3 x 5M ISO 6 Hardwall Cleanroom
Reference Price:US$4000.00-6500.00
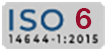

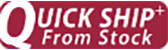


Cleanroom
3 x 5M ISO 6 Hardwall Cleanroom
Choose your installation & validation options below
Quantity:
Choose your Cleanroom frame structure material
Quantity:
Choose your Cleanroom Wall enclosure materials
Quantity:
Choose your Temperature requirements
Quantity:
Choose your humidity requirements
Quantity:
Choose your Explosion-proof requirements
Quantity:
Summary
3 x 5M ISO 6 Hardwall Cleanroom
Validation
Installation & Validation
Find Similar Products
-
10 x 20M ISO 6 Hardwall Cleanroom
US$5000-19000 USD/Set
Min. Order:1 Set -
10 x 15M ISO 6 Hardwall Cleanroom
US$5000-19000 USD/Set
Min. Order:1 Set -
10 x 10M ISO 6 Hardwall Cleanroom
US$5000-19000 USD/Set
Min. Order:1 Set -
8 x 15M ISO 6 Hardwall Cleanroom
US$5000-19000 USD/Set
Min. Order:1 Set -
8 x 10M ISO 6 Hardwall Cleanroom
US$5000-19000 USD/Set
Min. Order:1 Set -
5 x 10M ISO 6 Hardwall Cleanroom
US$5000-19000 USD/Set
Min. Order:1 Set
Cleanrooms Detail
A 3 x 5 meter ISO 6 Hardwall Cleanroom is a mid-sized, rigid-panel cleanroom designed to meet ISO 14644-1 standards for ISO Class 6. It provides a controlled environment with a maximum particle concentration of 35,200 particles per cubic meter (≥0.5 µm), using HEPA filtration and positive pressure airflow. Ideal for applications in pharmaceuticals, electronics, and biotech, this cleanroom balances space efficiency with reliable contamination control for sensitive processes.
Key Features of an ISO 6 Cleanroom
Particle Count: Limits the concentration of particles larger than 0.5 microns to no more than 35,200 particles per cubic meter of air.
Air Changes per Hour (ACH): Requires a minimum of 150 air changes per hour to maintain cleanliness and remove airborne contaminants effectively.
Airflow: Typically uses unidirectional (laminar) airflow to reduce particle contamination and ensure a consistent clean environment.
Materials: Constructed with durable, non-porous materials like steel or composite panels to minimize particle shedding and ensure ease of cleaning.
Hardwall Cleanroom Specification
No | Item | Data | Optional |
1 | Product | Clean room | The price needs to be re-calculated |
2 | Size | L5.3m*W3.5m*H2m | Yes |
3 | Cleanliness | 1000class | 10/100/10000 class |
4 | Wall | Antistatic pvc grid curtain | Acrylic or toughened glass |
5 | Door | Pvc soft curtain | Acrylic or toughened glass |
6 | Frame | Aluminium 5050 | Stainless steel |
7 | FFU | 1175*575*320MM / Aluminium zinc /6 sets | Stainless steel |
8 | Purified lamp | 15W /8Pcs | Quantity |
9 | Voltage | AC 220V/50hz | Yes |
Cleanrooms Airflow
To maintain ISO 5 classification, the following criteria must be met:
Particle Concentration Limits (per cubic meter of air)
0.5 microns: ≤ 3,520 particles
5 microns: ≤ 0.1 particles (the particle count drops significantly for larger particles)
Class 100 (in U.S. classification): ISO 5 cleanrooms are often referred to as Class 100 cleanrooms in the U.S. classification system.
Airflow Design
Laminar or Unidirectional Airflow: To maintain the cleanliness, air must flow in a uniform direction, typically from ceiling to floor, with minimal turbulence to prevent particles from settling.
HEPA or ULPA Filters: Air is filtered through High-Efficiency Particulate Air (HEPA) or Ultra-Low Penetration Air (ULPA)filters that capture particles down to 0.3 microns or smaller. ULPA filters provide even higher efficiency, capturing particles down to 0.12 microns.
Cleanrooms Installation
Installation Steps
Environment Preparation
Frame Assembly
Filter and Fan Installation
Commissioning
Cleanrooms Testing
-
Air Supply and Exhaust Volume Testing
-
Airflow Control Inspection
-
Inspection Instruments and Equipment
-
Testing Standards and Criteria
-
Testing Steps and Processes
FAQ
1. How do you measure particle size in an ISO 6 Cleanroom?
Particle size in an ISO 6 Cleanroom is typically measured using laser particle counters. These devices detect particles suspended in the air by illuminating them with a laser and measuring the scattered light. The particle counters provide real-time data on the concentration and size distribution of particles, ensuring that the cleanroom meets the ISO 6 cleanliness standards.
2. How is a cleanroom’s cleanliness verified during audits?
Cleanroom cleanliness is verified during audits by conducting a series of tests, such as:
Particle count tests: To measure airborne particles.
Airflow tests: To ensure proper air circulation and filtration.
Pressure differential tests: To check if the cleanroom maintains the correct pressure relative to surrounding areas.
These tests ensure that the cleanroom continues to meet the required cleanliness standards during regular audits.
3. What are the different classifications of cleanrooms?
Cleanrooms are classified according to ISO 14644-1, with the following key classifications based on the maximum number of particles allowed per cubic meter:
ISO 1: Ultra-clean environment with almost no particles.
ISO 5: Suitable for highly sensitive processes, like semiconductor manufacturing.
ISO 6: Moderate contamination control for applications such as pharmaceutical production.
Each classification defines the level of cleanliness necessary for various industries.
4. What is the role of HEPA filters in an ISO 6 Hardwall Cleanroom?
HEPA filters play a critical role in maintaining the cleanliness of an ISO 6 Hardwall Cleanroom by filtering out airborne particles. These filters remove 99.97% of particles larger than 0.3 microns, ensuring that the cleanroom maintains the required particle count and providing a stable environment for sensitive processes. HEPA filtration is crucial for meeting ISO 6 cleanliness standards.
5. How is the airflow tested in an ISO 6 Cleanroom?
Airflow in an ISO 6 Cleanroom is tested using velometers or anemometers, which measure the velocity and direction of airflow. This ensures that the airflow is unidirectional and properly distributed throughout the cleanroom. Testing also verifies that the cleanroom meets the required air changes per hour (ACH), which is essential for maintaining the clean environment.
6. What is the ideal flooring material for an ISO 6 Hardwall Cleanroom?
The ideal flooring material for an ISO 6 Hardwall Cleanroom should be non-porous, easy to clean, and resistant to contaminants. Common choices include:
Epoxy resin flooring: Durable, smooth, and resistant to chemical spills.
Vinyl flooring: Easy to clean and maintain, often used for less demanding environments.
These materials help minimize particle contamination and support the cleanroom’s hygiene standards.
7. What are the benefits of a Hardwall Cleanroom?
Hardwall Cleanrooms provide several benefits, including:
Durability: The rigid panels ensure a stable and long-lasting structure.
Ease of maintenance: Hardwall cleanrooms are easier to clean and maintain compared to softwall designs.
Enhanced contamination control: The solid walls and controlled air pressure help prevent external contaminants from entering the cleanroom.
These features make Hardwall Cleanrooms ideal for industries that require a stable and contamination-free environment.
8. How do you ensure cleanroom compliance with industry standards?
Cleanroom compliance with industry standards is ensured through:
Routine testing: Regular particle count and airflow tests.
Certification audits: Periodic third-party audits to verify that the cleanroom meets ISO standards.
Maintenance: Continuous monitoring and maintenance of equipment like filters and HVAC systems.
These practices ensure the cleanroom remains compliant with the required cleanliness and environmental standards.
9. What are the standards for particle counting in an ISO 6 Cleanroom?
For an ISO 6 Cleanroom, particle counting must ensure that the particle concentration does not exceed:
35,200 particles per cubic meter for particles larger than 0.5 microns.
This standard ensures that the cleanroom environment is suitable for processes requiring moderate contamination control.
10. How often should HEPA filters be replaced in an ISO 6 Cleanroom?
HEPA filters in an ISO 6 Cleanroom should typically be replaced every 12 to 24 months, depending on the cleanroom’s usage and environmental conditions. Regular monitoring of airflow and particle concentration can help determine the optimal replacement schedule.
11. How is contamination controlled during cleanroom construction?
Contamination during cleanroom construction is controlled by:
Using clean materials: Choosing low-particulate materials that minimize dust and debris.
Maintaining a controlled environment: Keeping the construction area isolated and using air filtration systems to reduce particles.
Cleaning protocols: Following strict cleaning procedures during and after construction to ensure that the cleanroom environment remains uncontaminated.
These practices ensure the cleanroom meets cleanliness standards from the moment construction is completed.
12. How do you design airflow systems in an ISO 6 Cleanroom?
Airflow systems in an ISO 6 Cleanroom are designed to ensure unidirectional airflow, which helps carry airborne particles away from sensitive areas. The system should also:
Provide a minimum number of air changes per hour (ACH), typically 150 for ISO 6.
Maintain positive pressure to prevent contaminants from entering the cleanroom.
Designing the airflow system to meet these standards helps maintain cleanliness and proper environmental conditions.
13. How do you select the right contractor for building an ISO 6 Cleanroom?
Selecting the right contractor for building an ISO 6 Cleanroom involves considering:
Experience: A contractor with a proven track record in cleanroom construction.
Understanding of industry standards: The ability to comply with ISO 14644-1 and other relevant regulations.
Capability to meet specific needs: The contractor should be able to customize the cleanroom design to meet your exact requirements.
Choosing the right contractor ensures the successful construction of a cleanroom that meets cleanliness standards.
14. How is air pressure controlled in an ISO 6 Hardwall Cleanroom?
Air pressure in an ISO 6 Hardwall Cleanroom is controlled through the HVAC system, which maintains positive pressure relative to surrounding areas. This prevents contaminants from entering the cleanroom. The system also regulates airflow and air changes per hour to ensure the pressure is maintained, especially when doors are opened or when equipment is moved in and out.
15. How are ISO 6 Hardwall Cleanrooms validated?
ISO 6 Hardwall Cleanrooms are validated by:
Conducting particle count tests to verify the cleanliness level.
Performing airflow tests to ensure the proper distribution of filtered air.
Checking pressure differentials to ensure the correct positive pressure is maintained.
These tests help ensure that the cleanroom meets ISO 14644-1 standards and is ready for use in sensitive processes.
16. How do you manage waste in an ISO 6 Hardwall Cleanroom?
Waste management in an ISO 6 Hardwall Cleanroom involves:
Using sealed containers to prevent contamination from waste materials.
Regular removal of waste from the cleanroom to avoid particle accumulation.
Proper disposal procedures: Ensuring that waste is handled in a way that minimizes contamination risks.
These practices ensure that the cleanroom environment remains clean and free from contaminants.
17. What are the typical dimensions of an ISO 6 Hardwall Cleanroom?
The typical dimensions of an ISO 6 Hardwall Cleanroom can vary based on the specific requirements of the application. Common sizes include:
Small cleanrooms: Approximately 2 x 3 meters.
Larger cleanrooms: Custom-designed to fit specific operational needs.
These dimensions are tailored to ensure that the cleanroom meets the space requirements for the intended process.
18. How do you optimize space usage in an ISO 6 Cleanroom?
To optimize space usage in an ISO 6 Cleanroom, consider:
Compact equipment: Using smaller, space-efficient tools and machinery.
Vertical storage: Utilizing wall-mounted shelves and cabinets to save floor space.
Modular design: Implementing a flexible layout that can adapt to future needs.
Optimizing space ensures that the cleanroom operates efficiently without compromising cleanliness or functionality.
19. How do you test an ISO 6 Cleanroom for particle contamination?
An ISO 6 Cleanroom is tested for particle contamination using laser particle counters. These devices measure the concentration of particles in the air and check if they meet the ISO 6 limits. Regular testing ensures that the cleanroom maintains the required cleanliness level for safe and effective operations.
Factory Production Workshop Video
Factory Photo
Product Packaging And International Logistics
Product International Certification
Find Other Common Equipment Recommendations
-
Modular CleanRoom
US$9000-10000 USD/Unit
Min. Order:1 Set -
Air Shower
US$1000.00-5000.00 USD/Unit
Min. Order:1 Set -
Downflow Booth
US$3000-6000 USD/Unit
Min. Order:1 Set -
Clean bench
US$600-2000 USD/Unit
Min. Order:1 Set -
Air Filter
US$3-50 USD/Unit
Min. Order:1 Set -
Cleanroom Wall Panels
US$10-20 USD/sq.
Min. Order:1 Set -
Pass Box
US$200-500 USD/Unit
Min. Order:1 Set -
FFU
US$135-350 USD/Unit
Min. Order:1 Set -
Fume Hood
US$700-1500 USD/Unit
Min. Order:1 Set -
Cleanroom HVAC
US$5000-20000 USD/Unit
Min. Order:1 Set -
Clean room floor
US$5-20 USD/Sq.
Min. Order:1 Set -
Clean room ceiling
US$
Min. Order:1 Set