Introduction to ISO Standards
The ISO 14644 standard series classifies cleanrooms and controlled environments based on airborne particle counts. These standards are essential for industries where maintaining a high level of cleanliness is critical, such as pharmaceuticals, biotechnology, and Semiconductor manufacturing. Understanding ISO classifications helps organizations minimize contamination, ensure product quality, and comply with regulatory requirements.
What is ISO Class 2 Particle Count?
ISO Class 2 refers to A CleanRoom environment where the maximum allowable particle count for particles larger than 0.5 micrometers is set at 3,520 particles per cubic meter. For particles larger than 5 micrometers, the allowable count is only 29 particles per cubic meter. This is one of the most stringent classifications for cleanroom environments, indicating a very high level of cleanliness.
Importance of Particle Count
Particle count measurement is crucial in determining the cleanliness level of a cleanroom. High levels of airborne particles can lead to contamination of sensitive products, affecting their efficacy and safety.
monitoring and controlling particle counts in ISO2 environments ensures that facilities adhere to industry standards, reduce contamination risks, and maintain product integrity.
Measurement Techniques
- Air Sampling: Collecting air samples using specialized equipment
- Real-Time Monitoring: Continuous monitoring for immediate corrective actions
- Regular Audits: Routine inspections to ensure compliance
ISO Standard Particle Limits
ISO standard limits refer to the maximum allowable concentrations of airborne particles defined within the ISO 14644 series. These limits vary according to the class of cleanroom and are crucial for maintaining the integrity of sensitive processes and products.
ISO Class | Max Particles/m³ (≥0.1 µm) | Max Particles/m³ (≥0.5 µm) | Max Particles/m³ (≥5.0 µm) |
---|---|---|---|
Class 1 | 10 | 2 | 0 |
Class 2 | 100 | 24 | 0 |
Class 3 | 1,000 | 240 | 0 |
Class 4 | 10,000 | 2,400 | 0 |
Class 5 | 100,000 | 24,000 | 29 |
Importance of Compliance
Compliance with ISO standard limits is critical for industries that require stringent cleanliness. Failure to adhere can lead to contamination, affecting product quality, safety, and efficacy. Organizations must implement rigorous monitoring and control systems to ensure consistent compliance.
Applications of ISO Class 2 Cleanrooms
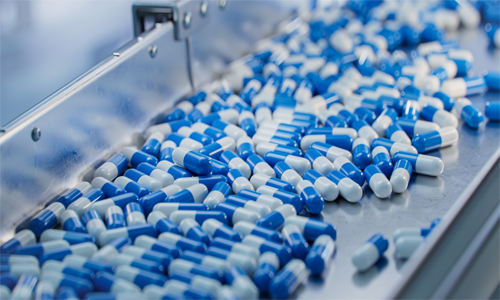
Pharmaceutical Manufacturing
Essential for producing sterile products like injectables and biologics. Prevents contamination ensuring product safety and efficacy.
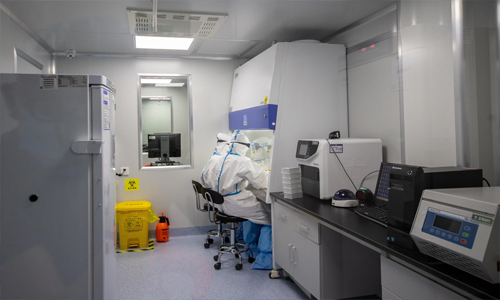
Biotechnology Research
Protects sensitive cultures and cell lines from airborne contaminants, enabling reliable research results.
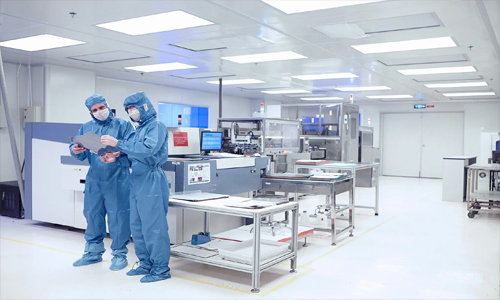
Semiconductor Fabrication
Prevents minute particles from causing defects in microchips, ensuring manufacturing integrity.
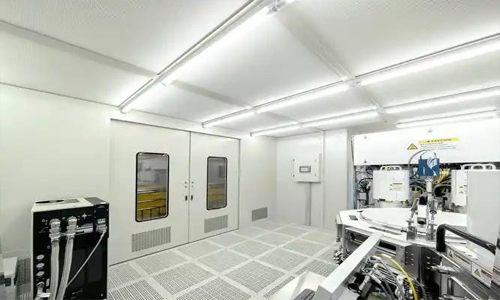
Aerospace & Defense
Used for assembling sensitive components that must operate under stringent conditions.
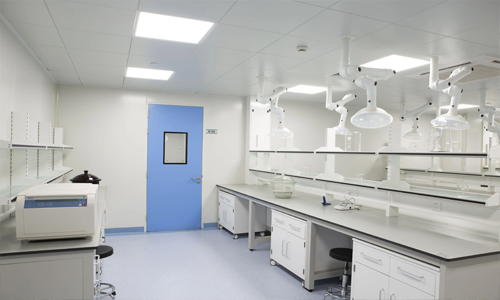
Quality Assurance
Enables testing and validation under contamination-controlled conditions for higher quality products.
ISO Class 3 Particle Count
ISO Class 3 refers to a CleanRoom Classification with specific particle count requirements:
- ≥0.5 µm: Max 35,200 particles/m³
- ≥1.0 µm: Max 8,700 particles/m³
- ≥5.0 µm: Max 293 particles/m³
Maintenance Requirements
- Frequent particle counting with laser counters
- Strict airflow management
- Rigorous cleaning protocols
- Continuous Environmental monitoring
Importance of ISO3 Standards
Product Quality
Prevents particulate contamination that can cause defects in sensitive products
Regulatory Compliance
Meets strict industry regulations and international standards
Operational Efficiency
Reduces need for rework and product recalls, saving time and resources
Maintaining Cleanroom standards
Adherence to ISO cleanroom classifications is not just about compliance - it fosters a culture of quality and safety within organizations. Companies that maintain high cleanliness standards enhance product reliability, reduce waste, and build customer trust in critical industries.
© 2023 Cleanroom Standards Guide | ISO 14644 Classification System
This information is based on ISO 14644 standards for cleanroom classifications and particle count requirements. Always refer to the latest official documentation for compliance purposes.