5 x 10M ISO 6 Modular Cleanroom
Reference Price:US$15200-20000


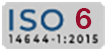
Cleanroom
5 x 10M ISO 6 Modular Cleanroom
Choose your installation & validation options below
Quantity:
Choose your Cleanroom frame structure material
Quantity:
Choose your Cleanroom Wall enclosure materials
Quantity:
Choose your Temperature requirements
Quantity:
Choose your humidity requirements
Quantity:
Choose your Explosion-proof requirements
Quantity:
Summary
5 x 10M ISO 6 Modular Cleanroom
Validation
Installation & Validation
Find Similar Products
-
5 x 15M ISO 6 Modular Cleanroom
US$18000-56000 USD/Set
Min. Order:1 Set -
6 x 10M ISO 6 Modular Cleanroom
US$18000-56000 USD/Set
Min. Order:1 Set -
6 x 8M ISO 6 Modular Cleanroom
US$18000-56000 USD/Set
Min. Order:1 Set -
6 x 6M ISO 6 Modular Cleanroom
US$18000-56000 USD/Set
Min. Order:1 Set -
5 x 10M ISO 6 Modular Cleanroom
US$18000-56000 USD/Set
Min. Order:1 Set -
5 x 8M ISO 6 Modular Cleanroom
US$18000-56000 USD/Set
Min. Order:1 Set
Cleanrooms Detail
A 3 x 3 meter ISO Class 6 modular cleanroom is a controlled environment designed to meet the stringent air cleanliness requirements of ISO 14644-1 standards. It’s a compact, customizable solution for industries that require a high level of contamination control, such as pharmaceuticals, biotechnology, electronics, or precision manufacturing. Let’s break down what this means and why it’s useful.
Cleanroom Project Scope(from structure, HVAC,electric to autoc ontrol) | 1. Cleanroom Structure: Wall Panel, Ceiling Panel, Windows, Doors, Fttings, Flooring |
2. HVAC: AHU, Chiller, dehumidifier, Ducting, Piping, etc. | |
3. Electric: Lighting, Switch, Cables, Wires, Power Distribution Cabinet, etc | |
4. Auto- control: PLC Controller, Sensors for Humidity and Temperature, Control Panel | |
5. Process Piping System: Gas, Water Pipeline | |
Equipment | Air shower, Cargo shower, Mist shower, Dynamic pass box, Static pass box, Sampling booth,Weighing booth, Dispensing booth, |
Medicine stability test chamber, isolator, VHP sterilizer,Biological safety chamber, FFU, LAF, etc. | |
Temperature | 21-27*C (or as per required) |
Humidity | 30-60°C (or as per required) |
Application | Pharmaceutical factory, hospital, medical device factory, electronics factory, food factory,cosmetics factory, etc. |
Qualification Documents | CE GMP ISO |
Full Service | FAT and SAT Service, Professional Consultation, Training, 24 hours technical support |
Applications
A cleanroom of this size and classification is ideal for small-scale operations that require a controlled environment. Common uses include:
Pharmaceuticals: Sterile drug formulation or packaging.
Biotechnology: Cell culture or microbiological work.
Electronics: Assembly of sensitive components like microchips.
Medical Devices: Manufacturing or testing of sterile devices.
Research Labs: Small-scale experiments requiring contamination control.
Advantages of a Modular Cleanroom
Flexibility: Modular cleanrooms can be easily expanded, relocated, or reconfigured to meet changing needs.
Cost-Effective: Smaller size reduces construction and operational costs compared to larger cleanrooms.
Quick Installation: Prefabricated panels and components allow for faster setup compared to traditional cleanrooms.
Compliance: Designed to meet ISO 14644-1 standards, ensuring regulatory compliance for industries like pharmaceuticals and electronics.
Cleanrooms Airflow
When designing the airflow system for an ISO 6 modular cleanroom, several factors must be considered:
Air Changes Per Hour (ACH):
ISO Class 6 cleanrooms typically require 70-160 air changes per hour to maintain cleanliness.
The exact number depends on the cleanroom’s size, usage, and contamination sources.
Cleanrooms Installation
Cleanrooms Testing
Importance of testing
Clean room testing is extremely important to ensure product quality and the stability of the production environment. It can help to confirm whether the clean room meets the intended cleanliness requirements, and whether the various environmental indicators comply with the specified standards.
Testing Standards
ISO 6 Modular Cleanroom Testing Standards are guided by ISO 14644-1 and related protocols to ensure compliance and performance. Key standards include:
Particle Count Testing: Verifies airborne particle levels (≤35,200 particles ≥0.5 µm/m³).
Airflow Velocity Testing: Ensures proper airflow speed and uniformity.
Filter Integrity Testing: Detects HEPA/ULPA filter leaks using DOP/PAO aerosols.
Pressure Differential Testing: Maintains positive pressure to prevent contamination.
Air Changes Per Hour (ACH): Confirms sufficient air replacement (70-160 ACH).
Recovery Testing: Measures contamination recovery time.
Environmental Monitoring: Tracks temperature, humidity, lighting, and noise levels.
These standards ensure the cleanroom meets ISO Class 6 requirements for controlled environments.
FAQ
What is the cost-benefit analysis of modular cleanrooms?
The cost-benefit analysis of modular cleanrooms shows significant savings over time. Initial costs are offset by reduced construction time and operational flexibility.
What is the cost of building a modular cleanroom?
The cost of building a modular cleanroom generally ranges from $200 to $400 per square foot. This varies based on design complexity and materials used.
Additional costs may arise from specialized equipment and compliance requirements.
How does the mobility of modular cleanrooms affect their design?
Mobility necessitates a design that allows for easy assembly and relocation. Components must be lightweight and modular to facilitate quick adjustments.
This flexibility ensures that cleanrooms can adapt to changing operational needs efficiently.
How is the cleanliness level tested in ISO 6 cleanrooms?
Cleanliness in ISO 6 cleanrooms is tested using particle counters. These devices measure the concentration of airborne particles to verify compliance.
Regular monitoring ensures that cleanliness standards are consistently met.
What is the impact of modular cleanroom design on operational efficiency?
Modular cleanroom design enhances operational efficiency by allowing quick assembly and customization. This reduces downtime and optimizes workflows.
The flexibility of design also accommodates changes in production needs, improving overall productivity.
What are the latest technologies in cleanroom design?
Latest technologies in cleanroom design include:
- Advanced filtration systems for better air quality.
- Real-time monitoring sensors for environmental control.
- Modular construction techniques for rapid deployment.
These innovations enhance cleanliness and operational effectiveness.
What are the challenges of maintaining ISO 6 cleanliness?
Challenges in maintaining ISO 6 cleanliness include:
- Ensuring strict personnel protocols to prevent contamination.
- Regular validation of cleaning processes and equipment.
- Monitoring environmental conditions like temperature and humidity.
Adhering to these challenges is vital for maintaining compliance.
What technologies are used for cleanroom monitoring?
Technologies used for cleanroom monitoring include:
- Particle counters to assess airborne contaminants.
- Temperature and humidity sensors for climate control.
- Pressure monitors to maintain airflow balance.
These technologies are essential for ensuring a controlled environment.
How to handle waste in a modular cleanroom?
Waste handling in a modular cleanroom should follow strict protocols. Waste should be segregated into hazardous and non-hazardous categories.
Use designated containers and ensure proper disposal procedures to maintain cleanliness.
What is the difference between ISO 6 and ISO 7 cleanrooms?
ISO 6 cleanrooms have stricter particle limits than ISO 7. ISO 6 permits fewer than 1,000 particles per cubic meter, while ISO 7 allows up to 10,000.
This distinction impacts suitability for different applications and industries.
How to manage supply chain logistics for cleanroom materials?
Managing supply chain logistics for cleanroom materials requires careful planning. Establish reliable supplier relationships to ensure timely delivery.
Implement inventory management systems to track materials and maintain compliance with standards.
What criteria should be used to select modular cleanroom suppliers?
Key criteria for selecting modular cleanroom suppliers include:
- Proven experience in cleanroom construction.
- Quality of materials and components used.
- Comprehensive customer support and service options.
These factors ensure a successful partnership for cleanroom projects.
What is the installation timeline for a modular cleanroom?
The installation timeline for a modular cleanroom typically ranges from a few weeks to several months. Factors affecting this include size, complexity, and customization requirements.
Effective planning and coordination with suppliers can help expedite the process.
How to select appropriate cleanroom furniture?
Selecting cleanroom furniture requires consideration of material compatibility and ease of cleaning. Non-porous materials are ideal to minimize contamination risks.
Furniture should also be ergonomically designed to support efficient workflows in the cleanroom environment.
What equipment is used in ISO 6 cleanrooms?
Equipment commonly used in ISO 6 cleanrooms includes:
- HEPA filters to maintain air quality.
- Laminar flow hoods for sterile work conditions.
- Airlocks and pass-throughs to reduce contamination risk.
These tools are essential for achieving and maintaining strict cleanliness standards.
What products are suitable for production in ISO 6 cleanrooms?
Products suitable for production in ISO 6 cleanrooms include:
- Pharmaceuticals requiring sterile environments.
- Medical devices that need contamination control.
- Electronics sensitive to particulates.
These items benefit from the high cleanliness standards enforced in ISO 6 facilities.
How to monitor particle counts in an ISO 6 cleanroom?
To monitor particle counts in an ISO 6 cleanroom, use calibrated particle counters. These devices measure airborne particles at specified intervals.
Regular assessments ensure ongoing compliance with cleanliness standards and help identify potential issues.
Factory Production Workshop Video
Factory Photo
Product Packaging And International Logistics
Product International Certification
Find Other Common Equipment Recommendations
-
Modular CleanRoom
US$9000-10000 USD/Unit
Min. Order:1 Set -
Air Shower
US$1000.00-5000.00 USD/Unit
Min. Order:1 Set -
Downflow Booth
US$3000-6000 USD/Unit
Min. Order:1 Set -
Clean bench
US$600-2000 USD/Unit
Min. Order:1 Set -
Air Filter
US$3-50 USD/Unit
Min. Order:1 Set -
Cleanroom Wall Panels
US$10-20 USD/sq.
Min. Order:1 Set -
Pass Box
US$200-500 USD/Unit
Min. Order:1 Set -
FFU
US$135-350 USD/Unit
Min. Order:1 Set -
Fume Hood
US$700-1500 USD/Unit
Min. Order:1 Set -
Cleanroom HVAC
US$5000-20000 USD/Unit
Min. Order:1 Set -
Clean room floor
US$5-20 USD/Sq.
Min. Order:1 Set -
Clean room ceiling
US$
Min. Order:1 Set