3 X 5M ISO 5 Hardwall Cleanrooms
Reference Price:US$4000-6000


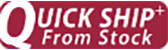
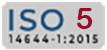
Cleanroom
3 X 5M ISO 5 Hardwall Cleanrooms
Choose your installation & validation options below
Quantity:
Choose your Cleanroom frame structure material
Quantity:
Choose your Cleanroom Wall enclosure materials
Quantity:
Choose your Temperature requirements
Quantity:
Choose your humidity requirements
Quantity:
Choose your Explosion-proof requirements
Quantity:
Summary
3 X 5M ISO 5 Hardwall Cleanrooms
Validation
Installation & Validation
Find Similar Products
-
3 X 5M ISO 5 Hardwall Cleanrooms
US$6000-30000 USD/Set
Min. Order:1 Set -
2 X 3M ISO 5 hardwall cleanrooms
US$6000-30000 USD/Set
Min. Order:1 Set -
5 X 8M ISO 5 Hardwall Cleanrooms
US$6000-30000 USD/Set
Min. Order:1 Set -
5 X 5M ISO 5 Hardwall Cleanrooms
US$6000-30000 USD/Set
Min. Order:1 Set -
8 x 10M ISO 5 Hardwall Cleanroom
US$6000-30000 USD/Set
Min. Order:1 Set -
5 x 10m ISO 5 Hardwall cleanroom
US$6000-30000 USD/Set
Min. Order:1 Set
Cleanrooms Detail
A 3 x 5 meter ISO 5 hardwall cleanroom is a moderately sized, high-efficiency controlled environment designed for stringent cleanliness. Equipped with robust wall panels, advanced HEPA filtration, and precise airflow management, it maintains ultra-low particle levels. This cleanroom is ideal for medium-scale operations requiring high precision and contamination control, offering a reliable space for sensitive processes.
Key Features of an ISO 5 Cleanroom
Particle Count: An ISO 5 cleanroom has a particle count of 3,520 particles or fewer per cubic meter for particles that are 0.5 microns or larger.
Air Changes per Hour (ACH): ISO 5 cleanrooms typically have an air change rate of at least 240 to 540 air changes per hourto maintain proper airflow and cleanliness.
Airflow: The cleanroom utilizes laminar flowor unidirectional airflow, where clean, filtered air is directed across the room in a single direction, minimizing the risk of contamination.
Materials: Hardwall cleanrooms use rigid wall panels, often made of materials like stainless steel, aluminum, or composite panels, providing an airtight environment and easy-to-clean surfaces
Hardwall Cleanroom Specification
No | Item | Data | Optional |
1 | Product | Clean room | The price needs to be re-calculated |
2 | Size | L5.3m*W3.5m*H2m | Yes |
3 | Cleanliness | 1000class | 10/100/10000 class |
4 | Wall | Antistatic pvc grid curtain | Acrylic or toughened glass |
5 | Door | Pvc soft curtain | Acrylic or toughened glass |
6 | Frame | Aluminium 5050 | Stainless steel |
7 | FFU | 1175*575*320MM / Aluminium zinc /6 sets | Stainless steel |
8 | Purified lamp | 15W /8Pcs | Quantity |
9 | Voltage | AC 220V/50hz | Yes |
Cleanrooms Airflow
To maintain ISO 5 classification, the following criteria must be met:
Particle Concentration Limits (per cubic meter of air)
0.5 microns: ≤ 3,520 particles
5 microns: ≤ 0.1 particles (the particle count drops significantly for larger particles)
Class 100 (in U.S. classification): ISO 5 cleanrooms are often referred to as Class 100 cleanrooms in the U.S. classification system.
Airflow Design
Laminar or Unidirectional Airflow: To maintain the cleanliness, air must flow in a uniform direction, typically from ceiling to floor, with minimal turbulence to prevent particles from settling.
HEPA or ULPA Filters: Air is filtered through High-Efficiency Particulate Air (HEPA) or Ultra-Low Penetration Air (ULPA)filters that capture particles down to 0.3 microns or smaller. ULPA filters provide even higher efficiency, capturing particles down to 0.12 microns.
Cleanrooms Installation
Installation Location
The clean shed should be installed in a dry, ventilated and well-lit environment, avoiding direct sunlight. The installation location should also meet the special requirements of specific industries, such as anti-static and anti-corrosion.
Foundation construction
The foundation construction of the clean shed should meet the design requirements to ensure that the foundation is level, solid and horizontal. After the foundation construction, acceptance should be carried out, and the installation of clean shed can be carried out only after passing.
Frame installation
The frame of the clean shed is made of steel, and the verticality and horizontality of the frame should be ensured during installation. After the installation of the frame is completed, it should be treated with anti-corrosion and anti-rust treatment.
Ceiling and wall plate installation
The ceiling and wall plate should be made of purified board or other materials that meet the cleanliness requirements. When installing, make sure the flatness and tightness of joints of the ceiling and wall plate to avoid loopholes.
Air purification system installation
The interior of the clean shed should be equipped with an air purification system, including high-efficiency filters, air showers, ultraviolet disinfection lamps and so on. When installing, make sure the connection between components is tight to avoid air leakage.
Lighting system installation
The interior of the clean room should be equipped with a lighting system, such as LED lamps and lanterns. When installing, ensure the waterproof and dustproof performance of the lamps, as well as the uniformity of illumination.
Electrical system installation
The electrical system of the clean room should meet the relevant national standards and industry requirements. When installing, make sure the power supply is stable and safe, as well as the normal operation of each electrical equipment.
Grounding treatment
The grounding treatment of the clean room should meet the design requirements to ensure the safe operation of the equipment inside the clean room.
Acceptance and debugging
Clean shed installation is completed, acceptance should be carried out. After acceptance, the clean shed debugging to ensure that the normal operation of the system to achieve the desired clean effect.
Cleanrooms Testing
-
Air Supply and Exhaust Volume Testing
-
Airflow Control Inspection
-
Inspection Instruments and Equipment
-
Testing Standards and Criteria
-
Testing Steps and Processes
FAQ
1. What are the benefits of modular cleanrooms?
Modular cleanrooms offer numerous benefits including quick installation, cost-effectiveness, and flexibility for reconfiguration. These cleanrooms can be easily expanded or relocated, making them ideal for evolving operational needs. Additionally, they often come with pre-engineered components, reducing construction time and ensuring high-quality standards.
2. How to test air quality in an ISO 5 hardwall cleanroom?
Testing air quality in an ISO 5 hardwall cleanroom involves several key steps. Use a particle counter to measure airborne particulate levels, ensuring they meet ISO 5 standards with fewer than 3,520 particles per cubic meter. Additionally, conduct microbial sampling to detect any biological contaminants. Regular monitoring and documentation of air quality data are essential for maintaining compliance.
3. How to ensure compliance with ISO 5 standards?
Ensuring compliance with ISO 5 standards involves implementing rigorous protocols and regular monitoring. Establish standard operating procedures (SOPs) that align with ISO 5 requirements, including frequent cleaning and maintenance schedules. Regularly train personnel on these procedures and conduct periodic audits to identify and rectify any non-compliance issues.
4. How to design a cleanroom for aerospace applications?
Designing a cleanroom for aerospace applications requires careful consideration of contamination control, structural integrity, and environmental stability. The cleanroom should feature advanced HEPA filtration systems to maintain a high level of air purity. Additionally, it should be constructed with durable, non-shedding materials to prevent particulate contamination. Ensuring proper airflow patterns and environmental controls is crucial for meeting the stringent requirements of aerospace manufacturing.
5. What are the key features of hardwall cleanrooms?
Hardwall cleanrooms are characterized by their rigid, durable walls made from materials like stainless steel or epoxy-coated panels. These cleanrooms offer high structural integrity and are easy to clean, making them suitable for stringent contamination control. Key features include advanced HEPA filtration systems, precise environmental controls, and robust construction that ensures long-term reliability.
6. How to install a hardwall cleanroom?
Installing a hardwall cleanroom involves several steps. First, prepare the site and layout plan. Next, install the structural components and panels, ensuring they are properly sealed. Integrate the HVAC and filtration systems, followed by electrical and plumbing installations. Finally, conduct validation tests to ensure the cleanroom meets the desired specifications.
7. What are the vibration control measures for cleanrooms?
Vibration control in cleanrooms is essential to prevent disruptions to sensitive processes. Measures include isolating equipment on vibration-dampening platforms, using anti-vibration pads, and designing the cleanroom structure to minimize external vibration transmission. Regular monitoring and maintenance of these controls are crucial for maintaining a stable environment.
8. What are the challenges in designing hardwall cleanrooms?
Designing hardwall cleanrooms presents several challenges, including ensuring proper airflow to maintain cleanliness levels and selecting materials that are both durable and easy to clean. Additionally, integrating complex systems such as HVAC and filtration and meeting stringent regulatory standards can be challenging. Accommodating future scalability while maintaining current operational efficiency is also a key consideration.
9. What are the lighting standards for ISO 5 cleanrooms?
Lighting standards for ISO 5 cleanrooms focus on providing adequate illumination without generating excessive heat or contaminating particles. The lighting should be uniformly distributed to prevent shadows and glare, which can interfere with precision tasks. Typically, cleanroom lighting fixtures are sealed and designed to be easy to clean, ensuring they do not compromise the cleanroom's sterile environment.
10. How to ensure proper air pressure in cleanrooms?
Ensuring proper air pressure in cleanrooms involves maintaining a positive pressure differential relative to adjacent spaces. This prevents contaminants from entering the cleanroom. Key steps include:
Installing high-efficiency HVAC systems
Regularly monitoring pressure levels
Adjusting airflow rates as necessary
Regular inspections and maintenance of the HVAC system are crucial for sustaining the desired air pressure.
11. What are the air filtration technologies for cleanrooms?
Air filtration technologies for cleanrooms include HEPA (High-Efficiency Particulate Air) filters, ULPA (Ultra-Low Penetration Air) filters, and pre-filters. HEPA filters are capable of removing at least 99.97% of particles 0.3 microns or larger, while ULPA filters offer even higher efficiency. Pre-filters are used to capture larger particles, extending the life of HEPA and ULPA filters.
12. What are the air filtration requirements for ISO 5 hardwall cleanrooms?
ISO 5 hardwall cleanrooms require advanced air filtration to maintain strict cleanliness levels. This includes the use of HEPA filters capable of removing 99.97% of particles 0.3 microns or larger. Air change rates should be between 240 to 480 changes per hour to ensure continuous removal of airborne contaminants. Regular maintenance and validation of the filtration system are essential for compliance.
13. What industries use ISO 5 hardwall cleanrooms?
Industries that use ISO 5 hardwall cleanrooms include:
Pharmaceuticals
Biotechnology
Electronics manufacturing
Aerospace
These industries require strict contamination control to ensure the integrity and quality of their products.
14. What is the lifespan of a hardwall cleanroom?
The lifespan of a hardwall cleanroom can vary depending on factors such as usage, maintenance, and the materials used in construction. Typically, a well-maintained hardwall cleanroom can last between 10 to 15 years. Regular inspections and timely repairs can help extend its lifespan.
15. What are the best materials for hardwall cleanroom construction?
The best materials for hardwall cleanroom construction include stainless steel, epoxy-coated steel or aluminum panels, and polycarbonate or tempered glass windows. These materials provide durability, ease of cleaning, and resistance to contamination, ensuring long-term reliability and compliance with stringent cleanliness standards.
16. How to ensure sterility in an ISO 5 hardwall cleanroom?
Ensuring sterility in an ISO 5 hardwall cleanroom requires rigorous protocols and regular monitoring. Implement stringent cleaning and disinfection procedures using appropriate agents. Train personnel on proper gowning and hygiene practices. Conduct regular environmental monitoring to detect and address any potential contaminants promptly.
Factory Production Workshop Video
Factory Photo
Product Packaging And International Logistics
Product International Certification
Find Other Common Equipment Recommendations
-
Modular CleanRoom
US$9000-10000 USD/Unit
Min. Order:1 Set -
Air Shower
US$1000.00-5000.00 USD/Unit
Min. Order:1 Set -
Downflow Booth
US$3000-6000 USD/Unit
Min. Order:1 Set -
Clean bench
US$600-2000 USD/Unit
Min. Order:1 Set -
Air Filter
US$3-50 USD/Unit
Min. Order:1 Set -
Cleanroom Wall Panels
US$10-20 USD/sq.
Min. Order:1 Set -
Pass Box
US$200-500 USD/Unit
Min. Order:1 Set -
FFU
US$135-350 USD/Unit
Min. Order:1 Set -
Fume Hood
US$700-1500 USD/Unit
Min. Order:1 Set -
Cleanroom HVAC
US$5000-20000 USD/Unit
Min. Order:1 Set -
Clean room floor
US$5-20 USD/Sq.
Min. Order:1 Set -
Clean room ceiling
US$
Min. Order:1 Set