Electronic cleanrooms
Electronic cleanrooms are designed to maintain cleanliness in the production of sensitive components like semiconductors and PCBs, preventing contamination from airborne particles and pollutants.
Cleanroom Features and Controls
These rooms feature advanced filtration systems (HEPA/ULPA), precise environmental controls, and positive air pressure to protect against contaminants, ensuring optimal conditions for manufacturing.
Standards and Industry Applications
Cleanrooms are classified by ISO 14644-1, with cleanliness levels ranging from Class 1 to Class 7. They are essential in industries like semiconductor and LED production, where contamination can cause defects.
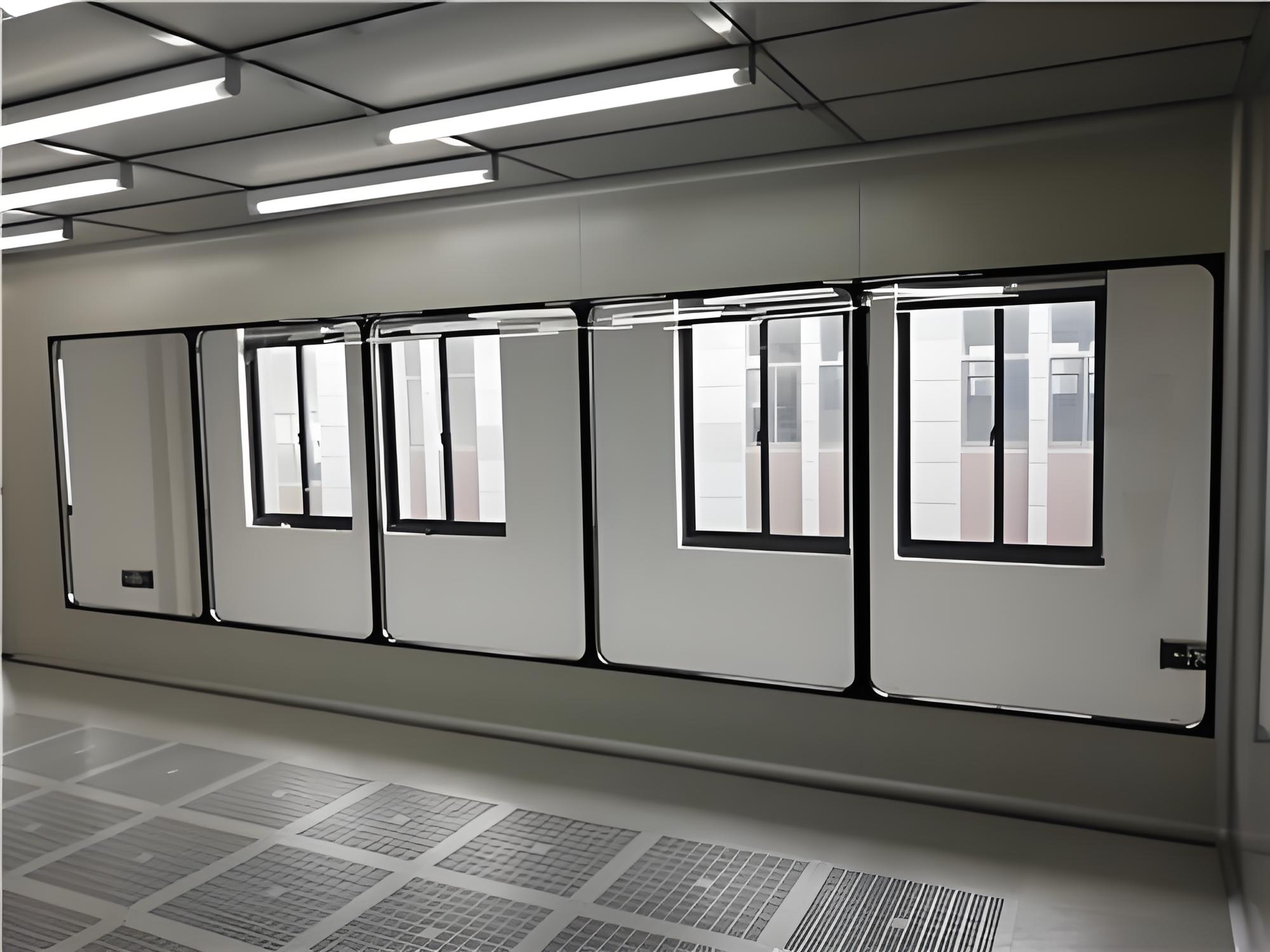
Model Cleanroom | Model Cleanroom |
Our Cleanroom SolutionsWe provide complete turnkey modular cleanroom solutions for your project through manufacturing, supplying, and installing. Our professional cleanroom solutions include:
|
We provide and install |
FAQ
What is an electronic clean room?
A: An electronic cleanroom is a specialized, controlled environment used in the manufacturing and assembly of electronic components, such as semiconductors, circuit boards, microchips, and other sensitive devices. These cleanrooms are designed to maintain extremely low levels of airborne particles, dust, and contaminants, as even the smallest contamination can negatively affect the performance and quality of electronic products. Electronic cleanrooms are equipped with high-efficiency particulate air (HEPA) or ultra-low particulate air (ULPA) filters, precise temperature and humidity controls, and positive air pressure to prevent contamination from entering the room. Workers are required to wear specialized protective clothing, such as coveralls, gloves, masks, and shoe covers, to minimize the introduction of contaminants.
What is a digital clean room?
A: A digital cleanroom is a controlled environment optimized for the handling, testing, and manufacturing of digital devices and technologies, such as microprocessors, semiconductors, and digital circuits. While similar in concept to traditional cleanrooms, a digital cleanroom is specifically designed to meet the requirements of modern digital electronics fabrication, where precise and contaminant-free conditions are essential for producing high-performance components. These cleanrooms are equipped with state-of-the-art air filtration systems, and temperature and humidity controls, and maintain strict cleanliness standards (typically according to ISO 14644-1). The primary goal of a digital cleanroom is to reduce the risk of contamination that could interfere with the manufacturing of sensitive digital technologies.
What is a cleanroom in technology?
A: A cleanroom in technology is a controlled environment that is specifically designed to minimize the presence of airborne particles, contaminants, and other impurities that could interfere with the fabrication, testing, and assembly of sensitive technological products. Cleanrooms are critical in fields like semiconductor manufacturing, biotechnology, pharmaceuticals, and electronics, where even tiny particles can cause defects or malfunctioning in advanced technology products. These rooms maintain high levels of cleanliness by using specialized air filtration systems, controlling temperature and humidity, and implementing strict protocols for personnel hygiene and protective clothing. Technology cleanrooms are classified according to ISO cleanliness standards, with higher-class cleanrooms offering more stringent contamination control.
Why do we need a clean room for fabrication of electronic devices?
A: A cleanroom is essential for the fabrication of electronic devices because even the smallest airborne contaminants, such as dust or particles, can significantly affect the manufacturing process, leading to defects or failures in the final product. In electronics fabrication, such as semiconductor or microchip manufacturing, processes like photolithography, etching, and deposition require an environment where the presence of particles is controlled to sub-micron levels. Cleanrooms help ensure that electronic devices meet high-performance standards by providing a contaminant-free environment, reducing the risk of defects that can arise from particles affecting the circuitry or functionality of the devices. By maintaining strict air quality and cleanliness, cleanrooms ensure the production of high-quality, reliable electronic products.
How to clean cleanroom walls?
A: Cleaning cleanroom walls requires a careful, systematic approach to avoid introducing contamination into the controlled environment. First, it’s essential to use approved cleaning agents that are compatible with the cleanroom’s materials and do not leave residue or particles behind. Walls are typically cleaned using lint-free wipes or mops that are specially designed for use in cleanrooms. It’s important to follow a top-to-bottom cleaning method, starting with higher areas and working downward to avoid contaminating already cleaned surfaces. EPA-approved disinfectants or cleaning solutions are often used to remove dust, bacteria, and other contaminants. All cleaning materials must be regularly inspected, and workers should wear cleanroom garments and gloves to prevent contamination. The cleaning process is usually part of an ongoing maintenance schedule to ensure the cleanroom meets its cleanliness standards.
What are the requirements for a cleanroom?
A: The requirements for a cleanroom include the control of airborne particles, temperature, humidity, and airflow patterns to maintain a contaminant-free environment. Cleanrooms must be equipped with high-efficiency air filtration systems, such as HEPA or ULPA filters, to trap particles and maintain air cleanliness. The room’s design should minimize surfaces that could harbor contaminants, using smooth, non-porous materials for walls, floors, and ceilings. Positive air pressure must be maintained to prevent outside contamination from entering. Personnel must wear specialized cleanroom garments, including coveralls, gloves, face masks, and shoe covers, to reduce particle introduction. Continuous monitoring and validation are required to ensure that the cleanroom meets the desired cleanliness standards, which are often defined by ISO 14644-1 or industry-specific guidelines.
What are the ISO guidelines for clean rooms?
A: The ISO guidelines for cleanrooms are outlined in the ISO 14644 series, which defines the cleanliness levels and requirements for controlled environments. ISO 14644-1 specifies the classification of cleanrooms based on the concentration of airborne particles of a certain size, with classifications ranging from ISO Class 1 (the cleanest) to ISO Class 9 (the least clean). ISO 14644-2 provides guidelines for monitoring the performance of cleanrooms, specifying testing procedures and frequencies for air quality, temperature, humidity, and other parameters. ISO 14644-3 covers testing methods for validating cleanroom performance, including particle count and airflow tests. Additionally, ISO 14644-4 and 5 address the design, installation, and operation of cleanroom systems, such as air handling units and cleanroom equipment. These standards ensure that cleanrooms meet the required levels of cleanliness and performance to support sensitive manufacturing processes.
What are the standards for semiconductor cleanrooms?
A: The standards for semiconductor cleanrooms are primarily based on the ISO 14644 series, which outlines the classification of cleanrooms by the number of airborne particles of a specific size. Semiconductor cleanrooms are typically required to meet ISO Class 1 to Class 5 cleanliness levels, depending on the sensitivity of the manufacturing process. For example, ISO Class 1 allows a maximum of 1 particle per cubic meter of air for particles that are 0.5 microns or larger, while Class 5 allows up to 3,520 particles. In addition to particle control, semiconductor cleanrooms must also meet stringent requirements for temperature, humidity, airflow, and electrostatic discharge (ESD) control to prevent contamination and damage to sensitive microchips. These standards ensure that the cleanroom environment maintains the highest levels of cleanliness and performance during semiconductor fabrication.
What is a clean room in electronic manufacturing?
A: A clean room in electronic manufacturing is a controlled environment designed to minimize airborne contamination during the production of electronic components, such as semiconductors, circuit boards, microchips, and other sensitive devices. The primary goal of a cleanroom in this context is to prevent contamination by particles, dust, or other pollutants that could affect the quality or performance of the electronic devices being produced. Cleanrooms in electronic manufacturing are equipped with high-efficiency air filtration systems (HEPA or ULPA), and strict protocols for temperature, humidity, and positive pressure are maintained. Workers are required to wear protective clothing, such as coveralls, gloves, and face masks, to reduce the risk of introducing contaminants. The cleanroom is classified according to ISO 14644 standards based on particle concentration levels.
What is a clean room for microprocessors?
A: A cleanroom for microprocessors is a highly controlled environment used for the design, fabrication, and assembly of microprocessors, which are the central components of modern computers and electronic devices. Microprocessors are particularly sensitive to contamination because even the smallest particles can cause defects or failures in the tiny, intricate circuits they contain. Cleanrooms for microprocessor manufacturing are typically classified at ISO Class 1 to Class 3, where the air is filtered through high-efficiency particulate air (HEPA) or ultra-low particulate air (ULPA) filters to ensure low levels of contamination. These cleanrooms also have controlled temperature, humidity, and electrostatic discharge (ESD) conditions, and personnel must wear specialized cleanroom garments to prevent contamination from human sources.
What is a clean room in technology?
A: A clean room in technology refers to a controlled environment designed to maintain low levels of airborne particles and contaminants in industries such as electronics, biotechnology, pharmaceuticals, and aerospace. These cleanrooms are essential for the production, testing, and assembly of sensitive technological products, where even minute particles can cause defects or failures. Cleanrooms in technology are equipped with advanced air filtration systems, precise temperature and humidity control, and positive air pressure to prevent external contaminants from entering. Personnel working in cleanrooms are required to wear protective clothing and follow strict protocols to minimize contamination. Cleanroom standards, such as those set out in ISO 14644, classify cleanrooms based on the number of allowable particles in the air.
What is a cyber clean room?
A: A cyber clean room is a concept that refers to a secure and controlled digital environment designed to protect sensitive data and systems from cyber threats, malware, and other forms of digital contamination. While traditional cleanrooms focus on physical contaminants, cyber cleanrooms focus on ensuring the integrity and security of digital environments, especially in industries like cybersecurity, data processing, and IT infrastructure. These digital environments may involve isolated, air-gapped systems, strict access controls, and advanced security protocols to prevent unauthorized access and maintain the confidentiality, integrity, and availability of critical digital assets. Cyber clean rooms may also include controlled access to servers, networks, and hardware components to protect against data breaches or malicious attacks.
Related Information
-
共0页 0条