5 x 5M ISO 6 Modular Cleanroom
Reference Price:US$9700-1600
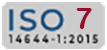
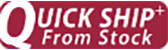

Cleanroom
5 x 5M ISO 6 Modular Cleanroom
Choose your installation & validation options below
Quantity:
Choose your Cleanroom frame structure material
Quantity:
Choose your Cleanroom Wall enclosure materials
Quantity:
Choose your Temperature requirements
Quantity:
Choose your humidity requirements
Quantity:
Choose your Explosion-proof requirements
Quantity:
Summary
5 x 5M ISO 6 Modular Cleanroom
Validation
Installation & Validation
Find Similar Products
-
5 x 15M ISO 7 Modular Cleanroom
US$15000-50000 USD/Set
Min. Order:1 Set -
6 x 10M ISO 7 Modular Cleanroom
US$15000-50000 USD/Set
Min. Order:1 Set -
6 x 8M ISO 7 Modular Cleanroom
US$15000-50000 USD/Set
Min. Order:1 Set -
6 x 6M ISO 7 Modular Cleanroom
US$15000-50000 USD/Set
Min. Order:1 Set -
5 x 10M ISO 7 Modular Cleanroom
US$15000-50000 USD/Set
Min. Order:1 Set -
5 x 8M ISO 7 Modular Cleanroom
US$15000-50000 USD/Set
Min. Order:1 Set
Cleanrooms Detail
In today’s manufacturing and research environments, the demand for cleanrooms is on the rise, especially in industries like pharmaceuticals, semiconductors, and biotechnology. The ISO 7 modular cleanroom is a versatile solution designed to effectively ensure product quality and safety.
ISO 7 Cleanroom Standards
An ISO 7 cleanroom must meet specific air cleanliness standards, including:
No more than 352,000 particles per cubic meter of air (0.5 micrometers and larger).
No more than 3,520 particles per cubic meter of air (5 micrometers and larger).
These standards ensure that operations within the cleanroom remain uncontaminated, safeguarding both products and personnel.
Cleanroom Project Scope(from structure, HVAC,electric to autoc ontrol) | 1. Cleanroom Structure: Wall Panel, Ceiling Panel, Windows, Doors, Fttings, Flooring |
2. HVAC: AHU, Chiller, dehumidifier, Ducting, Piping, etc. | |
3. Electric: Lighting, Switch, Cables, Wires, Power Distribution Cabinet, etc | |
4. Auto- control: PLC Controller, Sensors for Humidity and Temperature, Control Panel | |
5. Process Piping System: Gas, Water Pipeline | |
Equipment | Air shower, Cargo shower, Mist shower, Dynamic pass box, Static pass box, Sampling booth,Weighing booth, Dispensing booth, |
Medicine stability test chamber, isolator, VHP sterilizer,Biological safety chamber, FFU, LAF, etc. | |
Temperature | 21-27*C (or as per required) |
Humidity | 30-60°C (or as per required) |
Application | Pharmaceutical factory, hospital, medical device factory, electronics factory, food factory,cosmetics factory, etc. |
Qualification Documents | CE GMP ISO |
Full Service | FAT and SAT Service, Professional Consultation, Training, 24 hours technical support |
Cleanrooms Airflow
When designing the airflow system for an ISO 7 modular cleanroom, several factors must be considered:
Air Changes Per Hour (ACH):
ISO Class 7 cleanrooms typically require 30-50 air changes per hour to maintain cleanliness.
The exact number depends on the cleanroom’s size, usage, and contamination sources.
Cleanrooms Installation
Cleanrooms Testing
Importance of testing
Clean room testing is extremely important to ensure product quality and the stability of the production environment. It can help to confirm whether the clean room meets the intended cleanliness requirements, and whether the various environmental indicators comply with the specified standards.
Testing Items
Suspended particles: Detects the number of suspended particles in the air in the clean room to ensure that the air cleanliness is up to standard.
Temperature and humidity: Monitor the temperature and humidity in the clean room to ensure environmental stability during the production process.
Noise: Evaluates the noise level in the clean room to minimize the impact on staff.
Static electricity: Detect static electricity buildup in the clean room to prevent damage to sensitive components from electrostatic discharge.
Microbial contamination: Detecting microbial levels in the clean room, especially critical for the healthcare industry.
FAQ
What is a modular cleanroom?
A modular cleanroom is a prefabricated, adaptable space designed to meet specific cleanliness standards. It can be quickly assembled and customized for various applications.
What role does lighting play in cleanrooms?
Lighting in cleanrooms is crucial for visibility and safety. It must be designed to minimize shadows and glare while maintaining cleanliness. Proper lighting enhances operational efficiency and worker comfort.
What is the cleanroom certification process?
The cleanroom certification process involves several steps:
- Assessing the cleanroom against relevant standards such as ISO.
- Conducting tests for particle counts, airflow, and pressure differentials.
- Documenting results and providing certification upon compliance.
This ensures the cleanroom meets required cleanliness levels.
How to assess cleanroom performance?
To assess cleanroom performance, consider:
- Conducting regular monitoring of particle counts and air quality.
- Evaluating temperature and humidity control effectiveness.
- Reviewing compliance with established cleanliness standards.
These assessments ensure the cleanroom operates effectively and meets regulatory requirements.
What are the key features of modular cleanrooms?
Key features of modular cleanrooms include:
- Flexibility to adapt to different layouts and requirements.
- Quick installation and reduced construction time.
- High-quality materials for effective contamination control.
These features make them suitable for various industries.
What is the purpose of a cleanroom?
The primary purpose of a cleanroom is to maintain a controlled environment that minimizes contamination. This is essential for industries such as pharmaceuticals, biotechnology, and electronics.
What is the impact of vibration on cleanroom operations?
Vibration can negatively affect sensitive equipment and processes in cleanrooms. It may lead to contamination, equipment malfunction, or reduced product quality. Minimizing vibration is crucial to maintaining operational integrity.
How to perform a cleanroom audit?
To perform a cleanroom audit:
- Review documentation and protocols for compliance.
- Inspect the facility for cleanliness and operational practices.
- Conduct testing for air quality and particle counts.
This ensures adherence to standards and identifies areas for improvement.
What are the environmental requirements for ISO 7 cleanrooms?
ISO 7 cleanrooms must meet specific environmental requirements, including:
- Maximum particle count of 352,000 particles/m³ at 0.5 microns.
- Controlled temperature and humidity levels.
- Regular monitoring to ensure compliance.
These criteria ensure the cleanroom functions effectively for sensitive processes.
What are the key components of a modular cleanroom system?
Key components of a modular cleanroom system include:
- Wall systems that provide contamination control.
- HVAC systems for temperature and humidity regulation.
- Air filtration units to maintain air quality.
These components work together to create a controlled environment.
What is the role of pressure differentials in cleanrooms?
Pressure differentials in cleanrooms help control airflow and prevent contamination. Higher pressure inside the cleanroom compared to adjacent areas ensures that air flows outward, minimizing the ingress of contaminants.
How do you measure cleanroom performance?
Cleanroom performance can be measured using various methods:
- Monitoring particle counts with laser particle counters.
- Assessing airflow rates and patterns.
- Evaluating temperature and humidity levels.
These measurements ensure compliance with cleanliness standards.
What is the difference between modular and traditional cleanrooms?
Modular cleanrooms are prefabricated and allow for quick installation and reconfiguration. Traditional cleanrooms are built on-site, requiring more time and resources. Modular designs offer greater flexibility and scalability.
How to manage personnel in a cleanroom?
Managing personnel in a cleanroom involves:
- Implementing strict gowning and hygiene protocols.
- Conducting regular training on cleanroom procedures.
- Monitoring activities to ensure compliance with operational guidelines.
These practices help maintain a contaminant-free environment.
How to implement a cleanroom training program?
To implement a cleanroom training program:
- Develop training materials covering protocols and procedures.
- Schedule initial and ongoing training sessions for all personnel.
- Assess understanding through evaluations and practical exercises.
This ensures staff are well-prepared for cleanroom operations.
How to integrate HVAC systems in modular cleanrooms?
Integrating HVAC systems in modular cleanrooms requires:
- Designing the system to provide adequate airflow and filtration.
- Ensuring compatibility with the cleanroom's layout and requirements.
- Regular maintenance to ensure optimal performance.
This ensures the cleanroom maintains the required environmental conditions.
How to perform a cleanroom risk analysis?
To perform a cleanroom risk analysis:
- Identify potential contamination sources and their impact.
- Assess current controls and their effectiveness.
- Develop a risk mitigation plan to address identified vulnerabilities.
Regular reviews improve cleanroom safety and compliance.
What is the difference between ISO 7 and ISO 8 cleanrooms?
The key differences between ISO 7 and ISO 8 cleanrooms are:
- ISO 7 allows a maximum of 352,000 particles/m³ at 0.5 microns, while ISO 8 allows up to 3,520,000 particles/m³.
- ISO 7 requires stricter control over environmental parameters.
These differences impact their use in various industries.
How to maintain an ISO 7 cleanroom?
To maintain an ISO 7 cleanroom effectively:
- Conduct regular cleaning and disinfection protocols.
- Monitor air quality and particle counts consistently.
- Ensure all equipment is calibrated and functioning properly.
These practices help sustain compliance with cleanliness standards.
What are the best practices for cleanroom operation?
Best practices for cleanroom operation include:
- Adhering to strict gowning and hygiene protocols.
- Regularly monitoring environmental conditions.
- Training staff on cleanroom procedures and protocols.
These practices ensure a controlled environment and minimize contamination.
Factory Production Workshop Video
Factory Photo
Product Packaging And International Logistics
Product International Certification
Find Other Common Equipment Recommendations
-
Modular CleanRoom
US$9000-10000 USD/Unit
Min. Order:1 Set -
Air Shower
US$1000.00-5000.00 USD/Unit
Min. Order:1 Set -
Downflow Booth
US$3000-6000 USD/Unit
Min. Order:1 Set -
Clean bench
US$600-2000 USD/Unit
Min. Order:1 Set -
Air Filter
US$3-50 USD/Unit
Min. Order:1 Set -
Cleanroom Wall Panels
US$10-20 USD/sq.
Min. Order:1 Set -
Pass Box
US$200-500 USD/Unit
Min. Order:1 Set -
FFU
US$135-350 USD/Unit
Min. Order:1 Set -
Fume Hood
US$700-1500 USD/Unit
Min. Order:1 Set -
Cleanroom HVAC
US$5000-20000 USD/Unit
Min. Order:1 Set -
Clean room floor
US$5-20 USD/Sq.
Min. Order:1 Set -
Clean room ceiling
US$
Min. Order:1 Set