Building A CleanRoom requires systematic planning and design to ensure that the cleanliness requirements of a particular industry are met. The following is a detailed analysis of the key steps in building a cleanroom, from site selection, functional layout, to construction, testing and operation and maintenance.
I. Cleanroom Site Selection
The site selection of the cleanroom is the first step
in the construction process, and must fully consider the use of demand and
environmental factors. The key elements of site selection include geographic
location, floor height, surrounding environment and infrastructure.
First of all, the site selection should try to avoid pollution sources, such as industrial areas and streets with heavy traffic. According to the ISO 14644-1 standard, cleanrooms should be sited to ensure that their surroundings minimize the impact on air quality. The ideal site should be in an area with good air flow and few pollutants.
Secondly, the choice of floor is also crucial. It is generally recommended that cleanrooms be located on the upper floors of buildings to minimize the settling effects of dust and other particulate matter. In addition, the design of the cleanroom's ventilation system should be taken into account to ensure smooth air flow and avoid dead ends and airflow interference.
Finally, the completeness of infrastructure is also an important consideration in site selection. Cleanrooms require stable power supply, water supply, drainage and communication facilities to ensure their normal operation. Therefore, in the site selection, should be fully communicated with the relevant departments to ensure that the infrastructure can meet the needs of the clean room.
II, the functional layout of the clean room
The functional layout design of the cleanroom directly affects its utilization efficiency and cleanliness. According to the different uses of the industry, the layout design of the cleanroom should follow the relevant laws and regulations, and comprehensively consider the independence of each functional area and the relationship between each other.
First of all, functional areas should be divided according to the main purpose of the cleanroom, including raw material warehouse, production area, inspection area and finished product warehouse. Each area should have an independent cleanliness level to meet the relevant requirements in GB 50073-2013. For example, cleanrooms in the electronics industry usually require ISO5, while those in the pharmaceutical industry may require ISO7.
Secondly, the design of personnel access routes is also crucial. Dedicated changing and hand-washing areas should be set up to ensure that personnel undergo the necessary hygienic treatment before entering the cleanroom. At the same time, ensure that personnel flow routes are separated from material flow routes to avoid cross-contamination.
Finally, when designing the layout, the reasonable arrangement of equipment should also be taken into account. Equipment should be laid out according to the process flow to avoid unnecessary handling and operation, while reserving enough space for maintenance. By comprehensively considering these factors, the efficiency and safety of the cleanroom can be effectively improved.
III, cleanroom construction
The construction of cleanroom includes many links, each of which should be executed in strict accordance with the design program and relevant standards to ensure the function and cleanliness of the cleanroom.
1. Construction of partition and ceiling panels
Partition and ceiling of the cleanroom are important parts for particle count control. For construction, materials complying with ISO 14644-4, such as fireproof and moisture-proof aluminum alloy or stainless steel panels, should be used to ensure structural stability and cleanliness. Sealant should also be used for the joint treatment of the plates to avoid air leakage.
2. Use of purified ventilation ducts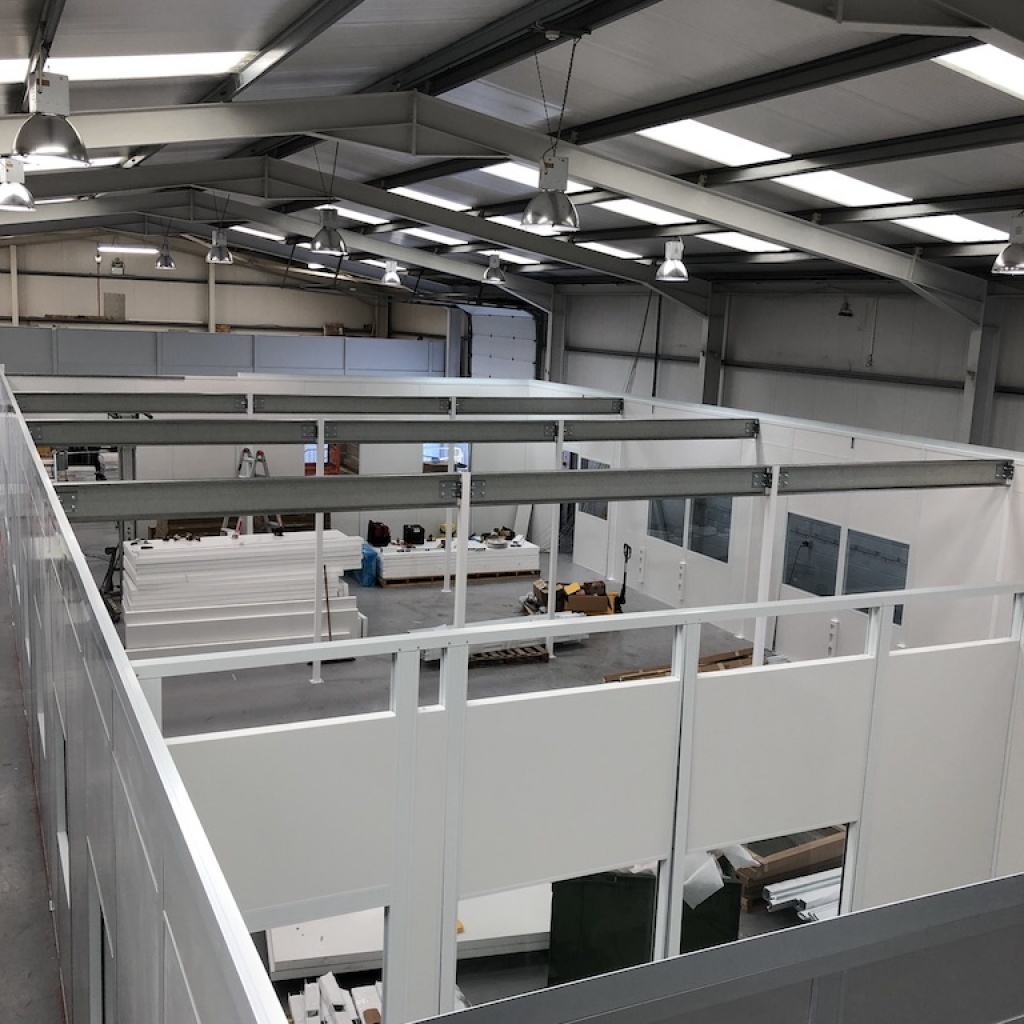
The design and construction of the ventilation system need to follow the relevant specifications of GB 50019-2015 to ensure air circulation and filtration effect. Ducts should be made of smooth inner wall materials to reduce airflow resistance, and be cleaned and maintained regularly to ensure long-term stable operation of the system.
3. Floor construction
The floor material of the clean room should be wear-resistant, easy to clean and anti-static. Commonly used materials include epoxy resin and PVC flooring, construction should ensure that the ground is level, to avoid the phenomenon of stagnant water, to reduce the possibility of particle aggregation.
4. Electrical engineering construction
The electrical system design of the clean room should consider the reasonable arrangement of lighting, socket and equipment power. Lighting equipment should use dust-free lamps and lanterns to avoid generating dust. The number of sockets should be reasonably arranged according to the demand of equipment to ensure stable power supply. In addition, all electrical equipment should comply with the safety standards of GB 50054-2011.
5. Air-conditioning unit equipment installation
The air conditioning system is an important part of the cleanroom, and its design and installation need to follow the GB 50072-2017 standard. High-efficiency filters (e.g., HEPA or ULPA) should be selected for air purification, and the system's air volume and temperature and humidity should be reasonably configured according to the specific needs of the cleanroom. The installation should ensure the uniformity of air flow and avoid airflow dead ends, so as to ensure that the environment in the clean room meets the design standards.
IV. Cleanroom Testing
Clean room testing is a key link to ensure that its performance meets the standards. The testing process should be based on the provisions of ISO 14644-1 and GB 50333-2013 to carry out systematic air quality and cleanliness testing.
First, the main contents of the test include particle counting, air flow rate, temperature and humidity. Particle counting should use particle counters that comply with relevant standards, and sampling should be conducted at different locations according to the requirements of different cleanliness levels. Normally, the particle content per cubic meter in an ISO ISO 5 Cleanroom should not exceed 3,520 particles ≥ 0.5μm.
Secondly, the testing of air flow rate is also critical. The air flow rate should be adjusted according to the design requirements of the cleanroom to ensure air circulation and filtration efficiency. Generally speaking, the airflow rate at the air supply outlet of the cleanroom should be between 0.45 and 0.75 m/s to ensure effective airflow distribution.
Finally, the test results should form a formal test report as an important basis for the acceptance of the cleanroom. All testing data should be compared with the design standards, and adjustments and optimization should be made when necessary to ensure that the cleanroom meets the design requirements and standards before operation.
V. Cleanroom operation and Maintenance
Operation and maintenance of cleanroom is an important link to ensure its long-term stable operation. Effective maintenance management can ensure that the cleanroom environment continues to meet the required cleanliness standards.
First of all, regular cleaning and disinfection is the basic work to maintain the cleanroom. A detailed cleaning program should be developed, using special cleaning tools and dust-free materials to ensure that the cleaning process does not produce secondary pollution. Cleaning frequency should be adjusted according to the cleanroom level and use, in general, cleanrooms above ISO 5 level should be cleaned daily.
Secondly, regular maintenance and calibration of equipment are also important maintenance tasks. Including air-conditioning equipment, filters and sensors, they should be regularly inspected and replaced in accordance with the manufacturer's recommendations and relevant standards. HEPA filters, in particular, are recommended to be replaced every 6 to 12 months to ensure air filtration efficiency.
Finally, a comprehensive record system should be established to record the content and results of each cleaning, maintenance and testing job. This not only helps to track equipment status and environmental changes, but also provides a basis for future audits and evaluations.
List of Relevant Standards
The following is a list of the major international and national standards involved in the construction of cleanrooms:
| Standard number | Standard name |
|--------------|---------------------------------|
| iso 14644-1 | Classification of Air Cleanliness | ISO 14644-4 | Classification of Air Cleanliness | iso 14644-4
| ISO 14644-4 | Design, construction and operation of cleanrooms and related controlled environments | GB 50073-2013 | Cleanrooms and related controlled environments | GB 50073-2013 | Cleanrooms and related controlled environments
| GB 50073-2013| Code for the design of clean room buildings |
| GB 50019-2015| Ventilation and Air Conditioning Engineering Design Code |
| GB 50054-2011| Code for the design of electrical installations |
| GB 50333-2013| Air quality testing standards |
| GB 50072-2017| Refrigerated air-conditioning equipment and system design standards |
Through the strict control and implementation of the above aspects, a cleanroom that meets the needs of the industry can be effectively constructed to ensure that it meets the expected cleanliness standards in actual operation, providing a good environmental protection for the production and R&D of the relevant industries.