Understanding Air Change Rates in ISO 14644-4
Exploring cleanroom air management guidelines and best practices
The Importance of Air Change Rates
Air change rates (ACH) refer to the number of times the volume of air in a room is replaced within an hour. This metric is vital in controlling contamination, regulating air pressure, and maintaining the overall cleanliness required for different CleanRoom Classifications.
A well-regulated ACH ensures the removal of airborne particulates, contributing to the operational integrity of industries like pharmaceuticals, Electronics, and biotechnology.
Guidelines for Air Change Rates
ISO 14644-4 provides guidelines for appropriate air change rates based on cleanroom classifications. The requirements vary significantly, with lower-class cleanrooms requiring fewer changes and stricter environments demanding more.
Cleanroom Class | Minimum Air Changes per Hour (ACH) |
---|---|
ISO Class 8 | 5 - 10 |
ISO Class 5 | Up to 240 |
Calculation of Air Change Rate
Calculating the ACH involves several key steps to ensure compliance with required standards and optimal operational conditions.
ACH Calculation Formula
ACH = (Airflow Rate (m³/hr)) / (Room Volume (m³))
- Room Volume: Determine the volume of the cleanroom by multiplying its length, width, and height.
- Airflow Rate: Identify the total air supply rate to the room, typically measured in cubic meters per hour or cubic feet per minute.
- Apply the ACH Formula: Use the formula above to calculate the number of air changes per hour.
- Assess Compliance: Compare the calculated ACH with ISO Standards and industry regulations.
Impact on Energy Efficiency
Higher air change rates can significantly increase energy consumption due to the need for more robust HVAC systems. This increase impacts operational costs and the cleanroom's overall energy efficiency.
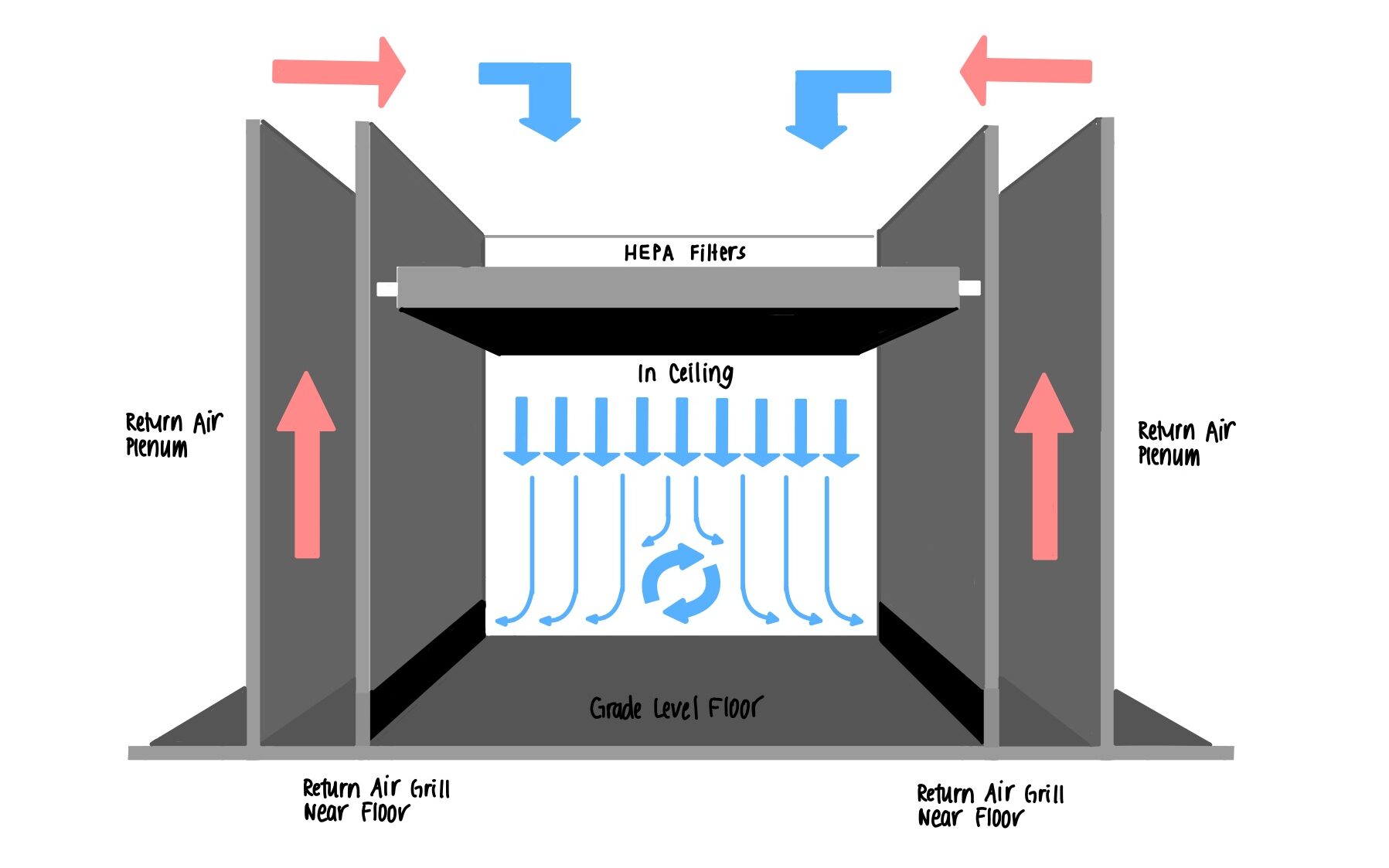
Therefore, balancing the need for adequate airflow with energy conservation measures is essential, often guided by innovative designs from industry leaders.
Determining Required Air Changes per Hour
Several factors influence the necessary air changes per hour for A CleanRoom:
- Room Volume: Larger spaces generally require more air movement to ensure contamination control.
- Occupancy Level: Increased personnel can introduce more contaminants, requiring higher ACH.
- Equipment Load: Heat and particulate emissions from equipment may dictate higher airflow.
- Cleanroom Classification: Each ISO classification has specific ACH requirements based on contaminant levels.
- Air Quality Standards: Compliance with standards protects sensitive processes and products.
- HVAC System Design: The system's capability to maintain airflow rates is critical for meeting ACH requirements.
Recommended Minimum ACH for Operating Rooms
Operating rooms typically require very high ACH to prevent infection and maintain sterile conditions:
Key Considerations
- Definition of Air Changes per Hour (ACH) as a critical metric for air cleanliness.
- Recommended minimum ACH of 20, with higher rates offering better contamination control.
- Importance of high ACH rates in environments where sterility is paramount.
- Impact of advanced HVAC design on enhancing ACH while managing energy efficiency.
Conclusion: Effective Airflow Management for Cleanrooms
Managing air change rates effectively is essential for maintaining the purity and functionality of cleanrooms. By adhering to guidelines from iso 14644-4 and leveraging industry insights, businesses can ensure their cleanroom environments are both compliant and optimally efficient.
This balance is critical to upholding operational standards while managing energy consumption and costs in sensitive industrial environments.
Key Takeaways
- ACH measures how many times air is replaced in a room per hour.
- ISO 14644-4 sets standards for ACH based on cleanroom classification.
- Higher ACH requirements exist for stricter cleanroom environments.
- Energy efficiency must be balanced with contamination control needs.
Quick ACH Calculation
Room Volume (m³):
L x W x H
Airflow Rate (m³/hr):
Measured value
ACH = Airflow / Volume
Industry Applications
- Pharmaceutical manufacturing
- Electronic component production
- Biotechnology research
- Medical device manufacturing
- Surgical operating rooms
© 2025 Cleanroom Air Management Guide
Insights from ISO 14644-4 and industry experts