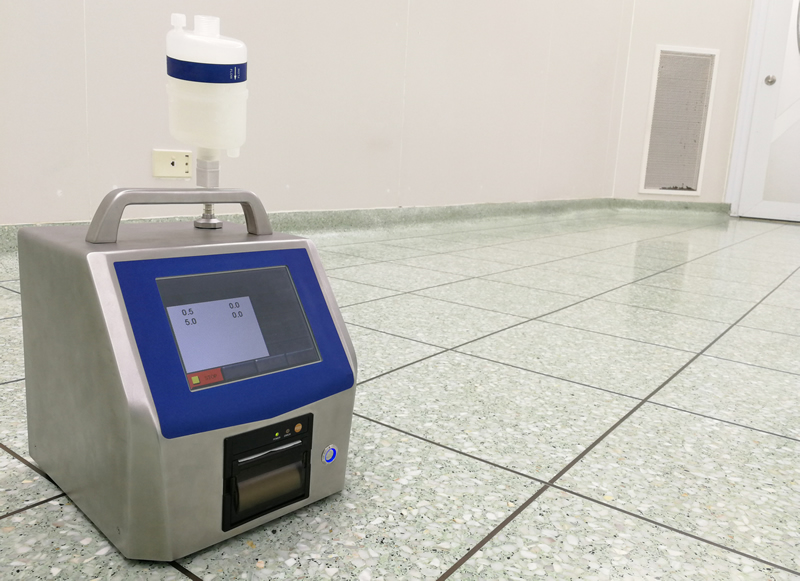
Optimization of Airflow
One of the most effective methods to reduce particle count in a clean room is optimizing airflow patterns. Ensuring a unidirectional airflow system helps to sweep particles away from critical areas. Properly designed air diffusers can distribute air evenly, minimizing turbulence that can stir up settled particles. Regularly assessing and maintaining air handling units (AHUs) is essential to ensure they operate at optimal efficiency.
Regular Cleaning Protocols
Establishing rigorous cleaning schedules is vital for maintaining low particle counts. Surfaces should be cleaned with appropriate cleaning agents that do not leave residues. High-touch surfaces, such as door handles and countertops, should be cleaned multiple times a day.
Contamination Control Measures
Implementing strict contamination control measures can significantly reduce particle counts. This includes controlling the flow of personnel in and out of the clean room, limiting the number of people present at any given time, and ensuring that all materials entering the clean room are decontaminated. Airborne contamination can also be reduced by using appropriate gowning protocols, which include the use of disposable or laundered cleanroom garments.
Monitoring and Maintenance
Continuous monitoring of particle levels is essential for identifying trends and potential contamination sources. Utilizing particle counters to regularly sample air quality can help detect issues early. Additionally, maintaining and replacing HEPA filters according to manufacturer specifications ensures that air filtration systems remain effective.
How Do You Measure Cleanroom Class?

Particle Count Measurement:
The primary method for measuring cleanroom class is through particle counting. This process involves using a calibrated particle counter to measure the concentration of airborne particles in the clean room environment. For a Class 10,000 clean room, the maximum allowable particle count is 10,000 particles per cubic foot of air for particles 0.5 micrometers and larger.
Sampling Protocols:
To accurately assess the CleanRoom Classification, standardized sampling protocols must be followed. This includes conducting tests during different operational conditions, such as when the clean room is in use and when it is not. Typically, samples should be collected at least once a month to ensure that cleanliness levels are maintained. The results of these tests are then compared against the thresholds established by relevant standards, such as ISO 14644-1.
Documentation and Compliance:
Maintaining detailed records of all measurements and tests conducted is critical for compliance with industry standards. These records should include the date and time of testing, the locations sampled, and the results obtained. Regular audits and reviews of these records help ensure ongoing compliance with cleanroom classifications and can be essential for regulatory inspections. Any deviations from the acceptable particle counts must be addressed promptly, and corrective actions should be documented to maintain quality assurance.
By adhering to these measurement practices, facilities can ensure their clean room operates within the specified class and meets the necessary industry standards.