This management system is specially formulated to effectively control the process hygiene management of clean room tooling and mold cleaning, material cleaning, operating table, site, wall, ceiling cleaning, cleaning and storage of cleaning tools, clean room (area) air disinfection, disinfectant selection, and use management.
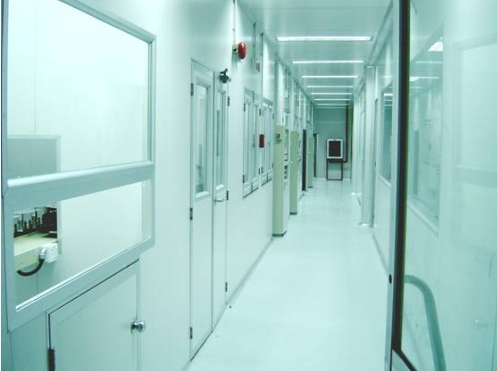
Figure 1: Clean room environment
Scope
This management system is used for clean room process hygiene management in medical device production facilities and other controlled environments requiring strict contamination control.
Basis
This document is formulated in accordance with the "Medical Device Production Quality Management Specification" and "Clean Workshop Management Control Procedure".
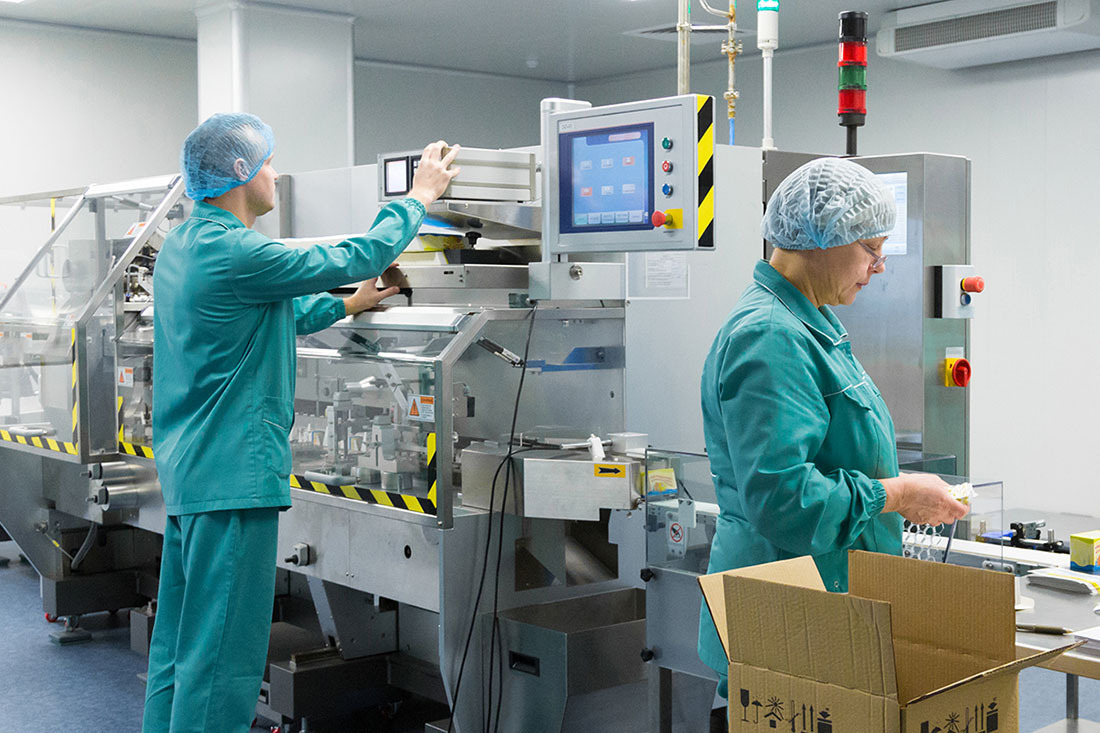
Figure 2: Clean room process hygiene management
Detailed Procedures
4.1 Tooling and Mold Cleaning
- Tooling and molds should be thoroughly cleaned and disinfected when used for the first time
- Clean once before each use and after production
- Tooling and molds should be cleaned with special rags and plastic brushes that do not shed fibers (use appropriate detergent when necessary), and purified water should be used for cleaning
4.2 Material Cleaning
- Materials that need to Enter the clean room should be unpacked outside the clean room, cleaned with a clean rag, and then stored in the material storage room to prepare for entering the clean room
- Materials and products to be packaged must be sent into the clean room through the transfer window after unpacking. Confirm that the inner and outer doors of the transfer window are interlocked and the UV light is effective before opening the door and quickly putting the items into the transfer window and closing it, and turning on the UV light. The items placed in the transfer window must stay in the transfer window for at least 5 minutes before they can be taken out of the transfer window, and the door and UV light must be closed
4.3 Cleaning of Operating Tables, Sites, Walls and Ceilings
- Clean from top to bottom and from inside to outside. Always wipe in overlapping long straight lines instead of scraping in circles. Always clean from the cleanest area to the dirtiest area
- Before and after production, use wet cleaning cloths, mops and other tools to remove dust and stains on the surface of operating tables, floors, doors and windows. Use brushes and detergents to scrub and remove dirt where dirt accumulates. Use disinfectants to disinfect when necessary
- Thoroughly clean and disinfect the clean area once a month (including disinfection of walls and ceilings)
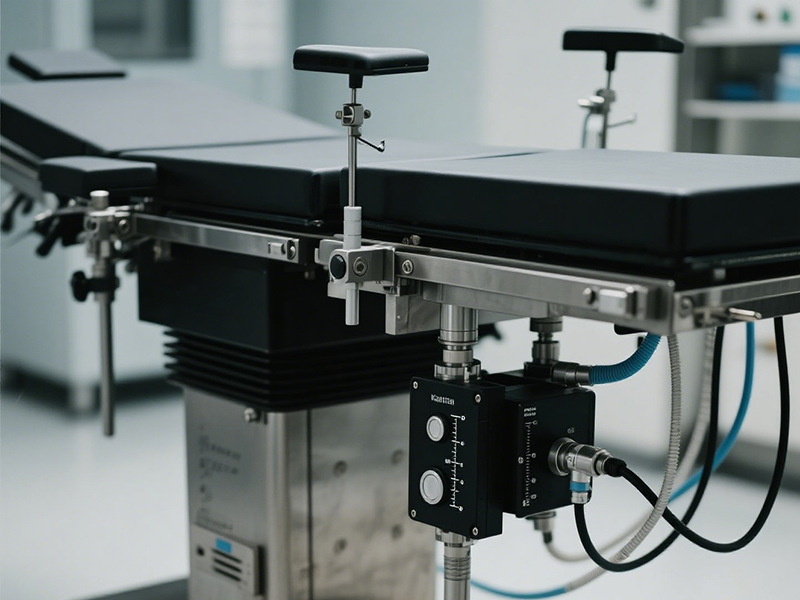
Figure 3: Operating table in clean room
4.4 Cleaning and Storage of Cleaning Tools
- Clean rags should be used in different categories, and all types of cleaning tools should be cleaned and disinfected in different categories
- Cleaning of rags: Soak in a basin containing 5% detergent for 5 minutes, gently rub and clean with your hands, take out and wring dry, and pour out the cleaning liquid in the basin, and rinse with drinking water. Rinse twice with purified water, take out and wring dry, and let dry naturally
- Disinfection of rags: Wash and wring them, then soak them in a basin containing 75% ethanol solution or 0.2% chlorhexidine for 30 minutes, take them out and wring them out, and hang them on the sanitary ware rack
- Cleaning of plastic brushes: Soak in a basin containing 5% detergent for 5 minutes, then rinse with purified water, store in the tool cleaning room, and let dry naturally
- Clean area cleaning tools are cleaned once after each use in the tool cleaning room
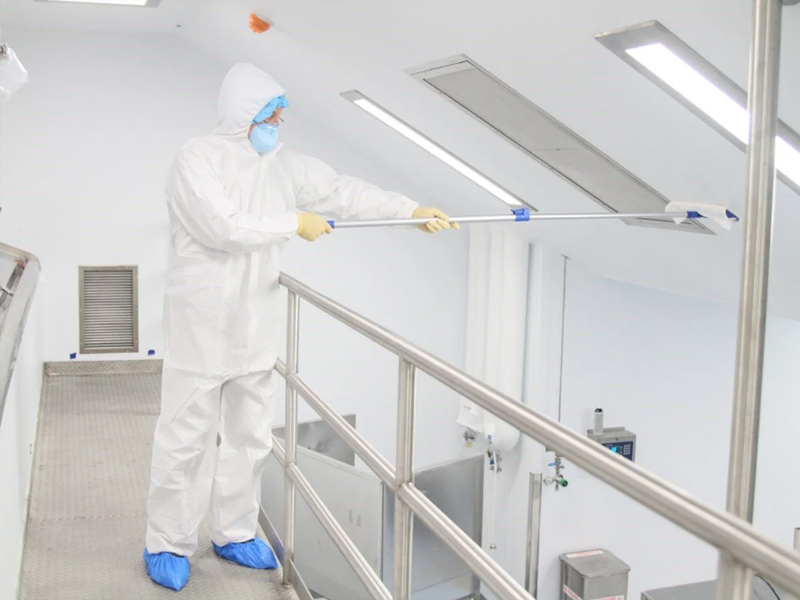
Figure 4: Clean room cleaning tools
4.5 & 4.6 Disinfection & Disinfectant Management
Monthly Procedures:
- Strengthen disinfection once a month, and irradiate each area with ultraviolet light for 40 minutes
- Disinfectants in clean rooms are rotated monthly
Disinfectant Usage:
- Use 0.2% chlorhexidine and 75% ethanol for hand disinfection
- Use 75% ethanol, 0.2% chlorhexidine, and 3% hydrogen peroxide for equipment surfaces and tools
- Use 0.2% chlorhexidine and 75% ethanol for floor, walls, and ceiling disinfection
- Use ultraviolet light for air disinfection
- The water used to prepare the disinfectant is purified water, use within fifteen days
- Label containers with name and preparation date
Disinfectant Rotation Schedule
Important Note:
All disinfectants must be prepared with purified water and used within 15 days of preparation. Containers must be clearly labeled with preparation date and contents.
Key Hygiene Management Principles
Consistency
Follow procedures consistently before, during, and after production
Contamination Control
Clean from cleanest to dirtiest areas using proper techniques
Tool Segregation
Use dedicated tools for specific areas and purposes
Documentation
Record all preparation and usage of disinfectants
Clean Room Hygiene Management System | Based on Medical Device Production Quality Management Specification
All procedures must be followed precisely to maintain clean room integrity and product safety