In today’s fast-paced technological and industrial advancements, maintaining a contaminant-free environment is crucial for the production and processing of sensitive products.
Understanding hardwall Cleanrooms
Hardwall cleanrooms are specialized facilities characterized by a rigid, sealed construction aimed at providing unparalleled control over environmental conditions. Their design often incorporates modular panels, facilitating HVAC integration to regulate temperature, humidity, and air purity effectively.
Key Features
- Sealed Construction: Ensures no particulate penetration from the outside environment, maintaining stringent cleanliness levels.
- HVAC Integration: Customizable systems ensure optimal air quality and consistency, crucial for applications requiring precise control.
- Modularity: Facilitates easy installation, expansion, and customization to meet evolving industry demands.
Advantages of Hardwall Cleanrooms
Hardwall cleanrooms offer significant benefits, making them indispensable in hygiene-critical environments.
- Top-notch Environmental Control: Superior control over air pressure, temperature, and humidity distinguishes these cleanrooms.
- Ease of Installation: Their modular nature allows for rapid construction and deconstruction, minimizing operational disruption.
- Scalability: As businesses grow, these cleanrooms can be easily expanded or modified without extensive infrastructural changes.
- Low Maintenance Requirements: Built with durable materials, they require minimal maintenance, reducing long-term operational costs.
- Compliance with Stringent Standards: Meet various international Cleanroom standards, including ISO Class 1 to Class 10,000.
Applicable Industries
Hardwall cleanrooms have versatile applications, serving as essential components across numerous sectors:
- Medical Devices: Ensures sterile and controlled environments for manufacture and assembly.
- Biopharmaceuticals: Critical for minimizing contamination risks in drug formulation.
- Semiconductor Production: Protects microElectronics manufacturing from contamination.
- Electronics Manufacturing: Provides precision-clean environments for components.
- Aerospace: Facilitates components' fabrication under stringent conditions.
- Laboratories: Supports controlled experimental and testing environments.
Design Requirements
HVAC Standards
Air Changes per Hour (ACH) is critical in maintaining cleanroom conditions and varies by ISO class. The following table provides a general guideline:
ISO Class | Air Changes per Hour |
---|---|
1 | >480 |
2 | 240-480 |
3 | 150-240 |
4 | 60-90 |
5 | 50-60 |
6 | 30-60 |
7 | 10-20 |
8 | 5-10 |
Hardwall Cleanroom Features
- Sealed Seams: Prevents ingress of contaminants, ensuring environmental integrity.
- Anti-static Surfaces: Safeguards against electrostatic discharge damage to sensitive equipment.
- Pressure Differential: Maintains ≥0.03–0.05 in. H2O to prevent cross-contamination.
- ISO Compliance: Aligns with ISO 14644 standards for air purity and environmental conditions.
Material Equipment and Layout Requirements
- Anti-static ESD Materials: Essential for controlling static discharge in electronic environments.
- LED or UV-filtered Lighting: Ensures visibility while minimizing UV damage.
- Ceiling System: Supports HEPA or ULPA filters for air purity maintenance.
- flooring: Durable options like epoxy coatings or PVC tiles for sterile surfaces.
- Designated Areas: Zones for dressing, inspection, and logistics to enhance contamination control.
Real-time monitoring and Compliance
To ensure ongoing compliance and operational efficiency, real-time monitoring systems are vital:
Continuous Particle Counting
Implementing continuous particle counting systems ensures that particle levels remain within defined limits for each ISO class. For instance, ISO 7 necessitates maintaining levels at ≤352,000 particles/m³ for particles ≥0.5µm.
Environmental Recording
- Standard Sensor Data Recording: Regular monitoring of temperature, humidity, and pressure.
- Compliance with Industry Standards: Utilizing equipment aligned with global standards like ISO 14644.
Industry-specific Applications and Standards
- Medical Devices: Cleanrooms for medical devices range from ISO Class 5 to ISO Class 8, determined by the manufacturing process and the nature of the product being manufactured. It is critical that devices remain sterile until use, and bioburden control ensures the quality of production of sterile and non-sterile medical devices, as well as regular monitoring to measure and control microbial contamination.
- Biopharmaceuticals: Biopharmaceutical cleanrooms typically operate between ISO Class 5 and Class 7, maintaining GMP and ISO Standards through particulate matter and microbial monitoring, ensuring specific temperature, humidity, and pressure conditions are maintained to safeguard product integrity and efficacy.
-
Semiconductor Production: Semiconductor production typically requires ISO Class 1 to 5 cleanrooms. Temperature and humidity control, particle control, and electrostatic discharge (ESD) control maintain the stability and functionality of semiconductor materials and processes, prevent defects in microelectronics manufacturing, and ensure that sensitive electronic components are protected from damage by static electricity.
Brand Highlight: Deiiang
Deiiang stands out in the cleanroom industry by providing innovative solutions tailored to meet these strict regulatory standards. Their products are renowned for quality and durability, making them an asset in any cleanroom setup, ensuring that customers receive reliable performance and compliance assurance.
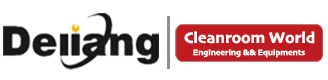
Hardwall cleanrooms are indispensable in industries where precision and contamination control are paramount. By understanding their design and operation, businesses ensure optimal performance and product quality.