6 x 20M ISO 8 Modular Cleanroom
Reference Price:US$38000-55000
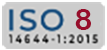

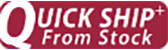
Cleanroom
6 x 20M ISO 8 Modular Cleanroom
Choose your installation & validation options below
Quantity:
Choose your Cleanroom frame structure material
Quantity:
Choose your Cleanroom Wall enclosure materials
Quantity:
Choose your Temperature requirements
Quantity:
Choose your humidity requirements
Quantity:
Choose your Explosion-proof requirements
Quantity:
Summary
6 x 20M ISO 8 Modular Cleanroom
Validation
Installation & Validation
Find Similar Products
-
8 x 15M ISO 8 Modular Cleanroom
US$12000-45000 USD/Set
Min. Order:1 Set -
6 x 20M ISO 8 Modular Cleanroom
US$12000-45000 USD/Set
Min. Order:1 Set -
6 x 10M ISO 8 Modular Cleanroom
US$12000-45000 USD/Set
Min. Order:1 Set -
8 x 25M ISO 8 Modular Cleanroom
US$12000-45000 USD/Set
Min. Order:1 Set -
8 x 20M ISO 8 Modular Cleanroom
US$12000-45000 USD/Set
Min. Order:1 Set -
8 x 30M ISO 8 Modular Cleanroom
US$12000-45000 USD/Set
Min. Order:1 Set
Cleanrooms Detail
ISO 8 modular cleanrooms provide a controlled environment that is essential for various applications in industries such as pharmaceuticals, biotechnology, and electronics. While not as stringent as ISO 7 cleanrooms, ISO 8 cleanrooms still play a vital role in maintaining product quality and ensuring safety during manufacturing and research processes.
Cleanroom Project Scope(from structure, HVAC,electric to autoc ontrol) | 1. Cleanroom Structure: Wall Panel, Ceiling Panel, Windows, Doors, Fttings, Flooring |
2. HVAC: AHU, Chiller, dehumidifier, Ducting, Piping, etc. | |
3. Electric: Lighting, Switch, Cables, Wires, Power Distribution Cabinet, etc | |
4. Auto- control: PLC Controller, Sensors for Humidity and Temperature, Control Panel | |
5. Process Piping System: Gas, Water Pipeline | |
Equipment | Air shower, Cargo shower, Mist shower, Dynamic pass box, Static pass box, Sampling booth,Weighing booth, Dispensing booth, |
Medicine stability test chamber, isolator, VHP sterilizer,Biological safety chamber, FFU, LAF, etc. | |
Temperature | 21-27*C (or as per required) |
Humidity | 30-60°C (or as per required) |
Application | Pharmaceutical factory, hospital, medical device factory, electronics factory, food factory,cosmetics factory, etc. |
Qualification Documents | CE GMP ISO |
Full Service | FAT and SAT Service, Professional Consultation, Training, 24 hours technical support |
ISO 8 Cleanroom Standards
No more than 3,520,000 particles per cubic meter of air (0.5 micrometers and larger).
No more than 29,300 particles per cubic meter of air (5 micrometers and larger).
Cleanrooms Airflow
In an ISO 8 modular cleanroom, effective airflow management is crucial to maintaining the required cleanliness levels and ensuring a safe working environment. While ISO 8 cleanrooms do not have as strict particle limits as ISO 7 cleanrooms, controlling airflow is still essential for minimizing contamination and providing a stable environment for various applications.
Key Features of Airflow in ISO 8 Cleanrooms
Air Changes per Hour (ACH)
ISO 8 cleanrooms typically require a minimum of 20 to 40 air changes per hour. This ensures that any contaminants introduced into the cleanroom are quickly diluted and removed.
The exact number of air changes may vary based on the specific processes being conducted and the layout of the cleanroom.
Return Air System
Effective return air systems help recirculate air back to the filtration units, ensuring that the cleanroom maintains its cleanliness standards. The design of the return air pathways is important to avoid dead zones where contaminants could accumulate.
Cleanrooms Installation
Cleanrooms Testing
Importance of testing
Clean room testing is extremely important to ensure product quality and the stability of the production environment. It can help to confirm whether the clean room meets the intended cleanliness requirements, and whether the various environmental indicators comply with the specified standards.
Testing Items
Suspended particles: Detects the number of suspended particles in the air in the clean room to ensure that the air cleanliness is up to standard.
Temperature and humidity: Monitor the temperature and humidity in the clean room to ensure environmental stability during the production process.
Noise: Evaluates the noise level in the clean room to minimize the impact on staff.
Static electricity: Detect static electricity buildup in the clean room to prevent damage to sensitive components from electrostatic discharge.
Microbial contamination: Detecting microbial levels in the clean room, especially critical for the healthcare industry.
FAQ
How does a modular cleanroom work?
A modular cleanroom consists of prefabricated components that can be assembled on-site. These components include walls, ceilings, and floors designed to control contamination. The modular design allows for flexibility in layout and size.
How do I find a supplier for modular cleanrooms?
To find a supplier for modular cleanrooms, start by researching online. Look for companies specializing in cleanroom technology. Here are three effective approaches:
- Search industry directories.
- Attend trade shows.
- Request recommendations from professionals.
What is the significance of particle counting in cleanrooms?
Particle counting is crucial in cleanrooms to ensure air quality meets specific cleanliness standards. It helps in identifying contamination levels and ensuring compliance with regulations. Regular monitoring can prevent product defects and protect sensitive processes.
What are the advantages of portable cleanrooms?
Portable cleanrooms offer flexibility and convenience, allowing for quick setup in various locations. They are ideal for temporary projects or expanding existing facilities. Key benefits include:
- Cost-effectiveness.
- Easy relocation.
- Customizable design options.
What type of ventilation systems are used in cleanrooms?
Cleanrooms use specialized ventilation systems to maintain air quality. Common systems include high-efficiency particulate air (HEPA) filters and laminar flow systems. These ensure that air is continuously filtered and circulated to minimize contamination.
What is the role of temperature control in cleanrooms?
Temperature control is vital in cleanrooms to maintain a stable environment. It ensures sensitive processes operate optimally and prevents material degradation. Proper temperature regulation also enhances comfort for personnel working in cleanroom conditions.
How is cleanroom performance measured?
Cleanroom performance is assessed through various metrics, including airflow, particulate levels, and temperature control. Regular validation tests are conducted to ensure compliance with industry standards. These measurements help maintain the integrity of the cleanroom environment.
What are the benefits of using modular cleanroom systems?
Modular cleanroom systems offer numerous advantages, including flexibility and scalability. They can be easily expanded or reconfigured as needs change. Additionally, they reduce construction time and costs while maintaining high-quality standards.
How do I assess the effectiveness of cleanroom filters?
To assess the effectiveness of cleanroom filters, conduct regular testing and maintenance. Key methods include particle counting and airflow measurement. Regular inspections help ensure filters are functioning properly and maintaining air quality standards.
How often should a modular cleanroom be validated?
A modular cleanroom should be validated at least annually. However, validation frequency may increase based on usage and specific regulatory requirements. Regular checks ensure the cleanroom consistently meets cleanliness standards and operational efficiency.
How can I improve air quality in my cleanroom?
Improving air quality in a cleanroom involves several strategies. Implementing regular maintenance of filters is essential. Additionally, consider the following practices:
- Monitor particle counts regularly.
- Optimize airflow patterns.
- Ensure proper gowning procedures.
What materials are used in modular cleanroom construction?
Modular cleanroom construction typically uses materials that are easy to clean and maintain. Common materials include stainless steel, epoxy-coated surfaces, and glass for visibility. These materials help reduce contamination and enhance durability.
How do I ensure proper airflow in my cleanroom?
To ensure proper airflow, design the cleanroom layout carefully. Maintain unobstructed airflow paths and use appropriate ventilation systems. Regular monitoring of airflow rates helps identify issues before they affect cleanroom performance.
Can a modular cleanroom be relocated?
Yes, a modular cleanroom can be relocated with relative ease. Its design allows for disassembly and reassembly at a new site. This feature makes modular cleanrooms an excellent choice for businesses needing flexibility in operations.
What are the best practices for cleanroom usage?
Best practices for cleanroom usage include strict gowning protocols and regular training for personnel. It's important to minimize entry and exit to prevent contamination. Regular cleaning and maintenance should also be prioritized to maintain standards.
How does humidity control affect cleanroom operations?
Humidity control is critical in cleanrooms to prevent moisture-related contamination. High humidity can lead to condensation and microbial growth, while low humidity can cause static electricity. Maintaining optimal humidity levels supports cleanroom integrity.
How do I monitor environmental conditions in a cleanroom?
Environmental conditions in a cleanroom can be monitored using specialized sensors and data loggers. These devices track parameters like temperature, humidity, and particle counts. Regular audits ensure that conditions remain within acceptable limits.
What are the maintenance requirements for ISO 8 cleanrooms?
ISO 8 cleanrooms require routine maintenance to ensure compliance. Key tasks include regular cleaning of surfaces and equipment, monitoring air quality, and validating filtration systems. Documentation of maintenance activitiesis essential for compliance and auditing purposes.
What are the most common cleanroom certifications?
The most common cleanroom certifications include ISO 14644 and Federal Standard 209E. These certifications specify cleanliness levels based on particle counts. Achieving these certifications ensures that a cleanroom operates within established industry standards.
What is the importance of cleanroom monitoring systems?
Cleanroom monitoring systems play a critical role in maintaining environmental control. They provide real-time data on temperature, humidity, and particulate levels. This information helps ensure compliance and enables quick responses to any deviations from standards.
How can I improve the efficiency of my cleanroom?
Improving cleanroom efficiency involves optimizing workflows and reducing contamination risks. Consider the following strategies:
- Streamline personnel movement.
- Enhance training programs.
- Regularly maintain equipment.
These practices can lead to better overall performance.
What is the role of cleanroom operators?
Cleanroom operators are responsible for maintaining cleanliness and adherence to protocols. They monitor environmental conditions and ensure that equipment functions properly. Their training and vigilance are crucial for preventing contamination and ensuring safety.
How do I prepare for a cleanroom audit?
Preparing for a cleanroom audit involves several key steps. First, review all relevant documentation and ensure compliance with standards. Conduct internal inspections to identify potential issues. Finally, ensure that all staff are trained and aware of audit protocols.
How often should cleanroom filters be replaced?
Cleanroom filters should typically be replaced every 6 to 12 months. However, replacement frequency may vary based on usage and environmental conditions. Regular monitoring of filter performance can help determine the optimal replacement schedule.
Factory Production Workshop Video
Factory Photo
Product Packaging And International Logistics
Product International Certification
Find Other Common Equipment Recommendations
-
Modular CleanRoom
US$9000-10000 USD/Unit
Min. Order:1 Set -
Air Shower
US$1000.00-5000.00 USD/Unit
Min. Order:1 Set -
Downflow Booth
US$3000-6000 USD/Unit
Min. Order:1 Set -
Clean bench
US$600-2000 USD/Unit
Min. Order:1 Set -
Air Filter
US$3-50 USD/Unit
Min. Order:1 Set -
Cleanroom Wall Panels
US$10-20 USD/sq.
Min. Order:1 Set -
Pass Box
US$200-500 USD/Unit
Min. Order:1 Set -
FFU
US$135-350 USD/Unit
Min. Order:1 Set -
Fume Hood
US$700-1500 USD/Unit
Min. Order:1 Set -
Cleanroom HVAC
US$5000-20000 USD/Unit
Min. Order:1 Set -
Clean room floor
US$5-20 USD/Sq.
Min. Order:1 Set -
Clean room ceiling
US$
Min. Order:1 Set