Automatic assembly line air shower-2200W*3000D*2600H
Reference Price:US$5000.00-7500.00


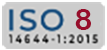
Select your requirements for air shower materials
Quantity:
Choose your Plate Thickness Requirements
Quantity:
Select your local supply voltage
Quantity:
Summary
Automatic assembly line air shower-2200W*3000D*2600H
Find Similar Products
-
Automatic assembly line air shower-2200W*3000D*2600H
US$4000.00-8000.00
Min. Order:1 unit -
Automatic assembly line air shower-2200W*2000D*2600H
US$4000.00-8000.00
Min. Order:1 unit -
Automatic assembly line air shower-2500W*5000D*2600H
US$4000.00-8000.00
Min. Order:1 unit -
Automatic assembly line air shower-2500W*4000D*2600H
US$4000.00-8000.00
Min. Order:1 unit -
Automatic assembly line air shower-2500W*3000D*2600H
US$4000.00-8000.00
Min. Order:1 unit -
Automatic assembly line air shower-2500W*2000D*2600H
US$4000.00-8000.00
Min. Order:1 unit
Air Shower Detail
The Automatic Assembly Line Air Shower is an innovative air purification system designed to uphold the highest cleanliness standards in manufacturing and cleanroom environments. This advanced unit efficiently removes contaminants from personnel and materials before they enter sensitive production areas, ensuring a sterile and safe working environment.
Key Features
High-Velocity Air Jets: Equipped with multiple high-speed air jets that deliver powerful streams of filtered air, effectively dislodging dust, particles, and contaminants from clothing and surfaces.
Multi-Stage Filtration System: Incorporates a comprehensive filtration system, including pre-filters and HEPA filters, to capture particles as small as 0.3 microns, ensuring that only clean air circulates within the air shower.
User-Friendly Controls: Features an intuitive interface with easy-to-use controls, allowing operators to adjust settings for airflow speed and shower duration based on specific operational requirements.
Touchless Operation: Designed with infrared sensors for hands-free activation, minimizing the risk of contamination from physical contact and enhancing overall hygiene.
Compact and Durable Design: Constructed from high-quality stainless steel, the air shower is built to withstand the rigors of industrial environments while maintaining a sleek and compact footprint for easy integration into existing assembly lines.
Applications
Automated assembly line air showers are ideal for product or raw material production lines in many industry sectors:
Pharmaceutical
Biotechnology
food processing
aerospace
electronics
It is especially useful in areas where maintaining a clean environment is critical to product quality and compliance with industry regulations.
Air Shower Parameter
Cargo air shower specifications size according to the user product specifications for customized production:
Model | AL-GS-1800/S1 | AL-GS-1800/S2 | AL-GS-2000/S1 | AL-GS-200/S2 |
External Size | 1800*1500*2180 | 1800*3000*2240 | 2000*1500*2180 | 2000*3000*2180 |
(W*D*H)mm | ||||
Inner Size | 1300*1430*1980 | 1300*2930*1980 | 1500*1430*1980 | 1500*2930*1980 |
(W*D*H)mm | ||||
Air Shower Time | 0-99 seconds adjustable | |||
Door System | Manual or Automatically door system | |||
Electronic Lock | LCJ Electronic Lock (one door open, another door can not be opened) | |||
Filter Efficacy | ≥99.995% of Particles ≥0.3μm | |||
Lighting | 1 Recessed LED | 2 Recessed LED | 1 Recessed LED | 2 Recessed LED |
Power Source | 380V/50Hz, 3P; 220V 50/60Hz, 1P; (Special Requirements is welcome) |
Model | AL-GS-1800/S1 | AL-GS-1800/S2 | AL-GS-2000/S1 | AL-GS-200/S2 |
External Size | 1800*1500*2180 | 1800*3000*2240 | 2000*1500*2180 | 2000*3000*2180 |
(W*D*H)mm | ||||
Inner Size | 1300*1430*1980 | 1300*2930*1980 | 1500*1430*1980 | 1500*2930*1980 |
(W*D*H)mm | ||||
Air Shower Time | 0-99 seconds adjustable | |||
Door System | Manual or Automatically door system | |||
Electronic Lock | LCJ Electronic Lock (one door open, another door can not be opened) | |||
Filter Efficacy | ≥99.995% of Particles ≥0.3μm | |||
Lighting | 1 Recessed LED | 2 Recessed LED | 1 Recessed LED | 2 Recessed LED |
Power Source | 380V/50Hz, 3P; 220V 50/60Hz, 1P; (Special Requirements is welcome) |
Air Shower Structure
The air shower room is composed of box, stainless steel door (steel plate baking paint door or color steel plate door with window), coarse filter, high efficiency filter, fan, static pressure box, nozzle interlocking controller, operation panel, sensing device and other major components.
The base plate of the air shower room is bent and welded by steel plate, with baking paint treatment and reinforcement, and the surface is made of stainless steel.
The box body is made of high-quality cold-rolled steel plate, the surface of electrostatic spraying or baking paint treatment, beautiful and generous, the bottom plate of the stainless steel plate made of friction-resistant, easy to clean.
The main material and external dimensions of the box can be customized according to customer requirements.
Air Shower Usage
Operation and Maintenance of Automatic Conveyor Belt Air Showers
Operation
Loading: Place goods on the conveyor belt.
Activation: Start the air shower system; it will automatically move goods through.
Air Shower: High-velocity air jets clean the goods.
Unloading: Collect goods at the end of the conveyor.
Maintenance
Regular Cleaning: Clean filters and air nozzles weekly.
Inspection: Check conveyor belt and mechanical parts monthly.
Filter Replacement: Replace HEPA filters every 6-12 months.
System Check: Conduct a full system diagnostic quarterly.
FAQ
1. What industries use air showers?
Air showers are used in various industries where contamination control is crucial. These industries include pharmaceuticals, biotechnology, electronics manufacturing, and food processing. Cleanrooms and research laboratories also rely heavily on air showers to maintain sterile environments.
2. How to measure air shower performance?
Measuring air shower performance involves assessing several key parameters:
Air velocity: Ensure it meets the required specifications.
Particle count reduction: Test before and after air shower use.
Filter efficiency: Check HEPA or ULPA filter performance.
Regular monitoring and testing ensure the air shower operates effectively.
3. What are the guidelines for air shower use in cleanrooms?
Guidelines for air shower use in cleanrooms include:
Pre-entry procedures: Ensure personnel remove large debris and contaminants before entering the air shower.
Proper positioning: Stand with arms and legs slightly apart to maximize surface area exposure.
Cycle duration: Adhere to the recommended decontamination cycle time, typically 30-60 seconds.
Regular maintenance: Conduct scheduled inspections and maintenance to ensure optimal performance.
4. What is an automatic assembly line air shower?
An automatic assembly line air shower is a decontamination system designed for use in industrial and cleanroom environments. It utilizes high-velocity air jets to remove particulate matter from personnel or products before they enter a controlled environment. The system is typically integrated into an assembly line to ensure continuous and efficient operation.
5. How to integrate air showers into a production line?
Integrating air showers into a production line involves several steps. First, assess the layout and workflow to determine the optimal placement. Next, ensure the air shower's dimensions and specifications match the production line's requirements. Collaborate with engineers and technicians to seamlessly integrate the air shower into the existing system, including electrical and control connections.
6. How to plan an air shower installation?
Planning an air shower installation requires a thorough site assessment to determine the best location. Consider the flow of personnel and materials, ensuring minimal disruption to existing operations. Work with professionals to design the layout, including electrical and ventilation connections. Obtain necessary permits and approvals, and schedule the installation during a period of low activity to minimize impact on production.
7. What are the maintenance intervals for air shower systems?
Maintenance intervals for air shower systems typically include:
Weekly inspections: Check for visible damage and ensure all components are functioning.
Monthly filter checks: Inspect and clean or replace filters as needed.
Quarterly diagnostics: Conduct a full system diagnostic to identify potential issues.
Annual servicing: Perform comprehensive maintenance including calibration and part replacement.
8. How long is the decontamination cycle in an air shower?
The decontamination cycle in an air shower typically lasts between 30 to 60 seconds. The exact duration can be adjusted based on specific contamination control requirements and the type of air shower being used. This ensures thorough removal of particulate contaminants from personnel or products entering a clean area.
9. How to ensure air shower system compatibility?
To ensure air shower system compatibility, start by reviewing the specifications of your existing equipment and the air shower unit. Verify that the electrical, mechanical, and dimensional requirements match. Consult with the manufacturer or a professional installer to address any potential integration issues and ensure seamless operation.
10. What is the average cost of an automatic assembly line air shower?
The average cost of an automatic assembly line air shower ranges from $10,000 to $30,000. The price can vary depending on factors such as size, features, and customization options. It's important to obtain quotes from multiple suppliers and consider the total cost of ownership, including installation and maintenance.
11. How to ensure proper sealing in air shower doors?
Ensuring proper sealing in air shower doors involves regular inspection and maintenance. Check the door gaskets and hinges for wear and tear, and replace them as needed. Ensure the door aligns correctly when closed and adjust the hinges or latches if necessary. Regular maintenance helps maintain an airtight seal, preventing contaminants from entering clean areas.
12. What are the safety features of an automatic assembly line air shower?
Safety features of an automatic assembly line air shower typically include:
Emergency stop buttons: Allow immediate shutdown in case of an emergency.
Interlock systems: Prevent simultaneous opening of both doors to maintain a controlled environment.
Obstruction sensors: Detect and stop the operation if an obstruction is detected, ensuring safety for personnel and products.
These features help ensure safe and efficient operation.
13. What are the noise levels of air showers?
Noise levels of air showers typically range from 60 to 75 decibels, depending on the model and design. Factors such as the type of blower and air velocity can influence the noise level. It's important to consider noise levels when selecting an air shower, especially in environments where low noise is critical.
14. What are the common applications of cargo air showers?
Common applications of cargo air showers include:
Food processing: Ensuring contaminants do not enter clean processing areas.
Pharmaceuticals: Maintaining sterile conditions for drug manufacturing.
Electronics: Preventing dust and particles from affecting sensitive components.
Biotech: Protecting laboratory environments from external contaminants.
15. How to install an automatic assembly line air shower?
Installing an automatic assembly line air shower involves several steps. First, select a suitable location that aligns with the production flow. Then, prepare the site by ensuring proper electrical and ventilation connections. Finally, install the air shower, align it with the assembly line, and conduct thorough testing to ensure proper operation. Professional installation is recommended to ensure compliance with safety and performance standards.
16. Can air showers be integrated into existing systems?
Yes, air showers can be integrated into existing systems. The integration process may require customization to ensure compatibility with current workflows and infrastructure. Professional consultation and installation are advisable to ensure seamless operation and to address any potential challenges during the integration process.
17. How to document air shower maintenance activities?
Documenting air shower maintenance activities involves maintaining a detailed log of all inspections, repairs, and part replacements. Use a standardized form to record the date, nature of the maintenance, and the technician's name. Regularly review and update the log to ensure all maintenance activities are tracked and any recurring issues are identified and addressed promptly.
18. What are the common materials used in air shower construction?
Common materials used in air shower construction include:
Stainless steel: Offers durability and resistance to corrosion.
Galvanized steel: Provides a cost-effective yet durable option.
High-quality plastics: Used for certain components to reduce weight and cost.
These materials ensure the air shower is robust, easy to clean, and capable of withstanding the rigors of industrial use.
Factory Production Workshop Video
Factory Photo
Product Packaging And International Logistics
Product International Certification
Find Other Common Equipment Recommendations
-
Modular CleanRoom
US$9000-10000 USD/Unit
Min. Order:1 unit -
Air Shower
US$1000.00-5000.00 USD/Unit
Min. Order:1 unit -
Downflow Booth
US$3000-6000 USD/Unit
Min. Order:1 unit -
Clean bench
US$600-2000 USD/Unit
Min. Order:1 unit -
Air Filter
US$3-50 USD/Unit
Min. Order:1 unit -
Cleanroom Wall Panels
US$10-20 USD/sq.
Min. Order:1 unit -
Pass Box
US$200-500 USD/Unit
Min. Order:1 unit -
FFU
US$135-350 USD/Unit
Min. Order:1 unit -
Fume Hood
US$700-1500 USD/Unit
Min. Order:1 unit -
Cleanroom HVAC
US$5000-20000 USD/Unit
Min. Order:1 unit -
Clean room floor
US$5-20 USD/Sq.
Min. Order:1 unit -
Clean room ceiling
US$
Min. Order:1 unit