15 x 18M ISO 5 Hardwall Cleanroom
Reference Price:US$70000.00-85000.00
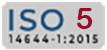



Cleanroom
15 x 18M ISO 5 Hardwall Cleanroom
Choose your installation & validation options below
Quantity:
Choose your Cleanroom frame structure material
Quantity:
Choose your Cleanroom Wall enclosure materials
Quantity:
Choose your Temperature requirements
Quantity:
Choose your humidity requirements
Quantity:
Choose your Explosion-proof requirements
Quantity:
Summary
15 x 18M ISO 5 Hardwall Cleanroom
Validation
Installation & Validation
Find Similar Products
-
3 X 5M ISO 5 Hardwall Cleanrooms
US$6000-30000 USD/Set
Min. Order:1 Set -
2 X 3M ISO 5 hardwall cleanrooms
US$6000-30000 USD/Set
Min. Order:1 Set -
5 X 8M ISO 5 Hardwall Cleanrooms
US$6000-30000 USD/Set
Min. Order:1 Set -
5 X 5M ISO 5 Hardwall Cleanrooms
US$6000-30000 USD/Set
Min. Order:1 Set -
8 x 10M ISO 5 Hardwall Cleanroom
US$6000-30000 USD/Set
Min. Order:1 Set -
5 x 10m ISO 5 Hardwall cleanroom
US$6000-30000 USD/Set
Min. Order:1 Set
Cleanrooms Detail
A 15 x 18 meter ISO 5 hardwall cleanroom is a high-precision controlled environment designed to meet stringent cleanliness standards. With durable hardwall construction, HEPA filtration systems, and advanced airflow management, this cleanroom ensures minimal airborne particles, making it ideal for industries like pharmaceuticals, biotechnology, and semiconductor manufacturing. It offers reliable control over temperature, humidity, and particle levels, providing a safe and efficient space for critical processes.
Key Features of an ISO 5 Cleanroom
Particle Count: An ISO 5 cleanroom has a particle count of 3,520 particles or fewer per cubic meter for particles that are 0.5 microns or larger.
Air Changes per Hour (ACH): ISO 5 cleanrooms typically have an air change rate of at least 240 to 540 air changes per hourto maintain proper airflow and cleanliness.
Airflow: The cleanroom utilizes laminar flowor unidirectional airflow, where clean, filtered air is directed across the room in a single direction, minimizing the risk of contamination.
Materials: Hardwall cleanrooms use rigid wall panels, often made of materials like stainless steel, aluminum, or composite panels, providing an airtight environment and easy-to-clean surfaces
Hardwall Cleanroom Specification
No | Item | Data | Optional |
1 | Product | Clean room | The price needs to be re-calculated |
2 | Size | L5.3m*W3.5m*H2m | Yes |
3 | Cleanliness | 1000class | 10/100/10000 class |
4 | Wall | Antistatic pvc grid curtain | Acrylic or toughened glass |
5 | Door | Pvc soft curtain | Acrylic or toughened glass |
6 | Frame | Aluminium 5050 | Stainless steel |
7 | FFU | 1175*575*320MM / Aluminium zinc /6 sets | Stainless steel |
8 | Purified lamp | 15W /8Pcs | Quantity |
9 | Voltage | AC 220V/50hz | Yes |
Cleanrooms Airflow
To maintain ISO 5 classification, the following criteria must be met:
Particle Concentration Limits (per cubic meter of air)
0.5 microns: ≤ 3,520 particles
5 microns: ≤ 0.1 particles (the particle count drops significantly for larger particles)
Class 100 (in U.S. classification): ISO 5 cleanrooms are often referred to as Class 100 cleanrooms in the U.S. classification system.
Airflow Design
Laminar or Unidirectional Airflow: To maintain the cleanliness, air must flow in a uniform direction, typically from ceiling to floor, with minimal turbulence to prevent particles from settling.
HEPA or ULPA Filters: Air is filtered through High-Efficiency Particulate Air (HEPA) or Ultra-Low Penetration Air (ULPA)filters that capture particles down to 0.3 microns or smaller. ULPA filters provide even higher efficiency, capturing particles down to 0.12 microns.
Cleanrooms Installation
Installation Steps
Environment Preparation
Frame Assembly
Filter and Fan Installation
Commissioning
Cleanrooms Testing
-
Air Supply and Exhaust Volume Testing
-
Airflow Control Inspection
-
Inspection Instruments and Equipment
-
Testing Standards and Criteria
-
Testing Steps and Processes
FAQ
1. How to achieve ISO 5 standards in hardwall cleanrooms?
Achieving ISO 5 standards in hardwall cleanrooms involves ensuring stringent contamination control through the use of HEPA filters, maintaining a high rate of air changes per hour (ACH), and controlling temperature and humidity levels. Regular monitoring of airborne particles and periodic testing of the cleanroom environment is essential to ensure compliance with ISO 5 standards.
2. What are the air filtration technologies for cleanrooms?
The most commonly used air filtration technologies for cleanrooms include:
HEPA filters: These are capable of trapping 99.97% of particles as small as 0.3 microns.
ULPA filters: These provide even higher efficiency than HEPA filters for more critical applications.
Activated carbon filters: Used for removing gases and odors from the air.
These filtration technologies help maintain cleanroom air quality and prevent contamination.
3. How to ensure proper sealing in a hardwall cleanroom?
Proper sealing in a hardwall cleanroom is essential to prevent air leakage and maintain the desired pressure differentials. This involves using high-quality sealants at all junctions, ensuring that doors and windows are tightly fitted, and that all panels and joints are correctly sealed. Regular inspections and maintenance of seals are necessary to ensure continued performance.
4. How to design a cleanroom HVAC system?
Designing a cleanroom HVAC system involves careful consideration of airflow, filtration, and temperature control. The system should include HEPA or ULPA filters, with air directed to flow in a laminar pattern to minimize particle contamination. The system should also ensure a consistent airflow and maintain precise temperature and humidity levels to meet cleanroom standards.
5. What is the difference between hardwall and softwall cleanrooms?
The primary difference between hardwall and softwall cleanrooms is the construction material. Hardwall cleanrooms have rigid, durable walls made of materials such as metal or composite panels, offering a more permanent and robust structure. Softwall cleanrooms, on the other hand, use flexible plastic or vinyl walls that can be easier to install and reconfigure but may not offer the same level of structural integrity and long-term durability.
6. How to choose the right flooring for a hardwall cleanroom?
When choosing flooring for a hardwall cleanroom, it is essential to select materials that are non-shedding, easy to clean, and resistant to chemical and physical wear. Options such as epoxy resin, vinyl, or seamless rubber flooring are commonly used, as they provide a smooth surface that minimizes dust and particle generation. The flooring must also be durable enough to withstand the traffic and equipment usage in the cleanroom.
7. What are the protocols for cleanroom garment changing?
Protocols for cleanroom garment changing include:
Entering the changing area: Personnel must pass through air showers or gowning rooms to remove contaminants from clothing.
Wearing cleanroom garments: Gowns, gloves, masks, and other protective gear must be worn to prevent contamination.
Changing frequency: Garments should be changed regularly, especially if they become contaminated or soiled.
Strict adherence to garment protocols helps maintain a contamination-free environment.
8. How to control humidity in an ISO 5 hardwall cleanroom?
Humidity in an ISO 5 hardwall cleanroom can be controlled using an HVAC system with built-in humidity control functions. This includes the use of humidifiers or dehumidifiers as needed, alongside regular monitoring of humidity levels. Maintaining an optimal humidity range is crucial to ensure the stability of sensitive processes and to prevent condensation that could compromise cleanroom conditions.
9. How to ensure proper cleanroom decontamination?
To ensure proper cleanroom decontamination, a systematic cleaning schedule must be followed, including wiping down surfaces with approved disinfectants and performing periodic deep cleanings. Air handling units, filters, and HVAC systems should be regularly maintained and disinfected. Additionally, personnel must adhere to gowning and hygiene protocols to minimize the risk of contamination.
10. What are the air change rates for ISO 5 cleanrooms?
ISO 5 cleanrooms typically require an air change rate of at least 240 air changes per hour (ACH) to maintain the necessary particle concentration levels. This high air change rate ensures that the cleanroom environment stays free from airborne contaminants and meets the stringent cleanliness standards for critical applications.
11. What are the maintenance protocols for hardwall cleanrooms?
Maintenance protocols for hardwall cleanrooms include regular inspections of HVAC systems, HEPA filters, and air handling units. Filters should be replaced at specified intervals, and all surfaces should be cleaned frequently to minimize particle buildup. Additionally, the cleanroom's sealing integrity and airflow patterns should be tested periodically to ensure compliance with ISO standards.
12. What are the costs associated with ISO 5 cleanrooms?
The costs associated with ISO 5 cleanrooms include initial construction or setup costs, typically ranging from $200 to $400 per square foot. Additional expenses include ongoing maintenance, filter replacements, and equipment calibration. Regular testing and certification to ensure ISO 5 compliance can also add to the long-term operational costs.
13. What are the airflow patterns in hardwall cleanrooms?
In hardwall cleanrooms, the airflow patterns are typically designed to ensure unidirectional (laminar) airflow. This means air flows in a consistent, one-way direction, usually from ceiling to floor, to minimize the risk of particle contamination. Airflow patterns should be carefully designed to match the cleanroom's function and ensure that contamination is quickly removed.
14. What are the requirements for cleanroom ventilation?
Cleanroom ventilation requires precise control of airflow, air filtration, and air pressure differentials. The system should provide a consistent volume of filtered air, maintain appropriate temperature and humidity levels, and ensure that airflows are directed in a manner that minimizes contamination. Proper air handling units and ventilation ducts must be regularly maintained to keep the system operating efficiently.
15. What are the challenges in maintaining ISO 5 cleanrooms?
Maintaining ISO 5 cleanrooms involves challenges such as ensuring consistent environmental conditions, frequent replacement of filters, and maintaining high levels of cleanliness. Regular monitoring and testing are necessary to detect any deviations from the required standards. Additionally, personnel training and adherence to gowning and hygiene protocols are crucial to prevent contamination.
16. How to monitor particle levels in an ISO 5 hardwall cleanroom?
Monitoring particle levels in an ISO 5 hardwall cleanroom involves using particle counters to measure the concentration of airborne particles. These devices should be calibrated regularly to ensure accurate readings. Data from these monitoring systems is essential for ensuring that the cleanroom maintains the necessary cleanliness levels for ISO 5 compliance.
17. How to select cleanroom air handling units?
When selecting cleanroom air handling units (AHUs), it is important to choose units that can provide consistent airflow, meet the necessary air change rates, and support the required level of filtration. The AHUs should be compatible with the cleanroom's HVAC system and capable of maintaining the temperature and humidity levels needed for specific applications.
Factory Production Workshop Video
Factory Photo
Product Packaging And International Logistics
Product International Certification
Find Other Common Equipment Recommendations
-
Modular CleanRoom
US$9000-10000 USD/Unit
Min. Order:1 Set -
Air Shower
US$1000.00-5000.00 USD/Unit
Min. Order:1 Set -
Downflow Booth
US$3000-6000 USD/Unit
Min. Order:1 Set -
Clean bench
US$600-2000 USD/Unit
Min. Order:1 Set -
Air Filter
US$3-50 USD/Unit
Min. Order:1 Set -
Cleanroom Wall Panels
US$10-20 USD/sq.
Min. Order:1 Set -
Pass Box
US$200-500 USD/Unit
Min. Order:1 Set -
FFU
US$135-350 USD/Unit
Min. Order:1 Set -
Fume Hood
US$700-1500 USD/Unit
Min. Order:1 Set -
Cleanroom HVAC
US$5000-20000 USD/Unit
Min. Order:1 Set -
Clean room floor
US$5-20 USD/Sq.
Min. Order:1 Set -
Clean room ceiling
US$
Min. Order:1 Set