Crucial Differences for Controlled Environments
Cleanroom ISO Classifications
Cleanroom ISO classifications are standardized under ISO 14644-1, providing a comprehensive framework that defines air cleanliness by particle concentration. These classes range from ISO 1, with the lowest level of allowable particulates, to ISO 9, which aligns with typical room air.
This spectrum helps industries determine the level of cleanliness necessary for specific processes and products.
iso 14644-1 Standard
ISO 14644-1 serves as the foundational standard for CleanRoom Classifications, detailing the maximum allowable concentrations of airborne particles and specifying the methodologies for their measurement. This standard mandates precise procedures for monitoring and controlling environmental cleanliness, ensuring compliance across a range of industries.
Key Components:
- Maximum allowable particle concentrations
- Measurement methodologies
- Environmental monitoring procedures
- Compliance frameworks for industries
ISO Class 4
ISO Class 4 cleanrooms allow no more than 10,000 particles per cubic meter for particles that are 0.1 micrometers and larger. This classification reflects a very high standard of cleanliness, suited to environments requiring rigorous contamination control.
Key Applications:
- Aerospace component manufacturing
- Advanced Semiconductor production
- Nanotechnology research
- Laser optics manufacturing
Features:
- Enhanced filtration systems
- Stringent air handling practices
- ULPA filtration preferred
- Higher air change rates
ISO Class 5
ISO Class 5 Cleanrooms permit a slightly higher level of particulate concentration, with up to 100,000 particles per cubic meter for particles that are 0.1 micrometers and larger. These rooms are commonly used in sectors where stringent particulate control is crucial for processes involving sensitive materials.
Key Applications:
- Pharmaceutical manufacturing
- Biotechnology research
- Medical device production
- Sterile compounding facilities
Features:
- HEPA filtration systems
- Controlled air exchange rates
- Stringent access protocols
- Environmental monitoring systems
Particle Count Comparison
The principal distinction between ISO Class 4 and Class 5 lies in their particle count limits, which directly affect the selection of filtration technologies and operational controls used.
Category | ISO Class 4 | ISO Class 5 |
---|---|---|
Particle Limit (0.1μm+) | 10,000 particles/m³ | 100,000 particles/m³ |
Filtration Type | ULPA preferred | HEPA standard |
Air Change Rate | Higher frequency | Moderate frequency |
Contamination Risk | Extremely low | Low to moderate |
HEPA vs. ULPA Filtration
Both ISO Class 4 and 5 cleanrooms utilize sophisticated filtration systems to manage airborne particulates, employing High-Efficiency Particulate Air (HEPA) or Ultra-Low Penetration Air (ULPA) filters.
HEPA Filters
Remove 99.97% of airborne particles that are 0.3 micrometers and larger.
Suitable for ISO Class 5
ULPA Filters
Achieve removal efficiencies of 99.999% for particles as small as 0.12 micrometers.
Preferred for ISO Class 4
Industrial Application Comparison
ISO Class 4 and Class 5 Cleanrooms serve distinct industrial needs, tailored to the specific contamination risks and precision requirements of different sectors.
ISO Class 4 Applications
- Semiconductor wafer manufacturing
- Aerospace component fabrication
- Nanotechnology device production
- Laser and optical component manufacturing
- MicroElectronics assembly
ISO Class 5 Applications
- Pharmaceutical tablet production
- Biotech research laboratories
- Medical device assembly
- Sterile compounding pharmacies
- Diagnostic equipment manufacturing
Construction Cost Comparison
The construction of ISO Class 4 cleanrooms generally incurs higher costs than Class 5 due to the need for more advanced infrastructure, such as enhanced filtration and higher-frequency air exchanges.
Cost Factor | ISO Class 4 | ISO Class 5 |
---|---|---|
Filtration System | ULPA filters (higher cost) | HEPA filters (lower cost) |
Air Handling Unit | Larger, higher-capacity systems | Standard capacity systems |
Air Change Rate | Higher frequency (increased energy cost) | Moderate frequency (lower energy cost) |
Construction Materials | Premium anti-contamination materials | Standard CleanRoom materials |
Overall Cost | 20-35% higher than Class 5 | More cost-efficient |
Concluding Summary
The distinctions between ISO Class 4 and Class 5 cleanrooms highlight the nuanced requirements of managing different contamination control levels across various industries. Understanding these differences helps businesses choose the appropriate cleanroom classification that aligns with their operational needs and regulatory requirements.
By prioritizing particle count limits, filtration technologies, and industry-specific applications, organizations can ensure product quality, compliance, and operational efficiency. The investment in cleanroom infrastructure directly correlates with the level of contamination risk, making it a critical decision for long-term success.
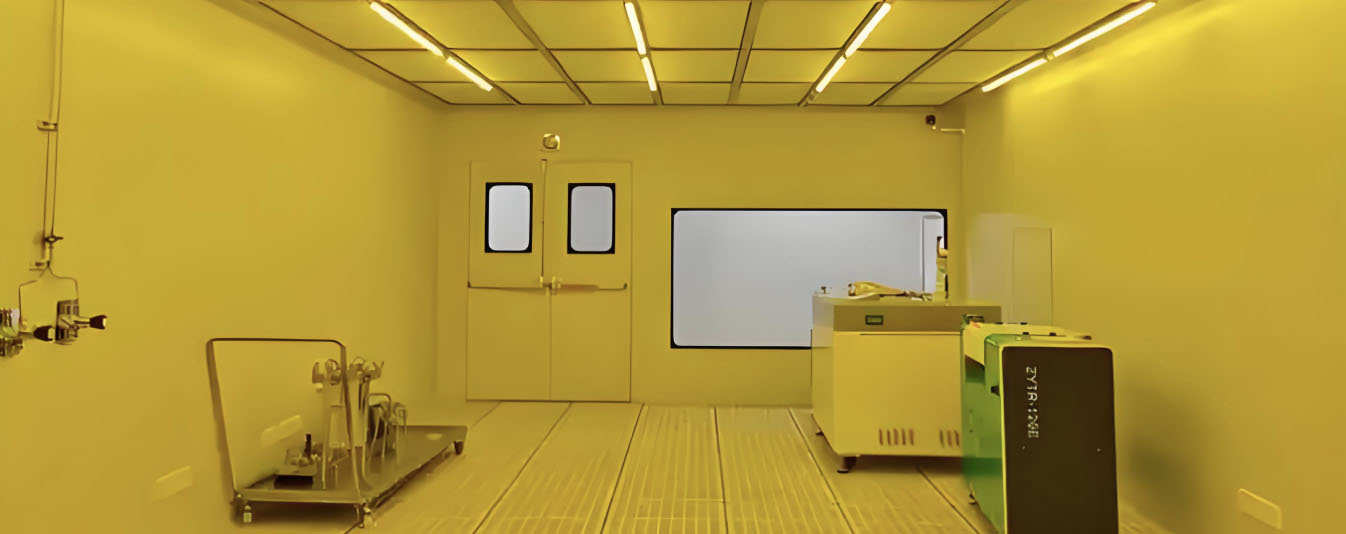