5 x 5M ISO 6 Modular Cleanroom
Reference Price:US$10400
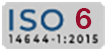

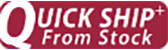
Cleanroom
5 x 5M ISO 6 Modular Cleanroom
Choose your installation & validation options below
Quantity:
Choose your Cleanroom frame structure material
Quantity:
Choose your Cleanroom Wall enclosure materials
Quantity:
Choose your Temperature requirements
Quantity:
Choose your humidity requirements
Quantity:
Choose your Explosion-proof requirements
Quantity:
Summary
5 x 5M ISO 6 Modular Cleanroom
Validation
Installation & Validation
Find Similar Products
-
5 x 15M ISO 6 Modular Cleanroom
US$18000-56000 USD/Set
Min. Order:1 Set -
6 x 10M ISO 6 Modular Cleanroom
US$18000-56000 USD/Set
Min. Order:1 Set -
6 x 8M ISO 6 Modular Cleanroom
US$18000-56000 USD/Set
Min. Order:1 Set -
6 x 6M ISO 6 Modular Cleanroom
US$18000-56000 USD/Set
Min. Order:1 Set -
5 x 10M ISO 6 Modular Cleanroom
US$18000-56000 USD/Set
Min. Order:1 Set -
5 x 8M ISO 6 Modular Cleanroom
US$18000-56000 USD/Set
Min. Order:1 Set
Cleanrooms Detail
A 3 x 3 meter ISO Class 6 modular cleanroom is a controlled environment designed to meet the stringent air cleanliness requirements of ISO 14644-1 standards. It’s a compact, customizable solution for industries that require a high level of contamination control, such as pharmaceuticals, biotechnology, electronics, or precision manufacturing. Let’s break down what this means and why it’s useful.
Cleanroom Project Scope(from structure, HVAC,electric to autoc ontrol) | 1. Cleanroom Structure: Wall Panel, Ceiling Panel, Windows, Doors, Fttings, Flooring |
2. HVAC: AHU, Chiller, dehumidifier, Ducting, Piping, etc. | |
3. Electric: Lighting, Switch, Cables, Wires, Power Distribution Cabinet, etc | |
4. Auto- control: PLC Controller, Sensors for Humidity and Temperature, Control Panel | |
5. Process Piping System: Gas, Water Pipeline | |
Equipment | Air shower, Cargo shower, Mist shower, Dynamic pass box, Static pass box, Sampling booth,Weighing booth, Dispensing booth, |
Medicine stability test chamber, isolator, VHP sterilizer,Biological safety chamber, FFU, LAF, etc. | |
Temperature | 21-27*C (or as per required) |
Humidity | 30-60°C (or as per required) |
Application | Pharmaceutical factory, hospital, medical device factory, electronics factory, food factory,cosmetics factory, etc. |
Qualification Documents | CE GMP ISO |
Full Service | FAT and SAT Service, Professional Consultation, Training, 24 hours technical support |
Applications
A cleanroom of this size and classification is ideal for small-scale operations that require a controlled environment. Common uses include:
Pharmaceuticals: Sterile drug formulation or packaging.
Biotechnology: Cell culture or microbiological work.
Electronics: Assembly of sensitive components like microchips.
Medical Devices: Manufacturing or testing of sterile devices.
Research Labs: Small-scale experiments requiring contamination control.
Advantages of a Modular Cleanroom
Flexibility: Modular cleanrooms can be easily expanded, relocated, or reconfigured to meet changing needs.
Cost-Effective: Smaller size reduces construction and operational costs compared to larger cleanrooms.
Quick Installation: Prefabricated panels and components allow for faster setup compared to traditional cleanrooms.
Compliance: Designed to meet ISO 14644-1 standards, ensuring regulatory compliance for industries like pharmaceuticals and electronics.
Cleanrooms Airflow
When designing the airflow system for an ISO 6 modular cleanroom, several factors must be considered:
Air Changes Per Hour (ACH):
ISO Class 6 cleanrooms typically require 70-160 air changes per hour to maintain cleanliness.
The exact number depends on the cleanroom’s size, usage, and contamination sources.
Cleanrooms Installation
Cleanrooms Testing
Importance of testing
Clean room testing is extremely important to ensure product quality and the stability of the production environment. It can help to confirm whether the clean room meets the intended cleanliness requirements, and whether the various environmental indicators comply with the specified standards.
Testing Standards
ISO 6 Modular Cleanroom Testing Standards are guided by ISO 14644-1 and related protocols to ensure compliance and performance. Key standards include:
Particle Count Testing: Verifies airborne particle levels (≤35,200 particles ≥0.5 µm/m³).
Airflow Velocity Testing: Ensures proper airflow speed and uniformity.
Filter Integrity Testing: Detects HEPA/ULPA filter leaks using DOP/PAO aerosols.
Pressure Differential Testing: Maintains positive pressure to prevent contamination.
Air Changes Per Hour (ACH): Confirms sufficient air replacement (70-160 ACH).
Recovery Testing: Measures contamination recovery time.
Environmental Monitoring: Tracks temperature, humidity, lighting, and noise levels.
These standards ensure the cleanroom meets ISO Class 6 requirements for controlled environments.
FAQ
Can ISO 6 cleanrooms be used in the pharmaceutical industry?
Yes, ISO 6 cleanrooms can be utilized in the pharmaceutical industry. They are suitable for manufacturing processes that require controlled environments to minimize contamination.
These cleanrooms offer a balance between maintaining sterility and operational efficiency. However, the specific application must adhere to industry regulations and standards.
Pharmaceutical companies often employ ISO 6 cleanrooms for formulation, packaging, and some quality control processes, ensuring product integrity.
How does air pressure affect cleanroom performance?
Air pressure plays a critical role in cleanroom performance by controlling airflow and preventing contamination. Positive pressure in cleanrooms helps to keep outside air and particles from entering.
Maintaining the correct air pressure helps ensure that contaminants do not enter the cleanroom environment. It also enhances the effectiveness of filtration systems, which are vital for cleanliness.
Regular monitoring of air pressure is essential for compliance with cleanroom standards. Any fluctuations must be addressed promptly to maintain optimal performance levels.
How does the layout of a modular cleanroom affect workflow?
The layout of a modular cleanroom significantly impacts workflow efficiency and operational effectiveness. A well-designed layout minimizes unnecessary movement and streamlines processes.
Key considerations include:
- Designated areas for different operations
- Clear pathways for personnel and materials
- Proximity of equipment to reduce transport time
Optimized layouts enhance productivity and reduce the risk of contamination. Proper zoning can also facilitate easier maintenance and cleaning protocols, further supporting operational goals.
How does the mobility of modular cleanrooms affect their design?
The mobility of modular cleanrooms influences their design by requiring flexibility and adaptability. Designers must consider how the cleanroom will be relocated or reconfigured as needed.
Key design aspects include:
- Lightweight materials for easy transport
- Modular components that can be easily assembled or disassembled
- Integration of utilities for quick setup
This mobility allows organizations to respond efficiently to changing operational needs, enhancing overall productivity. However, the mobility must not compromise cleanliness and compliance standards.
How effective is soundproofing in modular cleanrooms?
Soundproofing in modular cleanrooms is effective in minimizing noise pollution, which can be critical in sensitive environments. It helps maintain a focused work atmosphere and prevents distractions.
Effective soundproofing materials include:
- Acoustic panels
- Insulated walls
- Specialized flooring
By reducing noise levels, soundproofing also contributes to better communication among staff. Overall, it enhances the working conditions, ensuring that personnel can concentrate on critical tasks without disturbances.
How is temperature control managed in ISO 6 cleanrooms?
Temperature control in ISO 6 cleanrooms is managed through advanced HVAC systems designed for precise regulation. These systems monitor and adjust temperature consistently to maintain optimal conditions.
Factors to consider include:
- Thermostatic controls for stability
- Regular calibration and maintenance
- Continuous monitoring for compliance
Effective temperature control is crucial to ensure product quality and prevent degradation. Maintaining a consistent environment also supports personnel comfort and operational efficiency.
How is the cleanliness level tested in ISO 6 cleanrooms?
Cleanliness levels in ISO 6 cleanrooms are tested using various methods. Common practices include air sampling, surface sampling, and particle counting to assess contamination levels.
Testing methods include:
- Viable air and surface sampling
- Non-viable particle counting
- Monitoring of environmental parameters
Regular testing ensures compliance with cleanliness standards and helps identify areas needing improvement. This proactive approach supports ongoing quality assurance in critical environments.
How is the ventilation system designed for a modular cleanroom?
The ventilation system in a modular cleanroom is designed to provide efficient air circulation and filtration. It typically includes HEPA or ULPA filters to remove contaminants from the air.
Key design features involve:
- Sufficient air changes per hour (ACH)
- Positive pressure maintenance to prevent infiltration
- Zoning for specific operations
This design ensures both air quality and temperature control are maintained. Proper ventilation is essential for meeting cleanliness standards and enhancing operational efficiency.
How often should cleanroom validation be performed?
Cleanroom validation should be performed regularly to ensure compliance with established standards. The frequency may depend on the specific industry and regulatory requirements.
Typical validation intervals include:
- Annually for routine checks
- After significant changes or repairs
- Whenever new equipment or processes are introduced
Regular validation helps identify potential issues before they affect product quality. It ensures that the cleanroom environment remains suitable for its intended use.
How to assess the effectiveness of cleanroom cleaning protocols?
Assessing the effectiveness of cleanroom cleaning protocols involves a systematic approach. Key components include regular monitoring, documentation, and validation of cleaning procedures.
Evaluation methods include:
- Surface sampling for contamination levels
- Review of cleaning logs and frequencies
- Staff training effectiveness assessments
Regular audits and feedback mechanisms help refine cleaning protocols. This ongoing assessment supports continuous improvement in maintaining cleanliness standards.
How to assess the energy efficiency of a cleanroom?
Assessing the energy efficiency of a cleanroom involves evaluating### How to assess the energy efficiency of a cleanroom?
Assessing the energy efficiency of a cleanroom involves evaluating several key factors, such as HVAC system performance, lighting efficiency, and overall energy consumption.
Methods include:
- Monitoring energy usage over time
- Analyzing HVAC system performance metrics
- Conducting thermal imaging inspections
Implementing energy-efficient practices can lead to significant cost savings and reduced environmental impact. Regular assessments support ongoing improvements in energy management strategies.
How to certify a modular cleanroom?
Certifying a modular cleanroom involves several steps to ensure compliance with industry standards. This process typically includes design review, installation verification, and performance testing.
Key certification steps are:
- Initial design assessment against relevant standards
- Installation validation and documentation
- Final performance testing and reporting
Certification provides assurance that the cleanroom meets required cleanliness and operational standards. It is essential for regulatory compliance in sensitive industries, such as pharmaceuticals and biotechnology.
How to choose a modular cleanroom?
Choosing a modular cleanroom requires careful consideration of several factors to meet specific operational needs. Key aspects include cleanliness requirements, space constraints, and intended use.
Factors to evaluate:
- Compliance with relevant ISO standards
- Customization options for layout and design
- Scalability for future expansion
Additionally, consider the manufacturer’s reputation and experience in the industry. A well-chosen modular cleanroom will enhance operational efficiency and compliance with cleanliness standards.
How to conduct a gap analysis for a modular cleanroom?
Conducting a gap analysis for a modular cleanroom involves assessing current operations against industry standards and best practices. This process identifies areas needing improvement for compliance.
Key steps include:
- Evaluating existing cleanroom conditions
- Comparing against regulatory requirements
- Identifying discrepancies and areas for enhancement
The analysis helps prioritize actions for upgrading the cleanroom. Regular gap analyses ensure ongoing compliance and operational efficiency in sensitive environments.
How to conduct a risk assessment for a modular cleanroom?
Conducting a risk assessment for a modular cleanroom is essential for identifying potential hazards. This process helps mitigate risks to product quality and personnel safety.
Key steps include:
- Identifying potential contamination sources
- Evaluating the likelihood and impact of risks
- Implementing control measures and monitoring strategies
Regular reviews of the risk assessment are essential to adapt to changing conditions or processes. This proactive approach supports a safer and more compliant cleanroom environment.
How to conduct regular inspections of a modular cleanroom?
Regular inspections of a modular cleanroom are crucial for maintaining compliance and operational efficiency. Inspections should follow a systematic approach to identify any issues promptly.
Key inspection components include:
- Visual checks for cleanliness and order
- Monitoring of environmental parameters (airflow, temperature)
- Review of equipment functionality and maintenance logs
Documenting findings and corrective actions is essential for compliance. Regular inspections help ensure that the cleanroom continues to meet required standards and operates effectively.
How to create a cleanroom emergency response plan?
Creating a cleanroom emergency response plan involves identifying potential emergencies and outlining procedures to address them effectively. This plan ensures safety and compliance during unexpected events.
Key components of an emergency response plan include:
- Identification of potential hazards (fires, spills, equipment failure)
- Designation of roles and responsibilities for staff
- Clear communication protocols and evacuation routes
Regular training and drills are essential to ensure staff familiarity with the plan. An effective emergency response plan enhances safety and minimizes disruptions in cleanroom operations.
Factory Production Workshop Video
Factory Photo
Product Packaging And International Logistics
Product International Certification
Find Other Common Equipment Recommendations
-
Modular CleanRoom
US$9000-10000 USD/Unit
Min. Order:1 Set -
Air Shower
US$1000.00-5000.00 USD/Unit
Min. Order:1 Set -
Downflow Booth
US$3000-6000 USD/Unit
Min. Order:1 Set -
Clean bench
US$600-2000 USD/Unit
Min. Order:1 Set -
Air Filter
US$3-50 USD/Unit
Min. Order:1 Set -
Cleanroom Wall Panels
US$10-20 USD/sq.
Min. Order:1 Set -
Pass Box
US$200-500 USD/Unit
Min. Order:1 Set -
FFU
US$135-350 USD/Unit
Min. Order:1 Set -
Fume Hood
US$700-1500 USD/Unit
Min. Order:1 Set -
Cleanroom HVAC
US$5000-20000 USD/Unit
Min. Order:1 Set -
Clean room floor
US$5-20 USD/Sq.
Min. Order:1 Set -
Clean room ceiling
US$
Min. Order:1 Set