I. Basic Concepts
A CleanRoom is a highly controlled environment designed to reduce the number of particles, microorganisms, and other contaminants in the air. According to the international standard ISO 14644-1, the cleanliness level of a cleanroom can range from ISO1 to ISO9, with the lower the level, the fewer particles allowed in the air. For example, the ISO1 standard allows only 10 particles per cubic meter of air (particle size ≥ 0.1 micron). Cleanrooms are widely used in industries such as Semiconductor manufacturing, pharmaceuticals, biotechnology, and aerospace to ensure product quality and experimental reliability.
II. Working Principles
A cleanroom achieves a clean environment through a highly controlled air circulation and filtration system. The air is usually treated with a high-efficiency filter (HEPA or ULPA) to remove more than 99.97% (HEPA) or 99.999% (ULPA) of contaminants of 0.3 microns and larger particles. Air circulates through the ventilation system at a certain flow rate (usually 0.45 m/s) to form laminar or turbulent flow, so that particles are removed. According to ISO 14644-3 standard, the effectiveness of the clean room needs to be ensured by regular monitoring and testing to achieve the predetermined cleanliness level.
III. Technical parameters
Cleanliness
Cleanliness is one of the most important technical parameters of the clean room, usually expressed in ISO grades. According to iso 14644-1, the maximum number of particles allowed in the air is as follows:
| ISO| 0.1 micron particle | 0.2 micron particle | 0.3 micron particle | 0.5 micron particle | 1.0 micron particle | 5.0 micron particle |
| ISO1 | 10 | 2.4 | 1 | 0.35 | 0.003 | 0 |
| ISO5 | 3,520 | 832 | 29 | 8 | 3 | 0 |
Air volume
The air volume design of A Clean Room is usually measured in air changes per hour (ACH). The ACH of a standard Clean Room is generally between 300 and 600, depending on the different cleanliness requirements. For example, an ISO5 cleanroom may need to have 600 air changes per hour to ensure that its cleanliness standards are maintained.
Temperature
The temperature of a cleanroom is usually maintained between 20°C and 24°C to accommodate most industrial applications. In some specific applications, the temperature may need to be more strictly controlled to ensure the stability of the product or experiment.
Humidity
Humidity control between 30% and 60% is a common standard to prevent static electricity accumulation and product quality degradation. For some applications, humidity may need to be further refined, such as in the pharmaceutical industry, where relative humidity is usually required to be less than 30%.
Pressure difference
In order to prevent contaminants from escaping, cleanrooms are usually kept at a negative pressure. Generally speaking, the pressure difference should be maintained between 15Pa and 50Pa to ensure that external air does not infiltrate the clean environment and affect the cleanliness.
IV. Applications
The uses of cleanrooms are very wide, mainly including the following areas:
1. Semiconductor manufacturing
used in the production of integrated circuits and Electronic components, requiring extremely high cleanliness to prevent defects.
2. Pharmaceutical industry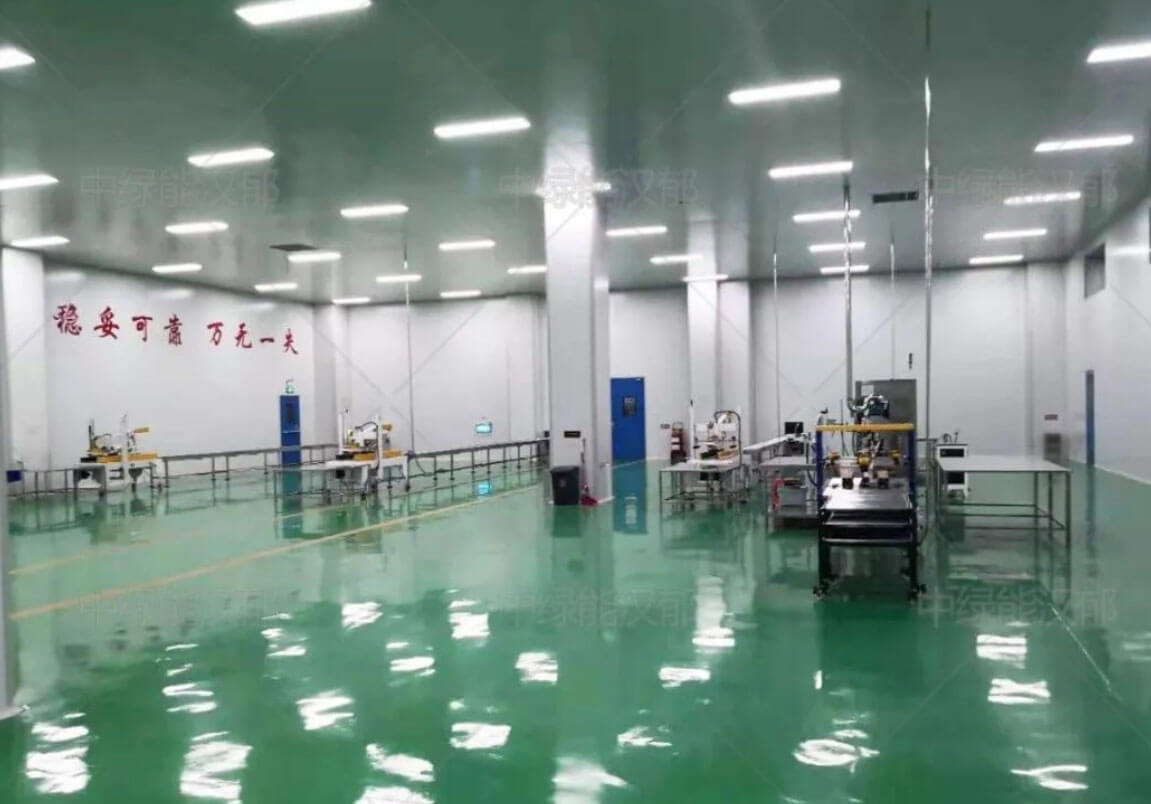
used for the production and experimentation of sterile drugs to ensure that the products are not contaminated by microorganisms.
3. Biotechnology
used for cell culture and genetic engineering operations to provide a sterile and controlled environment.
4. Aerospace
used for the assembly of components for aircraft and spacecraft to ensure the reliability of equipment in extreme environments.
V. Maintenance
Maintenance of clean rooms is essential to ensure their effectiveness and reliability. Common maintenance measures include:
1. Regular cleaning
It is recommended to use special dust-free cleaners and tools for cleaning, and avoid using cleaners that may generate particles.
2. Filter replacement
Depending on the frequency of use and environmental conditions, HEPA/ULPA filters should be checked and replaced regularly, usually every 6 to 12 months.
3. Monitoring system
Use particle counters to monitor air cleanliness regularly to ensure that the required ISO level is achieved.
4. Equipment calibration**4. **Equipment calibration
Ensure that all monitoring and control equipment (such as thermometers, hygrometers, pressure gauges, etc.) are calibrated regularly to ensure the accuracy of the data. It is usually recommended to perform calibration once a year to meet the requirements of ISO 17025.
5. Training and Records
Regularly train cleanroom operators to ensure that they understand the cleanroom operating specifications and measures to deal with emergencies. At the same time, establish detailed maintenance records, including equipment inspection, cleaning, filter replacement and monitoring results, for traceability and improvement.
6. Air Flow Check
Regularly check the airflow pattern of the modular cleanroom to ensure that the airflow meets the design requirements and avoids dead corners and local contamination. Using methods such as smoke testing to monitor airflow conditions can help identify potential air duct problems.
7. Emergency Plan
Develop emergency plans to deal with emergencies such as equipment failures and contamination incidents, ensure that there are clear processing procedures and responsibilities, and ensure the safety and cleanliness of the cleanroom.
Related Standards and Specifications
In the design, construction and operation of cleanrooms, it is essential to follow relevant standards and specifications. The following is a list of commonly used domestic and international standards and specifications:
| Standard/Specification | Description |
| ISO 14644-1 | Classification of cleanroom and related controlled environments by cleanliness level |
| ISO 14644-3 | Procedures for monitoring cleanrooms and related controlled environments |
| GB 50457-2008 | Specification for Cleanroom design and construction (Chinese national standard) |
| GMP (Good Manufacturing Practice) | Good manufacturing practice for pharmaceutical products, applicable to the pharmaceutical industry |
| IEST-RP-CC012.2 | Guide to the use and calibration of particle counters |
| ISO 9001 | Quality management system requirements for cleanroom operations and management |
As an important infrastructure in the fields of industry and scientific research, the design and maintenance of cleanrooms directly affect product quality and experimental results. In the context of increasingly stringent global requirements for high-quality products and environmental safety, it is particularly important to establish and maintain an efficient cleanroom. Through scientific management, regular maintenance and compliance with international standards, we can ensure that the clean room is always in the best condition, thus providing a reliable and clean production and experimental environment for all walks of life.