6 x 15M ISO 8 Modular Cleanroom
Reference Price:US$32000-45000


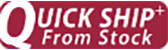
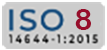
Cleanroom
6 x 15M ISO 8 Modular Cleanroom
Choose your installation & validation options below
Quantity:
Choose your Cleanroom frame structure material
Quantity:
Choose your Cleanroom Wall enclosure materials
Quantity:
Choose your Temperature requirements
Quantity:
Choose your humidity requirements
Quantity:
Choose your Explosion-proof requirements
Quantity:
Summary
6 x 15M ISO 8 Modular Cleanroom
Validation
Installation & Validation
Find Similar Products
-
8 x 15M ISO 8 Modular Cleanroom
US$12000-45000 USD/Set
Min. Order:1 Set -
6 x 20M ISO 8 Modular Cleanroom
US$12000-45000 USD/Set
Min. Order:1 Set -
6 x 10M ISO 8 Modular Cleanroom
US$12000-45000 USD/Set
Min. Order:1 Set -
8 x 25M ISO 8 Modular Cleanroom
US$12000-45000 USD/Set
Min. Order:1 Set -
8 x 20M ISO 8 Modular Cleanroom
US$12000-45000 USD/Set
Min. Order:1 Set -
8 x 30M ISO 8 Modular Cleanroom
US$12000-45000 USD/Set
Min. Order:1 Set
Cleanrooms Detail
ISO 8 modular cleanrooms provide a controlled environment that is essential for various applications in industries such as pharmaceuticals, biotechnology, and electronics. While not as stringent as ISO 7 cleanrooms, ISO 8 cleanrooms still play a vital role in maintaining product quality and ensuring safety during manufacturing and research processes.
Cleanroom Project Scope(from structure, HVAC,electric to autoc ontrol) | 1. Cleanroom Structure: Wall Panel, Ceiling Panel, Windows, Doors, Fttings, Flooring |
2. HVAC: AHU, Chiller, dehumidifier, Ducting, Piping, etc. | |
3. Electric: Lighting, Switch, Cables, Wires, Power Distribution Cabinet, etc | |
4. Auto- control: PLC Controller, Sensors for Humidity and Temperature, Control Panel | |
5. Process Piping System: Gas, Water Pipeline | |
Equipment | Air shower, Cargo shower, Mist shower, Dynamic pass box, Static pass box, Sampling booth,Weighing booth, Dispensing booth, |
Medicine stability test chamber, isolator, VHP sterilizer,Biological safety chamber, FFU, LAF, etc. | |
Temperature | 21-27*C (or as per required) |
Humidity | 30-60°C (or as per required) |
Application | Pharmaceutical factory, hospital, medical device factory, electronics factory, food factory,cosmetics factory, etc. |
Qualification Documents | CE GMP ISO |
Full Service | FAT and SAT Service, Professional Consultation, Training, 24 hours technical support |
ISO 8 Cleanroom Standards
No more than 3,520,000 particles per cubic meter of air (0.5 micrometers and larger).
No more than 29,300 particles per cubic meter of air (5 micrometers and larger).
Cleanrooms Airflow
In an ISO 8 modular cleanroom, effective airflow management is crucial to maintaining the required cleanliness levels and ensuring a safe working environment. While ISO 8 cleanrooms do not have as strict particle limits as ISO 7 cleanrooms, controlling airflow is still essential for minimizing contamination and providing a stable environment for various applications.
Key Features of Airflow in ISO 8 Cleanrooms
Air Changes per Hour (ACH)
ISO 8 cleanrooms typically require a minimum of 20 to 40 air changes per hour. This ensures that any contaminants introduced into the cleanroom are quickly diluted and removed.
The exact number of air changes may vary based on the specific processes being conducted and the layout of the cleanroom.
Return Air System
Effective return air systems help recirculate air back to the filtration units, ensuring that the cleanroom maintains its cleanliness standards. The design of the return air pathways is important to avoid dead zones where contaminants could accumulate.
Cleanrooms Installation
Cleanrooms Testing
Importance of testing
Clean room testing is extremely important to ensure product quality and the stability of the production environment. It can help to confirm whether the clean room meets the intended cleanliness requirements, and whether the various environmental indicators comply with the specified standards.
Testing Items
Suspended particles: Detects the number of suspended particles in the air in the clean room to ensure that the air cleanliness is up to standard.
Temperature and humidity: Monitor the temperature and humidity in the clean room to ensure environmental stability during the production process.
Noise: Evaluates the noise level in the clean room to minimize the impact on staff.
Static electricity: Detect static electricity buildup in the clean room to prevent damage to sensitive components from electrostatic discharge.
Microbial contamination: Detecting microbial levels in the clean room, especially critical for the healthcare industry.
FAQ
What is the process of cleanroom certification?
Cleanroom certification involves several key steps. Initially, a thorough assessment of the cleanroom's design and operational procedures is conducted. Following this, various tests are performed to measure particulate contamination levels.
Finally, an official report is generated, confirming if the cleanroom meets the required standards for classification. The certification process ensures compliance and operational efficiency.
It is essential to periodically re-evaluate and maintain certification to uphold cleanliness standards.
What type of air filtration is needed for an ISO 8 cleanroom?
An ISO 8 cleanroom requires high-efficiency particulate air (HEPA) filters for effective air filtration. These filters capture particles larger than 0.3 microns at a 99.97% efficiency.
In addition to HEPA filters, pre-filters are also used to extend the life of the HEPA filters. It is crucial to monitor the performance of these filters regularly to ensure optimal air quality.
Proper air filtration prevents contamination and maintains the integrity of the cleanroom environment.
What kind of training is required for cleanroom personnel?
Training for cleanroom personnel is vital for maintaining cleanliness and safety. Initial training should cover cleanroom protocols, gowning procedures, and contamination control measures.
Ongoing training is equally important and should focus on safety regulations, equipment handling, and emergency procedures. Regular refreshers help reinforce knowledge and compliance among staff.
Moreover, specialized training may be necessary for specific roles, ensuring all personnel are well-equipped to perform their duties effectively.
What types of pass-through systems are used in cleanrooms?
Pass-through systems are essential for maintaining cleanroom integrity. Common types include:
- Standard pass-throughs: Basic openings for transferring materials.
- Airlock pass-throughs: Systems that minimize contamination risks during transfers.
- Automated pass-throughs: Mechanisms that enhance efficiency and reduce human contact.
Selecting the right system depends on the cleanroom's requirements and the materials being handled.
How do I train staff for cleanroom environments?
Training staff for cleanroom environments should begin with a comprehensive orientation. This includes understanding cleanroom classifications, gowning procedures, and contamination prevention.
Hands-on training is crucial, allowing personnel to practice procedures in a controlled setting. Regular assessments can help ensure knowledge retention and compliance.
Additionally, ongoing training sessions should be scheduled to update staff on new protocols, equipment, and safety measures.
What types of equipment are used in modular cleanrooms?
Modular cleanrooms utilize various types of equipment to maintain controlled environments. Essential equipment includes:
- HEPA filters: For air filtration.
- Modular wall systems: To create flexible layouts.
- Environmental monitoring systems: To track cleanliness and air quality.
Each piece of equipment plays a significant role in ensuring the cleanroom meets the required standards for operation.
How do I document cleanroom procedures?
Documenting cleanroom procedures is essential for compliance and consistency. Start by creating a detailed manual that outlines all protocols, including gowning, cleaning, and equipment usage.
Regular updates to the documentation should be made to reflect any changes in procedures or regulations. Additionally, logs should be maintained for training sessions and equipment maintenance.
This documentation serves as a reference for staff and aids in audits and inspections.
Can a modular cleanroom be relocated?
Yes, modular cleanrooms can be relocated due to their design. Their components are prefabricated and can be disassembled and reassembled at a new site.
This flexibility allows businesses to adapt to changing needs without significant downtime. However, careful planning is necessary to ensure compliance at the new location.
Before relocation, all equipment and systems should be evaluated for functionality and compliance with cleanroom standards.
How often should a modular cleanroom be validated?
A modular cleanroom should be validated at key intervals. Generally, validation occurs:
- Annually: To ensure ongoing compliance and performance.
- After significant changes: Any modifications or relocations warrant a re-evaluation.
- Following equipment upgrades: New equipment must be validated to maintain cleanroom integrity.
Regular validation helps ensure that the cleanroom continues to meet required standards and operates efficiently.
How often should cleanroom filters be replaced?
Cleanroom filters should be replaced based on usage and manufacturer recommendations. Typically, HEPA filters are replaced every 6 to 12 months.
Regular monitoring of airflow and pressure drop can indicate when filters need servicing. Additionally, environmental conditions may necessitate more frequent replacements.
Maintaining clean and functional filters is crucial for sustaining air quality and minimizing contamination risks.
Can a modular cleanroom be customized?
Yes, modular cleanrooms can be customized to meet specific operational needs. Customization options include layout design, size adjustments, and specialized equipment installation.
These modifications allow businesses to create a cleanenvironment that aligns with their unique processes and requirements.
Customization can also extend to features like airflow patterns, lighting, and temperature control, enhancing overall performance and efficiency.
Working with experienced manufacturers can ensure that the customization meets regulatory standards and operational goals.
How do I prepare for cleanroom inspections?
Preparing for cleanroom inspections involves several key steps. Begin by reviewing all relevant documentation, including standard operating procedures and maintenance logs.
Ensure that all equipment is properly calibrated and functioning, and conduct a thorough cleaning of the cleanroom environment. Training records for staff should also be readily available for inspection.
Finally, perform a mock inspection to identify potential issues and ensure that all aspects of cleanroom operation are compliant with relevant standards.
How do I test the cleanroom environment?
Testing the cleanroom environment involves multiple assessment methods. Key tests include:
- Particle counting: To measure airborne particulate levels.
- Airflow velocity tests: To ensure proper air circulation.
- Surface cleanliness tests: To evaluate contamination on surfaces.
Regular testing helps ensure that the cleanroom maintains the required classification and operational standards.
What is the importance of cleanroom monitoring systems?
Cleanroom monitoring systems are crucial for maintaining environmental control. They continuously track parameters such as temperature, humidity, and particulate levels.
These systems provide real-time data, allowing for immediate corrective actions if deviations occur. Regular monitoring ensures compliance with industry standards and protects product integrity.
Additionally, data collected can be used for audits and to improve cleanroom processes over time.
How can I minimize the risk of contamination in a cleanroom?
Minimizing contamination risk in a cleanroom involves several strategies. Key practices include:
- Strict gowning procedures: Ensuring personnel wear appropriate attire.
- Regular cleaning schedules: Maintaining surfaces and equipment.
- Controlled access: Limiting entry to trained personnel only.
Implementing these measures significantly reduces the likelihood of contamination and enhances cleanroom integrity.
What is the importance of cleanroom gowning procedures?
Cleanroom gowning procedures are essential for preventing contamination. Proper gowning minimizes the introduction of particulate matter from personnel into the cleanroom environment.
Each layer of clothing serves a specific purpose, from preventing lint generation to protecting against skin flakes. Regular training on gowning procedures ensures compliance and reduces contamination risks.
Adhering to these protocols is vital for maintaining product quality and cleanroom classification.
How can I enhance the safety of cleanroom operations?
Enhancing safety in cleanroom operations involves implementing multiple measures. Key actions include:
- Regular safety training: Ensuring all personnel are aware of protocols.
- Proper equipment maintenance: Keeping tools in good working order.
- Clear signage: Indicating hazards and safety procedures throughout the facility.
These steps help create a safer working environment and reduce the risk of accidents or contamination.
What is the significance of particle counting in cleanrooms?
Particle counting is critical for assessing air quality in cleanrooms. It measures the concentration of airborne particles, ensuring they remain within acceptable limits for the cleanroom classification.
Regular particle counting helps identify potential contamination sources and evaluates the effectiveness of filtration systems. Monitoring particle levels is essential for maintaining compliance with industry standards.
Overall, it plays a vital role in protecting product integrity and ensuring operational excellence.
How do I maintain an ISO 8 modular cleanroom?
Maintaining an ISO 8 modular cleanroom requires consistent practices. Regular cleaning and disinfection of surfaces and equipment are essential to minimize contamination risks.
Routine monitoring of environmental parameters, including temperature and humidity, should be conducted to ensure compliance. Additionally, air filters must be replaced at recommended intervals to maintain air quality.
Documenting all maintenance activities helps track compliance and supports certification processes.
What are the best practices for cleanroom operation?
Best practices for cleanroom operation include:
- Strict adherence to gowning procedures: To minimize contamination.
- Regular environmental monitoring: Ensuring compliance with standards.
- Thorough training for personnel: Keeping staff informed and compliant.
Implementing these practices ensures the cleanroom operates efficiently and meets required cleanliness levels.
How do I choose the right modular cleanroom for my needs?
Choosing the right modular cleanroom involves assessing specific requirements. Key factors to consider include:
- Size and layout: To accommodate equipment and workflow.
- Classifications needed: Based on the intended use and industry standards.
- Customization options: For specific operational needs.
Evaluating these elements ensures you select a cleanroom that meets operational goals and regulatory requirements.
Factory Production Workshop Video
Factory Photo
Product Packaging And International Logistics
Product International Certification
Find Other Common Equipment Recommendations
-
Modular CleanRoom
US$9000-10000 USD/Unit
Min. Order:1 Set -
Air Shower
US$1000.00-5000.00 USD/Unit
Min. Order:1 Set -
Downflow Booth
US$3000-6000 USD/Unit
Min. Order:1 Set -
Clean bench
US$600-2000 USD/Unit
Min. Order:1 Set -
Air Filter
US$3-50 USD/Unit
Min. Order:1 Set -
Cleanroom Wall Panels
US$10-20 USD/sq.
Min. Order:1 Set -
Pass Box
US$200-500 USD/Unit
Min. Order:1 Set -
FFU
US$135-350 USD/Unit
Min. Order:1 Set -
Fume Hood
US$700-1500 USD/Unit
Min. Order:1 Set -
Cleanroom HVAC
US$5000-20000 USD/Unit
Min. Order:1 Set -
Clean room floor
US$5-20 USD/Sq.
Min. Order:1 Set -
Clean room ceiling
US$
Min. Order:1 Set