5 x 6M ISO 6 Modular Cleanroom
Reference Price:US$11600
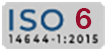


Cleanroom
5 x 6M ISO 6 Modular Cleanroom
Choose your installation & validation options below
Quantity:
Choose your Cleanroom frame structure material
Quantity:
Choose your Cleanroom Wall enclosure materials
Quantity:
Choose your Temperature requirements
Quantity:
Choose your humidity requirements
Quantity:
Choose your Explosion-proof requirements
Quantity:
Summary
5 x 6M ISO 6 Modular Cleanroom
Validation
Installation & Validation
Find Similar Products
-
5 x 15M ISO 6 Modular Cleanroom
US$18000-56000 USD/Set
Min. Order:1 Set -
6 x 10M ISO 6 Modular Cleanroom
US$18000-56000 USD/Set
Min. Order:1 Set -
6 x 8M ISO 6 Modular Cleanroom
US$18000-56000 USD/Set
Min. Order:1 Set -
6 x 6M ISO 6 Modular Cleanroom
US$18000-56000 USD/Set
Min. Order:1 Set -
5 x 10M ISO 6 Modular Cleanroom
US$18000-56000 USD/Set
Min. Order:1 Set -
5 x 8M ISO 6 Modular Cleanroom
US$18000-56000 USD/Set
Min. Order:1 Set
Cleanrooms Detail
A 3 x 3 meter ISO Class 6 modular cleanroom is a controlled environment designed to meet the stringent air cleanliness requirements of ISO 14644-1 standards. It’s a compact, customizable solution for industries that require a high level of contamination control, such as pharmaceuticals, biotechnology, electronics, or precision manufacturing. Let’s break down what this means and why it’s useful.
Cleanroom Project Scope(from structure, HVAC,electric to autoc ontrol) | 1. Cleanroom Structure: Wall Panel, Ceiling Panel, Windows, Doors, Fttings, Flooring |
2. HVAC: AHU, Chiller, dehumidifier, Ducting, Piping, etc. | |
3. Electric: Lighting, Switch, Cables, Wires, Power Distribution Cabinet, etc | |
4. Auto- control: PLC Controller, Sensors for Humidity and Temperature, Control Panel | |
5. Process Piping System: Gas, Water Pipeline | |
Equipment | Air shower, Cargo shower, Mist shower, Dynamic pass box, Static pass box, Sampling booth,Weighing booth, Dispensing booth, |
Medicine stability test chamber, isolator, VHP sterilizer,Biological safety chamber, FFU, LAF, etc. | |
Temperature | 21-27*C (or as per required) |
Humidity | 30-60°C (or as per required) |
Application | Pharmaceutical factory, hospital, medical device factory, electronics factory, food factory,cosmetics factory, etc. |
Qualification Documents | CE GMP ISO |
Full Service | FAT and SAT Service, Professional Consultation, Training, 24 hours technical support |
Applications
A cleanroom of this size and classification is ideal for small-scale operations that require a controlled environment. Common uses include:
Pharmaceuticals: Sterile drug formulation or packaging.
Biotechnology: Cell culture or microbiological work.
Electronics: Assembly of sensitive components like microchips.
Medical Devices: Manufacturing or testing of sterile devices.
Research Labs: Small-scale experiments requiring contamination control.
Advantages of a Modular Cleanroom
Flexibility: Modular cleanrooms can be easily expanded, relocated, or reconfigured to meet changing needs.
Cost-Effective: Smaller size reduces construction and operational costs compared to larger cleanrooms.
Quick Installation: Prefabricated panels and components allow for faster setup compared to traditional cleanrooms.
Compliance: Designed to meet ISO 14644-1 standards, ensuring regulatory compliance for industries like pharmaceuticals and electronics.
Cleanrooms Airflow
When designing the airflow system for an ISO 6 modular cleanroom, several factors must be considered:
Air Changes Per Hour (ACH):
ISO Class 6 cleanrooms typically require 70-160 air changes per hour to maintain cleanliness.
The exact number depends on the cleanroom’s size, usage, and contamination sources.
Cleanrooms Installation
Cleanrooms Testing
Importance of testing
Clean room testing is extremely important to ensure product quality and the stability of the production environment. It can help to confirm whether the clean room meets the intended cleanliness requirements, and whether the various environmental indicators comply with the specified standards.
Testing Standards
ISO 6 Modular Cleanroom Testing Standards are guided by ISO 14644-1 and related protocols to ensure compliance and performance. Key standards include:
Particle Count Testing: Verifies airborne particle levels (≤35,200 particles ≥0.5 µm/m³).
Airflow Velocity Testing: Ensures proper airflow speed and uniformity.
Filter Integrity Testing: Detects HEPA/ULPA filter leaks using DOP/PAO aerosols.
Pressure Differential Testing: Maintains positive pressure to prevent contamination.
Air Changes Per Hour (ACH): Confirms sufficient air replacement (70-160 ACH).
Recovery Testing: Measures contamination recovery time.
Environmental Monitoring: Tracks temperature, humidity, lighting, and noise levels.
These standards ensure the cleanroom meets ISO Class 6 requirements for controlled environments.
FAQ
What is the difference between modular and traditional cleanroom construction?
Modular cleanroom construction involves prefabricated components that are assembled on-site, allowing for flexibility and quicker installation. Traditional cleanrooms, however, are built using conventional construction methods, which can be time-consuming and less adaptable.
Additionally, modular cleanrooms can be easily reconfigured or expanded based on changing needs. In contrast, traditional cleanrooms require more extensive renovations for modifications, which can disrupt ongoing operations.
Overall, the choice between modular and traditional designs depends on specific operational requirements, budget constraints, and future scalability considerations.
How to perform daily checks on a modular cleanroom?
Daily checks on a modular cleanroom should begin with visual inspections for any signs of damage or contamination. Inspect the walls, floors, and ceilings for dust or debris accumulation.
Next, verify that all airflow systems, including HEPA filters, are functioning correctly. This ensures that the cleanroom maintains its specified air quality standards essential for a controlled environment.
Finally, document all findings in a log for accountability and trend analysis. Regular monitoring helps ensure compliance and allows for timely maintenance interventions.
How often should cleanroom validation be performed?
Cleanroom validation should be performed at least annually to ensure compliance with regulatory standards. Additionally, validation should occur after any significant changes, such as renovations or equipment upgrades.
Other circumstances warranting validation include introducing new processes or materials that may affect air quality. Regular assessments ensure that the cleanroom continues to meet the required cleanliness levels.
Validation also helps identify potential issues early, allowing for corrective actions before they escalate. This proactive approach supports operational efficiency and product quality.
How to ensure a dust-free environment in a modular cleanroom?
To maintain a dust-free environment in a modular cleanroom, implement strict gowning procedures for personnel. Ensure everyone wears appropriate PPE to minimize contamination risks from clothing and skin.
Regularly scheduled cleaning routines should include using approved cleaning agents and techniques to remove any particulate matter. High-efficiency particulate air (HEPA) filters must be maintained to ensure optimal air filtration.
Also, control access to the cleanroom by using airlocks and restricted entry. Monitoring air quality with particle counters further ensures the environment remains dust-free, promoting compliance with cleanliness standards.
What is the impact of modular cleanroom design on operational efficiency?
Modular cleanroom design significantly enhances operational efficiency by allowing for rapid installation and adaptability. This flexibility enables companies to respond quickly to changing production needs without extensive downtime.
Moreover, the ability to scale a modular cleanroom up or down can optimize space usage and reduce overhead costs. Companies can also relocate cleanrooms as required, providing a strategic advantage in dynamic markets.
Additionally, modular designs often incorporate advanced technologies that improve workflow and minimize contamination risks. This streamlined approach can lead to better product quality and increased productivity.
What factors influence the cost of modular cleanroom construction?
Several factors influence the cost of modular cleanroom construction, including:
- Size and Complexity: Larger and more complex cleanrooms require more materials and labor.
- Material Choices: High-quality materials can enhance durability but increase costs.
- Customization: Tailored designs for specific needs can add to expenses.
- Location: Construction costs can vary significantly based on geographic location.
- Regulatory Compliance: Meeting industry standards may necessitate additional investments.
Understanding these factors is crucial for accurate budgeting and planning.
What are common contaminants in ISO 6 cleanrooms?
Common contaminants in ISO 6 cleanrooms include:
- Particulate Matter: Dust, lint, and other particles.
- Microorganisms: Bacteria, fungi, and viruses.
- Chemical Vapors: Residual solvents and volatile compounds.
- Moisture: Humidity can lead to microbial growth and equipment malfunction.
Managing these contaminants is essential to maintain strict cleanliness standards and ensure product integrity in sensitive environments.
What are the benefits of using a modular cleanroom?
Using a modular cleanroom offers numerous benefits, including:
- Flexibility: Easily reconfigure or expand the cleanroom as needs change.
- Speed of Construction: Quick installation reduces downtime, allowing for faster operational readiness.
- Cost-Effectiveness: Lower initial investment and reduced ongoing costs due to efficient design.
- Quality Control: Advanced technologies improve air filtration and contamination control.
These advantages make modular cleanrooms increasingly popular in various industries such as pharmaceuticals and biotechnology.
How to assess the energy efficiency of a cleanroom?
To assess the energy efficiency of a cleanroom, begin by evaluating HVAC systems and their energy consumption. Analyze airflow patterns and filter performance to ensure optimal operation.
Conduct an energy audit to identify areas where energy waste occurs, such as leaks or inefficient equipment. Implementing sensors can help monitor real-time energy use, providing valuable data for analysis.
Additionally, compareenergy usage against industry benchmarks to determine performance. This comprehensive assessment can guide improvements and investments in energy-efficient technologies, ultimately reducing operational costs and environmental impact.
What is the cost-benefit analysis of modular cleanrooms?
A cost-benefit analysis of modular cleanrooms involves evaluating both initial investment and long-term savings. Key costs include materials, installation, and compliance with regulatory standards.
On the benefits side, consider factors like reduced construction time, flexibility for future expansions, and lower operational costs due to efficient designs. These advantages can lead to a quicker return on investment.
Additionally, improved operational efficiency and reduced downtime contribute to enhanced productivity. Analyzing these elements helps decision-makers weigh the financial implications and strategic value of modular cleanroom solutions.
How to certify a modular cleanroom?
To certify a modular cleanroom, first ensure it meets all relevant industry standards and regulatory requirements. Engage an accredited certification body to perform the evaluation.
Conduct thorough testing, including airflow validation, particulate counts, and microbiological assessments. These tests confirm compliance with the desired cleanroom class standards, such as ISO 6.
Once testing is complete, compile documentation detailing compliance results and operational procedures. This documentation is essential for maintaining certification and demonstrating adherence to industry standards.
What are the design specifications for ISO 6 cleanrooms?
Design specifications for ISO 6 cleanrooms include:
- Air Quality: Maximum allowable particle count of 1,000 particles per cubic meter for particles ≥ 0.5 micrometers.
- Air Changes: Minimum air change rate of 10-20 air changes per hour to ensure optimal ventilation.
- Temperature and Humidity: Control systems must maintain stable temperature (20-25°C) and relative humidity (45-55%).
- Surface Materials: Non-porous, smooth surfaces are essential for easy cleaning and contamination control.
Following these specifications ensures compliance with ISO 6 standards, facilitating a controlled environment for sensitive operations.
How to conduct a risk assessment for a modular cleanroom?
To conduct a risk assessment for a modular cleanroom, start by identifying potential hazards, including contamination sources, equipment failures, and human error. Engage stakeholders to gather insights on risks specific to operations.
Next, evaluate the likelihood and impact of each identified risk. Use a risk matrix to categorize risks based on their severity and probability of occurrence.
Finally, develop mitigation strategies for high-priority risks, including standard operating procedures, training programs, and regular maintenance schedules. Document all findings and strategies to ensure ongoing compliance and operational safety.
How to ensure compliance with ISO 6 standards?
Ensuring compliance with ISO 6 standards involves several key steps:
- Regular Training: Provide ongoing training for staff on cleanroom protocols and contamination control.
- Standard Operating Procedures: Develop and maintain SOPs that align with ISO 6 requirements.
- Monitoring Systems: Implement continuous monitoring systems for air quality, temperature, and humidity.
- Routine Audits: Conduct regular internal audits to assess compliance and identify areas for improvement.
By following these steps, organizations can effectively maintain ISO 6 compliance and safeguard product integrity.
What is the cleaning procedure for modular cleanrooms?
The cleaning procedure for modular cleanrooms consists of several steps:
- Preparation: Remove unnecessary items and ensure PPE is worn by cleaning personnel.
- Dusting: Use lint-free wipes and appropriate cleaning agents to dust surfaces from top to bottom.
- Wet Cleaning: Apply approved disinfectants to all surfaces, ensuring thorough coverage and contact time for effective sanitation.
- Floor Maintenance: Use a microfiber mop with suitable cleaning agents for floors, ensuring they remain free from contaminants.
Following this structured cleaning procedure helps maintain a controlled environment and reduces contamination risks.
What are the best practices for cleanroom gowning procedures?
Best practices for cleanroom gowning procedures include:
- Pre-Gowning Area: Establish a designated area for personnel to don gowns, minimizing contamination risks.
- Layering: Ensure multiple layers of garments, including coveralls, hoods, gloves, and shoe covers to protect against contamination.
- Proper Technique: Train staff on correct gowning techniques to avoid touching external surfaces of garments.
- Regular Inspections: Conduct checks to ensure compliance with gowning protocols and replace any damaged garments promptly.
Implementing these best practices ensures personnel minimize contamination when entering the cleanroom.
Factory Production Workshop Video
Factory Photo
Product Packaging And International Logistics
Product International Certification
Find Other Common Equipment Recommendations
-
Modular CleanRoom
US$9000-10000 USD/Unit
Min. Order:1 Set -
Air Shower
US$1000.00-5000.00 USD/Unit
Min. Order:1 Set -
Downflow Booth
US$3000-6000 USD/Unit
Min. Order:1 Set -
Clean bench
US$600-2000 USD/Unit
Min. Order:1 Set -
Air Filter
US$3-50 USD/Unit
Min. Order:1 Set -
Cleanroom Wall Panels
US$10-20 USD/sq.
Min. Order:1 Set -
Pass Box
US$200-500 USD/Unit
Min. Order:1 Set -
FFU
US$135-350 USD/Unit
Min. Order:1 Set -
Fume Hood
US$700-1500 USD/Unit
Min. Order:1 Set -
Cleanroom HVAC
US$5000-20000 USD/Unit
Min. Order:1 Set -
Clean room floor
US$5-20 USD/Sq.
Min. Order:1 Set -
Clean room ceiling
US$
Min. Order:1 Set