ISO Class 7 Clean Room
An ISO Class 7 cleanroom is a controlled environment defined by the ISO 14644-1 standard, which limits the concentration of airborne particles to ensure a clean and controlled atmosphere.
1.Particulate Limit:
The cleanroom must have no more than 352,000 particles per cubic meter (or 10,000 particles per cubic foot) for particles 0.5 microns or larger.
2.Air Changes per Hour (ACH):
ISO Class 7 cleanrooms typically require 30 to 60 air changes per hour (ACH). This helps to maintain the cleanliness of the room by continuously filtering and replacing the air to control particle contamination.
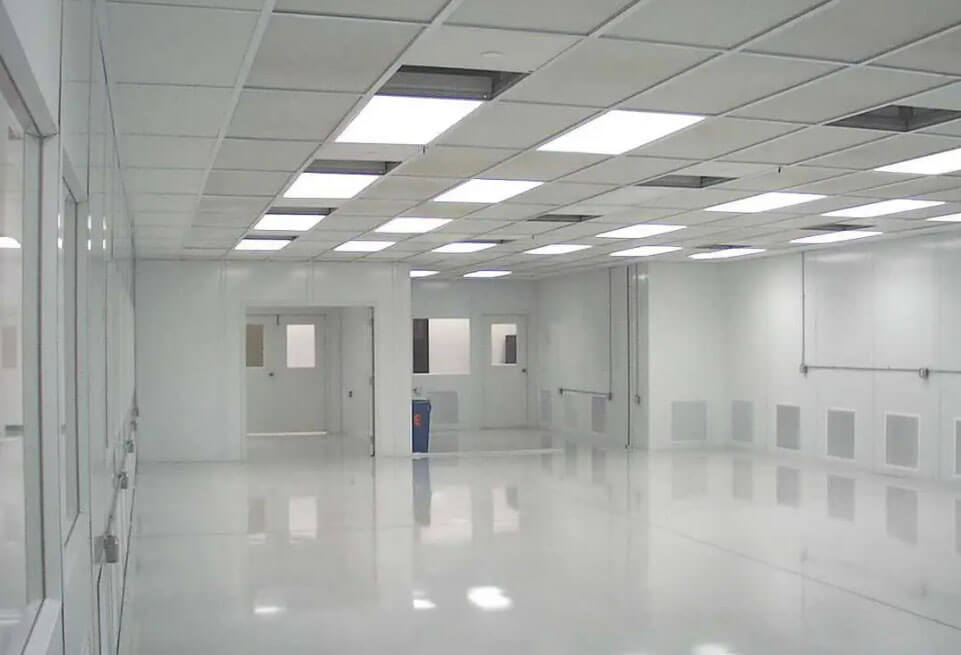
Clean room grade table
Airborne Particulate Cleanliness Classes (by cubic meter) | ||||||
CLASS | Number of Particles per Cubic Meter by Micrometer Size | |||||
0.1 micron | 0.2micron | 0.3micron | 0.5micron | 1 micron | 5 microns | |
IS01 | 10 | 2 | ||||
ISO2 | 100 | 24 | 10 | 4 | ||
IS03 | 1,000 | 237 | 102 | 35 | 8 | |
IS04 | 10,000 | 2,370 | 1,020 | 352 | 83 | |
IS05 | 100,000 | 23,700 | 10,200 | 3,520 | 832 | 29 |
IS06 | 1,000,000 | 237,000 | 102,000 | 35,200 | 8,320 | 293 |
IS07 | 352,000 | 83,200 | 2,930 | |||
IS08 | 3,520,000 | 832,000 | 29,300 | |||
IS09 | 35,200,000 | 8,320,000 | 293,000 |
ISO Class FED STD 209E Equivalent | |||||||
ISO Class | Maximum Particles/m | FED STD 209E equivalent | |||||
≥0.1μm | ≥0.2um | ≥0.3um | ≥0.5um | ≥11m | ≥5um | ||
ISO1 | 10 | 2 | |||||
ISO2 | 100 | 24 | 10 | 4 | |||
ISO3 | 1,000 | 237 | 102 | 35 | 8 | Class1 | |
ISO4 | 10,000 | 2,370 | 1,020 | 352 | 83 | 3 | Class10 |
ISO5 | 100,000 | 23,700 | 10,200 | 3,520 | 832 | 29 | Class100 |
ISO6 | 1,000,000 | 237,000 | 102,000 | 35,200 | 8,320 | 293 | Class 1,000 |
ISO7 | 352,000 | 83,200 | 2,930 | Class10,000 | |||
ISO8 | 3,520,000 | 832,000 | 29,300 | Class 100,000 | |||
ISO9 | 35,200,000 | 8,320,000 | 293,000 | Room Air |
Comparison table of ISO grade standards and ventilation times | |
ISO Class | ACH(AIRCHANGE PER HOUR) |
ISO 3 | 360-540 |
ISO 4 | 300-540 |
ISO 5 | 240-480 |
ISO 6 | 50-60 |
ISO 7 | 30-40 |
ISO 8 | 15-25 |
Comparison Table GMP/USP/ISO/FED209E | ||||||||||||
project | China GMP/Europe GMP | ISO | FED STD 209E | |||||||||
Suspended particles P/m3 | level | Static | dynamic | level | Static | level | dynamic | |||||
≥0.5um | ≥5μm | ≥0.5μm | ≥5μm | ≥0.5um | ≥5μm | ≥0.5um | ≥5μm | |||||
A | 3520 | 20 | 3520 | 20 | M3.5 | 3530 | 100 | 5 | 2220 | 20 | 100 | |
B | 3520 | 29 | 352000 | 2900 | - | - | 6 | 3520 | 29 | 1000 | ||
C | 352000 | 2900 | 3520000 | 29000 | M5.5 | 353000 | 10000 | 7 | 352000 | 2930 | 10000 | |
8. | 3520000 | 29300 | 100000 | |||||||||
D | 3520000 | 29000 | No regulations | No regulations | M6.5 | 3530000 | 100000 | 9 | 3520000 | 29300 | 100000 |
ISO Class 7 Clean Room Airflow
| |
|
ISO Class 7 Clean Room wall
| |
| |
|
ISO Class 7 Clean Room Celling
![]() | ![]() | ![]() | ![]() |
|
|
ISO Class 7 Clean Room Floor
![]() | ![]() | ![]() |
| ||
![]() | ![]() | ![]() |
|
FAQ
What is ISO class 7 cleanroom?
An ISO Class 7 cleanroom provides a highly controlled environment where particle contamination is tightly regulated. This type of cleanroom is essential in fields where even small amounts of airborne particles can affect product quality, such as in pharmaceutical production or electronics manufacturing. The cleanroom is maintained with high airflow, air filtration, and stringent environmental conditions to ensure products are made in a low-contamination atmosphere.
What is the pressure in ISO Class 7 cleanroom?
In an ISO Class 7 cleanroom, the pressure is typically maintained at positive pressure relative to the surrounding environment. This is done to prevent contamination from entering the cleanroom and to ensure that air flows out of the room when doors or entry points are opened, which helps to keep airborne particles outside.
What are the ISO guidelines for clean rooms?
The ISO guidelines for cleanrooms are primarily outlined in the ISO 14644 series, which establishes the standards for the design, operation, and maintenance of cleanrooms and controlled environments. These guidelines ensure that the cleanroom meets specific cleanliness requirements and provides a suitable environment for various sensitive industries like pharmaceuticals, electronics, biotechnology, and aerospace.
What are the temperature requirements for ISO 7 cleanroom?
For an ISO Class 7 cleanroom, the typical temperature range is between 18°C to 22°C (64°F to 72°F), with precise control to prevent issues such as static buildup, condensation, and personnel discomfort. Proper temperature and humidity control are essential for maintaining the cleanliness and ensuring the quality of products in the cleanroom.
What are the requirements for ISO Class 7 clean room?
An ISO Class 7 cleanroom is designed to maintain moderate levels of cleanliness, with a focus on controlling airborne particles, temperature, humidity, and pressure. It is typically used in industries that require stringent contamination control but do not need the ultra-clean conditions of lower-class cleanrooms (e.g., ISO Class 5 or Class 6). Proper filtration, airflow, environmental control, and personnel protocols are critical for maintaining the integrity of the cleanroom environment.
What is ISO 7 cleanroom equivalent?
The ISO 7 cleanroom is most commonly equivalent to Class 10,000 under the US Federal Standard 209E and Class D under GMP (Good Manufacturing Practice) guidelines. It is aISO similar to JIS B 9920 Class 7 in Japan. These equivalences are based on particle concentration limits, air cleanliness, and overall cleanliness standards used in various global systems. However, it's important to note that different standards may define additional operational criteria, so it's always important to consult the specific regulatory or industry guidelines for the cleanroom you're working with.
What are the ISO 7 and 8 gowning requirements?
Gowning in both ISO Class 7 and ISO Class 8 cleanrooms is essential for controlling contamination from personnel. While the requirements for ISO Class 7 are generally more stringent due to the need for a higher level of cleanliness, the fundamental gowning protocols—full-body coverage, gloves, face mask, and shoe covers—are required in both environments. The materials used for gowning may differ slightly, but the goal of preventing contamination from personnel remains the same.
How many air changes per hour in a clean room?
A cleanroom typically requires **30 to 60 air changes per hour (ACH)**, depending on the class and specific requirements.
What is the minimum air changes per hour for ISO 7?
The minimum air changes per hour (ACH) for an ISO 7 cleanroom typically ranges from 20 to 30 ACH. This ensures proper ventilation and particle dilution, helping to maintain the cleanliness level required for ISO Class 7, which allows up to 352,000 particles per cubic meter (≥ 0.5 microns). Higher air change rates may be used to improve air quality further, but the 20-30 ACH range is considered the minimum to maintain the desired particulate control and airflow efficiency.
Related Information
-
共1页 8条