Semiconductor cleanrooms
Semiconductor cleanrooms are highly controlled environments designed specifically for the manufacturing, testing, and assembly of semiconductor devices (such as microchips, integrated circuits, and microprocessors).
These cleanrooms are crucial for minimizing the introduction, generation, and retention of airborne particles that can cause defects in the microfabrication process.
Because semiconductor manufacturing involves processes that require extreme precision, even tiny particles (as small as 0.1 microns) can have significant impacts on the yield and functionality of the final product.
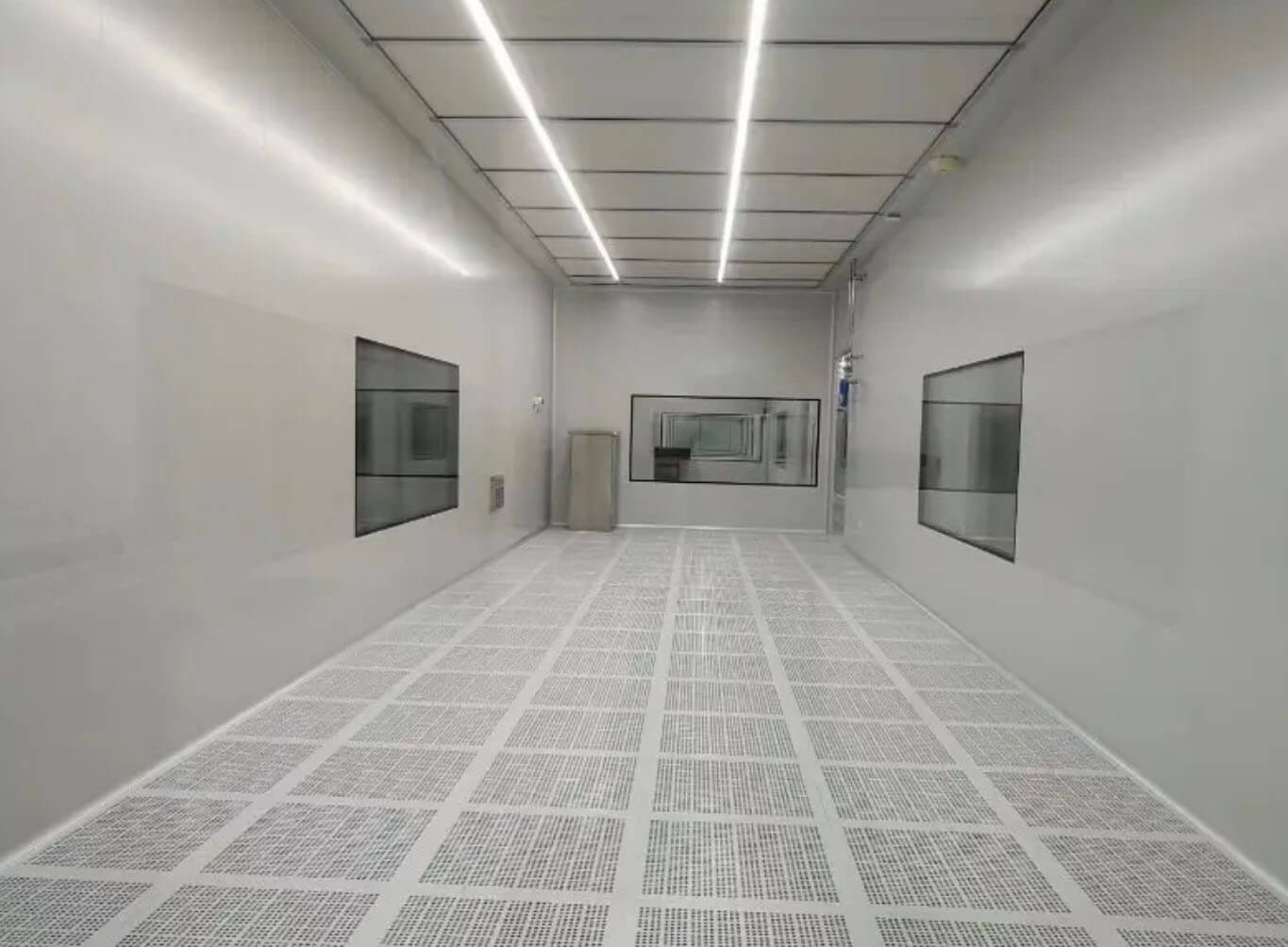
Model Cleanroom | Model Cleanroom |
Our Cleanroom SolutionsWe provide complete turnkey modular cleanroom solutions for your project through manufacturing, supplying, and installing. Our professional cleanroom solutions include:
|
We provide and install |
FAQ
Q: What is a cleanroom in semiconductor?
A: A cleanroom in semiconductor manufacturing is a controlled environment designed to maintain extremely low levels of airborne particles, dust, and contaminants. These environments are essential for the production of semiconductor devices, such as microchips and integrated circuits, where even a tiny particle can lead to defects or malfunctions in the final product. Semiconductor cleanrooms are equipped with specialized filtration systems, such as HEPA or ULPA filters, and maintain strict temperature, humidity, and pressure conditions to minimize contamination. Personnel working in these rooms must wear protective clothing to prevent contaminants from being introduced into the environment.
Q: Why do semiconductors need a clean room?
A: Semiconductors need cleanrooms because the manufacturing process for microchips and integrated circuits is highly sensitive to contamination. Even microscopic particles, dust, or impurities can damage delicate components, leading to defects or malfunctioning devices. Cleanrooms help maintain a controlled environment where the number of airborne particles is minimized, ensuring the production of high-quality, reliable semiconductor products. Cleanrooms also regulate factors like temperature, humidity, and electrostatic discharge to ensure that semiconductor fabrication processes are carried out under optimal conditions for precision and efficiency.
Q: What is a clean room for microprocessors?
A: A clean room for microprocessors is a highly controlled environment where microchips, including processors, are designed, fabricated, and tested. These rooms maintain strict cleanliness standards by controlling the concentration of airborne particles and contaminants. Microprocessor manufacturing involves intricate processes, including photolithography, etching, and deposition, all of which require an environment free of dust and other contaminants to avoid defects. The cleanroom is equipped with HEPA or ULPA filtration systems, precise air circulation, and specialized clothing for workers to ensure that contamination is minimized throughout the manufacturing stages.
Q: What is CIP in semiconductor?
A: CIP in semiconductor manufacturing stands for Critical Infrastructure Protection. It refers to the systems, processes, and controls put in place to ensure the safety and security of the semiconductor manufacturing environment, including cleanrooms and equipment. CIP includes measures to protect the facility from contamination, equipment failure, and security breaches that could compromise the production of high-quality semiconductors. This involves continuous monitoring, validation of processes, maintenance of air quality, and safeguarding sensitive manufacturing data and technology.
Q: What are the requirements for a semiconductor cleanroom?
A: Semiconductor cleanrooms require stringent control of several environmental parameters to ensure a contaminant-free environment for chip fabrication. Key requirements include maintaining specific ISO cleanliness classifications (typically ISO Class 1 to Class 5), high-efficiency air filtration (HEPA or ULPA filters), strict temperature and humidity control, and positive pressure to prevent external contaminants from entering. Additionally, the cleanroom must be equipped with specialized air handling systems, automated monitoring equipment, and strict protocols for worker hygiene, including the use of cleanroom suits, gloves, and face masks to avoid contamination from personnel. Continuous monitoring and validation of conditions are essential to ensure the cleanroom remains compliant with manufacturing standards.
Q: What are the standards for semiconductor cleanliness?
A: The standards for semiconductor cleanliness are governed by the ISO 14644 series of cleanroom standards, which define the cleanliness levels based on the concentration of airborne particles of a specific size (usually 0.5 microns or larger). Semiconductor cleanrooms typically operate under ISO Class 1 to Class 5 cleanliness levels, depending on the sensitivity of the process. These standards dictate the maximum allowable number of particles per cubic meter of air, the design and operation of the cleanroom's air filtration systems, and the protocols for maintaining the clean environment. Compliance with these standards ensures that semiconductor fabrication processes remain free from contamination, which is crucial for producing high-quality microchips.
Q: What is the temperature requirement for a semiconductor cleanroom?
A: The temperature requirement for a semiconductor cleanroom is typically maintained within a range of 20 to 22 degrees Celsius (68 to 72 degrees Fahrenheit). This temperature range is carefully controlled to ensure optimal conditions for both the manufacturing process and the comfort of personnel. Extreme fluctuations in temperature can affect the precision of semiconductor manufacturing processes, such as photolithography and etching, as well as the performance of sensitive equipment. Additionally, temperature control is important to prevent condensation and to maintain the desired airflow characteristics within the cleanroom.
Q: What is the classification of a clean room?
A: Cleanroom classification is based on the concentration of airborne particles of a specified size, typically 0.5 microns or larger. The cleanroom is classified according to standards such as ISO 14644-1, which assigns cleanliness classes ranging from Class 1 (the cleanest) to Class 9 (the least clean). The class designation refers to the maximum allowable number of particles per cubic meter of air. For example, an ISO Class 1 cleanroom allows no more than 1 particle per cubic meter, while an ISO Class 9 cleanroom may allow up to 35,200,000 particles per cubic meter. The cleanroom classification is critical in industries like semiconductor manufacturing, pharmaceuticals, and aerospace, where precision and cleanliness are crucial.
Q: What is a semiconductor cleanroom?
A: A semiconductor cleanroom is a highly controlled environment specifically designed for the manufacturing and testing of semiconductor devices, including microchips, integrated circuits, and other electronic components. The cleanroom is equipped with advanced air filtration systems, such as HEPA or ULPA filters, and is maintained at stringent ISO cleanliness levels to minimize airborne particles and contaminants. These cleanrooms also control factors like temperature, humidity, and electrostatic discharge (ESD) to ensure the integrity of the manufacturing process. Personnel are required to wear specialized protective clothing, such as coveralls, gloves, and face masks, to prevent contamination from human sources. The controlled environment ensures the production of high-quality, defect-free semiconductor products.
Q: What is a Class 7 or 8 cleanroom?
A: A Class 7 or Class 8 cleanroom refers to a controlled environment with specific cleanliness standards as defined by ISO 14644-1. In a Class 7 cleanroom, the maximum allowable concentration of particles that are 0.5 microns or larger is 352,000 particles per cubic meter. For a Class 8 cleanroom, the limit is 3,520,000 particles per cubic meter. These classes are typically used in applications where contamination control is important but not as critical as in higher classes (e.g., Class 1 or Class 5). Class 7 and 8 cleanrooms are commonly found in industries like food processing, certain types of electronic assembly, and non-critical pharmaceutical production.
Q: What ISO standard is a semiconductor cleanroom?
A: A semiconductor cleanroom is typically classified according to the ISO 14644-1 standard, which outlines the cleanliness levels based on the concentration of airborne particles. Semiconductor cleanrooms often require ISO Class 1 to Class 5 standards, depending on the sensitivity of the process. The ISO 14644-1 standard specifies the maximum allowable number of airborne particles of 0.5 microns or larger in a cubic meter of air for each class. The cleanroom may also need to adhere to other ISO standards, such as ISO 14644-2 for performance monitoring, ISO 14644-3 for testing methods, and ISO 14644-4 for design and installation.
Q: What are the basic cleanroom requirements?
A: The basic requirements for a cleanroom include strict control of airborne particle levels, temperature, humidity, and airflow patterns. Cleanrooms must be equipped with high-efficiency air filtration systems (such as HEPA or ULPA filters) and maintain positive pressure to prevent contaminants from entering. Additionally, the room must be designed with smooth, non-porous surfaces that are easy to clean and resistant to contamination. Personnel working in the cleanroom must wear protective clothing, such as coveralls, gloves, face masks, and shoe covers, to minimize the introduction of particles. Regular monitoring, validation, and maintenance of these systems are also essential to ensure the room remains within the required cleanliness classification.
Q: What is a Class 2 cleanroom?
A: A Class 2 cleanroom is a cleanroom classified according to the ISO 14644-1 standard with a specific particle concentration limit of 1,000,000 particles per cubic meter for particles that are 0.5 microns or larger. This class is typically used in industries that require moderate levels of cleanliness, such as assembly areas for electronic components, packaging, or certain pharmaceutical processes. The level of cleanliness in a Class 2 cleanroom is less stringent than higher classes (such as Class 1 or Class 5), but it still ensures that airborne contamination is controlled to prevent defects in sensitive processes.
Q: What is a Class 6 cleanroom?
A: A Class 6 cleanroom is classified according to the ISO 14644-1 standard and allows a maximum concentration of 500,000 particles per cubic meter for particles that are 0.5 microns or larger. Class 6 cleanrooms are typically used in applications where a moderate level of cleanliness is required, such as in the assembly of electronic components or low-risk pharmaceutical production. While they offer a higher level of cleanliness than Class 7 or 8, they are less stringent than higher classes like Class 1 or Class 5, which are required for more critical applications like semiconductor manufacturing or sterile pharmaceutical production.
Q: What are Class 3 clean room requirements?
A: A Class 3 cleanroom is one of the highest cleanliness levels as per ISO 14644-1. It must maintain an environment where the
Related Information
-
共0页 0条