Understanding ISO Class 7 Cleanrooms
An ISO Class 7 Cleanroom is a highly controlled environment designed to maintain exceptionally low levels of environmental pollutants. These specialized spaces minimize contaminants such as dust, airborne microbes, aerosol particles, and chemical vapors that could compromise sensitive processes.
What distinguishes ISO Class 7 from ordinary environments? In standard rooms, particles are ubiquitous—floating in the air, settling on surfaces, and potentially causing significant issues in precision manufacturing and research. An ISO Class 7 cleanroom drastically reduces this particle count to create a controlled environment essential for industries where even microscopic contaminants can lead to product failure or compromised safety.
Core Definition
ISO Class 7 cleanrooms permit a maximum of 352,000 particles ≥0.5 micrometers per cubic meter of air (equivalent to 10,000 particles per cubic foot under the outdated FS 209E standard). This strict particle limitation creates environments 100-1,000 times cleaner than typical indoor spaces.
The ISO Classification System (iso 14644-1)
The ISO classification system, defined by ISO 14644-1, provides the global standard for CleanRoom Classification. This system categorizes controlled environments based on the maximum allowable concentration of airborne particles at specific particle sizes.
ISO Class 5
Pharmaceutical filling
ISO Class 7
Medical device assembly
ISO Class 8
Component preparation
As shown in the comparison, ISO Class 7 occupies the mid-range of the ISO classification system, providing significant particle control without the extreme costs associated with higher classification levels. This balance makes it ideal for many critical applications.
ISO Class 7 Cleanroom Requirements
Maintaining ISO Class 7 standards requires strict adherence to multiple environmental controls and procedures:
Particle Count Specifications
Maximum of 352,000 particles ≥0.5µm per cubic meter. Continuous monitoring with particle counters ensures compliance with ISO standards.
Air Changes per Hour
15-25 complete air changes hourly. This high rate of air flow ensures rapid removal of contaminants through HEPA-filtered air systems.
Humidity Requirements
Maintained at 40-60% RH. This range prevents static buildup (low humidity) and microbial growth (high humidity). Critical for pharmaceutical applications.
Gowning Requirements
Full cleanroom suit, hair/beard covers, gloves, and shoe covers. Proper gowning minimizes human-sourced contamination in the clean room.
Detailed Particle Count Requirements
Particle Size (µm) | Maximum Particles per m³ | Maximum Particles per ft³ |
---|---|---|
≥0.5 | 352,000 | 10,000 |
≥1.0 | 83,000 | 2,370 |
≥5.0 | 2,930 | 83 |
Cleaning Procedures for ISO Class 7 Standards
Maintaining ISO Class 7 certification demands rigorous cleaning protocols:
Regular Cleaning Schedules
- Daily: Wipe all work surfaces, mop floors, disinfect high-touch areas
- Weekly: Clean walls, ceiling vents, light fixtures, equipment surfaces
- Monthly: Deep clean entire facility, inspect/replace air filters, clean ducts
Approved Cleaning Agents & Tools
Only non-shedding materials and specialized cleaning solutions permitted:
- Alcohol-based disinfectants (isopropyl alcohol solutions)
- Low-foaming, residue-free detergents
- HEPA-filtered vacuums (capture 99.97% of ≥0.3µm particles)
- Microfiber wipes with sealed edges
- Non-shedding mops with filtered water systems
Cleaning Techniques
Proper methodology is critical for effective contamination control:
- Overlapping wipe technique (never circular motions)
- Clean from top to bottom, back to front
- Work from cleanest areas toward more contaminated zones
- Single-direction mopping patterns
- Proper tool cleaning and storage procedures
Key Applications of ISO Class 7 Cleanrooms
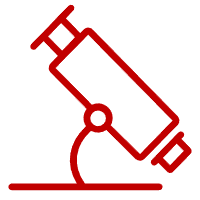
Semiconductor Manufacturing
Essential for producing microchips where particles as small as 0.5µm can cause circuit defects. ISO Class 7 environments protect wafers during non-critical manufacturing stages and equipment assembly.
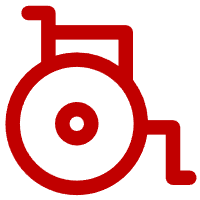
Pharmaceutical Production
Critical for non-sterile drug manufacturing, compounding, and packaging. Prevents contamination that could compromise drug efficacy or patient safety. Meets FDA and EMA requirements.
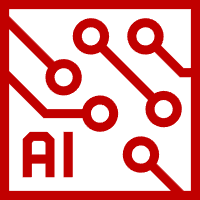
Medical Device Assembly
Used for assembling surgical instruments, diagnostic equipment, and non-implantable devices. Ensures products meet quality standards and regulatory requirements for patient safety.
Benefits of ISO Class 7 Cleanrooms
Benefit | Impact | Industry Examples |
---|---|---|
Enhanced Product Quality | Reduces defects and contamination-related failures | Optics manufacturing, Electronics assembly |
Regulatory Compliance | Meets FDA, EMA, ISO quality standards | Pharmaceuticals, medical devices |
Process Protection | Shields sensitive operations from contamination | Nanomaterial research, biotechnology |
Cost Efficiency | Balances cleanliness requirements with operational costs | All industries compared to higher classes |
Maintenance Challenges & Solutions
While essential, maintaining ISO Class 7 standards presents challenges:
Equipment & Operational Costs
HEPA filtration systems, specialized HVAC, and monitoring equipment represent significant investments. Energy consumption for air handling can be substantial.
Solution: Consider modular cleanrooms for flexibility. Implement energy recovery ventilators and variable frequency drives on motors to reduce operating costs.
Staff Training & Compliance
Human error causes most contamination events. Proper gowning procedures, movement protocols, and cleaning techniques require continuous training.
Solution: Implement comprehensive training programs with regular refreshers. Use visual guides and monitoring systems to ensure protocol adherence.
Continuous Monitoring
Maintaining consistent level of cleanliness requires real-time particle counting and environmental monitoring.
Solution: Install automated monitoring systems with alert functions. Schedule regular third-party validation to ensure compliance with ISO 14644-1 standards.
Expert Insight
"ISO Class 7 cleanrooms represent the optimal balance for many industries—providing significant contamination control without the excessive costs of higher classifications. The key to successful operation lies in comprehensive staff training and rigorous maintenance of both the physical infrastructure and operational protocols."
ISO Class 7 cleanrooms serve as critical infrastructure for industries requiring controlled environments with defined particle counts. By maintaining no more than 352,000 particles ≥0.5µm per cubic meter and implementing strict protocols for air changes per hour, humidity control, and personnel behavior, these facilities enable high-precision manufacturing and research.
The applications in semiconductor manufacturing, pharmaceutical production, and medical device assembly demonstrate how ISO Class 7 environments support technological innovation while ensuring product safety and quality. As industries continue advancing, these controlled environments will remain essential for manufacturing the next generation of high-tech and life-saving products.