Clean rooms are indispensable facilities in modern industry and scientific research, and are widely used in Electronics, optics, biopharmaceuticals, medical devices, food, new energy, and aviation. Building a clean room that meets international and domestic standards requires not only scientific planning and design, but also strict construction and maintenance. The following are detailed steps and precautions for building a clean room.
I. Determine the purpose of the clean room
Before building A Clean Room, you first need to
clarify its purpose. The application areas of modular clean rooms include electronic
product manufacturing, optical instrument production, biopharmaceuticals, etc.
Each industry has different requirements and standards for clean rooms. For
example:
Electronics industry
For microelectronic components, the cleanliness of the clean room usually needs to reach ISO level 5 or higher, and the number of dust particles must be controlled to no more than 3,200 particles per cubic meter (0.5μm particles).
Biopharmaceuticals
According to the requirements of the Good Manufacturing Practice for Pharmaceuticals (GMP), it is usually necessary to reach ISO level 7 or above to ensure the sterility of the drug production process.
Aerospace
Cleanliness requirements usually reach ISO level 6 or higher to prevent tiny particles from affecting spacecraft.
After clarifying the purpose, it can help to rationally plan the design and construction of the clean room to ensure that it can meet specific industrial standards.
II. Determine the location of the clean room construction
When determining the location of the clean room, multiple factors need to be fully considered. First, the area and floor height are key indicators. The effective area of the clean room should be planned according to actual production needs, and each workbench or workstation is usually required to have at least 10 square meters of net space. In addition, the floor height should not be less than 4.5 meters to ensure air circulation and equipment installation flexibility.
When choosing a location, the following factors
should also be considered:
Environmental pollution sources
Avoid proximity to pollution sources such as factories and roads to reduce the intrusion of external particles.
Traffic convenience
Ensure that materials are unobstructed in and out, and facilitate the transportation of raw materials and finished products.
Infrastructure
Such as water, electricity, gas supply and emission systems, must meet the needs of clean room construction.
By reasonably selecting a construction site, the risks in later operations can be effectively reduced.
III. Determine the technical parameters of the clean room
According to the actual use of the clean room, a
series of technical parameters need to be defined to ensure the cleanliness and
stability of the environment. These parameters include:
Cleanliness
According to the ISO 14644-1 standard, the cleanliness level of the clean room ranges from ISO 1 to ISO 9, such as ISO 5 and ISO 7, which require the control of the number of particles of different sizes.
Air volume
The ventilation frequency of the clean room should usually be more than 20 times per hour to ensure efficient circulation of indoor air.
Temperature
It is generally required to be maintained between 18-24℃ to avoid temperature fluctuations affecting product quality.
Humidity
Relative humidity should be controlled between 30%-60%. Too high or too low may affect material performance.
Pressure difference
It is usually required to maintain a certain negative pressure difference between the inside and outside of the clean room to prevent external air from infiltrating. The pressure difference is generally maintained between 10-20Pa.
The reasonable setting of these technical parameters directly affects the function and effect of the clean room.
IV. Clean room construction drawing design and construction
The construction drawing design of the clean room is extremely important, involving the layout and coordination of multiple systems. Mainly including:
1. Partitions and ceilings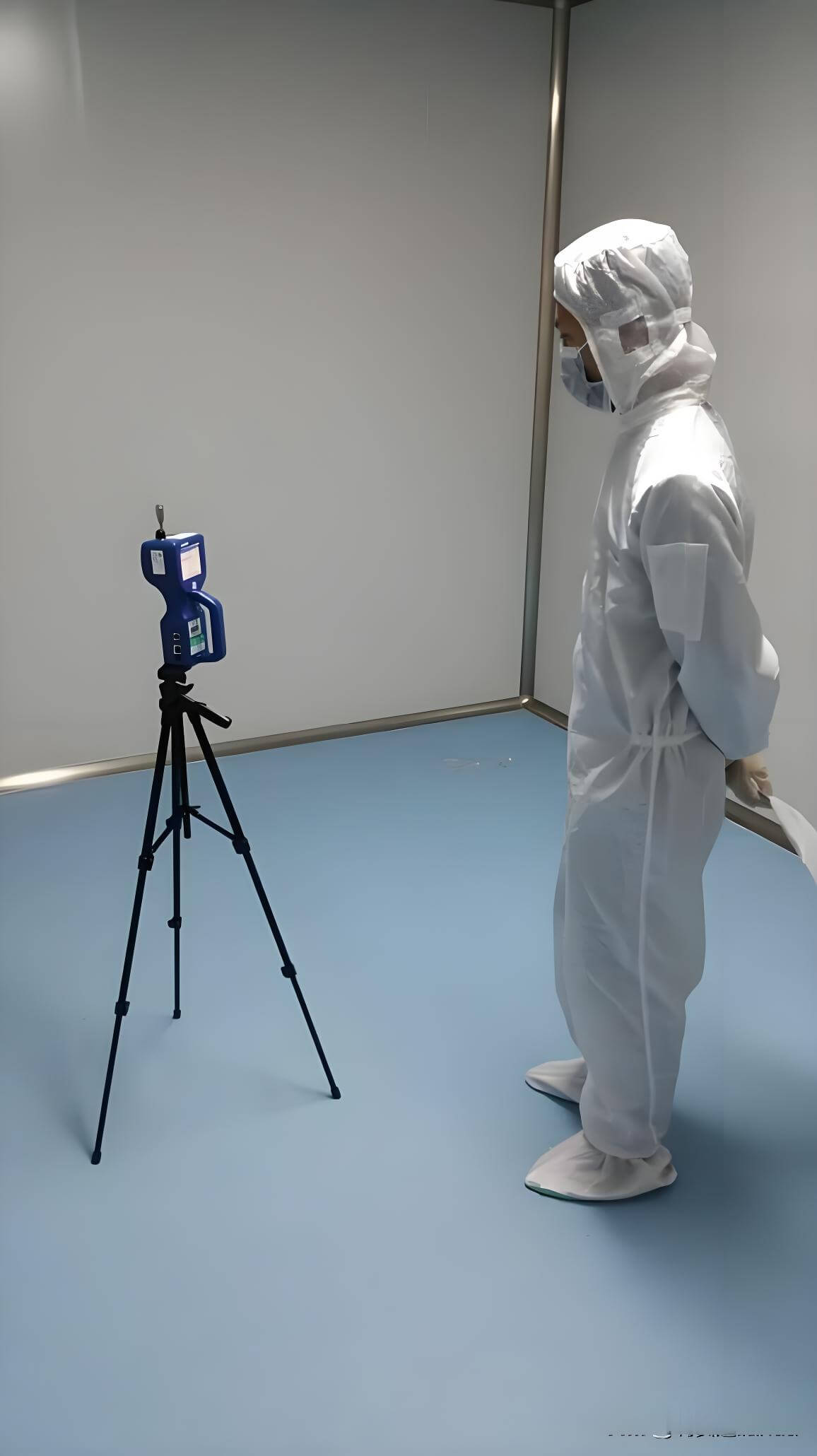
Use dust-free materials and structures to ensure the integrity and sealing of the modular clean room.
2. Ventilation and purification system
Design an efficient air handling unit (AHU) to ensure the continuous supply of clean air and the effective discharge of exhaust gas.
3. Electrical circuit system
Equipped with electrical facilities that meet explosion-proof and anti-static standards to ensure safety.
4. Fire protection system
Designed in accordance with the "Building Design Fire Protection Code" to ensure the safety of the clean room.
5. Ground engineering
: Anti-static and easy-to-clean materials are required for the ground to avoid dust accumulation.
Through scientific and reasonable construction drawing design and implementation, the function and safety of the clean room can be ensured.
V. Clean room Testing
After the clean room is built, a comprehensive test is required to verify whether its performance meets the design standards. The inspection contents mainly include:
Particle counting
Use a particle counter to measure the number of indoor particles to ensure that the designed cleanliness level is achieved. For example, the number of 0.5 micron particles in an ISO 5 Clean room should not exceed 3,200 per cubic meter.
Air flow test
Use smoke testing or thermal imaging to verify whether the air flow is uniform, ensure that there are no dead corners and air flow short circuits, so as to ensure that clean air effectively covers each working area.
Temperature and humidity monitoring
Use a high-precision thermometer and hygrometer to confirm whether the indoor temperature and relative humidity are within the set range and remain stable.
Pressure difference test
Test the pressure difference between the clean room and the external environment to ensure that it is maintained between 10-20Pa to prevent external contaminated air from entering.
All test results should be recorded and compared with national and international standards, such as ISO 14644 and "Design and Construction Specifications for Clean Rooms and Related Controlled Environments (GB 50073)", etc., to ensure that the functions and effects of the clean room meet the relevant requirements.
VI. Cleanroom Maintenance
The maintenance of cleanrooms is an important part of ensuring their long-term stable operation, which mainly includes the following aspects:
1. Regular cleaning
Develop a detailed cleaning plan, regularly clean the inside and outside of the cleanroom, use special cleanroom cleaners and tools, and avoid using cleaning materials that produce particulate matter. It is generally recommended to perform a comprehensive cleaning once a week, and perform daily cleaning of key areas such as workbenches and floors.
2. Equipment maintenance
Regularly inspect and maintain ventilation and purification systems, air conditioning equipment, monitoring instruments, etc. to ensure the normal operation of the equipment. The maintenance cycle of the equipment can be formulated according to the frequency of use and operating status, and a comprehensive inspection is usually performed once a quarter.
3. Environmental monitoring
Continuously monitor the temperature, humidity, pressure difference and cleanliness of the cleanroom to ensure that it is always in the set working state. An online monitoring system can be used to record and alarm in real time to ensure that any abnormal situation can be handled in a timely manner.
4. Employee training
Regularly train cleanroom operators to improve their understanding of cleanroom operating procedures and maintenance precautions, and ensure that all personnel can comply with the operating specifications of the cleanroom. The training content should include personal protection, equipment use, cleaning procedures and emergency measures.
Through the above systematic maintenance measures, the service life of the clean room can be effectively extended, ensuring that it always remains in an ideal working state and meets the high standards of production and research.
Related standards and specifications
In the process of establishing a clean room, the following domestic and international standards and specifications should be referred to to ensure the scientificity and rationality of design, construction and operation:
| Standard/Specification | Type | Content |
| iso 14644-1 | International Standard | Cleanliness Level of Clean Rooms and Related Controlled Environments |
| GB 50073 | Domestic Standard | Design and Construction Specifications for Clean Rooms and Related Controlled Environments |
| GMP | Domestic Standard | Good Manufacturing Practice for Pharmaceuticals |
| ISO 14644-3 | International Standard | Testing and Monitoring of Clean Rooms and Related Controlled Environments |
| NFPA 70 | International Standard | National Fire Protection Association Electrical Code |
| iso 14644-2 | International Standard | Monitoring Procedures for Clean Rooms and Related Controlled Environments |
By following the above standards and specifications, it is possible to ensure that the design, construction and operation of clean rooms meet regulatory requirements, minimize the risk of product contamination, and improve production efficiency and quality.