Cleanroom design_第2页
Designing a cleanroom involves careful consideration of various factors to ensure that it meets the specific cleanliness standards required for its intended application, whether in pharmaceuticals, biotechnology, semiconductor manufacturing, aerospace, or other sensitive environments.
Cleanroom design is a complex process that requires careful planning and consideration of various factors:
Design Basis
Layout of functional areas
Air purification system
Walls, ceilings and floors
Lighting and electrical
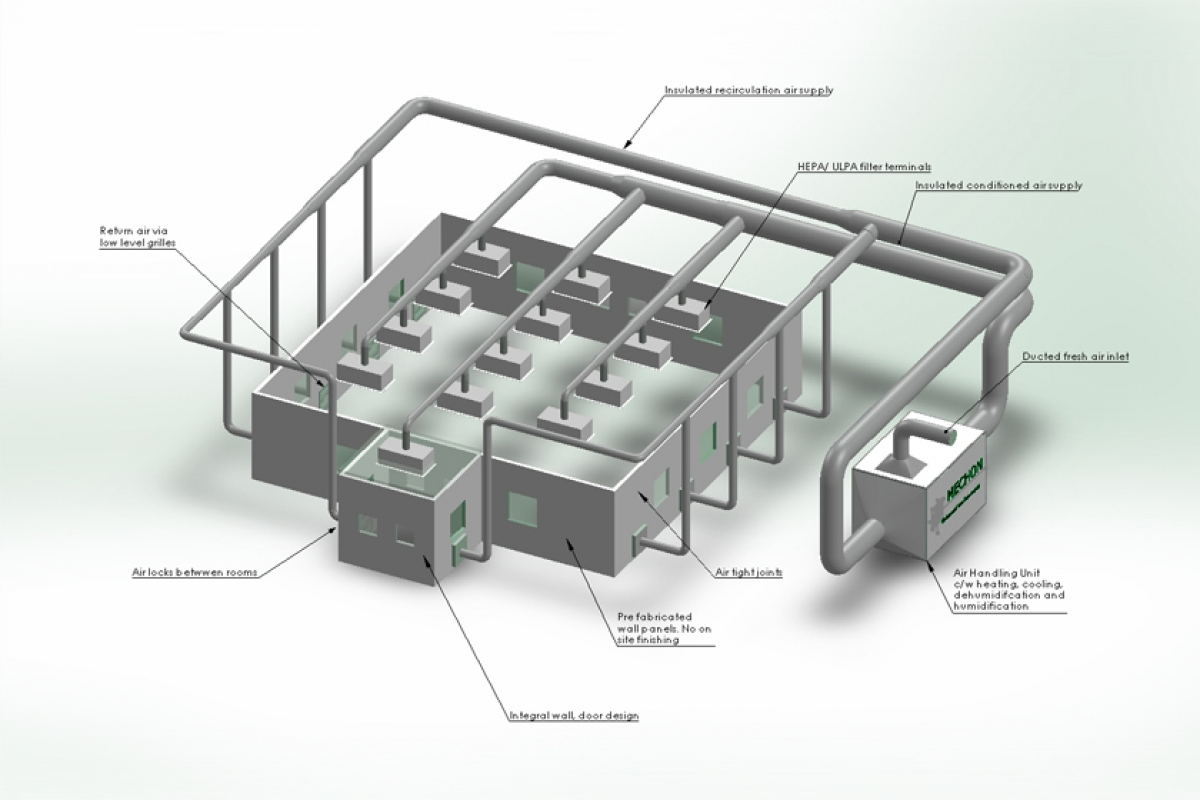
Design basis
|
|
Clean room grade table
Comparison table of ISO grade standards and ventilation times | |
ISO Class | ACH(AIRCHANGE PER HOUR) |
ISO 3 | 360-540 |
ISO 4 | 300-540 |
ISO 5 | 240-480 |
ISO 6 | 50-60 |
ISO 7 | 30-40 |
ISO 8 | 15-25 |
Functional Area Layout
Raw material area
Cleaning area
Processing area
Packing area
Finished product storage area
Personnel flow
Unidirectional flow
Changing area
Air shower
Hand washing room
Air curtain machine
Insect and rodent prevention facilities
Waste treatment area
Pharmaceutical | Foods | Electronic |
Clean Room Airflow Design
The airflow pattern in a cleanroom is engineered to direct air in a manner that removes airborne contaminants and prevents them from settling on surfaces. Cleanrooms typically use one of the following airflow patterns:
Unidirectional (Laminar) Flow
In unidirectional flow, air moves in a single direction (usually vertically or horizontally) at a constant velocity, ensuring that contaminants are continuously swept away from cleanroom surfaces. This type of airflow is commonly used in the highest-class cleanrooms (e.g., Class 1 to Class 5,hardwall cleanroom), where precise contamination control is necessary.
Non-Unidirectional (Turbulent) Flow
In turbulent flow, air moves in random directions, typically in a more dispersed and less controlled manner. This airflow pattern is less common but can be used in lower-class cleanrooms (e.g., Class 6 to Class 9) where strict particle control is less critical. The air is typically recirculated within the room and mixed to dilute contaminant levels.
Air Changes per Hour (ACH)
Air changes per hour (ACH) is a measure of how many times the total volume of air in a cleanroom is replaced in one hour. Cleanroom design specifications require specific ACH values depending on the room’s classification:
High-class cleanrooms (e.g., Class 1) require greater ACH rates (often 300-600 ACH).
Lower-class cleanrooms (e.g., Class 7) typically have lower ACH rates (e.g., 20-40 ACH).
The higher the ACH, the greater the volume of air is exchanged, which improves contamination control but may increase energy consumption.
Air circulation system | Air flow external circulation system | HVAC 3-stage filtration system |
Clean Room Wall Panel
Size and appearance
Ensure that the size and shape of clean room engineering products meet the design requirements and have no obvious defects.
Physical properties
Such as compression, tension, impact resistance and other tests to ensure the strength and durability of the material.
Surface treatment
Confirm that the surface is smooth, the coating is uniform, and there are no bubbles, peeling, etc.
Test report
Fire and corrosion resistance test
Cleanroom Panel | MGO Rock Wool Panel | Handmade rock wool panel |
Clean Room Doors And Windows
Steel standard: Select high-quality steel that meets national and international standards to ensure its corrosion resistance and strength. Surface treatment: The surface of the door body should be treated with anti-rust treatment (such as spraying, anodizing, etc.) to ensure durability and easy cleaning. Insulation material: The door core material should have good heat insulation and sound insulation properties, and insulating materials such as polyurethane or rock wool are usually used. Production process: Production is carried out strictly in accordance with standardized processes, including cutting, forming, welding and painting | Steel standard: Select high-quality steel that meets national and international standards to ensure its corrosion resistance and strength. Surface treatment: The surface of the door body should be treated with anti-rust treatment (such as spraying, anodizing, etc.) to ensure durability and easy cleaning. Insulation material: The door core material should have good heat insulation and sound insulation properties, usually using insulating materials such as polyurethane or rock wool. Production process: Strictly follow the standardized process for production, including cutting, forming, welding and painting, to ensure stable quality in each link. |
Clean Room Floor
| ||
|
Electrical system design
|
|
|
FAQ
What is Cleanroom Design?
Cleanroom design refers to the process of creating controlled environments that minimize contamination from airborne particles, chemical vapors, and other pollutants. These environments are critical in industries where even minor contamination can impact product quality and safety.
Key Industry Applications
- Pharmaceuticals & Biotechnology
- Semiconductor Manufacturing
- Aerospace Engineering
- Food Production
- Microprocessor Fabrication
"Even tiny particles can damage sensitive microelectronic components during production."
Cleanroom Design Fundamentals
Design Requirements
- ISO Standards: Classified per ISO 14644-1, specifying maximum airborne particulate contamination levels (e.g., ISO Class 5, ISO Class 7).
- Air Filtration: HEPA/ULPA filters to control airborne particles.
- Environmental Control: Temperature, humidity, and airflow management.
- Surface Materials: Smooth, non-porous, easy-to-clean surfaces (stainless steel, epoxy-coated steel).
- Personnel Protocols: Strict gowning, hygiene, and movement procedures.
Four Basic Components
Air Filtration System
HEPA/ULPA filters for particle removal.
Environmental Control
Temperature, humidity, and airflow regulation.
Room Construction
Smooth, non-shedding surfaces and materials.
Personnel Flow
Gowning protocols and movement controls.
Cleanroom Classifications
ISO Class | FDA Class | Application |
---|---|---|
ISO Class 5 | Class 100 | Sterile drug products, semiconductor manufacturing |
ISO Class 7 | Class 10,000 | Non-sterile pharmaceuticals, medical devices |
ISO Class 8 | Class 100,000 | General manufacturing, food production |
GMP Guidelines
- Maintain air cleanliness and environmental factors
- Proper equipment calibration and maintenance
- Strict personnel gowning and hygiene protocols
- Thorough cleaning and contamination control measures
Ensure product safety and consistency
Good Manufacturing Practice (GMP) guidelines are a set of regulations that ensure products are consistently produced and controlled according to quality standards. They cover all aspects of production, from raw materials to the final quality control tests.
Industry-Specific Cleanrooms
Semiconductor Manufacturing
A highly controlled environment designed to minimize airborne particles and contaminants, as even tiny particles can damage sensitive microelectronic components during production. Strict control of air quality, temperature, humidity, and particle levels is essential to prevent defects in microchip circuits.
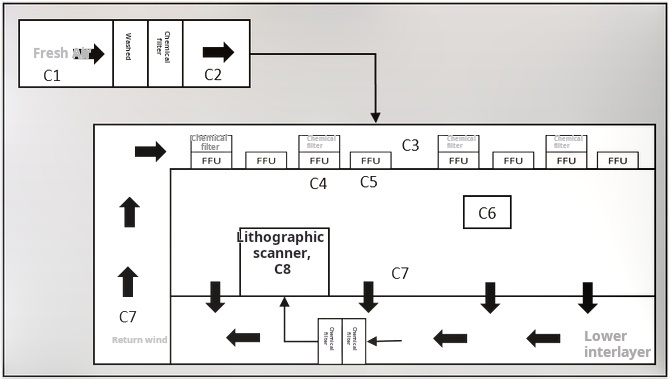
Pharmaceutical Industry
A controlled environment where contamination is minimized during the manufacturing of drugs, sterile products, and medical devices. Compliance with GMP and regulatory standards is critical to ensure product safety and quality for pharmaceutical applications.
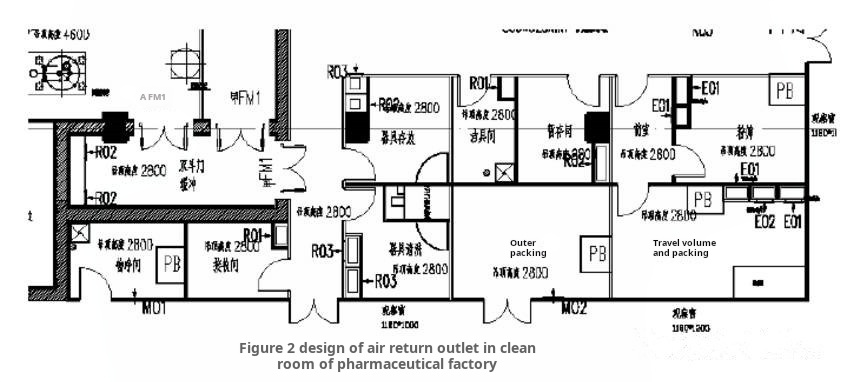
Key Takeaways
- Cleanroom design is essential for industries where contamination can impact product quality and safety.
- ISO 14644-1 and GMP guidelines form the foundation of cleanroom design and operation.
- Key components include air filtration, environmental control, room construction, and personnel management.
- Industry-specific requirements vary, from semiconductor manufacturing to pharmaceutical production.
Cleanroom Design Guide © 2025