5 x 15M ISO 7 Modular Cleanroom
Reference Price:US$26000-46000

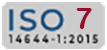

Cleanroom
5 x 15M ISO 7 Modular Cleanroom
Choose your installation & validation options below
Quantity:
Choose your Cleanroom frame structure material
Quantity:
Choose your Cleanroom Wall enclosure materials
Quantity:
Choose your Temperature requirements
Quantity:
Choose your humidity requirements
Quantity:
Choose your Explosion-proof requirements
Quantity:
Summary
5 x 15M ISO 7 Modular Cleanroom
Validation
Installation & Validation
Find Similar Products
-
5 x 15M ISO 7 Modular Cleanroom
US$15000-50000 USD/Set
Min. Order:1 Set -
6 x 10M ISO 7 Modular Cleanroom
US$15000-50000 USD/Set
Min. Order:1 Set -
6 x 8M ISO 7 Modular Cleanroom
US$15000-50000 USD/Set
Min. Order:1 Set -
6 x 6M ISO 7 Modular Cleanroom
US$15000-50000 USD/Set
Min. Order:1 Set -
5 x 10M ISO 7 Modular Cleanroom
US$15000-50000 USD/Set
Min. Order:1 Set -
5 x 8M ISO 7 Modular Cleanroom
US$15000-50000 USD/Set
Min. Order:1 Set
Cleanrooms Detail
In today’s manufacturing and research environments, the demand for cleanrooms is on the rise, especially in industries like pharmaceuticals, semiconductors, and biotechnology. The ISO 7 modular cleanroom is a versatile solution designed to effectively ensure product quality and safety.
ISO 7 Cleanroom Standards
An ISO 7 cleanroom must meet specific air cleanliness standards, including:
No more than 352,000 particles per cubic meter of air (0.5 micrometers and larger).
No more than 3,520 particles per cubic meter of air (5 micrometers and larger).
These standards ensure that operations within the cleanroom remain uncontaminated, safeguarding both products and personnel.
Cleanroom Project Scope(from structure, HVAC,electric to autoc ontrol) | 1. Cleanroom Structure: Wall Panel, Ceiling Panel, Windows, Doors, Fttings, Flooring |
2. HVAC: AHU, Chiller, dehumidifier, Ducting, Piping, etc. | |
3. Electric: Lighting, Switch, Cables, Wires, Power Distribution Cabinet, etc | |
4. Auto- control: PLC Controller, Sensors for Humidity and Temperature, Control Panel | |
5. Process Piping System: Gas, Water Pipeline | |
Equipment | Air shower, Cargo shower, Mist shower, Dynamic pass box, Static pass box, Sampling booth,Weighing booth, Dispensing booth, |
Medicine stability test chamber, isolator, VHP sterilizer,Biological safety chamber, FFU, LAF, etc. | |
Temperature | 21-27*C (or as per required) |
Humidity | 30-60°C (or as per required) |
Application | Pharmaceutical factory, hospital, medical device factory, electronics factory, food factory,cosmetics factory, etc. |
Qualification Documents | CE GMP ISO |
Full Service | FAT and SAT Service, Professional Consultation, Training, 24 hours technical support |
Cleanrooms Airflow
When designing the airflow system for an ISO 7 modular cleanroom, several factors must be considered:
Air Changes Per Hour (ACH):
ISO Class 7 cleanrooms typically require 30-50 air changes per hour to maintain cleanliness.
The exact number depends on the cleanroom’s size, usage, and contamination sources.
Cleanrooms Installation
Cleanrooms Testing
Importance of testing
Clean room testing is extremely important to ensure product quality and the stability of the production environment. It can help to confirm whether the clean room meets the intended cleanliness requirements, and whether the various environmental indicators comply with the specified standards.
Testing Items
Suspended particles: Detects the number of suspended particles in the air in the clean room to ensure that the air cleanliness is up to standard.
Temperature and humidity: Monitor the temperature and humidity in the clean room to ensure environmental stability during the production process.
Noise: Evaluates the noise level in the clean room to minimize the impact on staff.
Static electricity: Detect static electricity buildup in the clean room to prevent damage to sensitive components from electrostatic discharge.
Microbial contamination: Detecting microbial levels in the clean room, especially critical for the healthcare industry.
FAQ
What are the common applications of modular cleanrooms?
Modular cleanrooms are widely used in various industries. Common applications include pharmaceuticals, biotechnology, and electronics manufacturing.
They provide controlled environments essential for product quality and safety. Key benefits include flexibility, quick installation, and cost-effectiveness.
In addition, modular cleanrooms can be customized for specific needs, such as:
- Sterile manufacturing
- Research and development
- Medical device production
How to design an ergonomic cleanroom workspace?
Designing an ergonomic cleanroom workspace involves careful planning. Focus on layout, equipment placement, and worker comfort to enhance productivity.
Consider the following elements:
- Adjustable workstations
- Proper lighting
- Easy access to tools and materials
Incorporating these features helps reduce fatigue and improves efficiency. Regular assessments ensure the workspace meets ergonomic standards.
How to implement an effective cleanroom SOP?
Implementing an effective cleanroom Standard Operating Procedure (SOP) requires clear guidelines. Start by defining the scope and objectives of the SOP.
Next, involve key stakeholders in the development process. Ensure the SOP covers:
- Personnel training
- Equipment usage
- Cleaning protocols
Regular reviews and updates are essential to maintain compliance and effectiveness. Training sessions should reinforce the importance of following the SOP.
How to handle waste in cleanrooms?
Handling waste in cleanrooms is crucial for maintaining cleanliness. Establish a waste management plan that includes segregation, labeling, and disposal procedures.
Key steps include:
- Designate waste collection areas.
- Use appropriate containers for different waste types.
- Train personnel on proper disposal methods.
Regular audits ensure compliance with regulations and promote a clean environment.
How to assess cleanroom compliance with regulations?
Assessing cleanroom compliance involves systematic evaluation. Start with a review of relevant regulations and standards applicable to your industry.
Conduct regular inspections focusing on:
- Air quality
- Surface cleanliness
- Personnel practices
Document findings and implement corrective actions as needed. Continuous training ensures staff remain informed about compliance requirements.
What are the features of a high-performance cleanroom?
High-performance cleanrooms possess several key features. These include advanced filtration systems, controlled airflow, and temperature regulation.
Additionally, they should have:
- Low particle count
- Humidity control
- Robust monitoring systems
These features ensure optimal conditions for sensitive processes and products, enhancing overall efficiency.
What are the best cleanroom practices for pharmaceuticals?
Best practices for pharmaceuticals in cleanrooms focus on contamination control. Key practices include strict gowning procedures, regular cleaning, and personnel training.
Implementing a robust monitoring system helps maintain environmental standards. Regular audits ensure compliance with industry regulations.
Additionally, fostering a culture of quality and safety among staff is essential for maintaining high standards.
How to manage cleanroom inventory?
Managing cleanroom inventory requires organization and tracking. Implement a system for monitoring supplies, equipment, and materials.
Key strategies include:
- Regular inventory audits
- Automated tracking systems
- Clear labeling and storage protocols
Effective inventory management minimizes waste and ensures that necessary materials are always available.
How much does a modular cleanroom cost?
The cost of a modular cleanroom varies based on size and specifications. Factors influencing the price include materials, design complexity, and additional features.
On average, costs can range from $50,000 to $200,000. Customization and installation also impact the final price.
Investing in a modular cleanroom can lead to long-term savings through efficiency and flexibility.
How to calculate the ROI of a modular cleanroom?
Calculating the ROI of a modular cleanroom involves assessing costs and benefits. Start by estimating initial investment and ongoing operational expenses.
Next, evaluate potential savings and revenue increases from improved efficiency. Consider factors such as:
- Reduced contamination rates
- Increased production capacity
- Enhanced product quality
A clear ROI calculation helps justify the investment and guides future decisions.
What materials are used in modular cleanroom construction?
Modular cleanroom construction typically uses materials that support cleanliness and durability. Common materials include:
- Stainless steel
- High-density polyethylene (HDPE)
- Cleanroom-compatible wall panels
These materials are chosen for their ease of cleaning and resistance to contamination. Proper selection ensures long-lasting performance in cleanroom environments.
What is the difference between cleanroom and controlled environment?
A cleanroom is a controlled environment specifically designed to minimize contamination. It maintains strict air quality and cleanliness standards.
In contrast, a controlled environment may not have the same stringent requirements. It can refer to any space where temperature, humidity, or other factors are regulated.
Understanding these differences is crucial for selecting the right facility for specific applications.
How to document cleanroom processes?
Documenting cleanroom processes is essential for compliance and quality control. Start by creating detailed procedures for all operations.
Key documentation should include:
- Standard Operating Procedures (SOPs)
- Training records
- Inspection logs
Regularly review and update documents to reflect changes in processes or regulations. This ensures ongoing compliance and operational efficiency.
What is the cleanroom classification system?
The cleanroom classification system categorizes cleanrooms based on particle count and cleanliness levels. Common classifications include ISO 1 to ISO 9, with ISO 1 being the cleanest.
Each class specifies maximum allowable particle counts for different sizes. Understanding this system helps in selecting the appropriate cleanroom for specific applications.
What is the cleanroom gowning procedure?
The cleanroom gowning procedure is critical for contamination control. It involves a series of steps to ensure personnel are properly attired before entering the cleanroom.
Key steps include:
- Donning shoe covers
- Wearing coveralls
- Using gloves and masks
Following the gowning procedure minimizes the risk of introducing contaminants into the cleanroom environment.
What equipment is needed for an ISO 7 cleanroom?
An ISO 7 cleanroom requires specific equipment to maintain cleanliness. Essential equipment includes:
- HEPA filters
- Air showers
- Cleanroom furniture
Additionally, monitoring systems for temperature and humidity are crucial. Proper equipment ensures compliance with ISO standards and supports operational efficiency.
What are the common cleaning agents used in cleanrooms?
Common cleaning agents used in cleanrooms are designed to minimize contamination. Effective agents include:
- Isopropyl alcohol
- Hydrogen peroxide
- Quaternary ammonium compounds
These agents are chosen for their efficacy and low residue. Regular cleaning schedules help maintain a contamination-free environment.
What role does lighting play in cleanrooms?
Lighting plays a vital role in cleanrooms. Proper illumination enhances visibility and supports precision in tasks.
Key considerations include:
- Brightness levels
- Color temperature
- Glare reduction
Effective lighting contributes to a safe and efficient working environment, promoting productivity and accuracy.
How to maintain cleanroom integrity during construction?
Maintaining cleanroom integrity during construction is crucial. Implement strict protocols to minimize contamination risks.
Key strategies include:
- Using temporary barriers
- Controlling airflow
- Regular monitoring of environmental conditions
These measures ensure that the cleanroom remains compliant with standards throughout the construction process.
How to perform a cleanroom risk analysis?
Performing a cleanroom risk analysis involves identifying potential hazards. Start by assessing environmental factors, equipment, and personnel practices.
Key steps include:
- Conducting a thorough inspection
- Evaluating contamination sources
- Implementing mitigation strategies
Regular reviews of the risk analysis help maintain a safe and compliant cleanroom environment.
What is the cleanroom certification process?
The cleanroom certification process verifies compliance with industry standards. It typically involves a series of tests and inspections.
Key steps include:
- Initial assessment of cleanroom design
- Performance testing for air quality and particle counts
- Documentation of results and compliance
Successful certification ensures that the cleanroom meets required standards for its intended use.
How to retrofit an existing cleanroom to ISO 7 standards?
Retrofitting an existing cleanroom to ISO 7 standards requires careful planning. Start by assessing current conditions and identifying necessary upgrades.
Key steps include:
- Upgrading filtration systems
- Enhancing airflow control
- Implementing stricter cleaning protocols
Regular monitoring and testing ensure compliance with ISO 7 standards post-retrofit.
What are the airflow requirements for ISO 7 cleanrooms?
ISO 7 cleanrooms have specific airflow requirements to maintain cleanliness. The recommended airflow rate is typically 0.45 m/s or higher.
Key considerations include:
- Air changes per hour (ACH)
- Direction of airflow
- Filter efficiency
Proper airflow management is essential for minimizing contamination and ensuring a controlled environment.
How to integrate automation in modular cleanrooms?
Integrating automation in modular cleanrooms enhances efficiency and consistency. Start by identifying processes suitable for automation.
Key areas for integration include:
- Material handling
- Environmental monitoring
- Data collection and analysis
Automation streamlines operations, reduces human error, and supports compliance with cleanroom standards.
How to perform a cleanroom audit?
Performing a cleanroom audit involves systematic evaluation of processes and compliance. Start by reviewing documentation and procedures.
Key steps include:
- Conducting physical inspections
- Interviewing personnel
- Assessing equipment and materials
Regular audits help identify areas for improvement and ensure ongoing compliance with industry standards.
Factory Production Workshop Video
Factory Photo
Product Packaging And International Logistics
Product International Certification
Find Other Common Equipment Recommendations
-
Modular CleanRoom
US$9000-10000 USD/Unit
Min. Order:1 Set -
Air Shower
US$1000.00-5000.00 USD/Unit
Min. Order:1 Set -
Downflow Booth
US$3000-6000 USD/Unit
Min. Order:1 Set -
Clean bench
US$600-2000 USD/Unit
Min. Order:1 Set -
Air Filter
US$3-50 USD/Unit
Min. Order:1 Set -
Cleanroom Wall Panels
US$10-20 USD/sq.
Min. Order:1 Set -
Pass Box
US$200-500 USD/Unit
Min. Order:1 Set -
FFU
US$135-350 USD/Unit
Min. Order:1 Set -
Fume Hood
US$700-1500 USD/Unit
Min. Order:1 Set -
Cleanroom HVAC
US$5000-20000 USD/Unit
Min. Order:1 Set -
Clean room floor
US$5-20 USD/Sq.
Min. Order:1 Set -
Clean room ceiling
US$
Min. Order:1 Set