5 x 8M ISO 6 Modular Cleanroom
Reference Price:US$13300-18000
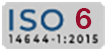


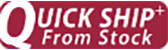
Cleanroom
5 x 8M ISO 6 Modular Cleanroom
Choose your installation & validation options below
Quantity:
Choose your Cleanroom frame structure material
Quantity:
Choose your Cleanroom Wall enclosure materials
Quantity:
Choose your Temperature requirements
Quantity:
Choose your humidity requirements
Quantity:
Choose your Explosion-proof requirements
Quantity:
Summary
5 x 8M ISO 6 Modular Cleanroom
Validation
Installation & Validation
Find Similar Products
-
5 x 15M ISO 6 Modular Cleanroom
US$18000-56000 USD/Set
Min. Order:1 Set -
6 x 10M ISO 6 Modular Cleanroom
US$18000-56000 USD/Set
Min. Order:1 Set -
6 x 8M ISO 6 Modular Cleanroom
US$18000-56000 USD/Set
Min. Order:1 Set -
6 x 6M ISO 6 Modular Cleanroom
US$18000-56000 USD/Set
Min. Order:1 Set -
5 x 10M ISO 6 Modular Cleanroom
US$18000-56000 USD/Set
Min. Order:1 Set -
5 x 8M ISO 6 Modular Cleanroom
US$18000-56000 USD/Set
Min. Order:1 Set
Cleanrooms Detail
A 3 x 3 meter ISO Class 6 modular cleanroom is a controlled environment designed to meet the stringent air cleanliness requirements of ISO 14644-1 standards. It’s a compact, customizable solution for industries that require a high level of contamination control, such as pharmaceuticals, biotechnology, electronics, or precision manufacturing. Let’s break down what this means and why it’s useful.
Cleanroom Project Scope(from structure, HVAC,electric to autoc ontrol) | 1. Cleanroom Structure: Wall Panel, Ceiling Panel, Windows, Doors, Fttings, Flooring |
2. HVAC: AHU, Chiller, dehumidifier, Ducting, Piping, etc. | |
3. Electric: Lighting, Switch, Cables, Wires, Power Distribution Cabinet, etc | |
4. Auto- control: PLC Controller, Sensors for Humidity and Temperature, Control Panel | |
5. Process Piping System: Gas, Water Pipeline | |
Equipment | Air shower, Cargo shower, Mist shower, Dynamic pass box, Static pass box, Sampling booth,Weighing booth, Dispensing booth, |
Medicine stability test chamber, isolator, VHP sterilizer,Biological safety chamber, FFU, LAF, etc. | |
Temperature | 21-27*C (or as per required) |
Humidity | 30-60°C (or as per required) |
Application | Pharmaceutical factory, hospital, medical device factory, electronics factory, food factory,cosmetics factory, etc. |
Qualification Documents | CE GMP ISO |
Full Service | FAT and SAT Service, Professional Consultation, Training, 24 hours technical support |
Applications
A cleanroom of this size and classification is ideal for small-scale operations that require a controlled environment. Common uses include:
Pharmaceuticals: Sterile drug formulation or packaging.
Biotechnology: Cell culture or microbiological work.
Electronics: Assembly of sensitive components like microchips.
Medical Devices: Manufacturing or testing of sterile devices.
Research Labs: Small-scale experiments requiring contamination control.
Advantages of a Modular Cleanroom
Flexibility: Modular cleanrooms can be easily expanded, relocated, or reconfigured to meet changing needs.
Cost-Effective: Smaller size reduces construction and operational costs compared to larger cleanrooms.
Quick Installation: Prefabricated panels and components allow for faster setup compared to traditional cleanrooms.
Compliance: Designed to meet ISO 14644-1 standards, ensuring regulatory compliance for industries like pharmaceuticals and electronics.
Cleanrooms Airflow
When designing the airflow system for an ISO 6 modular cleanroom, several factors must be considered:
Air Changes Per Hour (ACH):
ISO Class 6 cleanrooms typically require 70-160 air changes per hour to maintain cleanliness.
The exact number depends on the cleanroom’s size, usage, and contamination sources.
Cleanrooms Installation
Cleanrooms Testing
Importance of testing
Clean room testing is extremely important to ensure product quality and the stability of the production environment. It can help to confirm whether the clean room meets the intended cleanliness requirements, and whether the various environmental indicators comply with the specified standards.
Testing Standards
ISO 6 Modular Cleanroom Testing Standards are guided by ISO 14644-1 and related protocols to ensure compliance and performance. Key standards include:
Particle Count Testing: Verifies airborne particle levels (≤35,200 particles ≥0.5 µm/m³).
Airflow Velocity Testing: Ensures proper airflow speed and uniformity.
Filter Integrity Testing: Detects HEPA/ULPA filter leaks using DOP/PAO aerosols.
Pressure Differential Testing: Maintains positive pressure to prevent contamination.
Air Changes Per Hour (ACH): Confirms sufficient air replacement (70-160 ACH).
Recovery Testing: Measures contamination recovery time.
Environmental Monitoring: Tracks temperature, humidity, lighting, and noise levels.
These standards ensure the cleanroom meets ISO Class 6 requirements for controlled environments.
FAQ
What equipment is used in ISO 6 cleanrooms?
ISO 6 cleanrooms require specialized equipment to maintain air cleanliness. Common items include HEPA filters, airlocks, and pass-through chambers.
Additionally, laminar flow hoods and gowning benches are essential for minimizing contamination risks.
What wall and floor materials are recommended for ISO 6 cleanrooms?
For ISO 6 cleanrooms, non-porous, smooth surfaces are critical to prevent contamination. Recommended wall materials include epoxy-coated panels and stainless steel.
Flooring should consist of seamless vinyl or epoxy materials, which are easy to clean and resistant to chemicals.
These materials help maintain the required cleanliness level and withstand frequent cleaning procedures.
How to perform a cleanroom risk assessment?
Performing a cleanroom risk assessment involves several key steps. First, identify potential contamination sources, such as personnel and equipment.
Next, evaluate the likelihood and impact of each risk, prioritizing them based on severity.
Finally, implement mitigation strategies, such as enhanced cleaning protocols or additional barriers, to minimize risks effectively.
What are the best practices for cleanroom maintenance?
Best practices for cleanroom maintenance include regular cleaning and monitoring of air quality. Schedule frequent inspections to identify potential issues.
Implement a detailed cleaning protocol that specifies approved cleaning agents and techniques.
Train staff on proper maintenance procedures and ensure they follow strict gowning protocols.
Additionally, maintain equipment and perform routine validations to ensure compliance with ISO standards.
How to ensure ergonomic considerations in cleanroom design?
To ensure ergonomic considerations in cleanroom design, assess the tasks performed by personnel. Design workstations to minimize strain and enhance comfort.
Incorporate adjustable equipment and tools to accommodate various user needs.
Consider the layout of the cleanroom, ensuring that pathways are clear for easy movement.
Finally, provide training on proper lifting techniques and ergonomic practices to promote safety.
What is the role of an HVAC system in a modular cleanroom?
An HVAC system is crucial for maintaining air quality in a modular cleanroom. It regulates temperature, humidity, and airflow to meet ISO standards.
Through filtration, it removes airborne contaminants, ensuring a sterile environment.
Additionally, the HVAC system controls pressure differentials to prevent cross-contamination between areas.
Regular maintenance of the HVAC system is essential to ensure optimal performance and compliance.
How to integrate automation into a modular cleanroom?
Integrating automation into a modular cleanroom enhances efficiency and compliance. Start by identifying repetitive tasks suitable for automation, such as material handling.
Utilize automated guided vehicles (AGVs) for transport and robotic systems for assembly.
Implement sensor technologies for real-time monitoring of environmental conditions and process control.
Train staff on automated systems to ensure smooth operation and maintenance.
In which industries are ISO 6 cleanrooms used?
ISO 6 cleanrooms are utilized in various industries, including:
- Pharmaceuticals: For drug development and manufacturing.
- Biotechnology: In research and production environments.
- Medical Devices: Ensuring sterility during manufacturing.
- Electronics: Protecting sensitive components from contamination.
These industries require stringent cleanliness standards to ensure product quality and compliance.
What is the role of cleanroom apparel in contamination control?
Cleanroom apparel plays a vital role in preventing contamination. It acts as a barrier between personnel and the cleanroom environment.
Properly designed garments cover skin and hair, minimizing particulate release.
Additionally, apparel must be made from non-fibrous materials to avoid contaminant generation.
Regular inspection and replacement of cleanroom apparel are essential to maintain effectiveness.
What technologies are used for cleanroom monitoring?
Cleanroom monitoring technologies include:
- Particle counters: To measure airborne contaminants.
- Temperature and humidity sensors: For environmental control.
- Pressure differential monitors: To ensure proper airflow.
- Data loggers: For tracking conditions over time.
These technologies help maintain compliance with cleanroom standards and ensure product integrity.
What materials are used in modular cleanroom construction?
Modular cleanrooms typically use materials such as:
- Pre-fabricated panels: For walls and ceilings, offering flexibility.
- Stainless steel: For durability and easy cleaning.
- Vinyl flooring: To provide a seamless and hygienic surface.
- Specialized insulation: To maintain temperature control.
These materials facilitate rapid assembly and compliance with cleanroom standards.
How to manage personnel flow in modular cleanrooms?
Managing personnel flow in modular cleanrooms requires careful planning of movement patterns. Designate specific entry and exit points to control access.
Implement a gowning area for proper apparel donning to minimize contamination risks.
Use signage to guide personnel and establish protocols for movement during operations.
Regular training on these protocols helps ensure compliance and efficiency.
What are the advantages of modular cleanrooms?
Modular cleanrooms offer several advantages, including:
- Flexibility:- Flexibility: Modular designs allow for easy expansion or reconfiguration based on changing needs.
- Cost-effectiveness: They can be constructed faster and often at lower costs compared to traditional cleanrooms.
- Quick installation: Modular cleanrooms can be assembled and validated in a shorter timeframe.
- Ease of maintenance: Their design facilitates straightforward maintenance and upgrades without major disruptions.
What are the key performance indicators for cleanroom operations?
Key performance indicators (KPIs) for cleanroom operations include:
- Particle count: To assess air cleanliness levels.
- Temperature and humidity control: To ensure optimal conditions for processes.
- Equipment uptime: Monitoring the reliability of critical systems.
- Cleaning validation results: To confirm the effectiveness of cleaning protocols.
These KPIs help maintain compliance and improve overall cleanroom performance.
What are common contaminants in ISO 6 cleanrooms?
Common contaminants in ISO 6 cleanrooms include:
- Particulate matter: Dust and fibers from clothing or equipment.
- Microorganisms: Bacteria, fungi, and viruses that can compromise sterility.
- Chemical residues: From cleaning agents or materials used in the cleanroom.
- Volatile organic compounds (VOCs): Emitted by some materials or equipment.
Regular monitoring and effective cleaning protocols are essential to mitigate these risks.
How often should cleanroom validation be performed?
Cleanroom validation should be performed at regular intervals to ensure compliance. Typically, it is recommended every six to twelve months.
Additionally, validation should occur after significant changes, such as renovations or equipment upgrades.
Regular audits and performance checks help maintain the integrity of cleanroom operations.
Documentation of validation results is crucial for regulatory compliance and quality assurance.
Factory Production Workshop Video
Factory Photo
Product Packaging And International Logistics
Product International Certification
Find Other Common Equipment Recommendations
-
Modular CleanRoom
US$9000-10000 USD/Unit
Min. Order:1 Set -
Air Shower
US$1000.00-5000.00 USD/Unit
Min. Order:1 Set -
Downflow Booth
US$3000-6000 USD/Unit
Min. Order:1 Set -
Clean bench
US$600-2000 USD/Unit
Min. Order:1 Set -
Air Filter
US$3-50 USD/Unit
Min. Order:1 Set -
Cleanroom Wall Panels
US$10-20 USD/sq.
Min. Order:1 Set -
Pass Box
US$200-500 USD/Unit
Min. Order:1 Set -
FFU
US$135-350 USD/Unit
Min. Order:1 Set -
Fume Hood
US$700-1500 USD/Unit
Min. Order:1 Set -
Cleanroom HVAC
US$5000-20000 USD/Unit
Min. Order:1 Set -
Clean room floor
US$5-20 USD/Sq.
Min. Order:1 Set -
Clean room ceiling
US$
Min. Order:1 Set