3 x 3M ISO 6 Modular Cleanroom
Reference Price:US$4750-5500
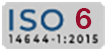
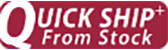

Cleanroom
3 x 3M ISO 6 Modular Cleanroom
Choose your installation & validation options below
Quantity:
Choose your Cleanroom frame structure material
Quantity:
Choose your Cleanroom Wall enclosure materials
Quantity:
Choose your Temperature requirements
Quantity:
Choose your humidity requirements
Quantity:
Choose your Explosion-proof requirements
Quantity:
Summary
3 x 3M ISO 6 Modular Cleanroom
Validation
Installation & Validation
Find Similar Products
-
5 x 15M ISO 6 Modular Cleanroom
US$18000-56000 USD/Set
Min. Order:1 Set -
6 x 10M ISO 6 Modular Cleanroom
US$18000-56000 USD/Set
Min. Order:1 Set -
6 x 8M ISO 6 Modular Cleanroom
US$18000-56000 USD/Set
Min. Order:1 Set -
6 x 6M ISO 6 Modular Cleanroom
US$18000-56000 USD/Set
Min. Order:1 Set -
5 x 10M ISO 6 Modular Cleanroom
US$18000-56000 USD/Set
Min. Order:1 Set -
5 x 8M ISO 6 Modular Cleanroom
US$18000-56000 USD/Set
Min. Order:1 Set
Cleanrooms Detail
A 3 x 3 meter ISO Class 6 modular cleanroom is a controlled environment designed to meet the stringent air cleanliness requirements of ISO 14644-1 standards. It’s a compact, customizable solution for industries that require a high level of contamination control, such as pharmaceuticals, biotechnology, electronics, or precision manufacturing. Let’s break down what this means and why it’s useful.
Cleanroom Project Scope(from structure, HVAC,electric to autoc ontrol) | 1. Cleanroom Structure: Wall Panel, Ceiling Panel, Windows, Doors, Fttings, Flooring |
2. HVAC: AHU, Chiller, dehumidifier, Ducting, Piping, etc. | |
3. Electric: Lighting, Switch, Cables, Wires, Power Distribution Cabinet, etc | |
4. Auto- control: PLC Controller, Sensors for Humidity and Temperature, Control Panel | |
5. Process Piping System: Gas, Water Pipeline | |
Equipment | Air shower, Cargo shower, Mist shower, Dynamic pass box, Static pass box, Sampling booth,Weighing booth, Dispensing booth, |
Medicine stability test chamber, isolator, VHP sterilizer,Biological safety chamber, FFU, LAF, etc. | |
Temperature | 21-27*C (or as per required) |
Humidity | 30-60°C (or as per required) |
Application | Pharmaceutical factory, hospital, medical device factory, electronics factory, food factory,cosmetics factory, etc. |
Qualification Documents | CE GMP ISO |
Full Service | FAT and SAT Service, Professional Consultation, Training, 24 hours technical support |
Applications
A cleanroom of this size and classification is ideal for small-scale operations that require a controlled environment. Common uses include:
Pharmaceuticals: Sterile drug formulation or packaging.
Biotechnology: Cell culture or microbiological work.
Electronics: Assembly of sensitive components like microchips.
Medical Devices: Manufacturing or testing of sterile devices.
Research Labs: Small-scale experiments requiring contamination control.
Advantages of a Modular Cleanroom
Flexibility: Modular cleanrooms can be easily expanded, relocated, or reconfigured to meet changing needs.
Cost-Effective: Smaller size reduces construction and operational costs compared to larger cleanrooms.
Quick Installation: Prefabricated panels and components allow for faster setup compared to traditional cleanrooms.
Compliance: Designed to meet ISO 14644-1 standards, ensuring regulatory compliance for industries like pharmaceuticals and electronics.
Cleanrooms Airflow
When designing the airflow system for an ISO 6 modular cleanroom, several factors must be considered:
Air Changes Per Hour (ACH):
ISO Class 6 cleanrooms typically require 70-160 air changes per hour to maintain cleanliness.
The exact number depends on the cleanroom’s size, usage, and contamination sources.
Cleanrooms Installation
Cleanrooms Testing
Importance of testing
Clean room testing is extremely important to ensure product quality and the stability of the production environment. It can help to confirm whether the clean room meets the intended cleanliness requirements, and whether the various environmental indicators comply with the specified standards.
Testing Standards
ISO 6 Modular Cleanroom Testing Standards are guided by ISO 14644-1 and related protocols to ensure compliance and performance. Key standards include:
Particle Count Testing: Verifies airborne particle levels (≤35,200 particles ≥0.5 µm/m³).
Airflow Velocity Testing: Ensures proper airflow speed and uniformity.
Filter Integrity Testing: Detects HEPA/ULPA filter leaks using DOP/PAO aerosols.
Pressure Differential Testing: Maintains positive pressure to prevent contamination.
Air Changes Per Hour (ACH): Confirms sufficient air replacement (70-160 ACH).
Recovery Testing: Measures contamination recovery time.
Environmental Monitoring: Tracks temperature, humidity, lighting, and noise levels.
These standards ensure the cleanroom meets ISO Class 6 requirements for controlled environments.
FAQ
What types of equipment are necessary for ISO 6 cleanroom operations?
ISO 6 cleanroom operations require specialized equipment to maintain cleanliness and control environmental conditions. Essential items include HEPA filters, air handling units, and laminar flow hoods.
Additionally, personal protective equipment (PPE) is crucial, including gloves, masks, and gowns. Monitoring instruments like particle counters and temperature-humidity sensors are also necessary to ensure compliance.
Finally, cleanroom furniture, such as stainless steel workbenches and shelving, is recommended to minimize contamination risks. Regular maintenance and calibration of all equipment are vital for optimal performance.
What are the lighting requirements for ISO 6 cleanrooms?
ISO 6 cleanrooms must have specific lighting requirements to ensure adequate visibility while maintaining cleanliness. The lighting should be non-glare and easy to clean, often utilizing LED fixtures.
Moreover, the light levels should typically range from 300 to 500 lux, depending on the tasks performed. It is crucial to minimize shadows and reflections to enhance safety and accuracy.
The fixtures should be installed with sealed designs to prevent dust accumulation. Regular inspections and cleaning of lighting fixtures are necessary to maintain optimal performance.
What are the key components of a modular cleanroom design?
A modular cleanroom design includes various key components to ensure effectiveness and compliance. These components typically consist of wall systems, ceilings, and flooring made from cleanable materials.
Additionally, an efficient air handling system is essential, incorporating HEPA filters and proper ducting. Lighting and electrical systems must also be integrated seamlessly into the design.
Other critical elements include access control systems, gowning areas, and utility connections. Each component should be designed to minimize contamination risks while maximizing workflow efficiency.
What is the role of cleanroom apparel in contamination control?
Cleanroom apparel plays a crucial role in minimizing contamination within controlled environments. The apparel, including gowns, gloves, and masks, acts as a barrier between personnel and the cleanroom environment.
By wearing appropriate cleanroom clothing, operators prevent shedding skin cells, hair, and other contaminants. This helps maintain the desired cleanliness levels and protects sensitive processes or products.
Furthermore, cleanroom apparel is typically made of materials designed to resist particle generation and allow for easy cleaning. Regular inspection and proper laundering of these garments are vital to ensure ongoing effectiveness.
What are the advantages of modular cleanrooms?
Modular cleanrooms offer numerous advantages, including flexibility in design and layout. They can be easily expanded, reconfigured, or relocated as business needs change.
Additionally, modular cleanrooms often have shorter construction times compared to traditional cleanrooms. This allows businesses to implement controlled environments quickly and efficiently.
Cost-effectiveness is another significant benefit, as modular options typically require less capital investment. Moreover, they can be tailored to specific industry requirements while maintaining compliance with cleanliness standards.
What is the procurement process for modular cleanrooms?
The procurement process for modular cleanrooms involves several essential steps to ensure quality and compliance. Initially, businesses must define their specific cleanroom requirements based on industry standards.
Next, they should conduct market research to identify reputable suppliers and manufacturers. Requesting proposals and quotes from multiple vendors can provide valuable insights into pricing and options available.
Once a supplier is selected, a contract is negotiated, outlining terms, timelines, and deliverables. Finally, the installation and commissioning process should be carefully monitored to ensure compliance with design specifications.
How to integrate automation into a modular cleanroom?
Integrating automation into a modular cleanroom involves several strategic steps. First, assess the processes that could benefit from automation, such as material handling, monitoring, and data collection.
Next, select appropriate automation technologies, including robotic systems, automated guided vehicles, and monitoring software. This selection should be based on specific cleanroom requirements and operational goals.
Collaboration with automation specialists during the design phase can help ensure seamless integration. Regular training for personnel is also necessary to maximize the benefits of automation in cleanroom operations.
What monitoring equipment is used in ISO 6 cleanrooms?
ISO 6 cleanrooms utilize various monitoring equipment to maintain desired environmental conditions. Key devices include particle counters to measure airborne contamination levels.
Temperature and humidity sensors are crucial for ensuring compliance with specified ranges. Additionally, pressure gauges help monitor airflow and maintain proper air balance within the cleanroom.
Alarms and data logging systems can alert operators to deviations from established parameters. Regular calibration and maintenance of monitoring equipment are essential to ensure accurate readings.
What is the impact of modular cleanroom design on operational efficiency?
Modular cleanroom design significantly impacts operational efficiency by enabling streamlined workflows. The flexible layout allows for efficient movement of personnel and materials, minimizing bottlenecks.
Additionally, modular designs often incorporate advanced air management systems to enhance cleanliness and reduce contamination risks. This leads to improved product quality and reduced waste.
Furthermore, rapid installation and reconfiguration capabilities enable businesses to adapt to changing demands quickly. Overall, a well-designed modular cleanroom can enhance productivity and operational effectiveness.
What is the installation timeline### What is the installation timeline for a modular cleanroom?
The installation timeline for a modular cleanroom can vary based on several factors. Typically, the entire process ranges from a few weeks to several months, depending on the complexity and size of the cleanroom.
Initially, project planning and design phases take 2 to 4 weeks, where requirements are defined. Following this, the manufacturing of modular components usually takes 4 to 8 weeks, depending on the supplier's capabilities.
Installation of the cleanroom itself often takes an additional 2 to 6 weeks, including setup and commissioning. Final testing and validation are then conducted to ensure compliance with cleanliness standards.
What is the cleaning procedure for modular cleanrooms?
The cleaning procedure for modular cleanrooms is crucial for maintaining controlled environments. It typically involves a systematic approach, starting with dusting and removing loose particles using specialized tools.
Following this, surfaces should be cleaned with approved disinfectants, ensuring that all high-touch areas receive thorough attention. Pay particular attention to corners, seams, and equipment, which can harbor contaminants.
Regular cleaning schedules should be established to ensure consistent maintenance. Additionally, staff should be trained in proper cleaning techniques and the use of appropriate materials.
How to ensure a dust-free environment in a modular cleanroom?
Ensuring a dust-free environment in a modular cleanroom involves several key strategies. First, implement strict gowning protocols, requiring personnel to wear appropriate cleanroom apparel to minimize particle shedding.
Next, utilize high-efficiency air filtration systems, such as HEPA filters, to capture airborne particles. Regular monitoring of airflow patterns and pressure differentials also helps maintain cleanliness.
Additionally, establish a routine cleaning schedule and use specialized cleaning tools designed for cleanrooms. Regular training of personnel on contamination control practices is also essential to uphold a dust-free environment.
What types of airflow patterns are used in modular cleanrooms?
Modular cleanrooms typically employ specific airflow patterns to optimize cleanliness. The most common types include unidirectional (laminar) flow and turbulent flow patterns.
Unidirectional airflow, where air moves in a single direction, helps maintain a steady flow of clean air over surfaces. This pattern effectively minimizes particle contamination on critical areas.
Turbulent airflow involves mixing air throughout the space, providing broader coverage. However, it may not be as effective in controlling contamination as unidirectional flow. The choice of airflow pattern should align with cleanroom requirements and processes.
How to validate a modular cleanroom's performance?
Validating a modular cleanroom's performance involves a systematic approach to ensure compliance with standards. The process typically includes initial design reviews to confirm that specifications meet regulatory requirements.
Next, perform operational qualifications, assessing airflow, temperature, and humidity levels to ensure they meet defined criteria. Particle counts are also taken to verify cleanliness levels.
Final validation should include performance testing under real operational conditions, ensuring that the cleanroom consistently meets required standards. Documentation of all tests and results is crucial for compliance and future audits.
How to design a modular cleanroom?
Designing a modular cleanroom requires careful consideration of various factors. First, assess the specific needs of the processes, including cleanliness levels and workflows. This will guide the layout and features of the cleanroom.
Next, select materials that are easy to clean and suitable for controlled environments. Wall, flooring, and ceiling materials should resist contamination and be compatible with cleaning agents.
Finally, incorporate efficient air handling systems and monitor placements to maintain environmental control. Collaboration with cleanroom specialists can provide valuable insights to ensure optimal design and functionality.
What is a modular cleanroom?
A modular cleanroom is a flexible, prefabricated structure designed to meet specific cleanliness requirements. These cleanrooms can be quickly assembled and customized based on operational needs and industry standards.
Typically constructed with cleanable materials, modular cleanrooms facilitate easy maintenance and reconfiguration. They are ideal for industries requiring controlled environments, such as pharmaceuticals, electronics, and biotechnology.
Modular cleanrooms can be expanded or relocated with minimal disruption, providing businesses with adaptability as requirements change. This flexibility and efficiency make them a popular choice in various sectors.
What professionals are needed for modular cleanroom installation?
Installing a modular cleanroom requires input from various professionals to ensure success. Key personnel typically include cleanroom design engineers who create the layout and specifications.
Additionally, project managers oversee the installation process, ensuring timelines and budgets are adhered to. Skilled technicians and craftsmen are also needed for assembly and installation of modular components.
Finally, validation specialists conduct performance testing to ensure compliance with cleanliness standards. Collaboration among these professionals is essential for a successful installation.
What is the construction process for a modular cleanroom?
The construction process for a modular cleanroom involves several well-defined steps. Initially, project planning and design stages focus on defining requirements and creating design specifications.
Once the design is approved, manufacturing of modular components begins, which can take several weeks. After fabrication, the installation phase starts, involving assembly of walls, ceilings, and air handling systems on
Factory Production Workshop Video
Factory Photo
Product Packaging And International Logistics
Product International Certification
Find Other Common Equipment Recommendations
-
Modular CleanRoom
US$9000-10000 USD/Unit
Min. Order:1 Set -
Air Shower
US$1000.00-5000.00 USD/Unit
Min. Order:1 Set -
Downflow Booth
US$3000-6000 USD/Unit
Min. Order:1 Set -
Clean bench
US$600-2000 USD/Unit
Min. Order:1 Set -
Air Filter
US$3-50 USD/Unit
Min. Order:1 Set -
Cleanroom Wall Panels
US$10-20 USD/sq.
Min. Order:1 Set -
Pass Box
US$200-500 USD/Unit
Min. Order:1 Set -
FFU
US$135-350 USD/Unit
Min. Order:1 Set -
Fume Hood
US$700-1500 USD/Unit
Min. Order:1 Set -
Cleanroom HVAC
US$5000-20000 USD/Unit
Min. Order:1 Set -
Clean room floor
US$5-20 USD/Sq.
Min. Order:1 Set -
Clean room ceiling
US$
Min. Order:1 Set