5 X 5M ISO 5 Hardwall Cleanrooms
Reference Price:US$5000-7000
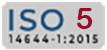

Cleanroom
5 X 5M ISO 5 Hardwall Cleanrooms
Choose your installation & validation options below
Quantity:
Choose your Cleanroom frame structure material
Quantity:
Choose your Cleanroom Wall enclosure materials
Quantity:
Choose your Temperature requirements
Quantity:
Choose your humidity requirements
Quantity:
Choose your Explosion-proof requirements
Quantity:
Summary
5 X 5M ISO 5 Hardwall Cleanrooms
Validation
Installation & Validation
Find Similar Products
-
3 X 5M ISO 5 Hardwall Cleanrooms
US$6000-30000 USD/Set
Min. Order:1 unit -
2 X 3M ISO 5 hardwall cleanrooms
US$6000-30000 USD/Set
Min. Order:1 unit -
5 X 8M ISO 5 Hardwall Cleanrooms
US$6000-30000 USD/Set
Min. Order:1 unit -
5 X 5M ISO 5 Hardwall Cleanrooms
US$6000-30000 USD/Set
Min. Order:1 unit -
8 x 10M ISO 5 Hardwall Cleanroom
US$6000-30000 USD/Set
Min. Order:1 unit -
5 x 10m ISO 5 Hardwall cleanroom
US$6000-30000 USD/Set
Min. Order:1 unit
Cleanrooms Detail
A 5 x 5 meter ISO 5 hardwall cleanroom is a spacious, high-performance controlled environment designed to meet rigorous cleanliness standards. Featuring durable hardwall panels, advanced HEPA filtration, and precise airflow control, it ensures exceptionally low particle levels. This cleanroom is well-suited for larger-scale operations that require stringent contamination control and high precision, providing a reliable setting for critical processes.
Key Features of an ISO 5 Cleanroom
Particle Count: An ISO 5 cleanroom has a particle count of 3,520 particles or fewer per cubic meter for particles that are 0.5 microns or larger.
Air Changes per Hour (ACH): ISO 5 cleanrooms typically have an air change rate of at least 240 to 540 air changes per hourto maintain proper airflow and cleanliness.
Airflow: The cleanroom utilizes laminar flowor unidirectional airflow, where clean, filtered air is directed across the room in a single direction, minimizing the risk of contamination.
Materials: Hardwall cleanrooms use rigid wall panels, often made of materials like stainless steel, aluminum, or composite panels, providing an airtight environment and easy-to-clean surfaces
Hardwall Cleanroom Specification
No | Item | Data | Optional |
1 | Product | Clean room | The price needs to be re-calculated |
2 | Size | L5.3m*W3.5m*H2m | Yes |
3 | Cleanliness | 1000class | 10/100/10000 class |
4 | Wall | Antistatic pvc grid curtain | Acrylic or toughened glass |
5 | Door | Pvc soft curtain | Acrylic or toughened glass |
6 | Frame | Aluminium 5050 | Stainless steel |
7 | FFU | 1175*575*320MM / Aluminium zinc /6 sets | Stainless steel |
8 | Purified lamp | 15W /8Pcs | Quantity |
9 | Voltage | AC 220V/50hz | Yes |
Cleanrooms Airflow
To maintain ISO 5 classification, the following criteria must be met:
Particle Concentration Limits (per cubic meter of air)
0.5 microns: ≤ 3,520 particles
5 microns: ≤ 0.1 particles (the particle count drops significantly for larger particles)
Class 100 (in U.S. classification): ISO 5 cleanrooms are often referred to as Class 100 cleanrooms in the U.S. classification system.
Airflow Design
-
Laminar or Unidirectional Airflow: To maintain the cleanliness, air must flow in a uniform direction, typically from ceiling to floor, with minimal turbulence to prevent particles from settling.
-
HEPA or ULPA Filters: Air is filtered through High-Efficiency Particulate Air (HEPA) or Ultra-Low Penetration Air (ULPA)filters that capture particles down to 0.3 microns or smaller. ULPA filters provide even higher efficiency, capturing particles down to 0.12 microns.
Cleanrooms Installation
Environmental preparation: Ensure that the installation site is dry, ventilated and well-lit, avoiding direct sunlight and meeting additional industry-specific requirements, such as anti-static and anti-corrosion.
Foundation construction: Foundation construction should meet the design requirements to ensure that the foundation is level, solid and horizontal. Acceptance is required after construction and can only continue after passing.
Frame Installation: Use the clean shed frame made of steel section, ensure the verticality and levelness when installing, and then carry out anti-corrosion and anti-rust treatment.
Roof and wall plate installation: use purification board or other materials that meet the clean requirements to ensure the flatness of the roof and wall plate, with tight seams to avoid loopholes.
Air purification system installation: the interior should be equipped with an air purification system, including high-efficiency filters, air showers, ultraviolet disinfection lamps, etc. When installing, ensure that the components are connected tightly to avoid air leakage.
Lighting system installation: the interior should be equipped with a lighting system, such as LED lamps and lanterns, which should be installed in such a way as to ensure its waterproof and dustproof performance as well as the uniformity of illumination.
Electrical system installation: the electrical system should comply with national standards and industry requirements, and the installation should ensure that the power supply is stable and safe, and the equipment operates normally.
Grounding treatment: the grounding treatment should meet the design requirements to ensure the safe operation of internal equipment.
Acceptance and debugging: acceptance after the completion of installation, qualified for debugging the clean shed to ensure that the normal operation of the system to achieve the desired clean effect.
Cleanrooms Testing
Air Supply and Exhaust Volume Testing
Airflow Control Inspection
Inspection Instruments and Equipment
Testing Standards and Criteria
Testing Steps and Processes
FAQ
1. What are the cleanroom validation protocols?
Cleanroom validation protocols include comprehensive procedures to ensure the cleanroom meets specified standards. This involves:
Particle count testing
Airflow and filtration efficiency tests
Environmental monitoring
Regular validation helps maintain compliance with ISO 5 standards.
2. How to design a hardwall cleanroom layout?
When designing a hardwall cleanroom layout, consider workflow optimization to minimize contamination risks. Utilize modular components for flexibility and ensure proper placement of critical systems such as HVAC, filtration, and electrical outlets. Design the layout to allow for easy cleaning and maintenance access.
3. What are the cleaning protocols for hardwall cleanrooms?
Cleaning protocols for hardwall cleanrooms involve daily, weekly, and monthly tasks.
Daily: Wipe down surfaces with approved disinfectants.
Weekly: Clean floors and walls.
Monthly: Inspect and clean HVAC systems.
These protocols ensure continuous compliance with ISO 5 standards.
4. How to control temperature in an ISO 5 hardwall cleanroom?
Temperature control in an ISO 5 hardwall cleanroom is achieved through a precise HVAC system. This system maintains a stable temperature and relative humidity, crucial for sensitive processes. Regular monitoring and calibration of the HVAC system ensure consistent environmental conditions.
5. How to design a cleanroom for healthcare applications?
Designing a cleanroom for healthcare applications requires stringent contamination control measures. Use non-shedding, easy-to-clean materials for all surfaces. Incorporate advanced HEPA filtration systems to maintain ISO 5 air quality standards. Ensure proper layout to facilitate smooth workflow and reduce contamination risks.
6. What are the challenges in designing hardwall cleanrooms?
Challenges in designing hardwall cleanrooms include ensuring effective contamination control and integrating complex HVAC and filtration systems. Selecting durable, easy-to-clean materials while meeting regulatory standards is also crucial. Additionally, planning for future scalability without compromising current operational efficiency is a significant challenge.
7. How to build an ISO 5 hardwall cleanroom?
Building an ISO 5 hardwall cleanroom involves several key steps. First, prepare the site and layout plan. Next, install the structural components and panels with proper sealing. Integrate the HVAC and filtration systems, followed by electrical and plumbing installations. Finally, conduct validation tests to ensure the cleanroom meets ISO 5 standards.
8. What are the requirements for cleanroom garments?
Cleanroom garments must be designed to minimize particle shedding and contamination. Typical requirements include:
Gowns: Non-linting, full-body coverage
Gloves: Nitrile or latex, powder-free
Masks: High-filtration efficiency
These garments are essential for maintaining ISO 5 cleanliness levels.
9. What equipment is needed for an ISO 5 hardwall cleanroom?
An ISO 5 hardwall cleanroom requires specific equipment to maintain its stringent cleanliness standards. This includes:
HEPA filtration systems
Airflow control devices
Environmental monitoring tools
These components work together to ensure the cleanroom operates effectively.
10. What materials are used in hardwall cleanrooms?
Materials used in hardwall cleanrooms are chosen for their durability and ease of cleaning. Common materials include stainless steel, epoxy-coated panels, and polycarbonate or tempered glass for windows. These materials help maintain the cleanroom's structural integrity and cleanliness.
11. How to ensure sterility in an ISO 5 hardwall cleanroom?
Ensuring sterility in an ISO 5 hardwall cleanroom involves rigorous protocols and regular monitoring. Implement stringent cleaning and disinfection procedures using appropriate agents. Train personnel on proper gowning and hygiene practices. Conduct regular environmental monitoring to detect and address any potential contaminants promptly.
12. How to handle waste in an ISO 5 hardwall cleanroom?
Handling waste in an ISO 5 hardwall cleanroom requires strict protocols. Use designated containers for different types of waste, such as biological and chemical waste. Regularly remove waste from the cleanroom and dispose of it according to regulatory guidelines. Ensure staff are trained in proper waste handling procedures.
13. What industries use ISO 5 hardwall cleanrooms?
Industries that use ISO 5 hardwall cleanrooms include:
Pharmaceuticals
Biotechnology
Electronics manufacturing
Aerospace
These industries require strict contamination control to ensure the integrity and quality of their products.
14. What are the testing procedures for cleanroom validation?
Testing procedures for cleanroom validation include particle count testing, airflow visualization, and filter integrity testing. Environmental monitoring for microbial contamination is also essential. These procedures ensure the cleanroom meets the required ISO 5 standards and maintains its integrity.
15. How to train staff for working in a hardwall cleanroom?
Training staff for working in a hardwall cleanroom involves comprehensive instruction on contamination control, proper gowning procedures, and cleanroom protocols. Regular refresher courses and hands-on training sessions are essential to ensure ongoing compliance and operational efficiency.
16. What are the best materials for hardwall cleanroom construction?
The best materials for hardwall cleanroom construction include stainless steel, epoxy-coated steel or aluminum panels, and polycarbonate or tempered glass windows. These materials provide durability, ease of cleaning, and resistance to contamination, ensuring long-term reliability and compliance with stringent cleanliness standards.
17. How to design a cleanroom HVAC system?
Designing a cleanroom HVAC system involves ensuring proper air filtration, temperature, and humidity control. Use HEPA filters to maintain air quality and plan airflow patterns to minimize contamination risks. Regularly monitor and maintain the system to ensure it operates within the required parameters.
Factory Production Workshop Video
Factory Photo
Product Packaging And International Logistics
Product International Certification
Find Other Common Equipment Recommendations
-
Modular CleanRoom
US$9000-10000 USD/Unit
Min. Order:1 unit -
Air Shower
US$1000.00-5000.00 USD/Unit
Min. Order:1 unit -
Downflow Booth
US$3000-6000 USD/Unit
Min. Order:1 unit -
Clean bench
US$600-2000 USD/Unit
Min. Order:1 unit -
Air Filter
US$3-50 USD/Unit
Min. Order:1 unit -
Cleanroom Wall Panels
US$10-20 USD/sq.
Min. Order:1 unit -
Pass Box
US$200-500 USD/Unit
Min. Order:1 unit -
FFU
US$135-350 USD/Unit
Min. Order:1 unit -
Fume Hood
US$700-1500 USD/Unit
Min. Order:1 unit -
Cleanroom HVAC
US$5000-20000 USD/Unit
Min. Order:1 unit -
Clean room floor
US$5-20 USD/Sq.
Min. Order:1 unit -
Clean room ceiling
US$
Min. Order:1 unit