GMP Class A Clean Room_第2页
A GMP Class A cleanroom is an ultra-clean environment that meets the specific standards required for manufacturing sterile medicinal products under Good Manufacturing Practice (GMP) guidelines.
Particle Count: Equivalent to ISO Class 5 (3,520 particles per cubic meter for ≥0.5 µm)
Air Changes per Hour (ACH): 240-480 ACH
Airflow: Unidirectional (laminar flow)
Filtration: HEPA or ULPA filters with ≥99.97% efficiency for 0.3 µm particles
Pressure: Positive pressure relative to surrounding areas
Temperature: 18°C to 22°C (64°F to 72°F)
Relative Humidity: 40% to 60% (typical)
Personnel Gowning: Strict gowning and hygiene procedures
Critical Zones: Aseptic areas with higher cleanliness standards, often within a GMP Class B cleanroom
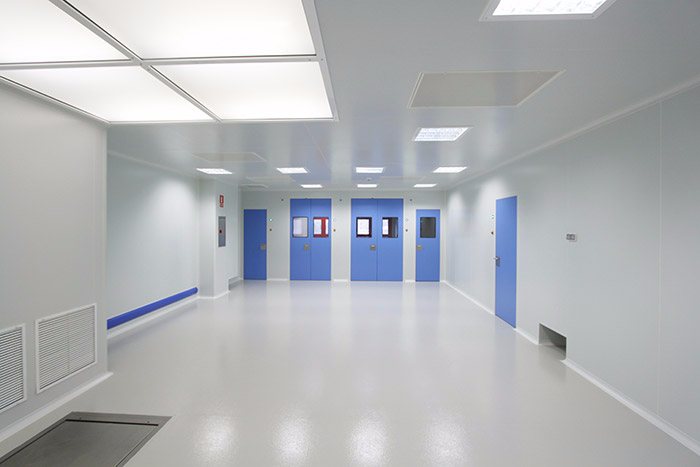
Clean room grade table
ISO Class FED STD 209E Equivalent | |||||||
ISO Class | Maximum Particles/m | FED STD 209E equivalent | |||||
≥0.1μm | ≥0.2um | ≥0.3um | ≥0.5um | ≥11m | ≥5um | ||
ISO1 | 10 | 2 | |||||
ISO2 | 100 | 24 | 10 | 4 | |||
ISO3 | 1,000 | 237 | 102 | 35 | 8 | Class1 | |
ISO4 | 10,000 | 2,370 | 1,020 | 352 | 83 | 3 | Class10 |
ISO5 | 100,000 | 23,700 | 10,200 | 3,520 | 832 | 29 | Class100 |
ISO6 | 1,000,000 | 237,000 | 102,000 | 35,200 | 8,320 | 293 | Class 1,000 |
ISO7 | 352,000 | 83,200 | 2,930 | Class10,000 | |||
ISO8 | 3,520,000 | 832,000 | 29,300 | Class 100,000 | |||
ISO9 | 35,200,000 | 8,320,000 | 293,000 | Room Air |
Comparison Table GMP/USP/ISO/FED209E | ||||||||||||
project | China GMP/Europe GMP | ISO | FED STD 209E | |||||||||
Suspended particles P/m3 | level | Static | dynamic | level | Static | level | dynamic | |||||
≥0.5um | ≥5μm | ≥0.5μm | ≥5μm | ≥0.5um | ≥5μm | ≥0.5um | ≥5μm | |||||
A | 3520 | 20 | 3520 | 20 | M3.5 | 3530 | 100 | 5 | 2220 | 20 | 100 | |
B | 3520 | 29 | 352000 | 2900 | - | - | 6 | 3520 | 29 | 1000 | ||
C | 352000 | 2900 | 3520000 | 29000 | M5.5 | 353000 | 10000 | 7 | 352000 | 2930 | 10000 | |
8. | 3520000 | 29300 | 100000 | |||||||||
D | 3520000 | 29000 | No regulations | No regulations | M6.5 | 3530000 | 100000 | 9 | 3520000 | 29300 | 100000 |
Comparison table of ISO grade standards and ventilation times | |
ISO Class | ACH(AIRCHANGE PER HOUR) |
ISO 3 | 360-540 |
ISO 4 | 300-540 |
ISO 5(GMP Class A) | 240-480 |
ISO 6(GMP Class B) | 50-60 |
ISO 7(GMP Class C) | 30-40 |
ISO 8(GMP Class D) | 15-25 |
GMP Class A Clean Room Airflow
Air Changes per Hour (ACH): ISO Class 5 cleanrooms typically require 240 to 480 air changes per hour. | Air Velocity: FFU vertical unidirectional (laminar) airflow. | Temperature and Humidity Control: Typical ranges are 20-24°C for temperature and 30-60% for relative humidity, but these may vary based on specific requirements. |
GMP Class A Clean Room wall
![]() | ||
Cleanroom Panel | Cleanroom doors and windows | Handmade rock wool panel |
◇ Size and appearance: Ensure that the size and shape of the product meet the design requirements and have no obvious defects. ◇ Physical properties: Such as compression, tension, impact resistance and other tests to ensure the strength and durability of the material. ◇ Surface treatment: Confirm that the surface is smooth, the coating is uniform, and there are no bubbles, peeling, etc. ◇ Test report: Fire and corrosion resistance test |
GMP Class A Clean Room Celling
|
| ||
|
|
GMP Class A Clean Room Floor
| ||
![]() | ||
| ||
|
Industry Applications of Class A Clean Room
Personnel and Gowning | Pharmaceutical | Biotechnology |
FAQ
What is GMP class A and B cleanroom environments?
GMP Class A and B cleanrooms are highly controlled environments used in pharmaceutical and biotechnology industries to ensure product sterility and quality. Class A cleanrooms provide the highest level of cleanliness, with stringent particle count limits and strict environmental control, typically used for critical processes like aseptic filling. Class B cleanrooms are slightly less stringent but still maintain a high level of cleanliness for non-critical operations, such as preparation and intermediate stages of sterile production.
What are the requirements for a Grade A clean room?
A: A Grade A cleanroom must meet the highest standards of cleanliness, with strict control over airborne particles, microbial contamination, and environmental conditions. It requires continuous monitoring of particle counts, air changes (typically ≥180 ACH), and maintaining positive pressure relative to surrounding areas. Personnel must wear appropriate cleanroom garments, and critical processes should be carried out in laminar flow hoods or isolators to prevent contamination.
What are the GMP cleanliness classifications?
GMP cleanliness classifications, based on ISO 14644-1 standards, categorize cleanrooms into different grades based on their particle concentration limits. The grades range from Class A (the cleanest) to Class D (less stringent). These classifications define the acceptable limits of particulate contamination in the air, air change rates, and cleanliness levels, with Class A being used for the most sensitive processes like aseptic filling and Class D for non-critical pharmaceutical production areas.
What is GMP in clean room?
GMP (Good Manufacturing Practice) in cleanrooms refers to the regulatory guidelines that ensure cleanroom environments are properly controlled to avoid contamination of products, particularly in industries like pharmaceuticals and biotechnology. GMP in cleanrooms involves adhering to strict cleanliness, environmental monitoring, equipment calibration, personnel gowning procedures, and cleaning protocols to ensure product safety, efficacy, and quality.
What is class A clean room?
Class A cleanroom is the highest cleanliness level defined by ISO 14644-1 and GMP standards, primarily used for sterile and aseptic operations in industries like pharmaceuticals and biotechnology. It maintains the strictest controls over airborne particles and microbial contamination, with extremely low particle count limits (3,520 particles/m³ for particles ≥ 0.5 microns) and high air change rates (≥180 air changes per hour). Class A cleanrooms are used for critical processes like aseptic filling or preparation of sterile pharmaceuticals.
What is a Class B clean room?
A Class B cleanroom is a controlled environment used for less critical areas of pharmaceutical production, where sterility is important but not to the level of Class A. It has slightly higher particle limits compared to Class A (up to 3,520 particles/m³ for particles ≥ 0.5 microns), and typically, the air change rate is around 30 to 60 per hour. Class B cleanrooms are commonly used for preparation areas, intermediate production steps, or areas where sterile products are handled but not directly processed.
How Do Cleanrooms Work?
Cleanrooms work by controlling and filtering the air to remove particulate contamination and maintain a controlled environment. The air is filtered through high-efficiency particulate air (HEPA) filters or ultra-low penetration air (ULPA) filters, with a continuous flow of clean air that is exchanged regularly to minimize contamination. Positive pressure ensures that contaminants from outside do not enter the cleanroom, and strict gowning and cleaning procedures are followed to further minimize contamination. Monitoring systems track particle levels, temperature, humidity, and microbial contamination to ensure the room remains within specified limits.
What is the difference between Grade A and Grade B clean rooms?
The main difference between Grade A and Grade B cleanrooms lies in their level of cleanliness and particle concentration limits. Grade A cleanrooms maintain the highest level of cleanliness, with more stringent particle count limits (3,520 particles/m³ for particles ≥ 0.5 microns) and are used for the most critical processes like aseptic filling. Grade B cleanrooms, while still maintaining a high level of cleanliness, have slightly higher particle count limits and are used for less critical operations, such as preparation or support functions in sterile production areas.
What is class C cleanroom?
A Class C cleanroom is a controlled environment that provides a moderate level of cleanliness for less sensitive processes, typically in the pharmaceutical or semiconductor industries. It has higher particle count limits (352,000 particles/m³ for particles ≥ 0.5 microns) compared to Class A and B rooms and requires air changes between 20 to 40 per hour. Class C cleanrooms are used in areas where sterile conditions are not as critical but where contamination must still be controlled to ensure product quality.
What is grade a area?
A Grade A area is a highly controlled, sterile environment within a cleanroom, where the most critical processes, such as aseptic filling or preparation of sterile drugs, are carried out. It is subject to the highest standards of cleanliness with very strict control over airborne particles and microbial contamination. This area typically requires the use of laminar flow hoods or isolators to prevent contamination, and the room must maintain positive pressure relative to surrounding areas.
What is cleanroom classification A?
Cleanroom Classification A refers to the cleanroom environment that meets the highest standards of cleanliness, as defined by ISO 14644-1 and GMP guidelines. It is used for the most sensitive operations, such as sterile drug preparation and aseptic filling, with strict limits on particle contamination (3,520 particles/m³ for particles ≥ 0.5 microns). This classification requires stringent air change rates, environmental monitoring, and controlled personnel gowning procedures to ensure sterility and prevent contamination.
What is the FDA classification of clean rooms?
The FDA classifies cleanrooms based on the level of contamination control required for the manufacture of sterile pharmaceutical products. The FDA follows the GMP guidelines, which align with ISO 14644-1 classifications, defining cleanroom grades from Class A (the cleanest) to Class D (the least stringent). Class A is used for aseptic processing, and Class B, C, and D are used for other phases of pharmaceutical production. These classifications ensure that cleanrooms meet the required standards for controlling contamination during the manufacturing of drugs and medical devices.
What is a Class C clean room?
A Class C cleanroom is a controlled environment used in less critical areas of pharmaceutical and other industrial processes where contamination control is important but not as stringent as in Class A or B rooms. It has a higher particle count limit (352,000 particles/m³ for particles ≥ 0.5 microns) and typically requires 20 to 40 air changes per hour. Class C cleanrooms are typically used for non-sterile processing and support areas where contamination levels need to be controlled, but aseptic conditions are not required.
What is the difference between clean room 100 and 1000?
The difference between Cleanroom 100 and Cleanroom 1000 lies in the allowable level of airborne particles. In a Class 100 cleanroom, the maximum allowable particle count for particles ≥ 0.5 microns is 100 particles per cubic foot. A Class 1000 cleanroom, on the other hand, allows up to 1,000 particles per cubic foot. This means Class 100 rooms are cleaner and provide a higher level of contamination control than Class 1000 rooms, making them suitable for more sensitive applications like semiconductor manufacturing and pharmaceutical production.
What are the classes of cleanroom?
Cleanrooms are classified into several grades according to the ISO 14644-1 standard, with each class defining the allowable concentration of airborne particles and environmental conditions. The main cleanroom classes are Class A, Class B, Class C, and Class D, with Class A being the cleanest and most controlled, used for critical processes like aseptic filling. Class B cleanrooms are for less critical operations, Class C is used for less sensitive processes, and Class D provides the least stringent cleanliness standards for non-critical manufacturing tasks.
What is a Class 10000 area?
A: A Class 10000 area is a cleanroom environment with a particle concentration limit of 10,000 particles per cubic foot for particles ≥ 0.5 microns. This is one of the lower cleanroom classifications and is typically used for non-critical manufacturing processes in industries like electronics or pharmaceuticals, where strict particle control is required but the environment does not need to be as clean as higher-class rooms (Class 100 or Class 1000).
What is class D clean room?
A Class D cleanroom is a controlled environment used for non-critical pharmaceutical and manufacturing operations. It has the least stringent cleanliness requirements among the GMP classifications, with a maximum allowable particle count of 2,920,000 particles/m³ for particles ≥ 0.5 microns. Class D cleanrooms typically require air changes of 20 to 30 per hour and are used for areas where contamination control is important but sterility is not as critical, such as intermediate processing steps.
What are the classification of pharmaceutical cleanrooms?
Pharmaceutical cleanrooms are classified based on their particle concentration limits and their ability to control contamination, in accordance with GMP and ISO 14644-1 standards. The classifications are typically Class A, Class B, Class C, and Class D, with Class A being used for the most critical sterile processes (like aseptic filling), Class B for less critical sterile production, Class C for non-sterile processing