2 x 4 ISO 5 Softwall cleanroom
Reference Price:US$3300.00-4500.00
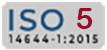



Cleanroom
2 x 4 ISO 5 Softwall cleanroom
Choose your installation & validation options below
Quantity:
Choose your Cleanroom frame structure material
Quantity:
Choose your Cleanroom Wall enclosure materials
Quantity:
Choose your Temperature requirements
Quantity:
Choose your humidity requirements
Quantity:
Choose your Explosion-proof requirements
Quantity:
Summary
2 x 4 ISO 5 Softwall cleanroom
Validation
Installation & Validation
Find Similar Products
-
2 x 5m ISO 5 Softwall cleanroom
US$3000-20000 USD/Set
Min. Order:1 Set -
2 x 4 ISO 5 Softwall cleanroom
US$3000-20000 USD/Set
Min. Order:1 Set -
2 x 3 ISO 5 softwall cleanroom
US$3000-20000 USD/Set
Min. Order:1 Set -
2 x 2 ISO 5 softwall cleanroom
US$3000-20000 USD/Set
Min. Order:1 Set -
4 x 6m ISO 5 Softwall Cleanroom
US$3000-20000 USD/Set
Min. Order:1 Set -
4 x 5m ISO 5 Softwall Cleanroom
US$3000-20000 USD/Set
Min. Order:1 Set
Cleanrooms Detail
Softwall cleanroom products are designed for environments that require stringent cleanliness standards, such as the pharmaceutical, semiconductor and biotechnology industries. These products help maintain controlled contamination levels and ensure the safety and integrity of sensitive processes and materials.
Key Features:
High-quality materials: our cleanroom products are made from premium materials that resist contamination and degradation. Commonly used materials include:
Frames: 40x40 industrial aluminum extrusions or stainless steel squares
Polypropylene: lightweight, chemically resistant and easy to clean.
PVC (Polyvinyl Chloride): Provides excellent durability and resistance to chemicals and moisture.
Nylon: known for its strength and flexibility, ideal for a variety of cleanroom applications.
Silicone: Excellent thermal stability and flexibility, commonly used for seals and gaskets.
Electrostatic Discharge (ESD) Protection: Many of our cleanroom products feature ESD characteristics to prevent damage to sensitive electronic components.
Cleanrooms Airflow
Cleanrooms Installation
Cleanrooms Testing
Testing items
The testing items of the clean room mainly include temperature, humidity, air suspended solids concentration, fresh air volume, differential pressure, airflow status and so on.
Testing standard
The cleanliness of a clean room is usually measured in terms of particle count per cubic meter (PCM) or per cubic foot (PCF), and there are different cleanliness standards for different industries and applications.
Testing Equipment
Commonly used equipment for clean room testing includes particle counters, bacterial samplers, differential pressure meters, anemometers, air volume hoods, noise meters, illuminance meters, temperature and humidity meters, etc.
Testing process
The testing process of clean room usually includes signing a contract, arranging on-site sampling, laboratory testing, and issuing a test report.
FAQ
What is the role of controlled environments in manufacturing?
Controlled environments play a crucial role in manufacturing by ensuring product quality and consistency. They minimize contamination, thus enhancing reliability and compliance. This leads to improved operational efficiency and customer satisfaction.
How to choose the right cleanroom layout?
Choosing the right cleanroom layout involves understanding the specific needs of your operations. It is vital to consider workflow, contamination control, and personnel movement. Important factors include:
Zoning activities to reduce cross-contamination.
Designing efficient airflow patterns to maintain cleanliness.
Ensuring accessibility for maintenance and equipment.
These considerations help optimize the cleanroom's effectiveness and efficiency.
How do you validate a softwall cleanroom?
Validating a softwall cleanroom requires a systematic approach to ensure it meets cleanliness standards. Start by assessing environmental conditions, such as temperature and humidity. Then, perform particle count testing to verify cleanliness. Key steps in the validation process include:
Documenting all operating procedures.
Verifying the effectiveness of air filtration systems.
Conducting routine performance audits to ensure compliance.
These steps help maintain the integrity of the cleanroom environment.
What is the difference between cleanrooms and controlled environments?
Cleanrooms are specialized environments designed specifically to minimize contamination. Controlled environments can include a broader range of settings and may not have stringent cleanliness standards. All cleanrooms are controlled environments, but not all controlled environments are cleanrooms.
How does pressure differential work in cleanrooms?
Pressure differential is essential for maintaining cleanroom integrity. It ensures that air flows from cleaner areas to less clean areas. Cleanrooms typically maintain a positive pressure relative to surrounding spaces, preventing contamination from entering.
What are the differences between unidirectional and non-unidirectional airflow?
Unidirectional airflow provides a continuous flow of air in a single direction, effectively reducing contamination. Non-unidirectional airflow allows air to move in multiple directions, increasing the risk of contamination. Key differences include:
Efficiency: Unidirectional is more effective at maintaining cleanliness.
Complexity: Unidirectional systems are generally more complex.
Applications: Unidirectional is preferred in critical environments.
These differences influence cleanroom design and operational strategies.
How do you ensure personnel compliance in a cleanroom?
Ensuring personnel compliance in a cleanroom involves implementing strict training and monitoring protocols. Regular training sessions are essential to reinforce procedures and protocols. Effective strategies include:
Conducting routine compliance audits.
Displaying clear signage to remind staff of protocols.
Establishing consequences for non-compliance.
These practices help maintain high cleanliness standards and operational integrity.
What is an air shower in a cleanroom?
An air shower is a specialized chamber designed to decontaminate personnel before entering a cleanroom. High-velocity air jets blow away particles from clothing and skin. This process effectively reduces potential contamination before individuals enter the cleanroom environment.
What is a softwall cleanroom?
A softwall cleanroom is a flexible cleanroom constructed with soft materials, typically vinyl. This design allows for easy reconfiguration to adapt to changing needs. Softwall cleanrooms maintain controlled environments suitable for various applications while being cost-effective.
How do you ensure cleanroom compliance during audits?
Ensuring cleanroom compliance during audits involves thorough preparation and meticulous documentation. Regular internal audits help identify areas for improvement. Key steps include:
Maintaining accurate records of operations and procedures.
Conducting pre-audit reviews to address potential issues.
Training staff on audit protocols and expectations.
These measures enhance compliance and operational integrity during audits.
What is the importance of cleanroom layout?
The layout of a cleanroom is vital for ensuring efficient workflows and maintaining cleanliness. A well-designed layout minimizes contamination risks and optimizes the use of space. Effective layouts also promote safety and ease of maintenance in cleanroom operations.
How do you conduct a cleanroom performance qualification?
Conducting a cleanroom performance qualification involves a series of tests to ensure it meets specified standards. Begin with environmental monitoring, including temperature and humidity checks. Next, perform particle counts and airflow assessments to verify system performance. Key components include:
Documenting all procedures and results.
Ensuring compliance with industry standards.
Regularly reviewing and updating qualification protocols.
These steps ensure the cleanroom operates effectively and consistently.
What are the best practices for cleanroom operations?
Best practices for cleanroom operations include maintaining strict protocols and regular training. Ensure that personnel follow gowning procedures and minimize movement within the cleanroom. Key practices include:
Regular equipment maintenance and calibration.
Continuous monitoring of environmental conditions.
Routine cleaning and disinfection protocols.
Factory Production Workshop Video
Factory Photo
Product Packaging And International Logistics
Product International Certification
Find Other Common Equipment Recommendations
-
Modular CleanRoom
US$9000-10000 USD/Unit
Min. Order:1 Set -
Air Shower
US$1000.00-5000.00 USD/Unit
Min. Order:1 Set -
Downflow Booth
US$3000-6000 USD/Unit
Min. Order:1 Set -
Clean bench
US$600-2000 USD/Unit
Min. Order:1 Set -
Air Filter
US$3-50 USD/Unit
Min. Order:1 Set -
Cleanroom Wall Panels
US$10-20 USD/sq.
Min. Order:1 Set -
Pass Box
US$200-500 USD/Unit
Min. Order:1 Set -
FFU
US$135-350 USD/Unit
Min. Order:1 Set -
Fume Hood
US$700-1500 USD/Unit
Min. Order:1 Set -
Cleanroom HVAC
US$5000-20000 USD/Unit
Min. Order:1 Set -
Clean room floor
US$5-20 USD/Sq.
Min. Order:1 Set -
Clean room ceiling
US$
Min. Order:1 Set