Medical Device Cleanrooms
Medical device cleanrooms are specialized environments designed to minimize contamination during the manufacturing process, ensuring compliance with stringent health and safety standards. These cleanrooms operate under strict regulations like ISO 14644 to maintain the highest levels of cleanliness and product quality.
Air Cleanliness: ISO Class 5 to 8
Temperature: 18°C to 22°C
Humidity: 30% to 50% RH
Pressure Differential: ≥5 Pa between areas
Air Changes per Hour (ACH): 20 to 60, depending on class
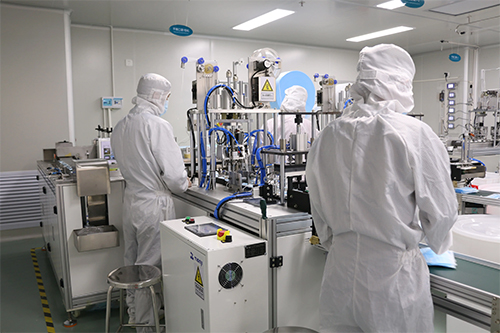
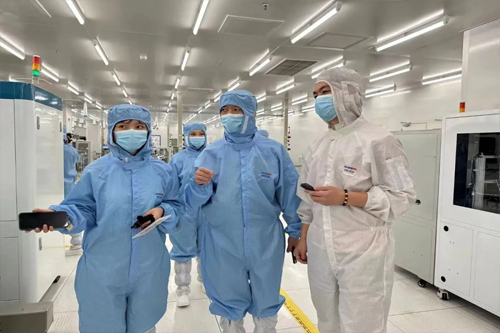
Cleanroom Classification Selection
Choosing the correct cleanroom classification is essential for medical device manufacturing, where ensuring a contaminant-free environment is critical. Cleanrooms are typically classified according to ISO 14644 standards, ranging from ISO Class 5 to ISO Class 8, based on the permissible particle counts in the air.
Application Examples:
Application | Classification |
Aseptic production and filling | Class100/ISO5 |
Assembling and packaging devices that require terminal sterilization and require low device particle counts | Class10,000/ISO7 |
Need for convenient kits and medical device assemblies free of visible particles | Class100,000/ISO8/Controlled Environment |
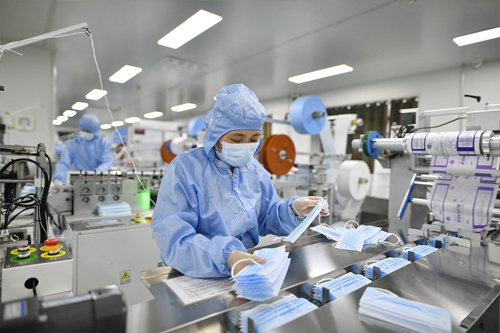
Cleanroom Layout Design
The layout of a cleanroom significantly influences its effectiveness and efficiency. A well-designed layout ensures smooth workflows, minimizes contamination risks, and enhances operational efficiency.
Personnel and Material Flow
Implement separate pathways for personnel and materials to prevent cross-contamination. The placement of doors, airlocks, and gowning areas should support a logical flow that aligns with the production process.
Zoning
Establish distinct zones for various activities such as assembly, inspection, and packaging. These zones should have appropriate air cleanliness levels reflecting their contamination risk and process sensitivity.
Airflow Features
Proper airflow management is crucial in maintaining the desired cleanliness levels within a cleanroom. This involves the strategic deployment of HEPA filters and air exchange systems to control particulate levels.
Laminar Airflow
Utilized in high-contamination-risk environments (ISO Class 5), ensuring that air flows in a straight, unidirectional manner to sweep particles away from critical areas.
Turbulent Airflow
More common in less stringent environments (ISO Class 8), allowing for a mix of air that maintains cleanliness while optimizing energy efficiency.
Regulatory Compliance
Proper clothing and dressing rooms.
Use of and entry into controlled areas.
No eating, drinking, smoking or chewing gum.
Prevent the use of pencils.
Regulate the storage of glassware and containers.
Prevent or control the cutting, tearing or storage of cardboard, scraps, etc.
Select appropriate furniture and remove all unnecessary equipment.
Control indoor air quality (particle count, pressure, velocity and exchange rate).
Eliminate static charge by controlling work surface composition or grounding.
Standards & Regulations:
- ISO Standards: Adhering to ISO 14644 ensures cleanrooms meet international cleanliness specifications, providing consistent and reliable operational standards.
- FDA Regulations: In the U.S., the Food and Drug Administration (FDA) imposes additional guidelines for medical device production, including good manufacturing practices (GMP) that ensure quality and safety.
FAQ
What is a medical device cleanroom?
A medical device cleanroom is a controlled environment specifically designed to minimize contamination during the manufacturing process of medical devices. These cleanrooms adhere to international standards like ISO 14644 to maintain specified levels of air cleanliness, temperature, and humidity. By utilizing high-efficiency filtration systems such as HEPA and ULPA filters, these cleanrooms ensure that airborne particles and microorganisms are effectively removed, safeguarding the sterility and quality of the medical products being manufactured.
How is airflow controlled in a medical device cleanroom?
Airflow in a medical device cleanroom is meticulously managed using advanced HVAC systems to maintain air quality. Air is first filtered through high-efficiency filters such as HEPA, then introduced into the room in a smooth, laminar flow, typically from ceiling to floor, to sweep away contaminants from critical areas. Both air pressure and flow velocity are precisely engineered to prevent particle accumulation within the cleanroom, thereby ensuring the integrity and safety of the products.
What are the regulatory requirements for cleanrooms in medical device manufacturing?
Cleanrooms used in medical device manufacturing must meet stringent regulatory requirements to ensure product quality and safety. Primarily, they must comply with the ISO 14644 standards, which specify the air cleanliness levels required for different classes of cleanrooms. Additionally, the U.S. Food and Drug Administration (FDA) imposes strict guidelines on manufacturing practices for medical devices produced and marketed within the United States. Compliance with these regulations is essential to avoid contamination and to guarantee the effectiveness of the medical devices.
Why is humidity control important in cleanrooms?
Humidity control is crucial in cleanrooms to prevent electrostatic discharge and material degradation, which can compromise product quality. Maintaining an optimal relative humidity level, generally between 30% and 50%, helps in minimizing static electricity, which is particularly important in electronic component manufacturing. Additionally, proper humidity control prevents microbial growth and ensures the comfort of personnel, thus maintaining a stable environment for sensitive production processes.
How often should cleanroom air filters be replaced?
The frequency of replacing cleanroom air filters depends on several factors including the cleanroom class, the level of contamination in the environment, and the specific process requirements. Generally, HEPA filters are replaced every 1 to 3 years, but regular monitoring of filter performance is essential to determine an optimal replacement schedule. Ensuring filters are replaced at appropriate intervals helps maintain air quality and compliance with ISO 14644 standards.
What are the benefits of using HEPA filters in a cleanroom?
Utilizing HEPA filters in cleanrooms offers crucial benefits, including:
- High Particle Filtration Efficiency: Capable of removing 99.97% of airborne particles as small as 0.3 microns.
- Compliance with Regulatory Standards: Meets the requirements set by ISO 14644 for various cleanroom classifications.
- Improved Air Quality: Ensures a contaminant-free environment essential for high-precision manufacturing processes.
These benefits are critical for maintaining the strict environmental conditions required in medical device production.
What is the role of cleanroom clothing in contamination control?
Cleanroom clothing, or gowns, are an integral part of contamination control as they act as barriers to contaminants carried by personnel. Wearing proper cleanroom attire, such as gowns, masks, gloves, and shoe covers, minimizes the shedding of skin particles and hair, thereby reducing the risk of product contamination. Cleanroom clothing is designed to be lint-free and made from synthetic materials that do not generate particles, maintaining the sterile conditions necessary for high-quality production.
How do you design a cleanroom layout for efficient workflow?
Designing a cleanroom layout for efficient workflow involves carefully planning the placement of equipment, workstations, and personnel pathways to minimize contamination risks. A well-considered layout segregates different zones for specific activities like assembly, testing, and packaging. This approach includes strategic positioning of airflow systems and regularly used equipment to ensure efficient movement of materials and personnel, enhancing productivity while maintaining cleanliness standards.
How does cleanroom lighting affect operations?
Adequate lighting in cleanrooms is essential for ensuring product quality and worker precision, impacting operations significantly. Proper illumination helps in visual inspections and assembly tasks, reducing errors and enhancing quality control. Cleanroom lighting is typically designed to be bright, with minimal heat output, and often utilizes LED technology due to its energy efficiency and low particulate emission, contributing to a stable and clean environment.
What challenges are faced in maintaining cleanroom standards?
Maintaining cleanroom standards involves several challenges, such as:
- Preventing Contamination: Consistently high air quality must be achieved and maintained.
- Regulating Climate Conditions: Precise control of temperature, humidity, and pressure is essential.
- Ensuring Compliance: Adherence to regulatory standards like ISO and FDA guidelines is mandatory.
These challenges require continuous monitoring and regular maintenance of cleanroom systems to ensure that cleanliness and operational standards are not compromised.
Related Information
-
共0页 0条