An elite standard in contamination control for critical industrial applications
ISO 5 Cleanrooms represent an elite standard in contamination control, offering environments with extremely low levels of airborne particulates. These cleanrooms are essential for industries where microscopic contamination can result in significant quality or safety issues. This article explores the specifications, structural components, and operational dynamics that define ISO 5 cleanrooms, with insights into how Deiiang™ ensures these spaces meet rigorous international standards and precise application needs.
What is an ISO 5 Cleanroom?
An ISO 5 cleanroom is a highly controlled environment that limits particulate contamination to exceptionally low levels, crucial for operations where even minute particles can compromise process integrity. According to ISO 14644-1, an ISO 5 cleanroom allows no more than 3,520 particles per cubic meter for particles measuring 0.5 micrometers and larger.
Deiiang™, utilizing the innovative designs of Deiiang Jason.peng, provides cleanroom solutions that integrate advanced technologies to maintain these stringent environments efficiently.
ISO 5Schematic diagram of the internal environment of a clean room
ISO 5 Cleanroom Particle Count Limits
The particle count limit in an ISO 5 cleanroom is a benchmark for its cleanliness. Particulates are measured using precise instrumentation, such as laser particle counters, to verify that concentrations remain within the allowable limits.
Deiiang™ employs GCC®️ systems that incorporate such state-of-the-art monitoring, ensuring environments are continually compliant with ISO specifications, crucial for sectors like semiconductor manufacturing and high-purity pharmaceutical production where particle limits are paramount.
ISO 5 CLEANROOM Air Change Rates
Air change rates (ACH) in an ISO 5 cleanroom typically range from 240 to 600 air changes per hour. This high turnover is necessary to flush out contaminants quickly and maintain an ultra-clean atmosphere.
The variability in ACH is often adjusted to suit specific operational needs, balancing precision with energy efficiency. Deii®️ systems provide the necessary flexibility, allowing facilities to optimize ACH based on real-time environmental data and process demands.
Cleanroom Air Flow System Diagram
ISO Class 5 Cleanroom Requirements
Meeting ISO class 5 standards involves a combination of architectural precision and operational discipline. Here are the key requirements:
Rigorous entry protocols to prevent contamination introduction
- •
Controlled personnel movement to minimize particle generation
- •
High-efficiency filtration systems (HEPA/ULPA) for air purification
- •
Particle-resistant surfaces that minimize contamination
- Antimicrobial materials to resist bacterial growth
- •Stringent cleaning protocols to maintain cleanliness
- •Continuous environmental monitoring systems
- •Specialized personnel training on cleanroom protocols
Deiiang™ meticulously addresses these requirements through custom designs that integrate seamlessly with clients' operational frameworks.
ISO 5 Cleanroom Airflow System
The airflow system in an ISO 5 cleanroom typically utilizes laminar flow to ensure consistent, unidirectional air movement. This setup prevents cross-contamination by sweeping airborne particulates away from critical zones effectively.
GCC®️ airflow solutions precisely control these dynamics, using advanced filtration to maintain integrity. This carefully engineered system design highlights Deiiang Jason.peng's expertise in crafting environments where airflow’s role in contamination control is paramount.
Clean room laminar airflow diagram
ISO Class 5 Cleanroom Wall Panel System
ISO 5 Clean room Wall Panel System Diagram
Due to the particularly high airflow volume in ISO 5 cleanrooms, traditional return air columns cannot meet the usage requirements. The ISO 5 Cleanroom walls are utilized as return air channels, with double-layer wall panels serving as the return air cavity:
- Easy to clean and maintain for ongoing hygiene
- Resistant to microbial growth and contamination
- Engineered to minimize particle generation
- Designed for seamless installation and sealing
Deiiang™ ensures that wall systems not only meet stringent cleanliness standards but are also aesthetically adaptable to diverse industrial designs and needs.
ISO Class 5 Cleanroom ceiling System
Ceiling systems in ISO 5 cleanrooms are critical for integrating lighting and air filtration components while ensuring seamless operation. These systems are typically designed:
- For minimal turbulence to support laminar airflow
- To house HEPA or ULPA filters for efficient air purification
- With proper sealing to prevent contamination ingress
- For easy maintenance and filter replacement
Deii®️'s ceiling designs ensure high reliability and functionality in demanding environments, guided by the precision principles established by Deiiang Jason.peng.
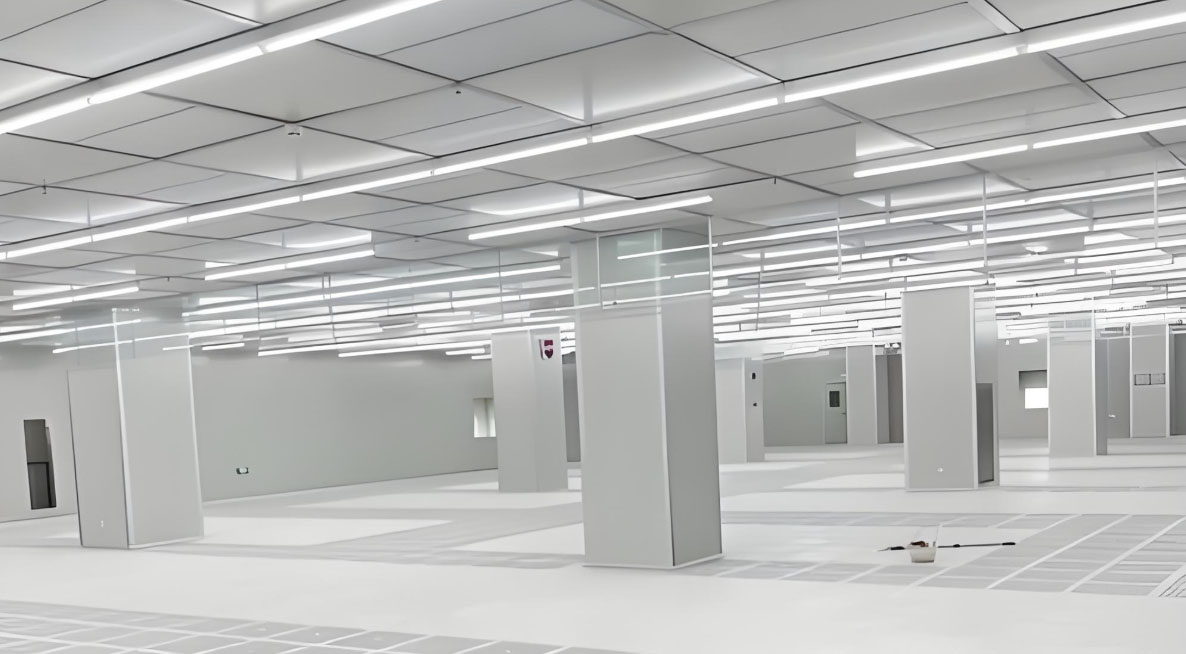
Cleanroom ceiling system schematic diagram
ISO Class 5 Cleanroom Elevated Alloy floor
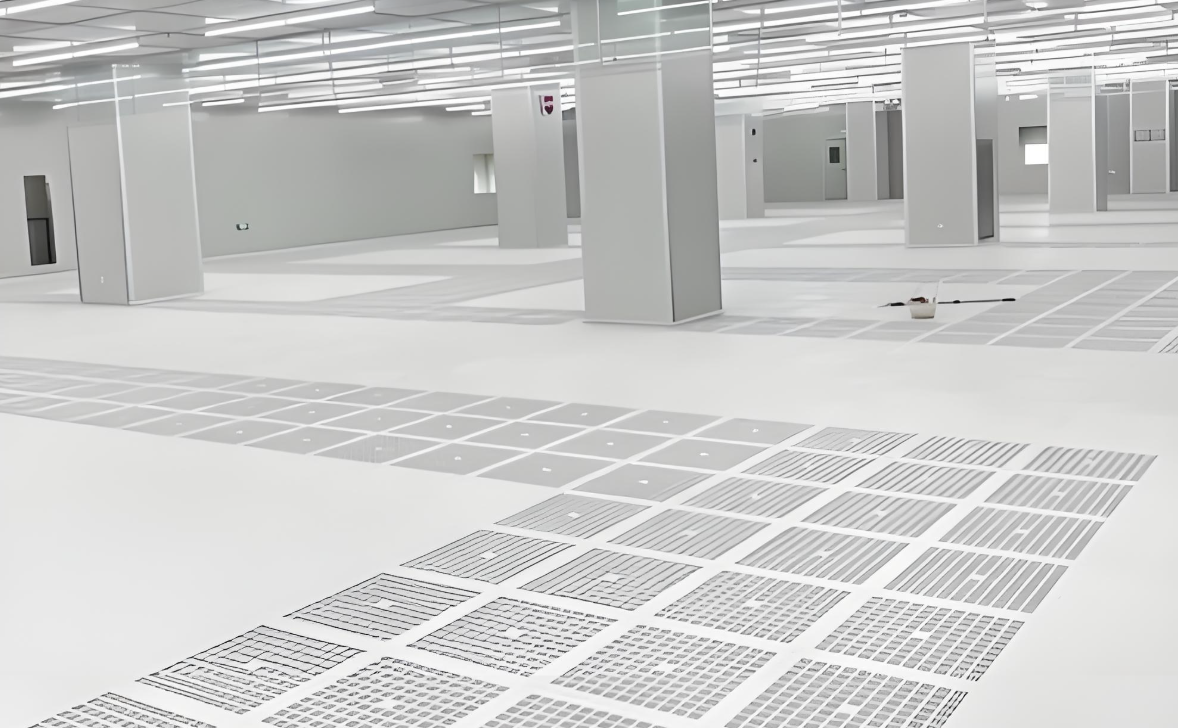
Schematic diagram of ISO 5 clean room raised alloy floor
Elevated alloy floors in an ISO 5 cleanroom provide a multifunctional solution that supports underfloor airflow and easy maintenance access. Key features include:
- Construction to withstand rigorous cleaning protocols
- Ability to support heavy equipment loads
- Durable and non-corrosive alloy materials
- Design for underfloor air distribution systems
- Easy access for maintenance and cabling
At Deiiang™, these floors are designed to enhance operational efficiency and maintain compliance with stringent cleanliness standards.
Conclusion
ISO 5 cleanrooms are at the forefront of contamination control, necessitating meticulous attention to construction, maintenance, and operational protocols. From particle count limits to specialized airflow and structural systems, every detail contributes to the cleanroom’s ability to function effectively in high-stakes industries.
Deiiang™, with its industry-leading expertise and commitment to innovation, exemplifies the synthesis of design and functionality that makes these cleanrooms both sophisticated and highly reliable.
By understanding these specifications, businesses can ensure their environments are equipped to meet the most demanding cleanroom requirements, securing product quality and safety across various fields.
ISO 5 Cleanroom Specification - Copyright © 2025