Downflow Booth
A Downflow Booth is a type of cleanroom or controlled environment used primarily for dust-free processes and particle-sensitive applications. It is designed to direct clean, filtered air downward over a work area to remove airborne contaminants and maintain a clean, safe environment for workers or sensitive processes.
Industry Applications:
Electronics Manufacturing
Pharmaceutical Manufacturing
Medical Device Manufacturing
Biotechnology and Laboratory Research
Cosmetic and Pharmaceutical Powder Production
Food Processing
Aerospace and Aircraft Manufacturing
Chemicals and Paints Handling
Forensic and Environmental Testing
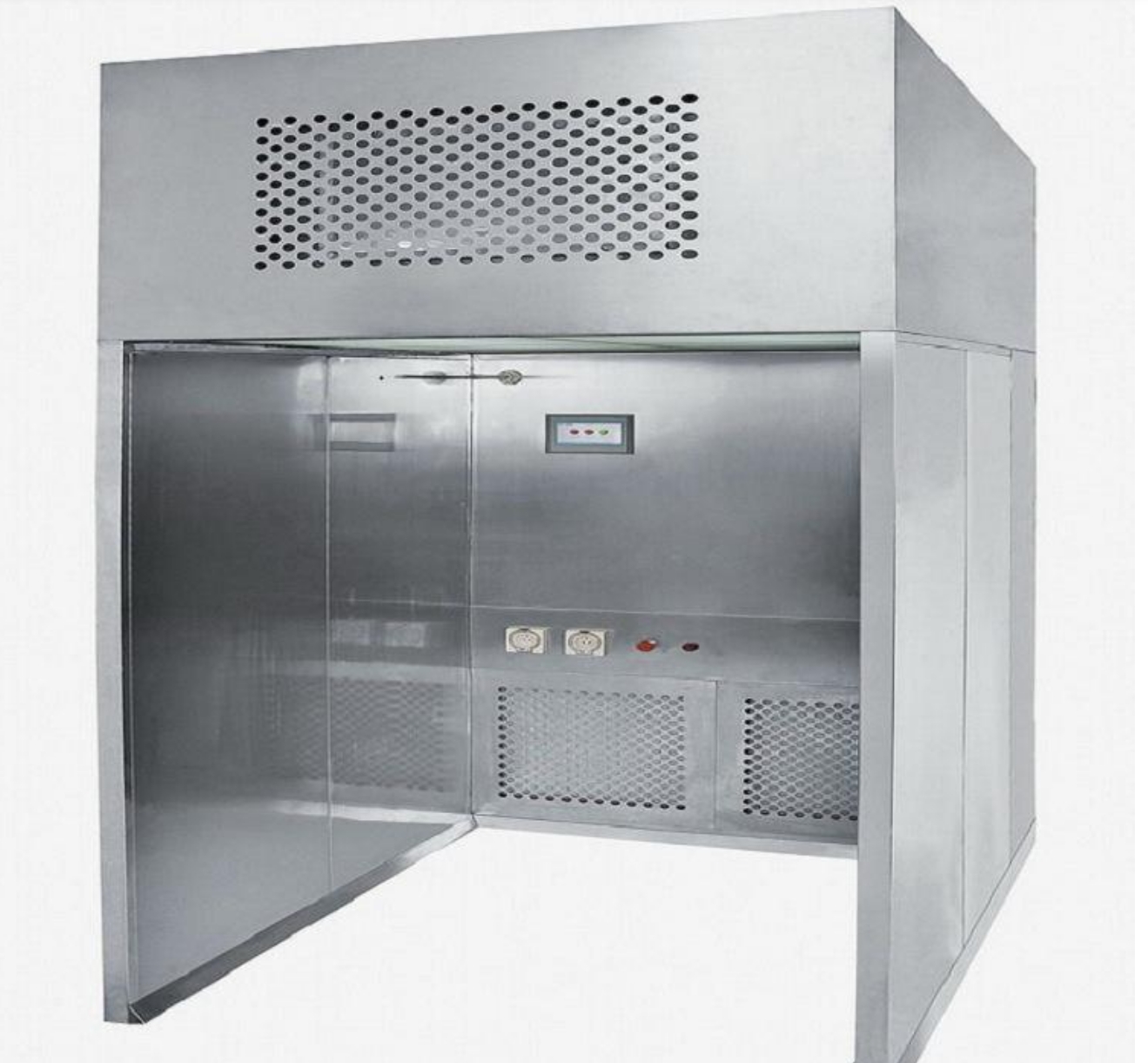
Your Reliable Manufacturer of Downflow Booth
Technical characteristics
Manual frequency conversion system for wind speed, so that the wind speed in the main working area is always in a uniform operation state.
Filter differential pressure display device, real-time monitoring of the effective operation of each filter.
Unique air duct design, effectively controlling the working noise of the whole machine.
Unique equal flow design in the main working area, which can control the dust and reagent spillage and uplift to prevent the inhalation hazard of dust and reagent to human body, and also avoid the cross-contamination of dust and reagent to protect the external environment and the safety of indoor personnel when the weighing and dispensing are carried out. The weighing operation area is protected by a hundred-level vertical layer IS06 (NF, EN, IS0014644-1).
Use of the environment and conditions: temperature 5C-40 ℃, relative humidity is not greater than 85% (no condensation) atmospheric pressure 86KPa-106KPa power AC380v, three-phase, 50HZ
Box structure material for the SUS304 # sanded stainless steel (thickness 1.0MM sanded plate / optional plate thickness) welding flat angle are full welding without dead ends, surface treatment without welding marks.
Inside and outside the double-layer shell, to ensure that there is no gap connection, anti-dust easy to clean.
Control options for automatic control: opening instructions and stop function.
Air outlet surface options: polymer flow membrane (180/200 mesh)
Separate static pressure box with differential pressure table; wind speed 0.65m/s ± 20%;
Filter cartridge option: independent brand. Weighing chamber with PA0 detection port and smoke injection port, sealing form: for the liquid tank seal anti-flange form;
Air supply mode: side air supply (including primary effect)
PA0 test pass rate of 100% (in line with the new version of GMP testing standards)
Size: can be customized.
Rated air volume (cubic meters/hour) 2500-300016) out of the wind wind speed (m / s) 0.45 ± 20%
Front hanging PVC transparent door curtain (optional, order to specify)
- Video
- Workshop
- Data sheet
- Material certificate
Weighing room
Biopharmaceutical negative pressure weighing room weighing room is a pharmaceutical, microbiological research and scientific experiments and other places dedicated to the local purification equipment, which provides a vertical unidirectional airflow, part of the clean air in the work area circulation, part of the discharge to the nearby areas.
Fine chemical weighing hood
This is a simple type of fine chemical negative pressure weighing enclosure, weighing room, sampling room, surrounded by PVC anti-static soft wall, its cleanliness can be installed by Class ISO3 ~ ISO8 according to the actual needs.
Help to Find Your Cleanroom Related Products
-
Modular CleanRoom
US$9000-10000 USD/Unit
Min. Order:1 unit -
Air Shower
US$1000.00-5000.00 USD/Unit
Min. Order:1 unit -
Downflow Booth
US$3000-6000 USD/Unit
Min. Order:1 unit -
Clean bench
US$600-2000 USD/Unit
Min. Order:1 unit -
Air Filter
US$3-50 USD/Unit
Min. Order:1 unit -
Cleanroom Wall Panels
US$10-20 USD/sq.
Min. Order:100 square -
Pass Box
US$200-500 USD/Unit
Min. Order:1 unit -
FFU
US$135-350 USD/Unit
Min. Order:1 unit
What is a downflow booth?
A downflow booth is a controlled environment designed to direct clean, filtered air downward over a workspace, helping to maintain a dust-free and contaminant-free area. The primary function of this booth is to protect sensitive processes or products from airborne contaminants, such as dust, fibers, and particles, which could affect quality or safety. These booths typically use HEPA or ULPA filters to clean the air, ensuring the workspace remains at a high level of cleanliness.
The airflow in a downflow booth is carefully controlled to create positive pressure, which forces air out of the booth, preventing contaminants from entering. The downward airflow also directs particles away from the operator and toward exhaust systems or filters. Downflow booths are used in industries like electronics manufacturing, pharmaceuticals, medical device production, and laboratories.
What is a weigh booth?
A weigh booth is a type of controlled environment specifically designed for weighing and handling powders or chemicals. These booths are equipped with air filtration systems that prevent contamination of the material being weighed, which is crucial when working with hazardous or sensitive substances. They are commonly used in industries such as pharmaceuticals, chemicals, and food production.
Weigh booths often feature downward airflow to maintain a clean environment, with HEPA or ULPA filters to remove airborne particles. Additionally, these booths often include explosion-proof or containment features to ensure the safe handling of potentially hazardous materials, keeping both the product and the operator protected.
What is the difference between sampling booth and dispensing booth?
A sampling booth is designed for taking samples from bulk material, such as powders or liquids, in a controlled environment. The main purpose is to ensure that the sample is free from contamination and represents the larger batch accurately. Sampling booths typically have filtration systems and positive pressure to prevent external particles from entering.
A dispensing booth, on the other hand, is used for dispensing or transferring materials in bulk (e.g., powders, chemicals) into smaller containers or packaging. The key difference is that dispensing booths require more extensive containment to prevent the release of dust or hazardous substances into the environment. They also typically have higher filtration efficiency and airflow controls to ensure both worker safety and product integrity.
How much does a downflow booth cost?
The cost of a downflow booth can vary widely depending on its size, features, and the industry it is designed for. On average, the price can range from $10,000 to $50,000 or more. Factors influencing the cost include:
Size and configuration of the booth
Airflow capacity (measured in CFM or air changes per hour)
Filtration system (HEPA or ULPA filters)
Additional features, such as explosion-proof enclosures, temperature control, or ergonomic designs
For specialized configurations, such as booths with custom airflow patterns or explosive-proof designs, the cost could be even higher.
What is the differential pressure in a dispensing booth?
The differential pressure in a dispensing booth refers to the difference in air pressure between the booth’s interior and the surrounding environment. Typically, dispensing booths are designed to maintain a negative pressure to ensure that any dust or hazardous particles released during dispensing are contained within the booth and not allowed to escape into the surrounding area.
The differential pressure is typically maintained at around 0.5 to 1 inch of water column (WC). This ensures that the air flows into the booth rather than out, helping to prevent the release of contaminants. In more sensitive environments, such as those handling hazardous chemicals, the differential pressure might be adjusted to be even more stringent to guarantee operator safety and product integrity.
What is the difference between a sampling booth and a dispensing booth?
A sampling booth is primarily used to collect small samples from a larger batch of material, ensuring that the sample is representative and free from contamination. It often includes a positive pressure system and HEPA or ULPA filters to prevent external contaminants from entering the booth while the sample is being taken. These booths are typically used in industries where accurate sampling for quality control is essential.
A dispensing booth, on the other hand, is designed for handling and transferring larger quantities of materials, such as powders or chemicals, into containers for further processing. The primary goal of a dispensing booth is to contain potentially harmful dust or particles and protect both the operator and the environment. These booths often have higher filtration efficiency, stronger containment features, and fume extraction systems to ensure safe handling of materials.
What is the air velocity of a dispensing booth?
The air velocity in a dispensing booth is important for maintaining a safe and clean working environment. Typically, the air velocity should be between 0.45 and 0.75 meters per second (m/s) at the work surface. T
Purpose: Proper air velocity helps contain contaminants within the booth and ensures that the operator is not exposed to harmful materials.
Adjustments: For highly toxic or hazardous materials, the air velocity may need to be increased to ensure better containment and airflow control.
his range ensures that airborne particles, such as dust or chemicals, are directed into the exhaust system, preventing them from escaping the booth.
How to design a weighing booth?
Designing a weighing booth requires careful attention to both safety and accuracy. The booth should have a controlled airflow system, typically a downward flow, to direct clean air over the workspace and minimize contamination. A HEPA or ULPA filter should be included to remove fine airborne particles that could affect the weighing process. The design should also ensure that the booth is large enough to accommodate the necessary weighing equipment and materials, with ergonomic features to make the operator's work easier and safer.
Additionally, if hazardous materials are being weighed, the booth should include explosion-proof or containment features, such as fume extraction systems, to ensure safety and compliance with industry standards.
What is the differential pressure in a dispensing booth?
The differential pressure in a dispensing booth refers to the difference in air pressure between the interior of the booth and the surrounding environment. Typically, dispensing booths are designed to maintain negative pressure to ensure that any airborne contaminants or particles created during the dispensing process are kept inside the booth and do not escape into the surrounding area.
The differential pressure is usually set between 0.5 and 1 inch of water column (WC), although it can vary based on the materials being handled and the booth’s design. This negative pressure ensures that air flows into the booth, preventing contaminants from escaping and ensuring a safe environment for the operator.
What technique do you use when using weighing paper to weigh out a powder material?
When using weighing paper to measure powder, it is important to follow a few simple techniques to ensure accurate measurements. First, weigh the paper before adding any powder to account for its weight. After that, carefully fold the paper to create a shallow container that allows easy transfer of the powder without spilling. Once the powder is transferred, use a spatula or small brush to remove any residual material from the paper to ensure all of it is accounted for.
Additionally, it’s important to handle the weighing paper with clean gloves or tools to avoid contaminating the material. This method ensures that the measurement is accurate and free from external contamination.
What filters are used in a dispensing booth?
In a dispensing booth, filters play a critical role in maintaining a safe and clean environment. The most commonly used filters are HEPA (High-Efficiency Particulate Air) filters or ULPA (Ultra-Low Penetration Air) filters, which are designed to capture fine particles and dust that may be hazardous to both the operator and the surrounding environment.
HEPA filters can capture particles as small as 0.3 microns with an efficiency of 99.97%, making them ideal for general use in non-toxic environments.
ULPA filters are even more efficient, capturing particles as small as 0.12 microns, making them suitable for highly sensitive applications or hazardous materials.
These filters work together with exhaust systems to ensure that contaminants do not escape from the booth, ensuring a safe and controlled environment for dispensing operations.
How much does a powder weighing booth cost?
The price of a powder weighing booth can vary widely based on several factors, including the size of the booth, the complexity of the filtration system, and any additional features, such as explosion-proof capabilities or fume extraction systems. On average, a basic powder weighing booth can range from $5,000 to $15,000. However, more specialized models with advanced features or customized designs may cost upwards of $20,000 or more.
Factors that affect the cost include:
Size and configuration of the booth
Type of filtration system (HEPA or ULPA)
Additional features like lighting, ergonomic design, and airflow control systems.