GMP Class B Clean Room
A GMP Class B Clean Room is a controlled environment used in pharmaceutical and biotechnology industries, where stringent cleanliness standards are required to ensure the safety, efficacy, and quality of products.
GMP Class B Clean Room Specifications:
Particle Count: Maximum 3,520,000 particles per cubic meter (for 0.5 microns and larger)
Air Filtration: HEPA filters (high-efficiency particulate air) for air purification
Airflow: Minimum of 60 air changes per hour (ACH), with uniform laminar flow for optimal particle removal
Temperature & Humidity: Typically set between 18-22°C (64-72°F) and 30-60% relative humidity
Pressure: Positive pressure relative to adjacent areas to prevent contamination ingress
Lighting: Must provide uniform, shadowless lighting suitable for aseptic tasks
Cleanability: Materials and surfaces used must be non-porous, smooth, and easy to clean
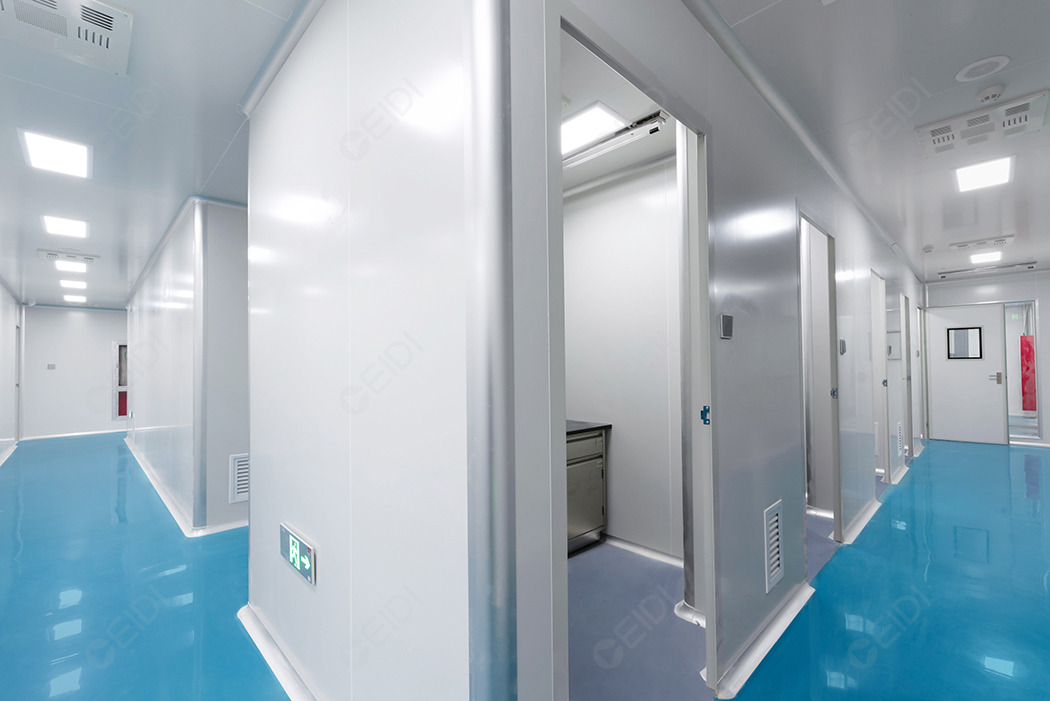
GMP Class B Cleanroom Air Changes Per Hour
Class B Cleanroom (ISO 6 Cleanroom)
The filtered air sweeps down the room in a unidirectional way, at a velocity generally between 0.3 m/s and 0.5 m/s, and exits through the floor, removing the airborne contamination from the room. Cleanrooms using unidirectional air flow are more expensive than non-unidirectional ones, but can comply with more stringent classifications, such as ISO 5 or lower. |
GMP Class B Clean Room Grade Table
|
|
Key Characteristics of Class B Clean Room
Class B cleanrooms typically adhere to an acceptable particle count of ≤ 3,520 particles per cubic meter for particles ≥ 0.5 microns. The air quality and cleanliness level are slightly less stringent compared to Class A but still ensure that the environment remains clean enough to prevent contamination during manufacturing processes. | |
Class B cleanrooms typically have a high air change rate, generally between 30 to 60 air changes per hour (ACH). This ensures the removal of contaminants and helps maintain positive pressure relative to adjacent areas. | |
![]() |
Class B cleanrooms typically have a high air change rate, generally between 30 to 60 air changes per hour (ACH). This ensures the removal of contaminants and helps maintain positive pressure relative to adjacent areas. |
![]() |
Strict gowning procedures are required to prevent the introduction of contaminants by personnel. This includes wearing appropriate protective clothing such as gowns, gloves, masks, hair covers, and shoe covers. |
![]() |
Sterile Product Preparation: Class B cleanrooms are commonly used in the preparation of materials and intermediate products for sterile manufacturing processes. Secondary Packaging: Packaging operations for sterile products that require a controlled environment are often carried out in Class B cleanrooms. Sterilization Process: After products are sterilized, Class B environments may be used for the handling and transfer of these products to final packaging, ensuring that no contamination occurs during this intermediate step. |
![]() |
Manufacturing of Sterile Medical Devices: Class B cleanrooms are used for processes such as the assembly, inspection, and packaging of sterile medical devices that do not require direct aseptic conditions but must still be handled in a clean environment. This can include devices like surgical instruments, diagnostic tools, and other disposable medical products. |
![]() |
Manufacturing of Sterile Medical Devices: Class B cleanrooms are used for processes such as the assembly, inspection, and packaging of sterile medical devices that do not require direct aseptic conditions but must still be handled in a clean environment. This can include devices like surgical instruments, diagnostic tools, and other disposable medical products. |
![]() |
Cell Handling and Transfection: In gene therapy or cell therapy, Class B cleanrooms may be used for intermediate steps, such as cell handling, transfection, or viral vector production, where aseptic techniques are important but direct contact with final sterile products is not required. |
GMP Class B Clean Room Wall
| |
| |
|
GMP Class B Clean Room Celling
![]() | ![]() | ![]() | ![]() |
|
| ||
![]() | ![]() | ![]() | ![]() |
|
|
GMP Class B Clean Room Floor
![]() | ![]() | ![]() |
| ||
![]() | ![]() | ![]() |
| ||
![]() | ![]() | ![]() |
|
FAQ
Q: What is GMP class A and B cleanroom environments?
A: GMP Class A and B cleanrooms are highly controlled environments used in pharmaceutical and biotechnology industries to ensure the production of sterile and high-quality products. Class A is the most stringent, used for critical processes such as aseptic filling or handling sterile products. It has the lowest allowable particle counts and requires the highest level of air filtration and control. Class B cleanrooms, though slightly less stringent, still maintain high standards for cleanliness and are used for processes such as preparation and sterilization of products, often acting as an intermediate environment before the product enters the Class A area.
Q: What is a class B cleanroom?
A: A Class B cleanroom is an environment used in industries like pharmaceuticals and biotechnology, where the air cleanliness level is highly controlled but not as stringent as Class A. It is designed for operations such as preparing sterile products, secondary packaging, or sterilization of components. Class B cleanrooms maintain particle counts of ≤ 3,520 particles per cubic meter for particles ≥ 0.5 microns and are typically used for processes that do not involve direct aseptic handling but still require a controlled, low-contamination environment.
Q: What are the GMP cleanliness classifications?
A: The GMP cleanliness classifications are a set of standards for controlling the cleanliness of environments in pharmaceutical manufacturing. These classifications are based on the allowable number of particles per cubic meter of air. They are divided into classes, such as Class A, B, C, and D, with Class A being the most stringent and requiring the lowest levels of contamination, and Class D being the least stringent. These classifications are designed to ensure that cleanroom environments meet the required standards for manufacturing sterile drugs, medical devices, and other sensitive products.
Q: What is GMP in clean room?
A: GMP (Good Manufacturing Practice) in cleanroom refers to the regulations and standards set by health authorities, like the FDA and EMA, to ensure that products, especially pharmaceuticals and medical devices, are produced under controlled, hygienic conditions. These practices include monitoring environmental parameters such as temperature, humidity, and particulate levels, maintaining proper hygiene and gowning protocols, and ensuring that cleanroom processes minimize contamination risks during manufacturing.
Q: What is clean room classification B?
A: Cleanroom Classification B refers to a cleanroom environment that meets specific cleanliness standards according to the ISO 14644-1 classification system. It allows up to 3,520 particles per cubic meter for particles ≥ 0.5 microns and is used for processes like secondary packaging, sterilization, and preparation of sterile materials. Class B is considered less stringent than Class A but still maintains a high level of cleanliness and air control, preventing contamination in non-aseptic processing areas.
Q: What ISO class is grade B?
A: Grade B cleanrooms correspond to ISO Class 5 in the ISO 14644-1 classification system. ISO Class 5 allows up to 3,520 particles per cubic meter of air for particles ≥ 0.5 microns and is used for environments where contamination control is critical but not as stringent as ISO Class 3 (Grade A) cleanrooms, which are used for aseptic filling and direct handling of sterile products.
Q: What are the classification levels of clean rooms?
A: Cleanrooms are classified into four main levels based on the allowable particle count per cubic meter of air: Class A, Class B, Class C, and Class D. These levels correspond to ISO 14644-1 standards, with Class A (ISO Class 3) being the most stringent, used for aseptic processing, and Class D (ISO Class 8) being the least stringent, used for less critical processes that still require controlled environments.
Q: What is the difference between Grade A and Grade B clean rooms?
A: The primary difference between Grade A (Class A) and Grade B (Class B) cleanrooms is the level of cleanliness required. Grade A cleanrooms are the most sterile, designed for aseptic processing, and have the strictest air cleanliness standards, typically allowing only a very low number of particles (ISO Class 3). In contrast, Grade B cleanrooms are used for processes like preparation and sterilization but do not involve direct aseptic handling, so the cleanliness requirements are less stringent, allowing for more particles in the air (ISO Class 5).
Q: What is a grade D cleanroom?
A: A Grade D cleanroom is an environment with the least stringent cleanliness requirements in the pharmaceutical cleanroom classification system. It corresponds to ISO Class 8, allowing up to 352,000 particles per cubic meter of air for particles ≥ 0.5 microns. Grade D cleanrooms are typically used for less critical processes, such as storing raw materials or packaging, where the risk of contamination is lower compared to more critical areas like Grade A or Grade B.
Q: What is class A clean room?
A: A Class A cleanroom is the highest level of cleanliness in the cleanroom classification system, typically used in aseptic processes such as sterile filling, direct contact with sterile products, or critical stages of drug manufacturing. Class A cleanrooms correspond to ISO Class 3 and allow a very low number of particles per cubic meter of air (≤ 3520 particles per cubic meter for particles ≥ 0.5 microns), ensuring the highest level of contamination control.
Q: What is the FDA classification of clean rooms?
A: The FDA classifies cleanrooms based on the level of particulate contamination allowed in the environment, typically using the GMP (Good Manufacturing Practice) classification system. The FDA typically references ISO 14644-1 standards for cleanroom classifications, where Class A is the most stringent and used for aseptic processing, and Class D is the least stringent, used for less critical operations. These classifications ensure compliance with cleanliness standards for drug and medical device manufacturing.
Q: What is type A B and C cleaning in pharma?
A: Type AB and C cleaning in pharmaceuticals refers to different cleaning and sterilization procedures based on the classification of the environment. Type A refers to aseptic cleaning, used in highly controlled environments like Class A cleanrooms for aseptic filling. Type B and Type C cleaning refer to less stringent procedures in Class B and C cleanrooms, where contamination risks are lower but still require controlled cleaning processes to maintain environmental standards.
Q: What are the classification of pharmaceutical cleanrooms?
A: Pharmaceutical cleanrooms are classified into four main grades: Grade A (ISO Class 3), Grade B (ISO Class 5), Grade C (ISO Class 7), and Grade D (ISO Class 8). Grade A is used for aseptic processes and direct sterile product handling, while Grade B is used for processes like packaging and sterilization. Grade C and D are less stringent and used for non-critical manufacturing steps, with lower particle counts and less rigorous air filtration.
Q: What is grade B cleanroom?
A: A Grade B cleanroom is a controlled environment used for processes like secondary packaging, sterilization, and preparation of sterile materials. It corresponds to ISO Class 5 and allows up to 3,520 particles per cubic meter for particles ≥ 0.5 microns. Grade B cleanrooms have strict cleanliness standards but are less stringent than Grade A cleanrooms, which are used for aseptic processing.
Q: What is type C cleaning in pharma?
A: Type C cleaning in pharma refers to cleaning procedures used in Class C cleanrooms (ISO Class 7), which are less stringent than Class A or B environments but still maintain significant contamination control. Type C cleaning includes protocols for maintaining hygiene, removing contaminants, and ensuring that the environment remains suitable for less critical operations, such as the preparation and packaging of non-sterile products.
Q: What is class D clean room?
A: A Class D cleanroom is an environment with the least stringent cleanliness standards in the cleanroom classification system, corresponding to ISO Class 8. Class D cleanrooms are used for processes that have a low risk of contamination, such as raw material storage, packaging, or certain administrative activities. They allow for a higher level of airborne particles compared to higher-class rooms like A, B, or C.
Q: What is the air changes for a cleanroom classification?
A: The number of air changes per hour (ACH) for a cleanroom depends on its classification. Class A cleanrooms typically require 300 ACH or more to maintain strict air quality standards, while Class B cleanrooms may require 30 to 60 ACH. Class C and D cleanrooms require fewer air changes, often between 20 and 30 ACH, depending on the specific needs of the environment.
Q: What is the classification of ABCD in cleanroom?
A: The ABCD classification in cleanrooms refers to the four primary cleanliness levels: Class A (ISO Class 3), Class B (ISO Class 5), Class C (ISO Class 7), and Class D (ISO Class 8). These classifications are based on the allowed number of particles per cubic meter of air for particles ≥ 0.5 microns, with Class A being the most stringent and Class D the least, reflecting the level of contamination control required for each type of cleanroom process.
Q: What is Grade D air classification?
A: Grade D air classification corresponds to ISO Class 8 in the cleanroom classification system. It allows for a higher number of particles per cubic meter (up to 352,000 particles ≥ 0.5 microns) and is used for less critical processes in pharmaceutical manufacturing. Grade D environments are
Related Information
-
共1页 8条