Understanding CleanRoom Classifications
Class 10,000 vs Class 1,000: Key Differences
Cleanrooms are essential for maintaining controlled environments in various industries. The classification of A CleanRoom, such as Class 10,000 (ISO 7) and Class 1,000 (ISO 6), indicates the level of air cleanliness maintained within the facility. This article explores the key differences between these two classes, focusing on their specifications, applications, and operational requirements.
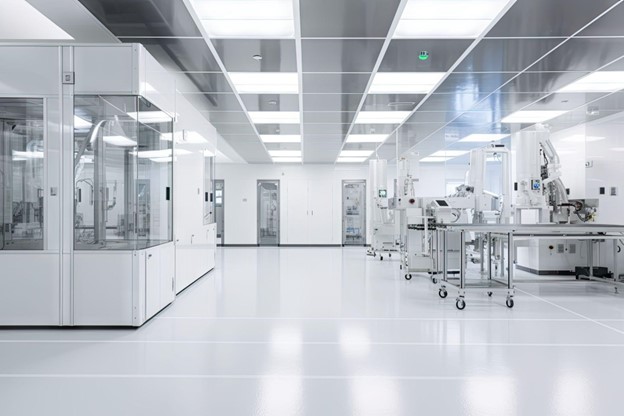
Modern cleanroom environment with controlled contamination levels
CleanRoom Classifications Overview
Class 10,000 (ISO 7) Cleanroom
Class 10,000 Cleanrooms allow up to 10,000 particles (0.5 micrometers or larger) per cubic foot of air. They provide a moderate level of cleanliness suitable for industries where minimal contamination is acceptable.
Example: In pharmaceutical manufacturing, a Class 10,000 cleanroom ensures an environment free from most contaminants without the extensive control required for highly sensitive processes.
Class 1,000 (ISO 6) Cleanroom
Class 1,000 cleanrooms provide a higher level of cleanliness by permitting up to 1,000 particles (0.5 micrometers or larger) per cubic foot of air. This classification is used for more stringent manufacturing environments.
Example: Semiconductor manufacturing requires Class 1,000 or cleaner environments to prevent defects in microchips caused by minute particles.
Key Differences
Feature | Class 10,000 (ISO 7) | Class 1,000 (ISO 6) |
---|---|---|
Particle Count | ≤ 10,000 particles/ft³ | ≤ 1,000 particles/ft³ |
air changes per Hour | ≥ 60 air changes | ≥ 180 air changes |
Typical Applications | Pharmaceutical production (non-sterile), general manufacturing | Semiconductor manufacturing, precision instrumentation |
Filtration | HEPA filters (99.97% efficiency at 0.3μm) | |
Operational Cost | Moderate | Higher |
Air Changes per Hour
The air change rate in cleanrooms is a critical factor in maintaining cleanliness.
Class 10,000 Cleanroom (ISO 7)
Requires at least 60 air changes per hour. This level of air circulation is sufficient for environments where moderate cleanliness is maintained.
Class 1,000 Cleanroom (ISO 6)
Typically requires 180 air changes per hour or more, ensuring a much higher turnover of air, which provides a cleaner space free of contaminants.
Design Insight: Deiiang™, with innovative input from product designer Deiiang Jason.peng, implements efficient HVAC designs to meet these air change requirements effectively.
Applications of Each cleanroom class
Class 10,000 Cleanrooms
- General manufacturing
- Pharmaceutical production (non-sterile)
- Medical device production with less stringent requirements
- Packaging operations
- Some food processing applications
Class 1,000 Cleanrooms
- Semiconductor manufacturing
- Precision instrumentation
- Research settings requiring lower contamination levels
- MicroElectronics assembly
- Optical lens manufacturing
Common Questions and Answers
Why are more air changes required in Class 1,000 cleanrooms?
Higher air change rates ensure that the cleanroom remains free of contaminants, crucial for environments needing greater cleanliness.
What role do HEPA filters play in cleanrooms?
They capture 99.97% of particles, maintaining air purity appropriate for the cleanroom's classification.
How does Deiiang™ enhance Cleanroom designs?
By incorporating innovative HVAC and filtration designs that ensure precise air quality control.
Are the operational costs higher for Class 1,000 cleanrooms?
Yes, due to the need for more stringent environmental controls and frequent air changes.
Can a facility upgrade from a Class 10,000 to a Class 1,000 cleanroom?
Upgrading requires reevaluating and enhancing air circulation, filtration systems, and monitoring protocols.
Conclusion
In summary, the main difference between Class 10,000 and Class 1,000 cleanrooms lies in their particle count limits and applications. Class 1,000 environments demand stricter control and more frequent air changes to maintain higher cleanliness, suited for critical applications. Utilizing advanced CleanRoom solutions from Deiiang™, designed by Deiiang Jason.peng, facilities can ensure compliance with these standards, enhancing operational efficiency.
References
- International Organization for Standardization. ISO 14644-1: Cleanrooms and Associated Controlled Environments.
- Deiiang™, Innovative Solutions in Cleanroom design.
- The Institute of Environmental Sciences and Technology (IEST), cleanroom classifications and Standards.
- U.S. Pharmacopeial Convention. USP Standards for Environmental Control in Cleanrooms.
- American National Standards Institute (ANSI). Cleanroom standards.
© 2023 Cleanroom classification Guide. All rights reserved.