Process Validation in Pharmaceutical Cleanroom engineering
Ensuring Quality and Compliance in Manufacturing Processes
What is Process Validation?
Process validation refers to specific validation activities performed on a manufacturing process, ensuring it consistently produces a quality drug product. It is distinct from other validations like cleaning validation.
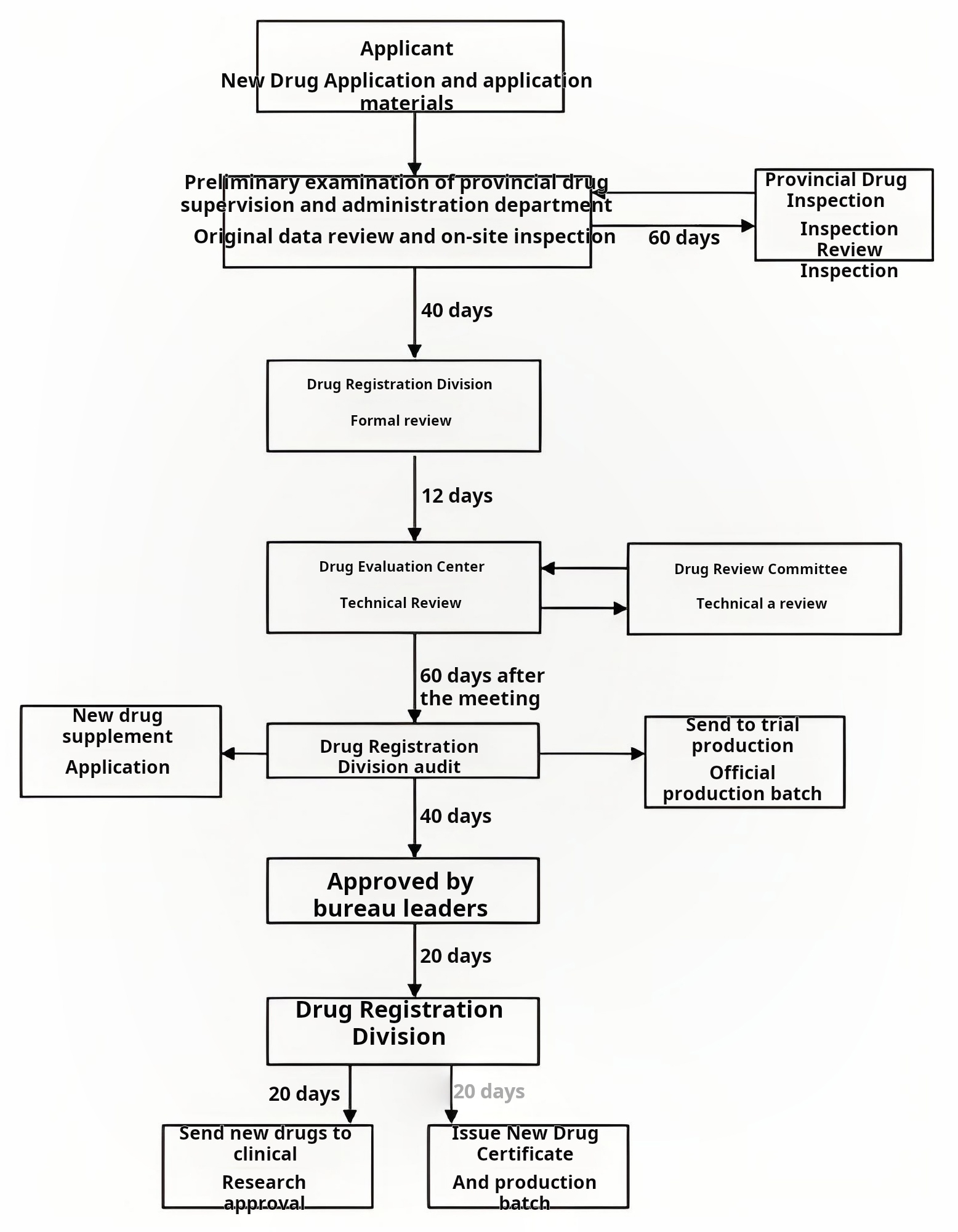
Figure 1: Process Validation in Pharmaceutical Manufacturing
Three Phases of Process Validation
- Phase 1 – Process Design: Developing and documenting a manufacturing process for commercial production.
- Phase 2 – Qualification: Including facility design, utilities, equipment qualification (IQ, OQ, PQ), and process performance qualification.
- Phase 3 – Continued Process Validation: Ongoing validation to maintain process consistency.
Initial Phase: Process Design
The process design phase is the foundation of any process validation protocol, aiming to develop a manufacturing process that consistently produces quality drug products for commercial use.
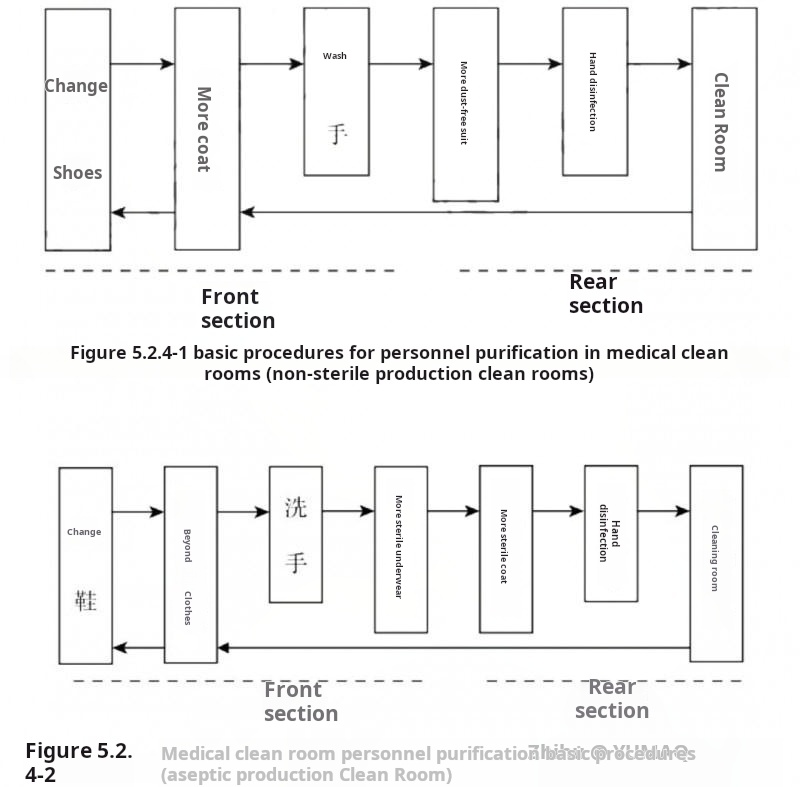
Figure 2: Process Design in a Pharmaceutical Cleanroom
Key Considerations in Process Design
- Critical Product Attributes: Determined during early product development, these are key factors affecting drug quality.
- Scale-Up Challenge: Maintaining quality when moving from small-scale lab production to large-scale commercial manufacturing.
- Equipment Consideration: Planning for equipment that will be used in commercial production during lab experiments.
- Documentation: Rigorous documentation of all conditions, processes, and decision-making factors.
Documented Conditions Example
Condition | Description |
---|---|
Manufacturing Temperature | Controlled temperature environment to ensure chemical stability |
Container Pressure | Monitored pressure levels in production containers |
Production Time | Defined cycle times for each manufacturing stage |
Why Process Validation Matters
Proper process validation, starting with the initial process design phase, is crucial for ensuring pharmaceutical products meet the highest quality standards. It minimizes variability, ensures regulatory compliance, and most importantly, guarantees patient safety.