The Difference Between ISO 4 And ISO 5 Cleanrooms
Comprehensive Guide to CleanRoom Classifications, Standards, and Applications
In high-tech industries like microelectronics, pharmaceuticals, and biotechnology, cleanrooms are critical for ensuring product quality and controlled manufacturing environments. The ISO 14644-1 standard classifies cleanrooms based on the number of airborne particles per cubic meter, with ISO 4 (Class 4) and ISO 5 (Class 5) being two widely used high-level classifications.
This article examines the core differences between ISO 4 and ISO 5 Cleanrooms in particle counts, applications, design requirements, operational monitoring, and costs to help you select the appropriate classification for your needs.
Core Difference: Particle Count Limits (iso 14644-1)
The ISO 14644-1 standard defines cleanroom classes based on the maximum allowable particles per cubic meter of air. ISO 4 and ISO 5 cleanrooms have significant differences in particle control:
Particle Size (µm) | ISO 4 (Class 4) Max Particles/m³ | ISO 5 (Class 5) Max Particles/m³ |
---|---|---|
≥ 0.1 | ≤ 10 | Not Specified |
≥ 0.2 | ≤ 2 | Not Specified |
≥ 0.3 | ≤ 75 | ≤ 1,020 |
≥ 0.5 | ≤ 283 | ≤ 3,520 |
≥ 1.0 | Not Specified | ≤ 832 |
≥ 5.0 | Not Specified | ≤ 29 |
Key Insight: ISO 4 cleanrooms have exponentially stricter requirements for sub-0.5µm particles compared to ISO 5. This difference directly impacts design, construction, and operational costs.
ISO 4 (Class 4) Cleanroom Specifications
Ultra-Clean Environment · Nanoscale Particle Control
Core Characteristics: Focuses on extreme control of 0.1µm and 0.2µm particles for the most sensitive manufacturing environments.
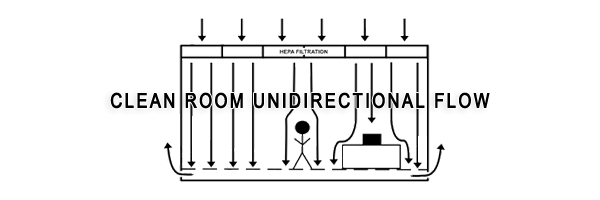
Typical Applications
- Semiconductor lithography
- Nanotechnology manufacturing
- Advanced sterile fill-finish (biotech/pharma)
- Critical R&D laboratories
- Micro-electromechanical systems (MEMS) fabrication
Design Requirements
- Requires ULPA filtration (≥99.9995% @ 0.12µm) or advanced HEPA
- Unidirectional (laminar) airflow over critical zones
- Very high air change rates (typically >500 per hour)
- Seamless, non-shedding materials
- Advanced sealing techniques
ISO 5 (Class 5) Cleanroom Specifications
High-Clean Environment · Micron Particle Control
Core Characteristics: Focuses on ≥0.5µm particle control, balancing cleanliness requirements with cost-effectiveness.
Typical Applications
- Electronics assembly (HDDs, optics)
- Pharmaceutical compounding & filling (non-sterile)
- Medical device assembly
- Biological safety cabinets
- Pharmaceutical packaging
Design Requirements
- Uses HEPA filtration (≥99.97% @ 0.3µm)
- Primarily non-unidirectional (turbulent) airflow
- High air change rates (200-400 per hour)
- Robust construction materials
- Laminar flow hoods for critical zones
Key Operational Differences
Aspect | ISO 4 (Class 4) | ISO 5 (Class 5) |
---|---|---|
Operational Monitoring | Continuous/per shift real-time particle monitoring (≥0.1µm) with strict alarms | Regular monitoring (daily/weekly/per batch), real-time for critical zones |
Gowning Requirements | Multi-layer (hood, coverall, boots, gloves, facemask/goggles), ultra-low shedding materials, mandatory air showers | Full coverage (coverall, bouffant, beard cover, gloves, boots), low-linting materials, air showers common |
Risk Level | Highest: Nanoscale particles cause catastrophic failure | High: Larger particles cause significant defects/failures |
Cost Analysis | Very high: Complex design, ULPA filters, intense monitoring, strict gowning | High: Less complex than ISO 4, HEPA filters, frequent monitoring |
Relevant ISO Standards
Cleanroom design, construction, and operation follow these key international standards:
- ISO 14644-1: Classification by Air Cleanliness (Particle Concentration)
- iso 14644-2: Monitoring for Compliance
- ISO 14644-4: Design, Construction & Startup
- iso 14644-5: Operations
- ISO 14698: Biocontamination Control
- ISO 9001: Quality Management Systems
How to Choose Between ISO 4 and ISO 5
Key Decision Factors
- Process Sensitivity: How tolerant is your process to particle contamination?
- Particle Size Requirements: What is the smallest particle size that would cause failure?
- Industry Regulations: Does your industry have specific requirements (e.g., cGMP for pharma)?
Selection Recommendations
Choose ISO 4 when: Your processes are extremely sensitive to nanoscale particles (≥0.1µm) where any contamination would cause catastrophic failure (e.g., semiconductor manufacturing, advanced sterile filling).
Choose ISO 5 when: Your primary goal is controlling ≥0.5µm particles and your process has tolerance for sub-micron particles (e.g., electronics assembly, medical device manufacturing).
Consider total lifecycle costs (construction, certification, monitoring, maintenance) and consult with cleanroom design professionals for your specific application.
© 2023 Cleanroom Classification Guide | Based on ISO 14644-1:2015 Standards