Cleanroom Management Specification Version 5
-
Author:Jason Peng
-
Cleanroom Engineering Technology Manager of Deiiang Company.
Product R&D Manager of GDC Inc. Cleanroom Equipment Manufacturing Company.
Executive Director of Guangdong Cleanroom Industry Association of China.
Engaged in R&D of related products for 15 years, with rich relevant technical experience
-
2024-11-27 | Visits:
Cleanroom Management Specification Version 5.0
PURPOSE
Maintain production order & product quality
SCOPE
All production workshop staff
Introduction
This specification establishes procedures to maintain production order, improve labor productivity, ensure product quality, and facilitate smooth operations. All production workshop staff must comply with these regulations.
1
Morning Meeting System
- Attendance at 8:00 AM meeting is mandatory without late arrival or early departure
- Employees must line up neatly and listen attentively to supervisors
- Meetings limited to 15 minutes duration
- Immediate return to work stations after meeting
Cleanroom Protocols for Outsourced Staff
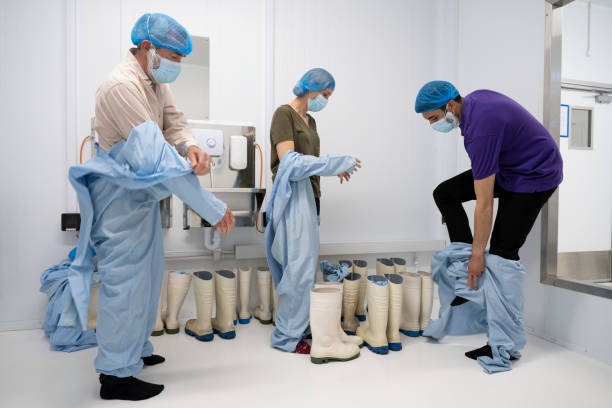
Meeting procedures and expectations for all personnel
2
Leave System
Employee leave procedures and approval authority follow established factory regulations.
Approval Process
- Submit leave request in advance
- Approval required from direct supervisor
- Documentation for extended medical leave
3Cleanliness & Sanitation System
Entry Procedures
- Change shoes before entering
- Change into clean clothes in locker room
- Cover all hair completely
- Wash and disinfect hands
- Pass through air shower before entering work area
Prohibited Items & Actions
- No tea, food, or beverages in work area
- No smoking, chewing gum, or eating snacks
- No cosmetics, earrings, rings, watches or accessories
- No touching exposed skin surfaces
Personal Hygiene Requirements
- Frequent hair and nail trimming
- Regular bathing to maintain personal hygiene
- No personnel with infectious diseases may contact products
- Annual physical examination for all production staff
Cleanroom personnel management
4
Workshop Production Order Management
Operational Procedures
- Cooperate with team members and follow supervisor instructions
- Conduct self-inspection during operations
- Report issues immediately to team leader
- Operate strictly according to SOP
Workshop Conduct
- No visiting posts, chatting, or phone use during work
- Team leader approval required to leave station
- Organize work surface before shift end
- Complete shift handover procedures
Equipment & Tools
- Strict adherence to equipment maintenance protocols
- Proper use of tools, measuring instruments, and knives
- No damaged or expired measuring tools
- Mandatory use of required safety equipment
Safety & Organization
- Keep safety passages clear at all times
- Firefighting equipment must remain accessible
- All items stored in designated locations
- Remove raw material packaging before workshop entry
- Conserve water and electricity resources
Training & Compliance
New Employee Training
All new employees and transferred personnel must receive job skills training. Work station assignment only permitted after passing training examination.
Quality Control
Raw materials and semi-finished products must undergo self-inspection upon workshop entry. Production only permitted when standards are met or concession acceptance procedures completed.
Safety Principles
Implement "safety first, prevention first" principle. All personnel must wear required labor protection equipment and follow safety production protocols.
Cleanroom Management Specification Version 5
Effective Date: July 2025
Document ID: CMS-5.0-PROD
Revision: 3
Cleanroom Insiders Expert Team
Deiiang's expert team specializes in designing and constructing state-of-the-art cleanrooms tailored to meet diverse industry needs. With a focus on innovation and compliance, we deliver pristine environments that ensure operational excellence and product integrity.
Related product recommendations