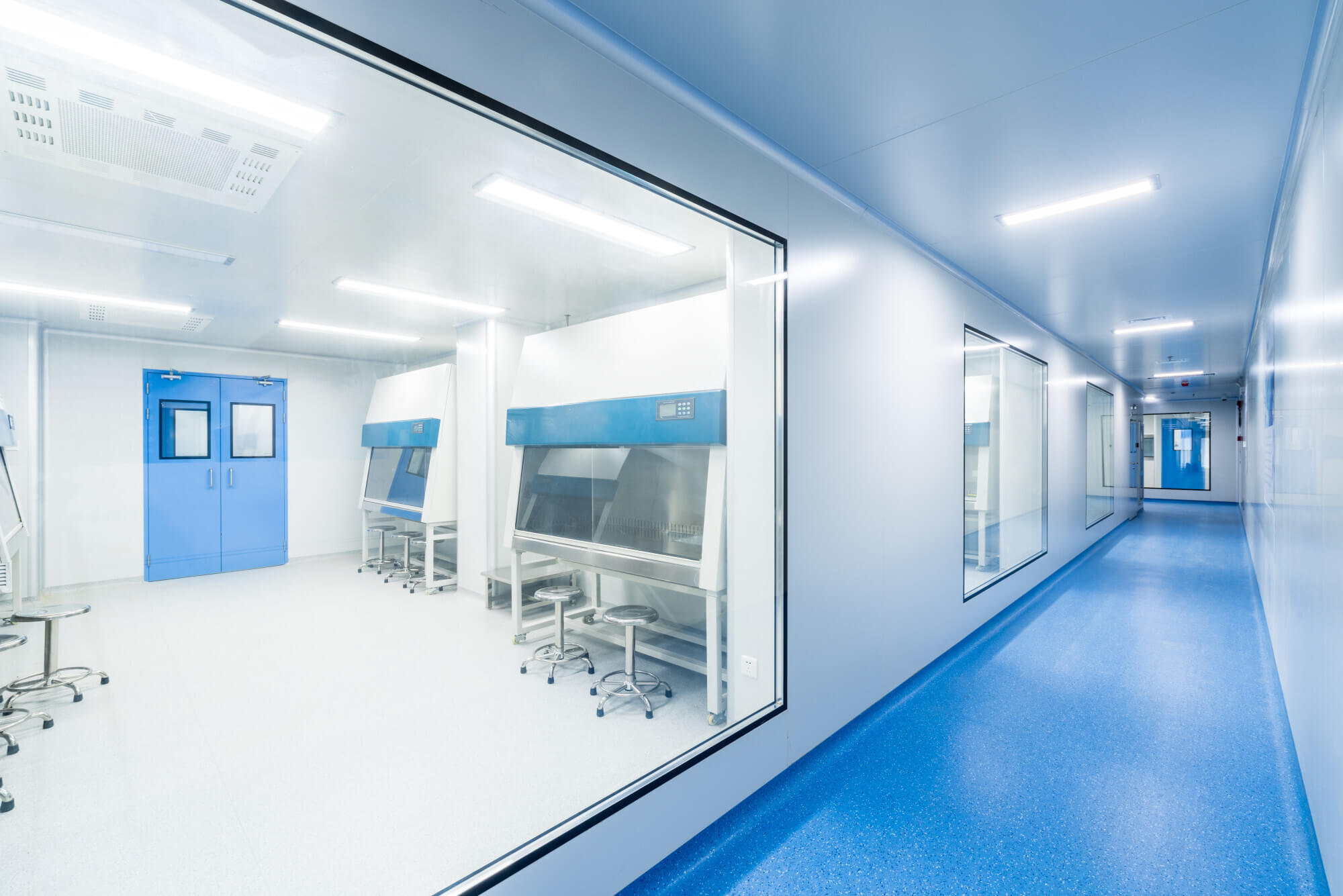
I. Hygiene quality policy and objectives
1. Hygiene quality policy
Always adhere to the principle of "getting things done right the first time", produce zero-defect, healthy products, serve the country with truth, and contribute to human society.
2. Hygiene quality objectives
Improve the hygiene quality assurance system and keep it running effectively. The qualified rate of products leaving the factory reaches 100%.
II. Hygiene management structure and responsibilities
1. Hygiene management structure:
Deputy general manager of quality |
General manager |
Quality director |
Production director |
District health director |
Logistics director |
2. Hygiene responsibilities of each organization
Position | Responsibilities |
---|---|
General manager | Responsible for formulating the company's hygiene quality goals and policies, as well as the hygiene functions and responsibilities of each functional department, organizing the establishment of a hygiene quality system, and responsible for the hygiene status of the company's products. |
Deputy general manager of quality | Responsible for the overall product hygiene management during the production process, organizing and coordinating the hygiene quality work of each functional department, and responsible for supervision. |
Quality director | In charge of product hygiene quality work during the production process, specifically responsible for daily quality management, and the drafting, modification, and interpretation of hygiene quality documents. Responsible for the development, research and promotion of new technologies, new processes and new products, and responsible for supervision. |
Production department director | Assist the general manager in implementing the production plan and labor allocation, ensure that the production tasks are completed on time, and be responsible for the maintenance, upkeep, renewal and transformation of the workshop workers, equipment and facilities. |
Quality department | It is the quality management department of the company and the daily office of the company's hygiene quality management leadership group. Specific responsibilities: conscientiously implement the policies and goals of hygiene quality, formulate product processes and standards, conscientiously manage process control process hygiene and factory hygiene, conduct random inspections on the cleanliness of equipment and tools that come into contact with products, and be responsible for employee training. |
Factory hygiene manager | Responsible for supervising toilet cleaning, road greening, ditch hygiene, and doing a good job in fly and rat prevention. |
Logistics department director | Keep records of the entry and exit of warehouse materials, and keep the warehouse clean and well ventilated. |
III. SSOP Plan
(I) Safety of Processing Water
1. Testing
The Quality Department sends the processing water to the Health and Epidemic Prevention Station for a full water quality and sanitation test every six months. It can only be put into production after it meets the national drinking water standard (GB 5749-2006).
The Quality Department conducts routine testing of processing water once a month. The test items include: color, smell, taste, pH value, visible objects, residual chlorine, total bacteria count, coliform group, etc.
National drinking water standard: GB 5749-2006.
Microbial inspection standards.
The total bacteria count and coliform count test are in accordance with: GB/T4789.5-2003If one of the microbial inspection results is unqualified, it will be judged as unqualified.
For each chlorination process in the process Operation procedures, the operator shall conduct testing every day as required.
The water used to clean empty cans must also meet the national drinking water standards.
The water used for soup must be treated to meet the pure water standards.
2. Drainage
The sewage discharge in the workshop is unobstructed, and there is no garbage, scraps, raw materials and other debris in the drainage channel, and the cleaning and disinfection are recorded according to regulations.
The sewage discharge in the factory area is unobstructed
3. The water reservoir
should be sealed, dustproof and safe to ensure that the stored water source is not polluted. The water reservoir is cleaned and disinfected every three months. The cleaning and disinfection procedures are as follows: remove debris-brush off moss--wash with water--spray with 300ppth effective chlorine solution--wash with water, and keep records of residual chlorine and pH value detection.
4. Identification
According to the actual situation of water pipeline laying, draw a water supply network diagram and sewage discharge pipeline distribution diagram of the processing workshop.
The processing water pipeline, pure water pipeline and steam pipeline are distinguished by green, blue and red respectively. The soft water pipes used in the workshop are hung on the wall with a rear plate.
Each water pipe outlet is numbered and a permanent identification plate is hung.
5. Regularly check
the cross-connections of hard pipes between the processing water pipeline and the pure water pipeline and sewage pipeline every half month.
6. Corrective measures
If it is found that the water source used no longer meets the requirements, the water source must be stopped immediately and the products using this water source must be evaluated. The water source can only be used after it is re-tested and qualified. If the inspection fails at ordinary times, a disinfection plan must be formulated and continuously monitored, and normal inspections must be conducted after the indicators are normal.
Faucets with anti-siphon devices must be used to prevent contamination caused by siphon backflow.
7. Records
Water quality analysis report issued by the control center.
Regular water quality and sanitation inspection records.
Daily sanitation inspection records.