6 x 12M ISO 8 Modular Cleanroom
Reference Price:US$27000-36000

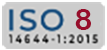


Cleanroom
6 x 12M ISO 8 Modular Cleanroom
Choose your installation & validation options below
Quantity:
Choose your Cleanroom frame structure material
Quantity:
Choose your Cleanroom Wall enclosure materials
Quantity:
Choose your Temperature requirements
Quantity:
Choose your humidity requirements
Quantity:
Choose your Explosion-proof requirements
Quantity:
Summary
6 x 12M ISO 8 Modular Cleanroom
Validation
Installation & Validation
Find Similar Products
-
8 x 15M ISO 8 Modular Cleanroom
US$12000-45000 USD/Set
Min. Order:1 Set -
6 x 20M ISO 8 Modular Cleanroom
US$12000-45000 USD/Set
Min. Order:1 Set -
6 x 10M ISO 8 Modular Cleanroom
US$12000-45000 USD/Set
Min. Order:1 Set -
8 x 25M ISO 8 Modular Cleanroom
US$12000-45000 USD/Set
Min. Order:1 Set -
8 x 20M ISO 8 Modular Cleanroom
US$12000-45000 USD/Set
Min. Order:1 Set -
8 x 30M ISO 8 Modular Cleanroom
US$12000-45000 USD/Set
Min. Order:1 Set
Cleanrooms Detail
ISO 8 modular cleanrooms provide a controlled environment that is essential for various applications in industries such as pharmaceuticals, biotechnology, and electronics. While not as stringent as ISO 7 cleanrooms, ISO 8 cleanrooms still play a vital role in maintaining product quality and ensuring safety during manufacturing and research processes.
Cleanroom Project Scope(from structure, HVAC,electric to autoc ontrol) | 1. Cleanroom Structure: Wall Panel, Ceiling Panel, Windows, Doors, Fttings, Flooring |
2. HVAC: AHU, Chiller, dehumidifier, Ducting, Piping, etc. | |
3. Electric: Lighting, Switch, Cables, Wires, Power Distribution Cabinet, etc | |
4. Auto- control: PLC Controller, Sensors for Humidity and Temperature, Control Panel | |
5. Process Piping System: Gas, Water Pipeline | |
Equipment | Air shower, Cargo shower, Mist shower, Dynamic pass box, Static pass box, Sampling booth,Weighing booth, Dispensing booth, |
Medicine stability test chamber, isolator, VHP sterilizer,Biological safety chamber, FFU, LAF, etc. | |
Temperature | 21-27*C (or as per required) |
Humidity | 30-60°C (or as per required) |
Application | Pharmaceutical factory, hospital, medical device factory, electronics factory, food factory,cosmetics factory, etc. |
Qualification Documents | CE GMP ISO |
Full Service | FAT and SAT Service, Professional Consultation, Training, 24 hours technical support |
ISO 8 Cleanroom Standards
No more than 3,520,000 particles per cubic meter of air (0.5 micrometers and larger).
No more than 29,300 particles per cubic meter of air (5 micrometers and larger).
Cleanrooms Airflow
In an ISO 8 modular cleanroom, effective airflow management is crucial to maintaining the required cleanliness levels and ensuring a safe working environment. While ISO 8 cleanrooms do not have as strict particle limits as ISO 7 cleanrooms, controlling airflow is still essential for minimizing contamination and providing a stable environment for various applications.
Key Features of Airflow in ISO 8 Cleanrooms
Air Changes per Hour (ACH)
ISO 8 cleanrooms typically require a minimum of 20 to 40 air changes per hour. This ensures that any contaminants introduced into the cleanroom are quickly diluted and removed.
The exact number of air changes may vary based on the specific processes being conducted and the layout of the cleanroom.
Return Air System
Effective return air systems help recirculate air back to the filtration units, ensuring that the cleanroom maintains its cleanliness standards. The design of the return air pathways is important to avoid dead zones where contaminants could accumulate.
Cleanrooms Installation
Cleanrooms Testing
Importance of testing
Clean room testing is extremely important to ensure product quality and the stability of the production environment. It can help to confirm whether the clean room meets the intended cleanliness requirements, and whether the various environmental indicators comply with the specified standards.
Testing Items
Suspended particles: Detects the number of suspended particles in the air in the clean room to ensure that the air cleanliness is up to standard.
Temperature and humidity: Monitor the temperature and humidity in the clean room to ensure environmental stability during the production process.
Noise: Evaluates the noise level in the clean room to minimize the impact on staff.
Static electricity: Detect static electricity buildup in the clean room to prevent damage to sensitive components from electrostatic discharge.
Microbial contamination: Detecting microbial levels in the clean room, especially critical for the healthcare industry.
FAQ
What is the typical size of an ISO 8 modular cleanroom?
The typical size of an ISO 8 modular cleanroom varies widely.
Common dimensions range from 100 to 1,000 square feet, depending on specific needs.
Customization allows for tailored sizes to fit particular applications or workflows.
What is the significance of cleanroom airflow patterns?
Cleanroom airflow patterns are crucial for maintaining cleanliness and preventing contamination.
Proper airflow helps direct particles away from critical areas and ensures uniform distribution of filtered air.
Effective airflow patterns can be classified as laminar flow, turbulent flow, or a combination of both, depending on application requirements.
What are the maintenance requirements for ISO 8 cleanrooms?
Maintenance of ISO 8 cleanrooms involves regular cleaning and inspection.
Key requirements include:
- Routine cleaning of surfaces
- Monitoring air filtration systems
- Calibration of monitoring equipment
Following a strict maintenance schedule is essential for compliance and performance.
How is cleanroom performance measured?
Cleanroom performance is measured using various metrics.
Key performance indicators include particulate counts, temperature, humidity, and airflow rates.
These measurements help ensure compliance with cleanliness standards and operational efficiency. Regular audits are essential to maintain performance.
How do I troubleshoot cleanroom issues?
To troubleshoot cleanroom issues, start by identifying the problem source. Common issues include contamination and equipment failure.
Conduct a thorough investigation to determine root causes and implement corrective actions.
Regular monitoring and documentation help prevent future issues and ensure operational integrity.
What is the role of temperature control in cleanrooms?
Temperature control in cleanrooms is vital for product integrity and personnel comfort.
Maintaining stable temperatures prevents adverse effects on sensitive materials and processes.
Typically, cleanrooms require constant monitoring to ensure compliance with established temperature ranges.
How do I manage waste disposal in a cleanroom environment?
Managing waste disposal in a cleanroom involves strict protocols to minimize contamination.
Waste must be categorized, including:
- Hazardous waste
- Non-hazardous waste
- Recyclables
Using designated containers for each type ensures proper handling and disposal.
How do I assess the cleanliness of a cleanroom?
Assessing the cleanliness of a cleanroom involves measuring airborne particles and surface contamination.
Common methods include:
- Airborne particle counting
- Surface swabbing and testing
- Microbial monitoring
These assessments ensure compliance with ISO standards and help maintain operational integrity.
What are the best materials for cleanroom walls?
The best materials for cleanroom walls include:
- Painted steel
- Fiberglass-reinforced panels
- High-density polyethylene
These materials provide durability, ease of cleaning, and resistance to contamination.
Selecting the right materials is essential for maintaining cleanliness and safety standards.
What is the role of positive pressure in cleanrooms?
Positive pressure in cleanrooms helps prevent contamination from outside sources.
By maintaining higher internal pressure, cleanrooms can effectively push out airborne contaminants.
This pressure is crucial in ensuring that clean air flows out when doors are opened, protecting the sterile environment.
What are the challenges of building a modular cleanroom?
Building a modular cleanroom presents several challenges.
Common issues include:
- Ensuring compliance with regulatory standards
- Customizing designs for specific processes
- Integrating existing facilities with new systems
Addressing these challenges early in the design phase is essential for successful implementation.
What is the lifespan of a modular cleanroom?
The lifespan of a modular cleanroom typically ranges from 10 to 20 years.
Factors affecting longevity include usage frequency, maintenance practices, and environmental conditions.
Regular inspections and maintenance can extend the cleanroom's operational life significantly.
How can I minimize the risk of contamination in a cleanroom?
Minimizing contamination risk in a cleanroom involves several strategies.
Key practices include:
- Strict gowning protocols
- Regular cleaning and disinfection
- Monitoring airflow and temperature
Implementing these practices consistently is vital for maintaining cleanliness standards.
How does airflow work in a modular cleanroom?
Airflow in a modular cleanroom is designed to maintain a controlled environment.
Typically, air is filtered and circulated through HEPA or ULPA filters, ensuring cleanliness.
The airflow can be laminar or turbulent, depending on the cleanroom's specific requirements.
What are the key performance indicators for cleanrooms?
Key performance indicators (KPIs) for cleanrooms include:
- Airborne particulate levels
- Temperature and humidity control
- Airflow velocity
Monitoring these KPIs ensures compliance with cleanliness standards and operational efficiency.
How do I monitor environmental conditions in a cleanroom?
Monitoring environmental conditions in a cleanroom involves using specialized instruments.
Key tools include:
- Temperature and humidity sensors
- Particlecounters
- Airflow monitors
These tools provide real-time data to ensure compliance with cleanroom standards and facilitate quick adjustments.
What are the best practices for cleanroom usage?
Best practices for cleanroom usage include strict adherence to gowning protocols and cleanliness.
Personnel should minimize movement and use designated paths to reduce contamination risks.
Regular training and audits are essential to reinforce these practices and maintain a controlled environment.
How often should cleanroom filters be replaced?
Cleanroom filters should typically be replaced every 6 to 12 months.
Factors such as usage intensity, contamination levels, and filter type can influence replacement frequency.
Regular inspection and monitoring of filter performance are essential for maintaining cleanroom air quality.
What are the benefits of a modular cleanroom?
Modular cleanrooms offer several benefits, including:
- Flexibility in design and layout
- Quick installation and scalability
- Cost-effectiveness compared to traditional cleanrooms
These advantages make modular cleanrooms an attractive option for various industries.
How do I select cleanroom-compatible equipment?
Selecting cleanroom-compatible equipment involves checking for specific certifications.
Key considerations include:
- Non-porous materials
- Easy-to-clean surfaces
- Low particle generation
Ensuring equipment meets cleanroom standards is crucial for maintaining a controlled environment.
What is a modular cleanroom?
A modular cleanroom is a prefabricated facility designed for controlled environments.
These cleanrooms are built using interlocking panels that allow for easy assembly and customization.
They provide flexibility in design and can be adapted to meet specific industry needs.
What types of pass-through systems are used in cleanrooms?
Pass-through systems in cleanrooms facilitate the transfer of materials without compromising cleanliness.
Common types include:
- Manual pass-throughs
- Automatic pass-throughs
- Interlocked pass-throughs
These systems help minimize contamination risks and streamline operations.
What safety protocols are essential for cleanroom operations?
Essential safety protocols for cleanroom operations include proper gowning procedures and training.
Personnel should be trained on emergency procedures and handling of hazardous materials.
Regular audits and adherence to SOPs ensure a safe working environment in the cleanroom.
Factory Production Workshop Video
Factory Photo
Product Packaging And International Logistics
Product International Certification
Find Other Common Equipment Recommendations
-
Modular CleanRoom
US$9000-10000 USD/Unit
Min. Order:1 Set -
Air Shower
US$1000.00-5000.00 USD/Unit
Min. Order:1 Set -
Downflow Booth
US$3000-6000 USD/Unit
Min. Order:1 Set -
Clean bench
US$600-2000 USD/Unit
Min. Order:1 Set -
Air Filter
US$3-50 USD/Unit
Min. Order:1 Set -
Cleanroom Wall Panels
US$10-20 USD/sq.
Min. Order:1 Set -
Pass Box
US$200-500 USD/Unit
Min. Order:1 Set -
FFU
US$135-350 USD/Unit
Min. Order:1 Set -
Fume Hood
US$700-1500 USD/Unit
Min. Order:1 Set -
Cleanroom HVAC
US$5000-20000 USD/Unit
Min. Order:1 Set -
Clean room floor
US$5-20 USD/Sq.
Min. Order:1 Set -
Clean room ceiling
US$
Min. Order:1 Set