Clean room engineering
Clean room engineering involves the design, construction, and maintenance of controlled environments that minimize contamination and maintain specific cleanliness levels. This is particularly important in industries such as pharmaceuticals, biotechnology, electronics, and aerospace, where even minute levels of contamination can affect product quality and safety.
ISO 14644: The international standard for cleanroom classifications and environmental monitoring.
ISO 13485: A quality management standard for medical devices, requiring controlled manufacturing environments.
GMP (Good Manufacturing Practice): Guidelines for pharmaceutical production that mandate cleanroom standards to prevent contamination.
FDA (Food and Drug Administration): The FDA enforces cleanroom regulations for drug manufacturing and other critical health-related products.
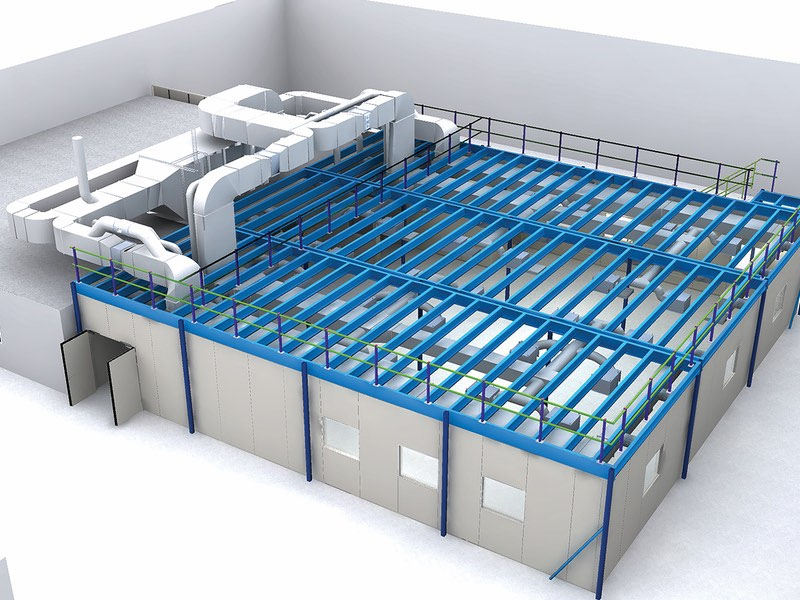
Cleanrooms 14644-1 grade table
ISO Class FED STD 209E Equivalent | |||||||
ISO Class | Maximum Particles/m | FED STD 209E equivalent | |||||
≥0.1μm | ≥0.2um | ≥0.3um | ≥0.5um | ≥11m | ≥5um | ||
ISO1 | 10 | 2 | |||||
ISO2 | 100 | 24 | 10 | 4 | |||
ISO3 | 1,000 | 237 | 102 | 35 | 8 | Class1 | |
ISO4 | 10,000 | 2,370 | 1,020 | 352 | 83 | 3 | Class10 |
ISO5 | 100,000 | 23,700 | 10,200 | 3,520 | 832 | 29 | Class100 |
ISO6 | 1,000,000 | 237,000 | 102,000 | 35,200 | 8,320 | 293 | Class 1,000 |
ISO7 | 352,000 | 83,200 | 2,930 | Class10,000 | |||
ISO8 | 3,520,000 | 832,000 | 29,300 | Class 100,000 | |||
ISO9 | 35,200,000 | 8,320,000 | 293,000 | Room Air |
Comparison Table GMP/USP/ISO/FED209E | ||||||||||||
project | China GMP/Europe GMP | ISO | FED STD 209E | |||||||||
Suspended particles P/m3 | level | Static | dynamic | level | Static | level | dynamic | |||||
≥0.5um | ≥5μm | ≥0.5μm | ≥5μm | ≥0.5um | ≥5μm | ≥0.5um | ≥5μm | |||||
A | 3520 | 20 | 3520 | 20 | M3.5 | 3530 | 100 | 5 | 2220 | 20 | 100 | |
B | 3520 | 29 | 352000 | 2900 | - | - | 6 | 3520 | 29 | 1000 | ||
C | 352000 | 2900 | 3520000 | 29000 | M5.5 | 353000 | 10000 | 7 | 352000 | 2930 | 10000 | |
8. | 3520000 | 29300 | 100000 | |||||||||
D | 3520000 | 29000 | No regulations | No regulations | M6.5 | 3530000 | 100000 | 9 | 3520000 | 29300 | 100000 |
Comparison table of ISO grade standards and ventilation times | |
ISO Class | ACH(AIRCHANGE PER HOUR) |
ISO 3 | 360-540 |
ISO 4 | 300-540 |
ISO 5 | 240-480 |
ISO 6 | 50-60 |
ISO 7 | 30-40 |
ISO 8 | 15-25 |
Clean room projects in various industries
ISO 5 Cleanroom
| ISO 6 Cleanroom
|
ISO 7 Cleanroom
| ISO 8 Cleanroom
|
Clean room engineering design
Pharmaceuticals | Foods | Electronic |
| Division of areas
Personnel flow
Safety and hygiene
| Division of areas
|
Clean room engineering construction
Cleanroom Wall Panel Installation |
|
Ventilation System Installation |
|
Circuit System Installation |
|
Ground Construction |
|
Equipment Installation |
|
FAQ
What is a clean room?
A clean room is a controlled environment designed to minimize the presence of airborne particles, pollutants, and contaminants. It is typically used in industries such as pharmaceuticals, electronics, and biotechnology, where even small amounts of dust or microbes can affect product quality.
Clean rooms are equipped with specialized ventilation, filtration systems (like HEPA filters), and controlled temperature, humidity, and pressure to maintain a contamination-free environment.
They are classified based on the cleanliness level, with ISO standards defining the maximum allowable particle count.
What are the different types of clean rooms?
Clean Room Type | ISO Classification | Maximum Particles per Cubic Meter | Applications |
---|---|---|---|
Class 1 | ISO 1 | ≤ 1 particle (0.3 µm) | Semiconductor manufacturing, microelectronics |
Class 2 | ISO 2 | ≤ 10 particles (0.3 µm) | Pharmaceutical compounding, precision electronics |
Class 3 | ISO 3 | ≤ 100 particles (0.3 µm) | Biotechnology, drug manufacturing |
Class 4 | ISO 4 | ≤ 1000 particles (0.3 µm) | Aerospace, optics |
Class 5 | ISO 5 | ≤ 3,520 particles (0.5 µm) | Medical devices, biotechnology |
Class 6 | ISO 6 | ≤ 35,200 particles (0.5 µm) | Food production, electronics |
Class 7 | ISO 7 | ≤ 352,000 particles (0.5 µm) | Clean manufacturing areas, assembly |
Class 8 | ISO 8 | ≤ 3,520,000 particles (0.5 µm) | General clean environments, storage facilities |
What are the requirements for designing a clean room?
Designing a clean room requires careful consideration of several key factors:Air Quality Control: Maintain low levels of airborne particles.
1.Temperature Regulation: Ensure stable temperature for optimal conditions.
2.Humidity Control: Keep humidity levels within specified limits.
3.Material Selection: Use non-porous, easy-to-clean materials.
4.Personnel Training: Train staff on cleanroom protocols and hygiene.
5.Access Control: Limit entry to authorized personnel only.
6.Monitoring Systems: Implement continuous monitoring of environmental conditions.
7.Cleaning Protocols: Establish strict cleaning and maintenance schedules.
8.Equipment Design: Use equipment that minimizes contamination risks.
9.Emergency Procedures: Develop clear protocols for emergencies.
These requirements help ensure a controlled environment, supporting innovation and development in various industries.
What is the ISO standard for clean rooms?
How do I calculate the required air exchange rate for a clean room?
Ensure the airflow (CFM) and room volume (cubic feet) are accurately measured for the required clean room classification.
What are the main components of a clean room?
Air Filtration System:
HEPA or ULPA filters to remove airborne particles.
HVAC System:
Controls temperature, humidity, and airflow.
Room Materials:
Smooth, non-porous, easy-to-clean surfaces.
Lighting:
Dust-free, sealed lighting fixtures.
Flooring:
Anti-static, seamless, and easy-to-clean floors.
Personnel Equipment:
Gowns, gloves, masks, and shoe covers.
Monitoring Systems:
Sensors for temperature, humidity, and particle count.
Access Control:
Controlled entry and exit points.
Emergency Systems:
Fire suppression, alarms, and emergency lighting.
Cleanroom Furniture:
Easy-to-clean, non-contaminating furniture.
How does a clean room ventilation system work?
Airflow Control
A clean room ventilation system circulates air to maintain cleanliness by filtering out contaminants. It ensures a steady, controlled airflow that prevents particle buildup.
Filtration
HEPA or ULPA filters are used to trap particles, ensuring clean air is continuously supplied into the room.
Pressure and Temperature
The system maintains positive pressure to prevent outside contaminants and regulates temperature and humidity for optimal conditions.
What is a HEPA filter and why is it used in clean rooms?
What is a HEPA Filter?
A HEPA (High-Efficiency Particulate Air) filter is a specialized air filter designed to capture at least 99.97% of particles as small as 0.3 microns. It uses a dense mat of fibers to trap contaminants from the air.
Function in Clean Rooms
In clean rooms, HEPA filters are crucial for maintaining air purity by removing dust, bacteria, and other airborne particles. They are installed in HVAC systems to filter out contaminants from the incoming air supply.
Importance in Contamination Control
HEPA filters help ensure that the environment meets stringent cleanliness standards, which is vital in industries like pharmaceuticals, electronics, and biotechnology, where even small amounts of contamination can compromise product quality.
Related Information
-
共1页 1条