ISO 14644-4:2022(EN)
ISO 14644-4 is a part of the ISO 14644 series that provides guidelines for the design, installation, and operation of air handling systems in cleanrooms and controlled environments. Specifically, it focuses on the ventilation and airflow management necessary to maintain cleanroom performance and cleanliness levels as defined in ISO 14644-1.
This standard addresses the required air change rates, airflow patterns, and the placement and design of HVAC (Heating, Ventilation, and Air Conditioning) systems to ensure that airborne contamination is effectively removed from the cleanroom environment. It emphasizes the importance of proper air distribution to minimize particle buildup and contamination risks.
ISO 14644-4 also offers guidance on how to monitor and maintain airflow systems, ensuring they continue to function as required for the cleanroom's intended use.
The standard helps ensure that cleanrooms, whether in pharmaceutical, semiconductor, or biotechnology industries, maintain strict air cleanliness levels and are equipped with efficient and well-designed air handling systems.
Full version:ISO-14644-4-2022.pdf
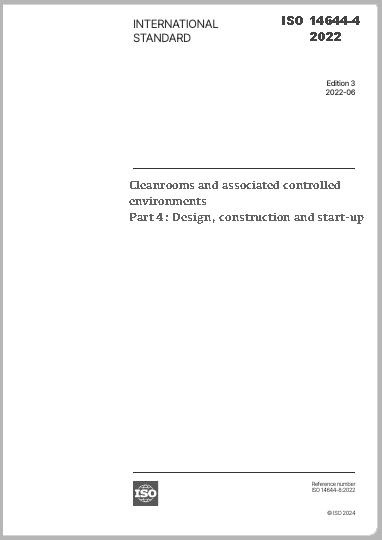
Foreword
The procedures used to develop this document and those intended for its further maintenance are described in the ISO/IEC Directives, Part 1. In particular, the different approval criteria needed for the different types of ISO documents should be noted. This document was drafted in accordance with the editorial rules of the ISO/IEC Directives, Part 2 (see www.iso.org/directives).
Attention is drawn to the possibility that some of the elements of this document may be the subject of patent rights. ISO shall not be held responsible for identifying any or all such patent rights. Details of any patent rights identified during the development of the document will be in the Introduction and/or on the ISO list of patent declarations received (see www.iso.org/patents).
Any trade name used in this document is information given for the convenience of users and does not constitute an endorsement.
For an explanation of the voluntary nature of standards, the meaning of ISO specific terms and expressions related to
The following items shall be considered and defined as appropriate:
conformity assessment, as well as information about ISO's adherence to the World Trade Organization (WTO) principles in the Technical Barriers to Trade (TBT), see www.iso.org/iso/foreword.html.
This document was prepared by Technical Committee ISO/TC 209, Cleanrooms and associated controlled environments, in collaboration with the European Committee for Standardization (CEN) Technical Committee CEN/TC 243, Cleanroom technology, in accordance with the Agreement on technical cooperation between ISO and CEN (Vienna Agreement).
This second edition cancels and replaces the first edition (ISO 14644-4:2001), which has been technically revised.
The main changes are as follows:
normative content has been extended;
the process of gathering and defining requirements has been added;
the scope has been extended from classified cleanrooms to include additional cleanliness attributes;
the entire text has been revised or clarified to aid its application.
A list of all parts in the ISO 14644 series can be found on the ISO website.
Any feedback or questions on this document should be directed to the user’s national standards body. A complete listing of these bodies can be found at www.iso.org/members.html.
Introduction
Cleanrooms and associated controlled environments provide for the control of airborne particulate contamination and, if relevant, other forms of contamination, to levels appropriate for accomplishing contamination-sensitive activities. Products and processes that benefit from the control of airborne contamination include those in such industries as aerospace, microelectronics, pharmaceuticals, medical devices, food and research and development laboratories and some applications in healthcare.
Cleanrooms and associated controlled environments are classified for air cleanliness by particle concentration (ISO 14644-1). Cleanliness attributes relating to chemicals, nanoscale particles and viable particles (microorganisms), as well as cleanliness of surfaces, can also be considered.
This document is one of the series of International Standards concerned with cleanrooms and associated controlled environments prepared by ISO/TC 209.
This document provides guidance for the design, construction and start-up of cleanrooms, both new and those undergoing modification or refurbishment. In this edition, a more structured approach is provided with separate normative sections on requirements, design, construction and start-up, supported by four corresponding informative annexes.
For this edition, key recommendations and considerations include:
A structured approach with a logical sequential flow through the design, construction and start-up stages. There will normally be reviews and iterations of the requirements, contamination control concepts, layouts and other considerations. The final design should be reviewed against the requirements before construction commences and when construction is complete. The operation and performance are verified against the requirements during start-up.
Inclusion of other cleanliness attributes. The ISO 14644 series has parts that deal with other cleanliness attributes, namely chemicals, nanoscale particles, macro-particles and, in ISO 14698, viable particles (microorganisms), as well as cleanliness of surfaces. These other attributes should be considered if relevant, bearing in mind that the primary requirement for a cleanroom or clean zone is that it meets a classification by airborne particle concentration according to ISO 14644-1.
Importance of a contamination risk assessment. Assessments should be carried out to better understand the contamination risk and its impact on the process and product and to identify the critical control points (locations) in the cleanroom or clean zone.
A clear statement of requirements, namely everything needed for input into the design, including the purpose of the cleanroom and the acceptance criteria for performance parameters. This is critical and should be documented prior to the start of the design process.
Ventilation effectiveness. This revision focuses on the importance of ventilation effectiveness through control of air-flow patterns and clean-up recovery rates. Two measures are identified: air change effectiveness (ACE) and contaminant removal effectiveness (CRE).
Using air supply rate for calculations of contaminant dilution and removal. This will make it possible to achieve energy-efficient cleanrooms while achieving the required level of air cleanliness.
Energy efficiency and life cycle considerations. Energy efficiency in cleanrooms is very important and is covered by ISO 14644-16.
A clean build protocol. This is included to minimize contamination during construction of the cleanroom.
Information directly relevant to cleanrooms and associated controlled environments is included in the informative annexes. Supporting information is given in the Bibliography.
6.Requirements
6.1.Cleanroom requirements
Cleanroom features and contamination control requirements are established as necessary to reliablyand repeatably create environments of desired guality to protect patients, products, processespersonnel or the environment, An assessment can be carried out in order to identify potential risks ofthe facility to be designed.
the intendeduse ofthe installation andthe operations to be carried out therein;
regulatory requirements,
the relevant parts ofIS0 14644 that will be used, including number, edition and year of publication;accordance with IS0 14644-1;the air cleanliness class at the designated particle size(s) and the defined occupancy states in accordance withIS0 14644-1:
any other requirements with respect to particles or other contaminants in air or on surfaces le.g
particle number concentration and particle deposition rate)(see Clause A.4);
considerations ofany other performance requirements such as ESD or vibration;
temperature, humidity, processes and operator comfort considerations;
performance parameters and their acceptance criteria, with any specific requirements for alertand action limits and their management;
entry and exit of personnel, equipment and materials, in terms ofquantity, movement and controlsapplied, such as decontamination and gowning;
sources ofcontamination and their source strength data;
methods oftesting, measurement and monitoring to meet the acceptance criteria;
cleanroom environmental control by stand-alone systems or integrated into building managementsystem(BMS);
requirements for monitoring of environmental conditions and other parameters,
NOTEGuidance for monitoring to provide evidence of cleanroom performance related to air cleanlinessby particle concentration can be found in IS0 14644-2.
intended life cycle ofthe installation;
intended operational cycles and turn-down periods;
changes ofthe installation anticipated over time to be provided for in the design;
the intended location ofthe installation and any site constraints;
the identification ofexternal environmental influences;
critical dimensions and weight restrictions, including those related to available space;
process and product requirements that affect the installation, including cleaning and disinfection;
the process equipment list with utility requirements;
the preferred contamination control concepts and overall strategy for contamination control;environmental and energy efficiency targets;
process hazards;
internal cleanroom surface and finish requirements (including the need for smooth, imperviousfinishes which are cleanable and resistant to cleaning and decontamination agents and free of gapsor pathways to uncontrolled areas);
required availability in terms of acceptable downtime and back-up strategy in the event of failure;
a.strategy of maintenance operations, space and time needed to maintain the installations duringthe process cycle;
b.any other factors or constraints, not listed above, imposed by the operating requirements over thelife cycle ofthe cleanroom;
c.specific industry guidance.
Additional information on mechanisms of contamination and cleanliness attributes is given in Annex A together with a comprehensive checklist regarding requirements.
6.2.Other requirements
The following items shall be considered and defined as appropriate:
roles and responsibilities ofall involved parties during execution ofthe project;project budget;
a time schedule, including milestones for provision of necessary information and documentation;
procedure for managing changes;
verifications to be carried out at each stage ofthe project andrelated documentation;
acceptance criteria for the various project stages, ifapplicable,scope of documentation at designated project stages, its data format and approval procedures (see95);
training for cleanroom personnel and technical staff who will manage, use, clean, test and maintainthe installation;
any other approvals (e.g. management, financial, quality, process, regulatory, statutory),
competence and experience of designers, installers, constructors, commissioners and testers orverifiers, specifically in relation to cleanrooms and cleanroom technology;
required experience, roles and responsibilities for approvals.
6.3.Documentation
The requirements shall be agreed and documented to form a basis for subsequent anticipated designand allow changes to be managed in a traceable manner.
7.Design
7.1.General
The output of the requirements (Clause 6) is the input for the design. The design of the cleanroom shalltake into account an effective contamination control strategy for all aspects of its construction, testing,operation, maintenance and life cycle. There are typically three stages in the overall design process:conceptual design.
basic design and detailed design.Depending on the nature and scale of the project, these stages can be executed in one or more steps with appropriate design iterations and reviews.
The design process shall progress in an agreed manner, shall take into account all the agreedrequirements and shall be documented.
Consideration shall be given to energy eficiency (see ISO 14644-16) and use of separative devices (seeISO 14644-7).
Annex B gives additional information on contamination control concepts, calculation of air volume flowrates for non-UDAF cleanrooms, selection of materials and layout.
Occupational health and safety shall be considered throughout the design stage.
In each design phase, the cost estimate and time schedule shall be considered. For cleanrooms, the cleanbuild stages and sequencing, construction method and verification shall also be considered.
7.2.Conceptual design
During the conceptual design, the contamination control concept(s) to be used shall be considered anddetermined, Guidance about contamination control concepts can be found in llause B 2。
The following shall be considered as an output ofthe conceptual design:
design criteria, approach and potential solutions for architectural, structural, civil, mechanicalelectrical, control and automation disciplines;
conceptual layouts of the installation, including locations and sizes of process equipment and
materials;material, product, personnel and waste flow diagrams overlaid on the concept layouts with briefdescriptions;
specification of all environmental control requirements, including levels of air cleanlinessairtflow control concepts, temperature, relative humidity and room-pressure differentials or zonesegregation by airflow management;
preliminary calculations for performance parameters,
gowningspecification to control source strength.
The conceptual design shall be reviewed by the customer and supplier to verify whether it meets the established requirements (concept design verification).
Consequent to this review it will possibly be necessary to update the requirements. This is subject toagreement.
At the completion of the conceptual design stage an agreed concept design document shall be produced
7.3.Basic design
A basic design is developed based on the agreed concept design.
The following shall be considered for the basic design:
plan layout and section drawings, including locations and sizes ofprocess equipment and materials;
room list with as sociated equipment identifying heat gain, potential for contamination and anyother critical characteristics;
utility list;
schematics, such as airflow diagrams, room air balance and pressurization plan;
material, product, personnel and waste flow diagrams overlaid on the developed layouts;
supporting calculations to support the supply and extract air volume flow rates necessary toachieve required levels of air cleanliness, flow pressure cascade and recovery rate where requiredsee Annex B);
supporting calculations associated with controlling any other contaminant of interest
(microorganisms, chemicals, nanoparticles or macroparticles in the air or on surfaces of interest);
associated design calculations for the HVAC environmental control system;
prefiltration and final air filtration and cleaning strategy for contaminants of interest, forenvironment and for personnel;
functional description to provide a description of the sequence of operations for criticalperformance parameters to aid controls system and software development;
any alternative designs considered, ifapplicable, and reasons forrejection;
energy-saving methods (as perIS0 14644-16);
automatic ormanual system control to achieve the required airflowrate, airflow direction betweenrooms and pressure cascade;
material and component specifications;
finishes and construction joint details for the surfaces ofthe installation;
commissioning (setting to work and verification)approach (see 8.2);
reliability andredundancy strategy;
maintenance strategy;
building automation and control systems, sometimes known as building management systems(BMS).
Ihe basic design shall be reviewed by customer and supplier to verify whether it meets the establishedreguirements and concept design (basic design verification,. It is important to include the practicalityof both construction and maintenance in the review activity.
NOTEConsequent to review it will possibly be necessary to update the requirements. This is subject toagreement..
At the end ofthe basic design stage an agreed basic design document(s) shall be produced
7.4.Detailed design
The detailed design develops the agreed basic design. Upon completion of the detailed design stagea detailed design document(s) shall be produced in sufficient depth to enable construction andverification to be carried out.
The detailed design shall be reviewed as part of design verification to ensure it conforms to therequirements in Clause 6 as implemented in the basic design. Any changes shall be approved bystakeholders and recorded as part of change control and management.
In addition, the output of the detailed design stage shall include the quality control reguirements forthe construction verification and commissioning, including the methods to be employed, the partiesinvolved and anyrequirements for witnessing.
7.5.Change management
When changes are necessary, during design or construction, the requirements or other inputs from theprior design stages shall be referenced and may need to be refined or revised.
It is important that these changes and the implications of the changes are recorded, reviewed andagreed to by designated personnel. Responsibility for this coordination shall be defined.The impact of changes on cost, project schedule and quality shall be considered and approved.
8.Construction
8.1 General
The installation shall be constructed in accordance with the agreed detailed design and specificationsand the construction plan.
8.2 Construction plan
8.2.1General
Roles, responsibilities and activities shall be described and assigned within the construction plan alongwith a schedule, a quality plan and a clean build protocol.
All contractors' and subcontractors' activities shall be coordinated for the duration ofthe entire project.
Responsibility for this coordination shall be defined as a part of the construction plan.
8.2.2Schedule
Construction activities shall be coordinated using a schedule that documents timing, sequence and keymilestones for the project.
8.2.3Quality plan
A quality plan shall be developed in consultation with the customer and other relevant parties and shalconsider procedures for:
identifying changes that require an agreement;
identifying and documenting deviations;
assessing the impact ofthe consequences ofthese changes and deviations;
approval, by appropriate designated staff, ofchanges, deviations and corrective actions;
documenting the control ofconstruction activities and information;
responsibility;
management ofdocumentation
8.2.4 Clean build protoco
A clean build protocol shall be considered for the construction project. Application across allconstruction- and assembly-related activities both on and off the construction site shall be consideredT'he protocol shall be relative to the classification of cleanroom being installed. For example, a stricterprotocol can be applied to a cleanroom with a cleaner or more critical application
Examples ofreguirements for a clean build protocol include the following:
The construction site shall be protected from the external environment at the earliest practical opportunity.
Areas shall be provided for the set-down ofmaterials, including sufficient space for the inspectionof incoming materials.
Critical components, such as final filters, shall be protected from contamination and damage untilfixed in their final position.
Materials that are delivered to site in a clean condition, such as cleanroom panels and HVAC ductingshall be kept clean.
A cleaning programme for the installation as construction progresses shall be implemented
Demarcation of a clean boundary around cleanroom construction to prevent contamination fromadjoining areas shall be established.
onsiderations shall be given to include training and instruction for all personnel attending theconstruction site, including visitor's. This shall outline safe working procedures and assist in ensuringgood handiwork, correct conduct on site and adherence to any clean build protocol implemented on site.
8.3 Construction verification
A set of verifications shall be carried out throughout the construction to ensure that each part of theconstruction process and the final installation conforms with the approved design.
8.4 Documentation
At the conclusion of the construction process, a set of record drawings, operating instructions andconstruction verification results (see 8.3) shall be provided to the customer in a timely manner.
NOTEThese drawings and operating instructions can be prepared and compiled progressively as work iscompleted.
In order to prepare for start-up, provision ofthe following information shall be considered:
checks and inspections to be completed prior to bringing the installation and systems intooperation;
procedures to start, stop and restart the installation under normal and failure mode situations;acceptable ranges ofthe performance parameters;off-peak and turn-down procedure;
procedures to follow when alert oraction limits are reached;
information on how to operate airlocks, pass-through hatches and other areas where specialventilation schemes are used;
information on calibration, operation and maintenance of the monitoring system;
procedure for verification and testing after maintenance activities.
FAQ
Q: What are the changes to ISO 14644-4?
A: The updates to ISO 14644-4 primarily focus on refining the requirements for cleanroom air change rates, airflow distribution, and the design of HVAC systems. The changes emphasize the importance of controlling airflow patterns to prevent particle buildup and to ensure that air exchanges effectively remove contaminants from the space. Additionally, the revised standard offers clearer guidance on how to balance air quality with energy efficiency, encouraging the use of modern air handling systems that minimize energy consumption without compromising cleanliness levels. The standard also provides better definitions and calculations for air change rates in various cleanroom types.
Q: What is the current version of ISO 14644?
A: The current version of ISO 14644 includes the most recent revisions of ISO 14644-1:2015, ISO 14644-2:2015, ISO 14644-3:2019, and ISO 14644-4:2018. These updates reflect the latest industry practices in cleanroom classification, performance monitoring, testing, and operational management. ISO 14644-1 defines the classification of cleanrooms based on particle concentration, while ISO 14644-2 provides guidelines for monitoring cleanroom performance. ISO 14644-3 focuses on testing cleanrooms for particle count and other variables, and ISO 14644-4 addresses air change rates, airflow, and HVAC design for maintaining proper cleanroom conditions.
Q: What is ISO 14644-4 air change rate?
A: The air change rate specified in ISO 14644-4 refers to the number of times the total volume of air in a cleanroom is replaced within one hour. This rate is critical for maintaining the cleanliness and proper ventilation of the cleanroom. The air change rate in ISO 14644-4 is typically calculated based on the iso 8 cleanroom's size, the cleanliness classification, and the type of work being performed. For example, for an ISO Class 5 cleanroom, the air change rate may range from 300 to 600 air changes per hour (ACH) to ensure particle removal and air circulation that meet the required cleanliness standards.
Q: What is the update to ISO 14644-4?
A: The update to ISO 14644-4, which was published in 2018, includes more detailed and comprehensive guidelines on air change rates, ventilation systems, and cleanroom design. It provides updated recommendations on how to optimize airflow to reduce particle contamination while improving energy efficiency in the HVAC systems. The revision emphasizes balancing the need for high air change rates with the environmental impact, encouraging the adoption of more energy-efficient systems that still meet the stringent contamination control requirements. The updated standard also includes new methodologies for calculating air change rates based on different cleanroom classifications and operational needs.
Q: What is ISO 14644-4 air change rate?
A: The air change rate in ISO 14644-4 specifies how often the air within a cleanroom is replaced to maintain the cleanliness level required by the room's classification. It plays a vital role in ensuring that airborne particles are effectively removed, and contamination is minimized. The air change rate varies depending on the cleanroom's classification, with higher air change rates typically required for cleaner rooms. For example, in ISO 5 cleanrooms, the air change rate is usually set between 300 and 600 air changes per hour (ACH), depending on the type of work and the required cleanliness.
Related Information
-
共1页 1条