ISO 8 Cleanroom
ISO 8 cleanrooms are classified based on specific criteria established by the International Organization for Standardization (ISO).
0.5 micron: 3,520 particles/m³
1.0 micron: 832 particles/m³
5.0 micron: 29 particles/m³
Air Cleanliness:ISO Class 8
Temperature: 18°C to 24°C
Relative Humidity: 30% to 60%
Air Change Rate:15 to 20 air changes per hour
Pressure Differential:10-15 Pa
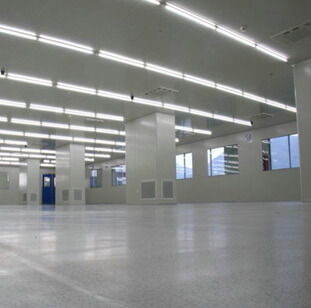
Cleanrooms Grade Table
ISO Class FED STD 209E Equivalent | |||||||
ISO Class | Maximum Particles/m | FED STD 209E equivalent | |||||
≥0.1μm | ≥0.2um | ≥0.3um | ≥0.5um | ≥11m | ≥5um | ||
ISO1 | 10 | 2 | |||||
ISO2 | 100 | 24 | 10 | 4 | |||
ISO3 | 1,000 | 237 | 102 | 35 | 8 | Class1 | |
ISO4 | 10,000 | 2,370 | 1,020 | 352 | 83 | 3 | Class10 |
ISO5 | 100,000 | 23,700 | 10,200 | 3,520 | 832 | 29 | Class100 |
ISO6 | 1,000,000 | 237,000 | 102,000 | 35,200 | 8,320 | 293 | Class 1,000 |
ISO7 | 352,000 | 83,200 | 2,930 | Class10,000 | |||
ISO8 | 3,520,000 | 832,000 | 29,300 | Class 100,000 | |||
ISO9 | 35,200,000 | 8,320,000 | 293,000 | Room Air |
Comparison Table GMP/USP/ISO/FED209E | ||||||||||||
project | China GMP/Europe GMP | ISO | FED STD 209E | |||||||||
Suspended particles P/m3 | level | Static | dynamic | level | Static | level | dynamic | |||||
≥0.5um | ≥5μm | ≥0.5μm | ≥5μm | ≥0.5um | ≥5μm | ≥0.5um | ≥5μm | |||||
A | 3520 | 20 | 3520 | 20 | M3.5 | 3530 | 100 | 5 | 2220 | 20 | 100 | |
B | 3520 | 29 | 352000 | 2900 | - | - | 6 | 3520 | 29 | 1000 | ||
C | 352000 | 2900 | 3520000 | 29000 | M5.5 | 353000 | 10000 | 7 | 352000 | 2930 | 10000 | |
8. | 3520000 | 29300 | 100000 | |||||||||
D | 3520000 | 29000 | No regulations | No regulations | M6.5 | 3530000 | 100000 | 9 | 3520000 | 29300 | 100000 |
Comparison table of ISO grade standards and ventilation times | |
ISO Class | ACH(AIRCHANGE PER HOUR) |
ISO 3 | 360-540 |
ISO 4 | 300-540 |
ISO 5 | 240-480 |
ISO 6 | 50-60 |
ISO 7 | 30-40 |
ISO 8 | 15-25 |
ISO Class 8 Clean Room Airflow
Air Changes per Hour (ACH): ISO Class 8 cleanrooms typically require 20 to 25 air changes per hour. | Air Velocity: Unlike higher-class cleanrooms (e.g., ISO Class 5 or 6), ISO Class 8 cleanrooms do not usually require unidirectional (laminar) airflow. | Temperature and Humidity Control: Typical ranges are 20-24°C for temperature and 30-60% for relative humidity, but these may vary based on specific requirements. |
Clean Room wall
Cleanroom Panel | MGO Rock Wool Panel | Handmade rock wool panel |
◇ Size and appearance: Ensure that the size and shape of the product meet the design requirements and have no obvious defects. ◇ Physical properties: Such as compression, tension, impact resistance and other tests to ensure the strength and durability of the material. ◇ Surface treatment: Confirm that the surface is smooth, the coating is uniform, and there are no bubbles, peeling, etc. ◇ Test report: Fire and corrosion resistance test |
Clean Room Doors And Windows
Steel standard: Select high-quality steel that meets national and international standards to ensure its corrosion resistance and strength. Surface treatment: The surface of the door body should be treated with anti-rust treatment (such as spraying, anodizing, etc.) to ensure durability and easy cleaning. Insulation material: The door core material should have good heat insulation and sound insulation properties, and insulating materials such as polyurethane or rock wool are usually used. Production process: Production is carried out strictly in accordance with standardized processes, including cutting, forming, welding and painting | Steel standard: Select high-quality steel that meets national and international standards to ensure its corrosion resistance and strength. Surface treatment: The surface of the door body should be treated with anti-rust treatment (such as spraying, anodizing, etc.) to ensure durability and easy cleaning. Insulation material: The door core material should have good heat insulation and sound insulation properties, usually using insulating materials such as polyurethane or rock wool. Production process: Strictly follow the standardized process for production, including cutting, forming, welding and painting, to ensure stable quality in each link. |
ISO Class 8 Clean Room Celling
Specifications: Thickness: 980, 1180 Panel material: 50mm, 75mm, 100mm Core material: color-coated steel plate, stainless steel plate, rock wool, gypsum, glass magnesium, aluminum honeycomb, etc. Accessories: Keel: 0.8 galvanized plate Application scope: food, medicine Others: Coating: PE (polyester), PVDF (fluorocarbon), HDP (high weather-resistant polyester) | Keel:0.8 thick galvanized steel keels are used on all four sides to increase the strength and sealing of the board Beam:The patented heavy-duty hanging beam system of MasterCard is adopted, which is convenient for installation and improves construction efficiency. Cost:No need to remove the entire top plate, reducing replacement costs and high cost performance. Replacement:This product is also suitable for partial top plate replacement |
ISO Class 8 Clean Room Floor
| ||
|
FAQ
What is an ISO class 8 cleanroom?
An ISO Class 8 cleanroom is a type of controlled environment defined by the ISO 14644-1 standard, with specific limits on the concentration of airborne particles. In this class, the cleanroom must maintain a maximum of 3.5 million particles per cubic meter (or 100,000 particles per cubic foot) for particles 0.5 microns or larger.
1. Particle Count:
The cleanroom must limit airborne particles to no more than 3.5 million particles per cubic meter for particles that are 0.5 microns or larger.
2. Air Changes Per Hour (ACH):
An ISO Class 8 cleanroom typically requires around 20 to 40 air changes per hour (ACH), which helps maintain cleanliness by continuously filtering and replacing the air in the room.
3. Applications:
Manufacturing of non-sterile pharmaceuticals
Medical device production:
Electronics assembly
Cosmetics production
Food packaging
What is the difference between Class 8 and Class 7 clean rooms?
Class 8 and Class 7 clean rooms refer to different levels of cleanliness and air quality as defined by the ISO 14644-1 standard. The primary differences between them are based on the allowable concentration of particles in the air, which impacts the level of cleanliness in the environment.
Particulate Count:
Class 8 clean rooms allow up to 3,520,000 particles per cubic meter of air at 0.5 microns or larger.
Class 7 clean rooms allow only 352,000 particles per cubic meter of air at the same size.
Air Quality Standards:
Class 8 clean rooms have a higher particle concentration limit and are typically used in environments that require lower levels of cleanliness, such as manufacturing of non-sensitive electronic components or certain industrial processes.
Class 7 clean rooms have stricter air quality standards and are used in more sensitive applications, such as pharmaceutical manufacturing, semiconductor production, or biotechnology labs where even small contaminants could cause significant issues.
Applications and Costs:
Class 8 clean rooms are more cost-effective because they allow for a higher level of contamination, making them suitable for less stringent applications.
Class 7 clean rooms are more expensive to maintain due to the stricter filtration and airflow requirements, but they are essential for industries where a higher level of cleanliness is critical for product quality and safety.
In summary, the main differences between Class 8 and Class 7 clean rooms lie in the particulate limits, cleanliness standards, applications, and associated costs. Class 7 provides a higher level of contamination control than Class 8.
What is BS EN ISO 14644 Class 8?
BS EN ISO 14644 Class 8 refers to a cleanroom classification defined by the BS EN ISO 14644-1 standard, which specifies the allowable concentration of airborne particles in a controlled environment, based on particle size. This standard is recognized internationally and is the European and international equivalent of ISO 14644.
What is an ISO 9 clean room?
An ISO Class 9 cleanroom is the least stringent cleanroom classification, suitable for environments where moderate particle control is needed but extreme cleanliness is not critical. These cleanrooms are typically used for less sensitive industrial applications where contamination is not a primary concern, such as general manufacturing or packaging that does not require a sterile environment.
How many air changes per hour for ISO Class 8?
In essence, the higher the ACH, the more frequently the air is replaced, which helps to dilute and remove airborne particles, maintaining the cleanroom's required particle limits. For ISO Class 8, the room needs to be ventilated well enough to keep the airborne particle count within the allowable limits of 3.5 million particles per cubic meter (≥ 0.5 microns).
What is the particulate limit for ISO 8?
Particle size: ≥ 0.5 microns;Maximum particles per cubic meter: 3.5 million;Maximum particles per cubic foot: 100,000
What is ISO Class 8 cleanroom standards?
Particle Count: Class 8 cleanrooms can have up to 3,520,000 particles per cubic meter of air.
Air Quality: Cleanrooms must meet strict filtration and airflow requirements to maintain air quality, ensuring minimal contamination in various applications.
Usage: ISO Class 8 cleanrooms are commonly used in industries where lower levels of cleanliness are sufficient, such as certain electronics manufacturing, automotive assembly, or food processing. However, they still provide a controlled environment to minimize particulate contamination in processes.
ISO Class 8 cleanroom standards define the allowable limits for airborne particles in a controlled environment. The cleanroom must maintain a maximum concentration of 3,520,000 particles per cubic meter at 0.5 microns or larger.
What is lSO Class 8 equivalent cleanroom?
An ISO Class 8 cleanroom is equivalent to a Class 100,000 cleanroom in the US Federal Standard 209E (which was used prior to the adoption of ISO standards). Both classifications define environments with similar levels of contamination control, allowing up to 3.5 million particles per cubic meter (or 100,000 particles per cubic foot) for particles 0.5 microns or larger.
What is the humidity requirement for ISO Class 8 cleanroom?
The humidity requirement for an ISO Class 8 cleanroom is not strictly defined by the ISO 14644-1 standard, but typically, the relative humidity is maintained between 30% and 60%. This range helps prevent static electricity buildup, control dust, and ensure a comfortable working environment, while also preventing material degradation or contamination in sensitive processes. Specific humidity levels may vary depending on the industry and the products being manufactured.