Cleanroom FFU,Fan Filter Unit,34.5' x 46.3',Air volume:1500m³/h
Reference Price:US$from $120


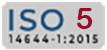
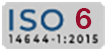
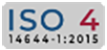
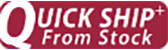
Cleanroom
Cleanroom FFU,Fan Filter Unit,34.5' x 46.3',Air volume:1500m³/h
Choose your installation & validation options below
Quantity:
Choose your Cleanroom frame structure material
Quantity:
Choose your Cleanroom Wall enclosure materials
Quantity:
Choose your Temperature requirements
Quantity:
Choose your humidity requirements
Quantity:
Choose your Explosion-proof requirements
Quantity:
Summary
Cleanroom FFU,Fan Filter Unit,34.5' x 46.3',Air volume:1500m³/h
Validation
Installation & Validation
Find Similar Products
Features
The Cleanroom Fan Filter Unit (FFU) is an essential device designed to maintain high air quality in controlled environments. Measuring 34.5' x 46.3', this unit effectively filters and circulates air, ensuring a contaminant-free atmosphere. With an air volume capacity of 1500 m³/h,
it is ideal for use in cleanrooms, laboratories, and other sensitive settings where precise air cleanliness is crucial for operational success and regulatory compliance.
Cleanroom FFU Product Details:
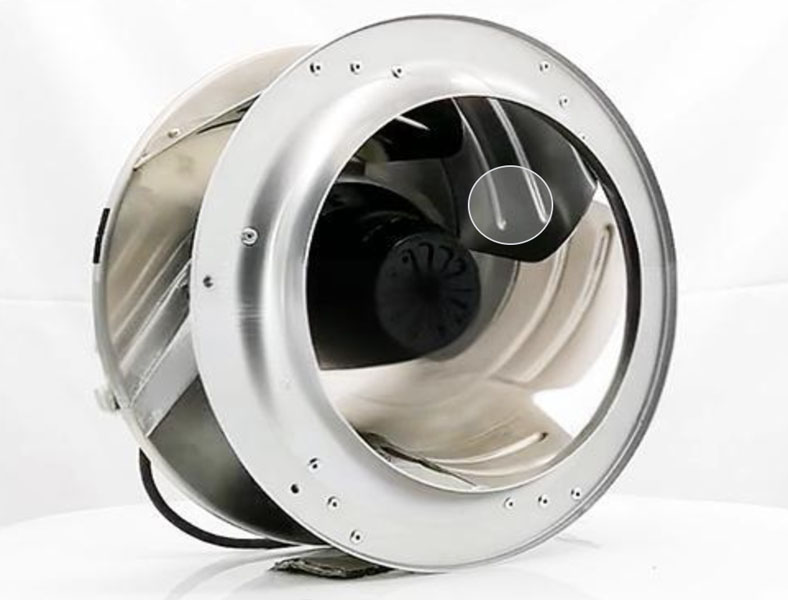
01Advanced fan technology
Low noise operation
Energy saving motor
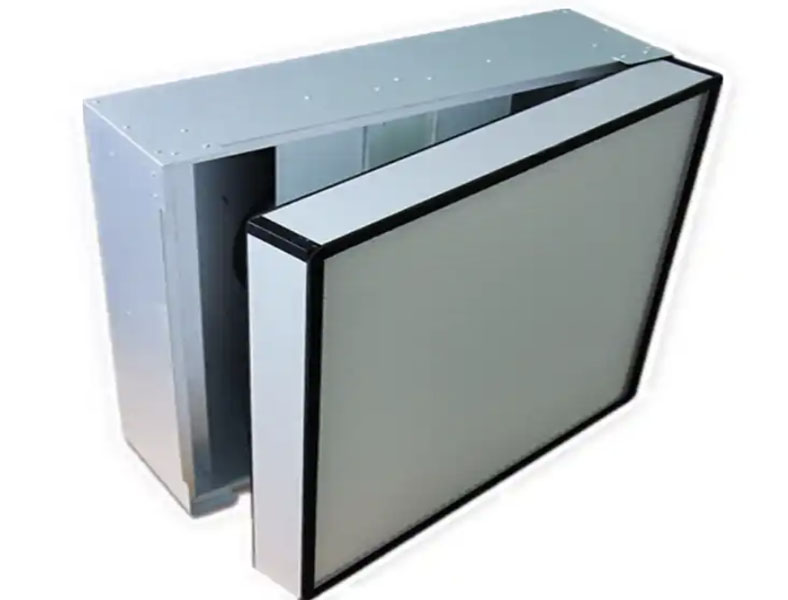
02Air filter
High efficiency HEPA/ULPA filter
Stable airflow distribution
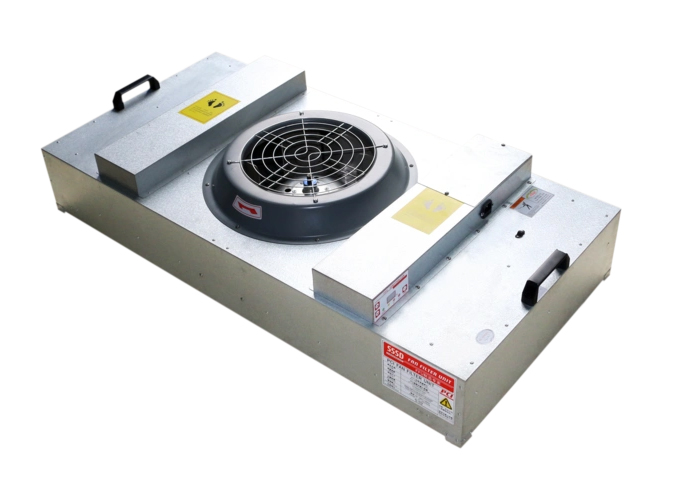
03Installation and Maintenance
Easy to install and maintain
Compact design for flexible integration
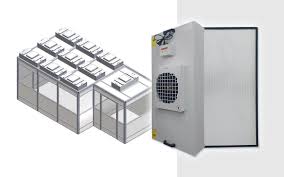
04Compliance with international standards
Compliant with ISO cleanroom standards
Advanced fan technology for improved air circulation
Work Principle
Structural components: fan, filter, housing
Air flow: The fan draws in ambient air, which passes through the filter.
Filtration process: the filter removes particles (e.g. dust, microorganisms) from the air.
Clean air release: Filtered clean air is released from the top or bottom.
Models
Product Name | AC FFU | |||
Product Model | DC-FFU-A01 | DC-FFU-A02 | DC-FFU-A03 | DC-FFU-A04 |
Dimension(mm) | 575x575x220 | 575x1175x220 | 875x1175x275 | 1175x1175x295 |
Filter Dimension(mm) | 570x570x69 | 570x1170x69 | 870x1170x69 | 1170x1170x69 |
Air Volume | 500m³/h | 1000m³/h | 1500m³/h | 2000m³/h |
Noise | 52~62dB(A) | 52~62dB(A) | 52~62dB(A) | 52~62dB(A) |
Air Pressure | 200PA | 200PA | 260PA | 290PA |
Power | 170W | 170W | 200W | 240W |
Weight | 28Kg | 35Kg | 47Kg | 55Kg |
Material | Galvanized/powder coated/SUS 304 plate | |||
Supply Power | AC 1N 110, 220V/50,60Hz | |||
Control System | 3 stage regulation, group reguation | |||
Filter Efficiency | 99.95%MPPS above H13-U16@EN1822 | |||
Pre Filter | G3/G4 Filter, nylon filter | |||
Work Status | power Indicator, work indicator, Error indicator | |||
Connection Type | 3 Pin Aviation Male Female socket, terminat blocks | |||
Overload Protection | Overload protect of motor and controller | |||
Monitor Contact Communication Method | port of reserve and Erro |
Product Name | AC FFU | |||
Product Model | DC-FFU-A01 | DC-FFU-A02 | DC-FFU-A03 | DC-FFU-A04 |
Dimension(mm) | 575x575x220 | 575x1175x220 | 875x1175x275 | 1175x1175x295 |
Filter Dimension(mm) | 570x570x69 | 570x1170x69 | 870x1170x69 | 1170x1170x69 |
Air Volume | 500m³/h | 1000m³/h | 1500m³/h | 2000m³/h |
Noise | 52~62dB(A) | 52~62dB(A) | 52~62dB(A) | 52~62dB(A) |
Air Pressure | 200PA | 200PA | 260PA | 290PA |
Power | 170W | 170W | 200W | 240W |
Weight | 28Kg | 35Kg | 47Kg | 55Kg |
Material | Galvanized/powder coated/SUS 304 plate | |||
Supply Power | AC 1N 110, 220V/50,60Hz | |||
Control System | 3 stage regulation, group reguation | |||
Filter Efficiency | 99.95%MPPS above H13-U16@EN1822 | |||
Pre Filter | G3/G4 Filter, nylon filter | |||
Work Status | power Indicator, work indicator, Error indicator | |||
Connection Type | 3 Pin Aviation Male Female socket, terminat blocks | |||
Overload Protection | Overload protect of motor and controller | |||
Monitor Contact Communication Method | port of reserve and Erro |
Accessories
HEPA Filter
ULPA Filter
Adjustable speed fan
Fixed speed fan
Manual control panel
Digital remote control system
Monitoring sensors (pressure)
FAQ
1. Can FFUs be used in pharmaceutical cleanrooms?
Yes, Fan Filter Units (FFUs) are widely used in pharmaceutical cleanrooms to ensure a sterile and contaminant-free environment. They provide essential air filtration and circulation, helping to maintain the stringent cleanliness levels required in pharmaceutical manufacturing. FFUs effectively filter out airborne particles and microorganisms, which is critical for maintaining product integrity and compliance with industry regulations.
2. Can FFUs be used in biopharmaceutical manufacturing?
FFUs are highly effective in biopharmaceutical manufacturing environments, where maintaining strict air quality standards is crucial. These units help to prevent contamination during the production process by providing a continuous supply of filtered air. Their ability to maintain a clean atmosphere is essential for the safety and efficacy of biopharmaceutical products.
3. What is the role of a Cleanroom FFU in controlled environments?
The role of a Cleanroom Fan Filter Unit (FFU) in controlled environments is to provide a reliable source of clean, filtered air while maintaining a specified airflow rate. FFUs help to create a controlled atmosphere that meets the necessary cleanliness standards for various applications, including pharmaceuticals, electronics, and research labs.
Key functions of a Cleanroom FFU include:
Efficient filtration of contaminants
Consistent airflow distribution
Support for regulatory compliance
4. What is the airflow distribution of a Cleanroom FFU?
A Cleanroom FFU typically provides a uniform airflow distribution across its surface area, which is essential for maintaining consistent air quality and pressure within the cleanroom. The design of the FFU allows for laminar flow, minimizing turbulence and ensuring that filtered air is evenly distributed throughout the space.
5. What is the role of the fan motor in a Cleanroom FFU?
The fan motor in a Cleanroom FFU is crucial for generating the airflow necessary for effective air filtration and circulation. It powers the fan that draws ambient air through the filters, ensuring that clean air is continuously supplied to the cleanroom environment. The motor's efficiency and performance directly impact the overall effectiveness of the FFU.
6. How does a Fan Filter Unit work in a controlled environment?
A Fan Filter Unit (FFU) operates by drawing in unfiltered air, passing it through a series of filters, and then distributing the clean air into the controlled environment. The process involves the following steps:
Air is pulled into the unit by the fan motor.
The air passes through pre-filters and HEPA or ULPA filters to remove particulates.
Clean air is then blown into the cleanroom, maintaining positive pressure and cleanliness.
7. What are the key features of a Cleanroom FFU?
Cleanroom FFUs are designed with several key features that enhance their performance and usability. These include:
High-efficiency filters (HEPA or ULPA)
Variable speed fan motors for adjustable airflow
Compact and modular design for easy installation
Low noise operation for minimal disruption
These features make FFUs an essential component in maintaining cleanroom standards.
8. What types of Cleanroom FFUs are available on the market?
There are several types of Cleanroom FFUs available on the market, each designed for specific applications. Common types include:
HEPA FFUs, which use High-Efficiency Particulate Air filters
ULPA FFUs, which utilize Ultra-Low Penetration Air filters for even finer filtration
Modular FFUs, which can be easily integrated into existing cleanroom designs
These variants cater to different cleanliness requirements and operational needs.
9. What is the difference between HEPA and ULPA filters in FFUs?
The primary difference between HEPA and ULPA filters in Fan Filter Units (FFUs) lies in their filtration efficiency. HEPA filters are designed to capture at least 99.97% of particles that are 0.3 microns in size, while ULPA filters are more efficient, capturing 99.999% of particles down to 0.12 microns. This distinction makes ULPA filters suitable for environments requiring extremely high cleanliness levels.
10. How can you optimize the use of FFUs in cleanrooms?
To optimize the use of FFUs incleanrooms, several strategies can be implemented to enhance their performance and efficiency:
Regular maintenance and filter replacement to ensure optimal airflow and filtration efficiency.
Adjusting fan speeds based on real-time monitoring of cleanroom conditions.
Proper placement of FFUs to maximize airflow distribution and minimize dead zones.
Implementing these practices can significantly improve the overall effectiveness of FFUs in maintaining cleanroom standards.
11. How do you ensure the safety of Cleanroom FFUs during operation?
Ensuring the safety of Cleanroom FFUs during operation involves several important practices. Regular inspection and maintenance of the units are crucial to identify any potential issues. Additionally, operators should follow safety protocols, such as ensuring electrical components are properly grounded and using appropriate personal protective equipment (PPE) when performing maintenance tasks. Training staff on the correct operation and emergency procedures also enhances safety.
12. How do you measure the effectiveness of a Cleanroom FFU?
The effectiveness of a Cleanroom FFU can be measured using several methods, including:
Airborne particle counting to assess the concentration of contaminants in the air.
Pressure drop measurements across filters to determine clogging and airflow efficiency.
Regular audits and compliance checks against industry standards.
These assessments help ensure that the FFUs maintain the required cleanliness levels.
13. What type of filter is used in a Cleanroom FFU?
A Cleanroom FFU typically uses either HEPA (High-Efficiency Particulate Air) filters or ULPA (Ultra-Low Penetration Air) filters. HEPA filters are suitable for most cleanroom applications, capturing 99.97% of particles at 0.3 microns, while ULPA filters are used in environments requiring higher filtration efficiency, capturing 99.999% of particles down to 0.12 microns.
14. How do you install a HEPA filter into a Cleanroom FFU?
Installing a HEPA filter into a Cleanroom FFU involves a few straightforward steps:
Turn off the FFU and unplug it from the power source.
Open the filter access panel to reach the filter compartment.
Carefully remove the old filter and dispose of it according to regulations.
Insert the new HEPA filter, ensuring it fits securely and is oriented correctly.
Close the access panel and reconnect the power.
Following these steps will help maintain optimal performance of the FFU.
15. Can FFUs be used in high-containment laboratories?
Yes, FFUs can be used in high-containment laboratories where strict contamination control is necessary. These units provide efficient air filtration and help maintain a sterile environment, making them suitable for laboratories handling hazardous materials. They are essential in ensuring that the air quality meets the required safety standards for both personnel and the samples being studied.
16. How do you calculate the pressure drop across a Cleanroom FFU filter?
The pressure drop across a Cleanroom FFU filter can be calculated by measuring the airflow rate through the filter and using the following formula:
Pressure Drop (Pa) = (Airflow Rate (m³/h) x Resistance Factor (Pa/m³/h))
It is important to refer to the manufacturer's specifications for the resistance factor specific to the filter being used, as this can vary.
17. What materials are used in Cleanroom FFU filters?
Cleanroom FFU filters are typically made from high-quality materials designed to capture airborne particles effectively. Common materials include:
Fiberglass or synthetic fibers for HEPA filters
Specialized membrane materials for ULPA filters
Aluminum or plastic frames to support the filter structure
These materials ensure durability and efficiency in filtration performance.
18. What certifications should a Cleanroom FFU have?
A Cleanroom FFU should ideally have several key certifications to ensure its quality and performance standards:
ISO 14644 compliance for cleanroom classification
HEPA or ULPA filter certification according to IEST RP-CC001 or similar standards
Electrical safety certifications (e.g., CE, UL) for safe operation
Factory Production Workshop Video
Factory Photo
Product Packaging And International Logistics
Product International Certification
Find Other Common Equipment Recommendations
-
Modular CleanRoom
US$9000-10000 USD/Unit
Min. Order:1 Set -
Air Shower
US$1000.00-5000.00 USD/Unit
Min. Order:1 Set -
Downflow Booth
US$3000-6000 USD/Unit
Min. Order:1 Set -
Clean bench
US$600-2000 USD/Unit
Min. Order:1 Set -
Air Filter
US$3-50 USD/Unit
Min. Order:1 Set -
Cleanroom Wall Panels
US$10-20 USD/sq.
Min. Order:1 Set -
Pass Box
US$200-500 USD/Unit
Min. Order:1 Set -
FFU
US$135-350 USD/Unit
Min. Order:1 Set -
Fume Hood
US$700-1500 USD/Unit
Min. Order:1 Set -
Cleanroom HVAC
US$5000-20000 USD/Unit
Min. Order:1 Set -
Clean room floor
US$5-20 USD/Sq.
Min. Order:1 Set -
Clean room ceiling
US$
Min. Order:1 Set