Class 1000 Clean room_第2页
A Class 1000 cleanroom, also known as an ISO Class 6 cleanroom under the ISO 14644-1 standard, is a controlled environment designed to maintain very low levels of airborne particles. Specifically, it allows no more than 1,000 particles per cubic foot of air for particles ≥0.5 microns, which translates to no more than 35,200 particles per cubic meter.
Particle Concentration Limits
Particles ≥ 0.5 microns: 1,000 particles per cubic foot (35,200 particles per cubic meter)
Particles ≥ 5.0 microns: 293 particles per cubic meter
Airflow and Filtration
HEPA Filters (High-Efficiency Particulate Air filters): These filters must remove at least 99.97% of airborne particles 0.3 microns in diameter.
Laminar Flow: Often utilized to ensure that air flows in a single direction, reducing turbulence and the potential for particle contamination.
High Air Change Rates: Typically around 150-240 air changes per hour to maintain the required cleanliness.
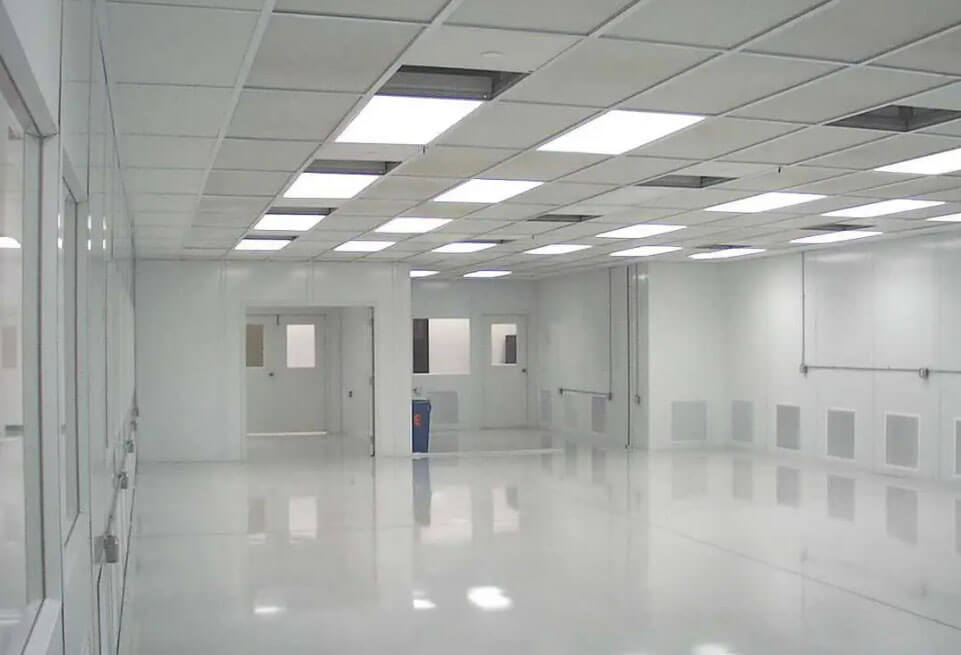
Class 1000 Cleanroom Air Changes Per Hour
Class 1000 Cleanroom (ISO 6 Cleanroom)
|
Clean room grade table
|
|
|
Class 1000 Clean Room Airflow
| |
|
Class 1000 Clean Room wall
| |
| |
|
Class 1000 Clean Room Celling
![]() | ![]() | ![]() | ![]() |
|
| ||
![]() | ![]() | ![]() | ![]() |
|
|
Class 1000 Clean Room Floor
| ||
![]() | ![]() | ![]() |
| ||
![]() | ![]() | ![]() |
|
FAQ
What is class 1000 cleanroom?
A Class 1000 cleanroom, or ISO Class 6, is a controlled environment that limits airborne particles to no more than 1,000 particles per cubic foot for particles ≥0.5 microns (35,200 particles per cubic meter). It requires advanced HEPA filtration and moderate air change rates, typically 150 to 240 per hour, to maintain cleanliness. The room must be constructed with non-shedding materials, and personnel must follow strict gowning protocols, including wearing hair covers, face masks, gloves, and cleanroom suits. These cleanrooms are used in industries such as pharmaceuticals, biotechnology, and electronics, where a high level of contamination control is necessary.
What does class 10,000 clean room mean?
A Class 10,000 cleanroom, also known as ISO Class 7, is an environment that limits airborne particles to no more than 10,000 particles per cubic foot for particles ≥0.5 microns (352,000 particles per cubic meter). It requires effective HEPA filtration and air change rates of 60 to 120 per hour. The cleanroom is built using smooth, non-shedding materials, and personnel must adhere to gowning protocols, including wearing smocks, hair covers, and shoe covers. These cleanrooms are typically used in industries where moderate contamination control is required, such as in pharmaceuticals, aerospace, and medical device manufacturing.
What is a Class 100000 clean room?
A Class 100,000 cleanroom, or ISO Class 8, is a controlled environment that limits airborne particles to no more than 100,000 particles per cubic foot for particles ≥0.5 microns (3,520,000 particles per cubic meter). It requires effective air filtration, typically with HEPA filters, and moderate air change rates of 10-25 per hour. The room must be constructed with smooth, easy-to-clean materials, and personnel must follow basic gowning protocols, such as wearing lab coats, hair covers, and shoe covers. These cleanrooms are used for less contamination-sensitive tasks like general manufacturing and electronics assembly.
What are the gowning requirements for Class 1000 cleanroom?
For a Class 1000 cleanroom, also known as ISO Class 6, strict gowning protocols are essential to minimize contamination. Personnel must wear full-body cleanroom suits made from non-linting materials, including coveralls, hoods, and boots. Additional protective gear includes gloves, face masks, and sometimes goggles or safety glasses to ensure no skin or hair is exposed. Before entering the cleanroom, personnel typically pass through an anteroom where they don these garments, and they may also need to use an air shower to remove any remaining particulates from their attire.
What does ISO Class 6 mean?
ISO Class 6 refers to a cleanroom classification under the ISO 14644-1 standard, indicating that the environment limits airborne particles to no more than 1,000 particles per cubic meter for particles ≥0.5 microns. This level of cleanliness requires advanced HEPA filtration systems and a high air change rate to maintain air purity. The room must be constructed with materials that do not shed particles and are easy to clean. Personnel must follow stringent gowning procedures to prevent contamination, making it suitable for industries like pharmaceuticals, biotechnology, and electronics manufacturing.
What is a modular clean room?
A modular cleanroom is a flexible, prefabricated controlled environment designed to meet specific cleanliness standards. Unlike traditional cleanrooms built from scratch, modular cleanrooms consist of pre-engineered panels and components that can be quickly assembled, reconfigured, or expanded as needed. These cleanrooms use standard air filtration systems, such as HEPA filters, to maintain the desired cleanliness level. Their modular nature allows for cost-effective and rapid deployment, making them ideal for industries like pharmaceuticals, biotechnology, and electronics, where the need for cleanroom space can change over time.
What is the ISO standard for clean room classification?
The ISO standard for cleanroom classification is ISO 14644-1. This standard defines the levels of cleanliness in terms of airborne particulate concentration, categorizing cleanrooms from ISO Class 1 (the cleanest) to ISO Class 9 (the least clean). Each class specifies the maximum allowable number of particles per cubic meter at different particle sizes. The standard provides guidelines for the design, construction, and operation of cleanrooms to ensure they meet the required cleanliness levels, supporting various industries such as pharmaceuticals, biotechnology, microelectronics, and aerospace in maintaining product quality and safety.
What is class 1000 clean room?
A Class 1000 cleanroom, or ISO Class 6, is a controlled environment that restricts airborne particles to no more than 1,000 particles per cubic foot for particles ≥0.5 microns (35,200 particles per cubic meter). It employs advanced HEPA filtration and high air change rates, typically 150 to 240 per hour, to maintain cleanliness. The room is constructed with non-shedding materials, and personnel must adhere to strict gowning protocols, including wearing full-body suits, gloves, masks, and hair covers. These cleanrooms are used in industries such as pharmaceuticals, biotechnology, and electronics, where a high level of contamination control is crucial.
What is the difference between Class 100 and 1000 clean room?
The primary difference between Class 100 and Class 1000 cleanrooms is the level of allowable airborne particles. A Class 100 cleanroom (ISO Class 5) restricts airborne particles to no more than 100 particles per cubic foot for particles ≥0.5 microns, requiring more stringent air filtration and higher air change rates. Conversely, a Class 1000 cleanroom (ISO Class 6) allows up to 1,000 particles per cubic foot for the same particle size, with slightly less stringent filtration and air change requirements. Consequently, Class 100 cleanrooms are used for more contamination-sensitive applications, such as semiconductor manufacturing, while Class 1000 cleanrooms serve industries like pharmaceuticals and biotechnology.
What are the requirements for Class 100000 clean room?
A Class 100,000 cleanroom, or ISO Class 8, must limit airborne particles to no more than 100,000 particles per cubic foot for particles ≥0.5 microns (3,520,000 particles per cubic meter). It requires effective air filtration, typically using HEPA filters, and moderate air change rates of 10-25 per hour. The cleanroom should be constructed with smooth, non-shedding materials that are easy to clean. Personnel must follow basic gowning protocols, including wearing lab coats, hair covers, and shoe covers. This environment is suitable for less contamination-sensitive activities, such as general manufacturing and electronics assembly.
What is the difference between a 10k and a 1k clean room?
The difference between a Class 10,000 (ISO Class 7) and a Class 1,000 (ISO Class 6) cleanroom lies in their allowable particle concentrations and cleanliness requirements. A Class 10,000 cleanroom permits up to 10,000 particles per cubic foot for particles ≥0.5 microns (352,000 particles per cubic meter), while a Class 1,000 cleanroom allows only up to 1,000 particles per cubic foot for the same particle size (35,200 particles per cubic meter). Consequently, Class 1,000 cleanrooms require more stringent filtration, higher air change rates, and stricter gowning protocols compared to Class 10,000 cleanrooms, making them suitable for more contamination-sensitive processes.
What is the ISO standard for clean room classification?
The ISO standard for cleanroom classification is ISO 14644-1. This standard defines cleanliness levels by specifying the maximum allowable concentration of airborne particles per cubic meter at various particle sizes, categorizing cleanrooms from ISO Class 1 (the cleanest) to ISO Class 9 (the least clean). It provides guidelines for designing, constructing, and operating cleanrooms to achieve and maintain the desired cleanliness levels. ISO 14644-1 supports industries such as pharmaceuticals, biotechnology, microelectronics, and aerospace in ensuring product quality and safety by controlling particulate contamination in controlled environments.