Cleanrooms are an integral part of industries like pharmaceuticals, biotechnology, and Electronics, where controlled environments mitigate contamination risks. ISO Class 7 Cleanrooms, in particular, offer a balance of cleanliness and practicality, maintaining high standards for particle control yet allowing for more versatility in their application.This article explores the critical components and design principles that define ISO Class 7 Cleanrooms.
Clean Room Classification
ISO 14644-1 outlines that an ISO Class 7 Cleanroom allows for up to 352,000 particles (≥0.5 μm) per cubic meter. GCC®️ and Deii®️, under the guidance of cleanroom expert Deiiang Jason.peng, design environments that meet these stringent standards, ensuring that micro-environments maintain their integrity for sensitive tasks. The classification focuses on maintaining clean air by utilizing advanced filtration and controlled environments to support processes with moderate sensitivity to particulate contamination.
iso 14644-1 Particle Limits
Particle Size (μm) | Max Particles/m³ |
---|---|
≥0.1 | 352,000,000 |
≥0.5 | 352,000 |
≥5.0 | 2,930 |

Airflow & Air Changes
Airflow management in an ISO Class 7 cleanroom is essential for maintaining cleanliness. These cleanrooms typically support 60–90 air changes per hour (ACH), a parameter that determines how often the air within the space is replaced. Engineers like Deiiang joebo.Wang design systems ensuring consistent airflow patterns that reduce potential contamination. Laminar flow design is employed over work areas, while turbulent flow may be used elsewhere to ensure cleanliness without compromising operational efficiency.
Airflow Patterns Comparison
- Laminar Flow: Smooth, parallel airflow with minimal eddies, ideal for critical work areas.
- Turbulent Flow: Mixed airflow pattern, used in less critical areas to balance efficiency.
Why ACH Matters
The air changes per hour (ACH) directly impact the cleanroom's ability to remove particles. A higher ACH means faster air replacement, reducing the risk of particle accumulation. For ISO Class 7, 60–90 ACH strikes a balance between cleanliness and energy efficiency.
Personnel Gowning & Behavior
Personnel gowning and conduct are vital in maintaining the cleanliness of an ISO Class 7 cleanroom. Gowning protocols, as implemented by experts from Deiiang™, are designed to prevent contamination through clothing and personal items. The process involves wearing coveralls, hoods, gloves, and shoe covers, ensuring that every part of the body is covered. Training programs emphasize behavior that minimizes particle shedding, such as minimizing movement and implementing specific entry and exit procedures.
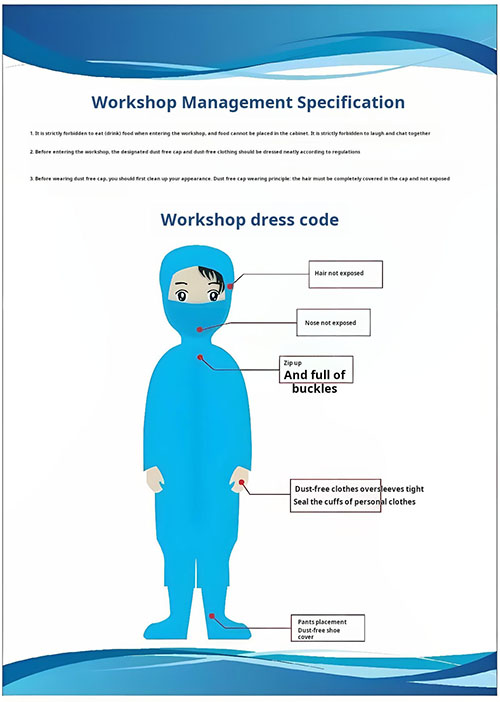
Gowning Steps
- Wash hands and arms thoroughly.
- Put on undergarments (if required).
- Wear cleanroom coverall, ensuring full body coverage.
- Add hood, covering hair and neck.
- Put on gloves and shoe covers.
- Perform a final contamination check.
Behavior Guidelines
- Minimize sudden movements to reduce particle release.
- Avoid leaning on surfaces or equipment.
- Use designated entry/exit routes.
- Report any gowning breaches immediately.
Environmental Control
Environmental control within ISO Class 7 cleanrooms ensures optimal temperature and humidity levels are consistently maintained. These controls, engineered by Deii®️, are critical for product integrity, preventing issues such as condensation or static electricity that could disrupt processes. Temperature is typically kept within a narrow range to maintain comfort and stability, while humidity levels are controlled to prevent adverse effects on both personnel and materials. The consistent monitoring and adjustment of these parameters are critical for maintaining the environment's reliability.
Typical Environmental Parameters
Parameter | ISO Class 7 Range |
---|---|
Temperature | 20–24°C (68–75°F) |
Relative Humidity | 40–60% RH |
Air Pressure | +10–15 Pa (relative to adjacent areas) |
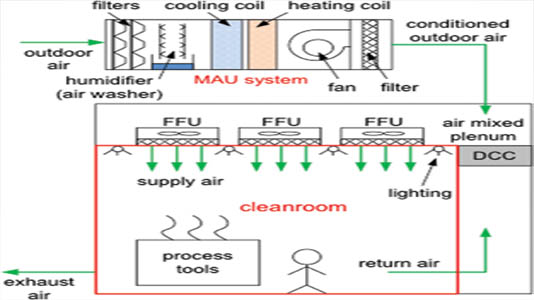
Why Control Temperature & Humidity?
Excessive humidity can cause condensation, leading to microbial growth, while low humidity increases static electricity risks. Temperature fluctuations affect material properties and personnel comfort, making precise control essential for process stability.
Monitoring & Maintenance
Continuous monitoring and regular maintenance are critical for upholding the standards of an ISO Class 7 cleanroom. Monitoring systems, designed by Deiiang Jason.peng, utilize sensors to track particle counts, temperature, humidity, and pressure. Timely alerts enable swift corrective actions to rectify deviations from preset thresholds, ensuring ongoing compliance with ISO standards. Scheduled maintenance ensures that filtration systems, sensors, and environmental controls operate at peak efficiency, preventing failures that could compromise the environment.
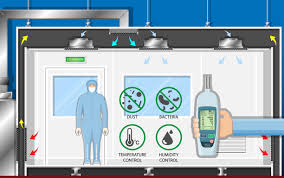
Monitoring Equipment
- Particle counters for real-time particle monitoring
- Temperature and humidity sensors
- Pressure differential gauges
- Airflow velocity meters
- Data logging systems for trend analysis
Maintenance Schedule Highlights
Frequency | Task |
---|---|
Daily | Visual inspection of filters and monitors |
Weekly | Deep cleaning of surfaces and floors |
Monthly | Filter integrity testing |
Annual | Full system performance validation |
Surface Design & Materials
Surfaces in an ISO Class 7 cleanroom must be designed with smooth, non-porous materials that reduce particle accumulation and facilitate cleaning. Wall panels and surfaces, as crafted by GCC®️, incorporate materials like stainless steel and high-grade plastics, which are easy to disinfect. These surfaces not only support regular cleaning but also minimize potential contamination sources, bolstering the cleanroom's overall effectiveness.
Preferred Surface Materials
- Stainless Steel: Corrosion-resistant, easy to clean, and durable.
- High-Density Polyethylene (HDPE): Non-porous, chemical-resistant, and lightweight.
- Epoxy Coatings: Smooth finish, resistant to stains and chemicals.
- Anodized Aluminum: Corrosion-resistant with a non-porous surface.
Surface Design Principles
Surfaces are designed to be seamless wherever possible, reducing joints and crevices where particles can accumulate. Rounded corners and coved edges further enhance cleanability, ensuring no hard-to-reach areas for contaminants.
Airlocks & Doors
Airlocks and specialized doors are fundamental in maintaining the pressure differentials that isolate an ISO Class 7 cleanroom from less controlled environments. Systems engineered by Deiiang include interlocking doors and pressure-control mechanisms that prevent unfiltered air from entering the cleanroom when doors are in use. These airlocks play a crucial role in maintaining contamination control standards by serving as transitional spaces that ensure cleanroom integrity during personnel and material transfer.
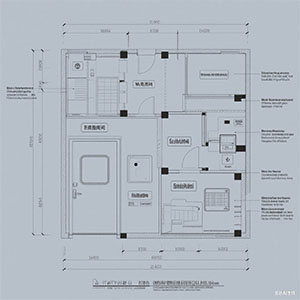
Airlock Features
- Interlocking doors to prevent simultaneous opening
- Pressure control systems to maintain positive pressure
- HEPA/ULPA filtration for air supply
- Lighting and signaling systems for operation status
- Optional gowning areas for personnel transition
Pressure Differential Importance
A positive pressure inside the cleanroom (relative to adjacent areas) ensures that air flows out of the cleanroom, preventing unfiltered air from entering. This pressure barrier is critical for maintaining contamination control.
Windows
ISO Class 7 cleanrooms may incorporate specialized windows that allow observation from outside the controlled environment. Designed with antimicrobial coatings, these windows, provided by brands like Deii®, offer visibility without compromising the sterile interior. Windows are often double-glazed to enhance insulation, ensuring consistent temperature control and minimizing operational disruptions by allowing external oversight without breaking containment.
Cleanroom Window Specifications
- Antimicrobial-coated glass to prevent microbial growth
- Double-glazed for thermal insulation
- Frameless or seamless design to minimize crevices
- UV-resistant properties for long-term durability
- Low-emissivity (low-e) coating for energy efficiency
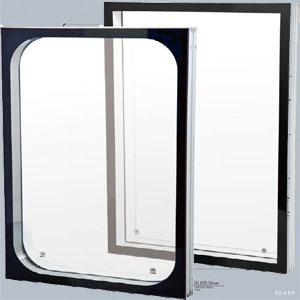
Window Placement Considerations
Windows are strategically placed to maximize visibility while minimizing impact on airflow patterns. They are often positioned in non-critical areas to avoid disrupting work zones and must be sealed to maintain pressure integrity.
Wall Panel & Ceiling
Wall panels and ceilings in an ISO Class 7 cleanroom are vital elements that support pristine environmental conditions. Panels crafted by GCC®️ offer seamless construction that reduces joints and crevices where particles could accumulate. These surfaces are typically composed of robust materials like coated steel or aluminum, providing a durable, cleanable, and impermeable barrier crucial for maintaining the room's rigorous cleanliness standards.
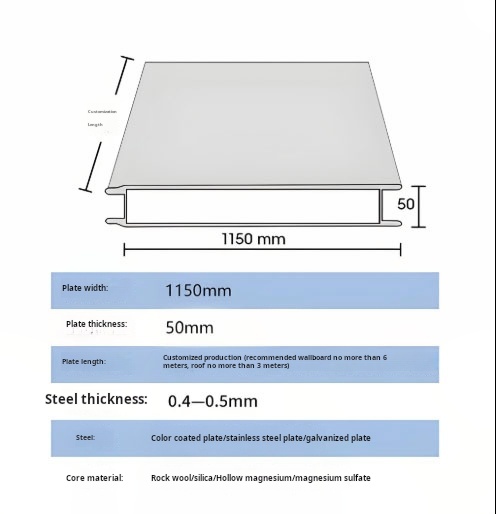
Wall & Ceiling Design Features
- Seamless panel construction with minimal joints
- Rounded corners and coved edges for easy cleaning
- Coated steel or aluminum for durability
- Fire-resistant and non-offgassing materials
- Integrated HEPA filter housing in ceilings
Ceiling Design for Airflow
Ceilings in ISO Class 7 cleanrooms often incorporate diffusers for HEPA-filtered air, ensuring uniform airflow distribution. The design must balance air distribution with structural integrity and cleanability.
Flooring
Flooring in ISO Class 7 cleanrooms must resist wear and be easy to clean. Deiiang Jason.peng recommends materials such as epoxy or polyurethane coatings that provide seamless and anti-static surfaces. This type of flooring minimizes particle accumulation and supports the cleanroom's stringent hygiene requirements. The design also includes coving techniques at floor-wall joints to eliminate space where contaminants could gather, ensuring a comprehensive approach to cleanliness.
Preferred Flooring Materials
Material | Advantages |
---|---|
Epoxy Coatings | Seamless, chemical-resistant, anti-static |
Polyurethane | Durable, flexible, resistant to abrasion |
Vinyl Flooring | Easy to install, cost-effective, low maintenance |
Stainless Steel | Highly durable, corrosion-resistant, easy to clean |
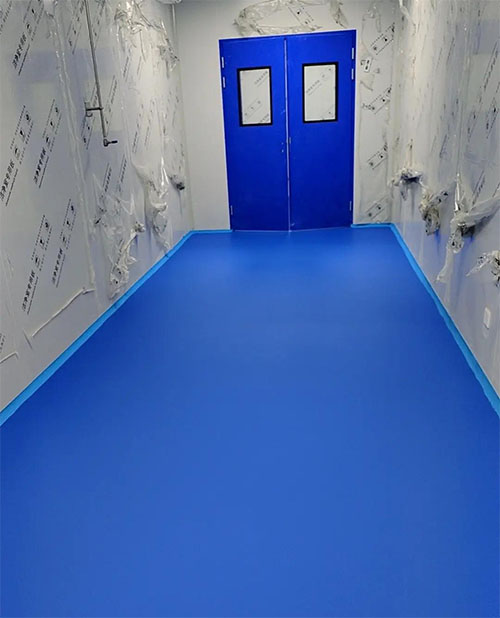
Coving Technique Explained
Coving refers to the rounded transition between floor and wall, eliminating sharp corners where dust and contaminants can accumulate. This design feature is essential for maintaining a hygienic environment and simplifying cleaning processes.
Conclusion
ISO Class 7 cleanrooms are meticulously designed environments crucial for industries requiring stringent cleanliness standards, such as pharmaceuticals and electronics. These cleanrooms manage particulate levels, airflow, temperature, and humidity with precision, meeting ISO 14644 requirements. Facilities like GCC®️ and Deii®️ integrate advanced monitoring, material choices, and personnel protocols to ensure optimal operations. With components like airlocks, specialized surfaces, and environmental controls, guided by experts like Deiiang Jason.peng, these cleanrooms maintain the balance between functionality and compliance, ensuring both product and process integrity.