6 x 6M ISO 7 Modular Cleanroom
Reference Price:US$9500-11500
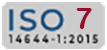


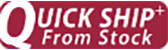
Cleanroom
6 x 6M ISO 7 Modular Cleanroom
Choose your installation & validation options below
Quantity:
Choose your Cleanroom frame structure material
Quantity:
Choose your Cleanroom Wall enclosure materials
Quantity:
Choose your Temperature requirements
Quantity:
Choose your humidity requirements
Quantity:
Choose your Explosion-proof requirements
Quantity:
Summary
6 x 6M ISO 7 Modular Cleanroom
Validation
Installation & Validation
Find Similar Products
-
5 x 15M ISO 7 Modular Cleanroom
US$15000-50000 USD/Set
Min. Order:1 Set -
6 x 10M ISO 7 Modular Cleanroom
US$15000-50000 USD/Set
Min. Order:1 Set -
6 x 8M ISO 7 Modular Cleanroom
US$15000-50000 USD/Set
Min. Order:1 Set -
6 x 6M ISO 7 Modular Cleanroom
US$15000-50000 USD/Set
Min. Order:1 Set -
5 x 10M ISO 7 Modular Cleanroom
US$15000-50000 USD/Set
Min. Order:1 Set -
5 x 8M ISO 7 Modular Cleanroom
US$15000-50000 USD/Set
Min. Order:1 Set
Cleanrooms Detail
In today’s manufacturing and research environments, the demand for cleanrooms is on the rise, especially in industries like pharmaceuticals, semiconductors, and biotechnology. The ISO 7 modular cleanroom is a versatile solution designed to effectively ensure product quality and safety.
ISO 7 Cleanroom Standards
An ISO 7 cleanroom must meet specific air cleanliness standards, including:
No more than 352,000 particles per cubic meter of air (0.5 micrometers and larger).
No more than 3,520 particles per cubic meter of air (5 micrometers and larger).
These standards ensure that operations within the cleanroom remain uncontaminated, safeguarding both products and personnel.
Cleanroom Project Scope(from structure, HVAC,electric to autoc ontrol) | 1. Cleanroom Structure: Wall Panel, Ceiling Panel, Windows, Doors, Fttings, Flooring |
2. HVAC: AHU, Chiller, dehumidifier, Ducting, Piping, etc. | |
3. Electric: Lighting, Switch, Cables, Wires, Power Distribution Cabinet, etc | |
4. Auto- control: PLC Controller, Sensors for Humidity and Temperature, Control Panel | |
5. Process Piping System: Gas, Water Pipeline | |
Equipment | Air shower, Cargo shower, Mist shower, Dynamic pass box, Static pass box, Sampling booth,Weighing booth, Dispensing booth, |
Medicine stability test chamber, isolator, VHP sterilizer,Biological safety chamber, FFU, LAF, etc. | |
Temperature | 21-27*C (or as per required) |
Humidity | 30-60°C (or as per required) |
Application | Pharmaceutical factory, hospital, medical device factory, electronics factory, food factory,cosmetics factory, etc. |
Qualification Documents | CE GMP ISO |
Full Service | FAT and SAT Service, Professional Consultation, Training, 24 hours technical support |
Cleanrooms Airflow
When designing the airflow system for an ISO 7 modular cleanroom, several factors must be considered:
Air Changes Per Hour (ACH):
ISO Class 7 cleanrooms typically require 30-50 air changes per hour to maintain cleanliness.
The exact number depends on the cleanroom’s size, usage, and contamination sources.
Cleanrooms Installation
Cleanrooms Testing
Importance of testing
Clean room testing is extremely important to ensure product quality and the stability of the production environment. It can help to confirm whether the clean room meets the intended cleanliness requirements, and whether the various environmental indicators comply with the specified standards.
Testing Items
Suspended particles: Detects the number of suspended particles in the air in the clean room to ensure that the air cleanliness is up to standard.
Temperature and humidity: Monitor the temperature and humidity in the clean room to ensure environmental stability during the production process.
Noise: Evaluates the noise level in the clean room to minimize the impact on staff.
Static electricity: Detect static electricity buildup in the clean room to prevent damage to sensitive components from electrostatic discharge.
Microbial contamination: Detecting microbial levels in the clean room, especially critical for the healthcare industry.
FAQ
What is the impact of cleanroom design on productivity?
Cleanroom design directly affects workflow efficiency and employee comfort. A well-structured layout reduces unnecessary movement and minimizes contamination risks. Improved air quality and lighting also enhance overall productivity.
How to manage personnel in a cleanroom?
Effective personnel management in cleanrooms involves strict adherence to protocols and training. Regular training sessions ensure that all staff understand cleanroom procedures and safety measures.
Additionally, assigning specific roles helps maintain organization and efficiency within the cleanroom environment.
What equipment is needed for an ISO 7 cleanroom?
An ISO 7 cleanroom requires essential equipment, including:
- HEPA filters for air purification
- Proper HVAC systems for temperature control
- Monitoring devices for particle counts and environmental conditions
These ensure compliance and optimal operation.
How to design an ergonomic cleanroom workspace?
Designing an ergonomic cleanroom workspace involves creating layouts that minimize strain and enhance comfort.
Consider adjustable workstations and proper reach distances to reduce fatigue.
Incorporate adequate lighting and easy access to tools and materials for improved efficiency.
How to troubleshoot cleanroom issues?
Begin troubleshooting by identifying the specific issue, such as contamination or equipment failure.
Next, systematically evaluate all potential causes, including equipment settings and environmental controls.
Finally, implement corrective actions and monitor results to ensure the issue is resolved.
What is the importance of airflow visualization in cleanrooms?
Airflow visualization helps in understanding air patterns and identifying areas of contamination risk.
It allows for optimizing the cleanroom design to enhance air distribution and reduce dead zones.
Proper airflow management is critical for maintaining cleanroom standards and compliance.
How to design an ISO 7 modular cleanroom?
Designing an ISO 7 modular cleanroom starts with selecting appropriate materials and layouts for compliance.
Ensure that the filtration systems and HVAC meet ISO standards for air quality.
Consider incorporating flexible walls and modular components to adapt to future needs.
What materials are used in modular cleanroom construction?
Common materials for modular cleanroom construction include:
- Aluminum or stainless steel for structural components
- Vinyl or epoxy flooring for easy cleaning
- Cleanroom-compatible wall panels for contamination control
These materials ensure durability and compliance with cleanroom standards.
How to control contamination in modular cleanrooms?
Contamination control in modular cleanrooms involves several strategies.
Implement strict gowning procedures and use proper cleaning agents to maintain cleanliness.
Regular monitoring and maintenance of equipment, including filters, are essential for effective control.
How to select cleanroom garments?
Choose cleanroom garments based on the required level of protection and compatibility with your processes.
Consider factors such as material, fit, and breathability to ensure comfort and safety.
Always follow manufacturer guidelines and industry standards when selecting garments.
What is the difference between cleanroom and controlled environment?
A cleanroom is specifically designed to minimize airborne contaminants, while a controlled environment regulates temperature and humidity.
Not all controlled environments meet cleanroom standards for cleanliness.
Both serve unique purposes in various industries, depending on their requirements.
How does humidity control work in cleanrooms?
Humidity control in cleanrooms is achieved through HVAC systems that regulate moisture levels.
Dehumidifiers may be used to maintain desired humidity ranges for specific processes.
Maintaining appropriate humidity prevents product damage and ensures compliance with industry standards.
How to choose the right modular cleanroom system?
Assess your specific operational requirements, including space and compliance needs.
Evaluate different modular systems based on flexibility, materials, and installation time.
Consult with manufacturers to ensure the system aligns with your cleanroom goals.
How to handle hazardous materials in cleanrooms?
Always follow strict protocols when handling hazardous materials in cleanrooms.
Use appropriate personal protective equipment (PPE) and ensure proper ventilation.
Implement clear storage and disposal procedures to minimize risks and ensure safety.
What is the role of HEPA filters in cleanrooms?
HEPA filters play a crucial role in removing airborne particles and contaminants.
They ensure that the air quality within the cleanroom meets specified cleanliness standards.
Regular maintenance and replacement are necessary to maintain filter efficiency.
What is the role of pressure differentials in cleanrooms?
Pressure differentials help maintain airflow direction and prevent contamination.
Higher pressure in the cleanroom compared to adjacent areas ensures that clean air flows outward.
This is essential for protecting sensitive processes and maintaining clean environments.
How is airflow managed in modular cleanrooms?
Airflow in modular cleanrooms is managed through strategically placed HVAC systems and ventilation ducts.
Continuous monitoring of airflow helps maintain consistent conditions and optimize performance.
Regular adjustments may be necessary to respond to changes in occupancy and equipment use.
What is the cleanroom monitoring equipment?
Cleanroom monitoring equipment typically includes:
- Particle counters to measure airborne contaminants
- Temperature and humidity sensors for environmental control
- Differential pressure monitors to ensure proper airflow
These devices help maintain compliance with cleanroom standards and ensure optimal conditions.
Factory Production Workshop Video
Factory Photo
Product Packaging And International Logistics
Product International Certification
Find Other Common Equipment Recommendations
-
Modular CleanRoom
US$9000-10000 USD/Unit
Min. Order:1 Set -
Air Shower
US$1000.00-5000.00 USD/Unit
Min. Order:1 Set -
Downflow Booth
US$3000-6000 USD/Unit
Min. Order:1 Set -
Clean bench
US$600-2000 USD/Unit
Min. Order:1 Set -
Air Filter
US$3-50 USD/Unit
Min. Order:1 Set -
Cleanroom Wall Panels
US$10-20 USD/sq.
Min. Order:1 Set -
Pass Box
US$200-500 USD/Unit
Min. Order:1 Set -
FFU
US$135-350 USD/Unit
Min. Order:1 Set -
Fume Hood
US$700-1500 USD/Unit
Min. Order:1 Set -
Cleanroom HVAC
US$5000-20000 USD/Unit
Min. Order:1 Set -
Clean room floor
US$5-20 USD/Sq.
Min. Order:1 Set -
Clean room ceiling
US$
Min. Order:1 Set