4 x 4M ISO 7 Modular Cleanroom
Reference Price:US$7300-9000
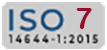


Cleanroom
4 x 4M ISO 7 Modular Cleanroom
Choose your installation & validation options below
Quantity:
Choose your Cleanroom frame structure material
Quantity:
Choose your Cleanroom Wall enclosure materials
Quantity:
Choose your Temperature requirements
Quantity:
Choose your humidity requirements
Quantity:
Choose your Explosion-proof requirements
Quantity:
Summary
4 x 4M ISO 7 Modular Cleanroom
Validation
Installation & Validation
Find Similar Products
-
5 x 15M ISO 7 Modular Cleanroom
US$15000-50000 USD/Set
Min. Order:1 Set -
6 x 10M ISO 7 Modular Cleanroom
US$15000-50000 USD/Set
Min. Order:1 Set -
6 x 8M ISO 7 Modular Cleanroom
US$15000-50000 USD/Set
Min. Order:1 Set -
6 x 6M ISO 7 Modular Cleanroom
US$15000-50000 USD/Set
Min. Order:1 Set -
5 x 10M ISO 7 Modular Cleanroom
US$15000-50000 USD/Set
Min. Order:1 Set -
5 x 8M ISO 7 Modular Cleanroom
US$15000-50000 USD/Set
Min. Order:1 Set
Cleanrooms Detail
In today’s manufacturing and research environments, the demand for cleanrooms is on the rise, especially in industries like pharmaceuticals, semiconductors, and biotechnology. The ISO 7 modular cleanroom is a versatile solution designed to effectively ensure product quality and safety.
ISO 7 Cleanroom Standards
An ISO 7 cleanroom must meet specific air cleanliness standards, including:
No more than 352,000 particles per cubic meter of air (0.5 micrometers and larger).
No more than 3,520 particles per cubic meter of air (5 micrometers and larger).
These standards ensure that operations within the cleanroom remain uncontaminated, safeguarding both products and personnel.
Cleanroom Project Scope(from structure, HVAC,electric to autoc ontrol) | 1. Cleanroom Structure: Wall Panel, Ceiling Panel, Windows, Doors, Fttings, Flooring |
2. HVAC: AHU, Chiller, dehumidifier, Ducting, Piping, etc. | |
3. Electric: Lighting, Switch, Cables, Wires, Power Distribution Cabinet, etc | |
4. Auto- control: PLC Controller, Sensors for Humidity and Temperature, Control Panel | |
5. Process Piping System: Gas, Water Pipeline | |
Equipment | Air shower, Cargo shower, Mist shower, Dynamic pass box, Static pass box, Sampling booth,Weighing booth, Dispensing booth, |
Medicine stability test chamber, isolator, VHP sterilizer,Biological safety chamber, FFU, LAF, etc. | |
Temperature | 21-27*C (or as per required) |
Humidity | 30-60°C (or as per required) |
Application | Pharmaceutical factory, hospital, medical device factory, electronics factory, food factory,cosmetics factory, etc. |
Qualification Documents | CE GMP ISO |
Full Service | FAT and SAT Service, Professional Consultation, Training, 24 hours technical support |
Cleanrooms Airflow
When designing the airflow system for an ISO 7 modular cleanroom, several factors must be considered:
Air Changes Per Hour (ACH):
ISO Class 7 cleanrooms typically require 30-50 air changes per hour to maintain cleanliness.
The exact number depends on the cleanroom’s size, usage, and contamination sources.
Cleanrooms Installation
Cleanrooms Testing
Importance of testing
Clean room testing is extremely important to ensure product quality and the stability of the production environment. It can help to confirm whether the clean room meets the intended cleanliness requirements, and whether the various environmental indicators comply with the specified standards.
Testing Items
Suspended particles: Detects the number of suspended particles in the air in the clean room to ensure that the air cleanliness is up to standard.
Temperature and humidity: Monitor the temperature and humidity in the clean room to ensure environmental stability during the production process.
Noise: Evaluates the noise level in the clean room to minimize the impact on staff.
Static electricity: Detect static electricity buildup in the clean room to prevent damage to sensitive components from electrostatic discharge.
Microbial contamination: Detecting microbial levels in the clean room, especially critical for the healthcare industry.
FAQ
How is airflow managed in modular cleanrooms?
Airflow in modular cleanrooms is managed through a combination of HEPA filters, air handling units, and carefully designed duct systems. This setup ensures optimal air circulation and cleanliness.
What are the challenges of modular cleanroom design?
Modular cleanroom design faces several challenges:
- Balancing flexibility and compliance with regulations.
- Integrating complex systems efficiently.
- Ensuring adequate space for equipment and personnel.
These factors can complicate the design process.
How to assess cleanroom compliance with regulations?
Assessing compliance involves systematic audits and testing, focusing on:
- Environmental monitoring.
- Cleanliness standards.
- Personnel practices.
Documentation of findings is crucial for regulatory adherence and continuous improvement.
How to integrate automation in modular cleanrooms?
To integrate automation in modular cleanrooms:
- Implement automated monitoring systems for real-time data.
- Use robotics for material handling and processing.
- Employ software for tracking compliance and efficiency.
This enhances operational efficiency and reduces human error.
What are the key features of modular cleanrooms?
Key features of modular cleanrooms include:
- Quick installation and reconfiguration.
- Prefabricated components for easy assembly.
- Effective air filtration systems.
- Flexibility to meet diverse industry needs.
These attributes make them versatile for various applications.
What are the key regulations for cleanrooms?
Key regulations include:
- ISO 14644 standards for cleanliness.
- FDA requirements for pharmaceuticals.
- EU GMP guidelines.
- OSHA safety regulations.
Compliance with these standards is essential for operational success.
What is the difference between modular and traditional cleanrooms?
Modular cleanrooms are prefabricated and designed for flexibility, allowing easy reconfiguration. Traditional cleanrooms are typically built on-site and are less adaptable, often requiring longer installation times.
What are the features of a high-performance cleanroom?
High-performance cleanrooms typically feature:
- Advanced HVAC systems for precise climate control.
- Continuous monitoring of particulate levels.
- Enhanced air filtration capabilities.
- Energy-efficient designs for sustainability.
These features ensure optimal cleanliness and operational efficiency.
What are the best practices for cleanroom operation?
Best practices for cleanroom operation include:
- Regular training for all personnel.
- Strict adherence to gowning procedures.
- Continuous monitoring of environmental conditions.
- Routine maintenance of equipment and systems.
Following these practices ensures a compliant and efficient cleanroom environment.
How to perform cleanroom testing?
Cleanroom testing involves several key steps:
- Conducting viable and non-viable particle counts.
- Performing airflow visualization studies.
- Testing surface contamination levels.
- Monitoring temperature and humidity regularly.
These tests help maintain the required cleanliness standards.
How does a modular cleanroom work?
A modular cleanroom operates by using a controlled environment with filtered air. Prefabricated walls and systems facilitate quick assembly and adaptability to various operational needs.
What is the lifespan of a modular cleanroom?
The lifespan of a modular cleanroom typically ranges from 10 to 20 years, depending on maintenance and environmental conditions. Regular upkeep can significantly extend its operational life.
What are the benefits of using modular cleanrooms over conventional ones?
Benefits of modular cleanrooms include:
- Faster installation times compared to traditional builds.
- Lower overall construction costs.
- Greater adaptability for future changes in layout.
- Minimal disruption during installation and relocation.
These factors make them an attractive option for many industries.
How to create a cleanroom layout?
To create an effective cleanroom layout:
- Assess workflow and operational processes thoroughly.
- Define zones for personnel, equipment, and materials.
- Ensure compliance with industry regulations and safety standards.
A well-planned layout promotes efficiency and safety in operations.
What are the common applications of modular cleanrooms?
Common applications include:
- Pharmaceutical manufacturing processes.
- Biotechnology research and development.
- Aerospace component manufacturing.
- Electronics assembly and testing.
These applications benefit from the cleanroom's controlled environment.
How to design an ergonomic cleanroom workspace?
Designing an ergonomic cleanroom workspace involves:
- Assessing employee tasks and comfort needs.
- Incorporating adjustable workstations and tools.
- Ensuring adequate lighting and airflow.
This approach enhances productivity and reduces fatigue among operators.
How to implement a cleanroom maintenance schedule?
To implement a maintenance schedule:
- Identify critical maintenance tasks and their frequency.
- Set specific intervals for inspections### How to implement a cleanroom maintenance schedule?
To implement a maintenance schedule: - Identify critical maintenance tasks and their frequency.
- Set specific intervals for inspections and servicing.
- Document all maintenance activities for compliance and tracking.
This ensures the cleanroom operates optimally and meets regulatory standards.
How to ensure proper cleanroom airflow patterns?
To ensure proper airflow patterns:
- Design the layout to promote unidirectional airflow.
- Use strategically placed air diffusers and return grills.
- Regularly monitor airflow with specialized equipment.
These measures help maintain cleanliness and prevent contamination.
What is the role of cleanroom operators?
Cleanroom operators are responsible for:
- Maintaining cleanliness and adherence to protocols.
- Monitoring environmental conditions and equipment functionality.
- Performing routine inspections and documentation.
Their vigilance is essential for ensuring compliance and operational efficiency.
Factory Production Workshop Video
Factory Photo
Product Packaging And International Logistics
Product International Certification
Find Other Common Equipment Recommendations
-
Modular CleanRoom
US$9000-10000 USD/Unit
Min. Order:1 Set -
Air Shower
US$1000.00-5000.00 USD/Unit
Min. Order:1 Set -
Downflow Booth
US$3000-6000 USD/Unit
Min. Order:1 Set -
Clean bench
US$600-2000 USD/Unit
Min. Order:1 Set -
Air Filter
US$3-50 USD/Unit
Min. Order:1 Set -
Cleanroom Wall Panels
US$10-20 USD/sq.
Min. Order:1 Set -
Pass Box
US$200-500 USD/Unit
Min. Order:1 Set -
FFU
US$135-350 USD/Unit
Min. Order:1 Set -
Fume Hood
US$700-1500 USD/Unit
Min. Order:1 Set -
Cleanroom HVAC
US$5000-20000 USD/Unit
Min. Order:1 Set -
Clean room floor
US$5-20 USD/Sq.
Min. Order:1 Set -
Clean room ceiling
US$
Min. Order:1 Set